When it comes to building a steel garage, one of the first questions that comes to mind is whether you need footings. The short answer is: Yes, most steel garages require footings, especially if you want to ensure your structure is stable and long-lasting. Footings are essential because they provide a strong foundation that supports the weight of your garage and prevents settling or shifting over time.
But how do you know if your garage really needs them, and what type of footings is right for your specific project? In this article, we’ll walk you through everything you need to know, from the basics of footings to understanding how different soil types, environmental conditions, and your garage’s size affect the foundation design. We’ll also discuss the various types of footings, their requirements, and the best way to plan for them to ensure the safety and longevity of your steel garage.
By the end of this article, you’ll be able to determine whether footings are necessary for your project confidently, and if so, how to plan and execute them to protect your investment.
What Are Footings?
Footings are the “foundation” of your steel garage, essentially the “foot” of the structure. They spread the garage’s weight evenly across the ground, ensuring stability and preventing the building from sinking or shifting. Think of footings as the base or root keeping your steel garage firmly anchored to the earth.
Typically made of concrete, footings are buried beneath the ground to support the entire structure. Depending on the type of soil and local conditions, different types of footings may be used to ensure the garage stays secure for years to come.
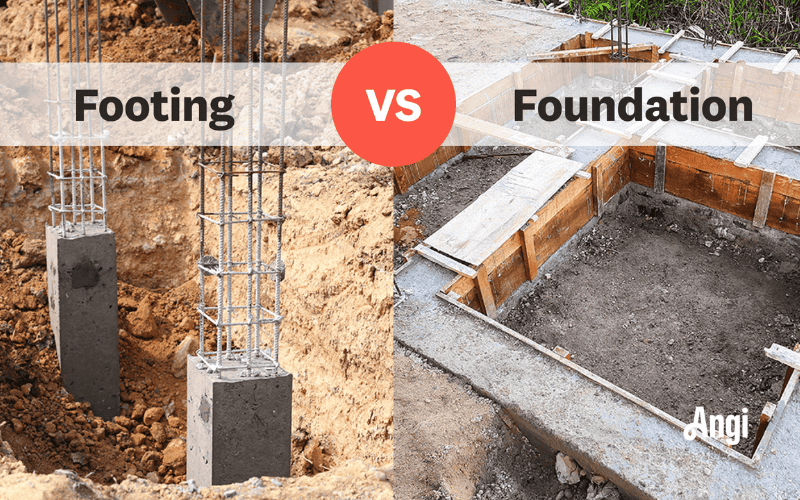
Do I Need Footings for My Steel Garage? Why?
Reasons You May Need Footings:
- Larger or Heavier Garages: Footings are essential if your steel garage is large or you plan to store heavy vehicles or equipment inside. They help evenly distribute the weight of the structure and prevent uneven settling of the ground beneath.
- Poor Soil Conditions: In areas with soft, unstable, or high-moisture soil, footings help stabilize the structure by providing a solid foundation that prevents the garage from shifting or sinking over time.
- Local Building Codes: In many areas, building regulations require footings for permanent or large structures like steel garages, especially in regions that experience freezing temperatures or earthquakes. Footings add stability and prevent damage from environmental factors.
⚠️A Common Misconception:
Some clients assume that smaller steel garages don’t need footings. However, this is a risky assumption. Without proper foundation support, your garage could experience settling or shifting, leading to potential structural issues, safety risks, and costly repairs.
How Do Soil and Environmental Conditions Impact Footing Design?
Soil type and environmental conditions play a crucial role in determining whether footings are necessary and, if so, how they should be designed. In unstable soil environments, it is especially important to assess the soil conditions and choose the appropriate type of footings. Here are two typical soil and environmental factors that influence footing design and how to adjust the design accordingly.
1. Impact of Unstable Soil and Solutions
In moist, soft soil, or loose sandy soil, the soil’s bearing capacity is lower, making it more prone to settling. To prevent structural settling or tilting, you may need to take the following measures:
- Increase the depth of footings: In soft soils, footings should be made deeper to penetrate the unstable upper layers and reach more solid-bearing soil. This often involves increasing the footing depth to 18 inches or even 24 inches, depending on the specific requirements of the site.
- Use larger footing areas: Enlarging the base area of the footings helps distribute the weight of the building, reducing the risk of settling. For soft soil, wide strip footings or slab foundations are commonly used.
- Soil stabilization: In some cases, soil stabilization methods may be needed, such as soil compaction, adding reinforcement layers, or using concrete piles to increase the soil’s load-bearing capacity.
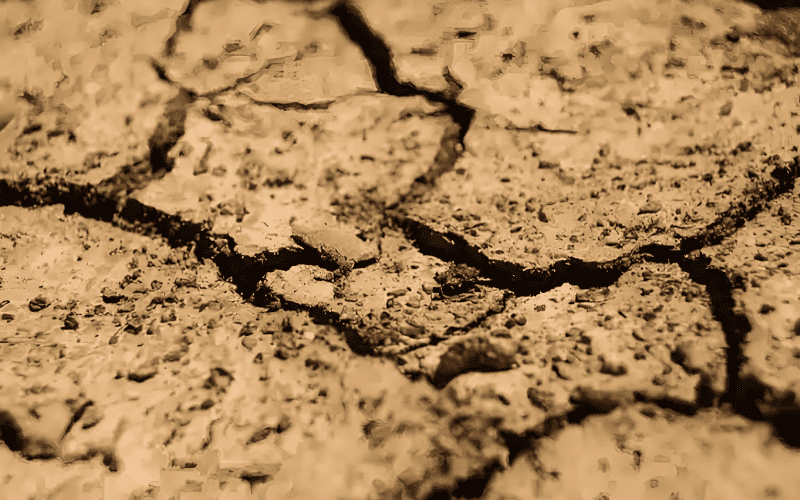
2. Impact of Frozen Ground (Frost Heave) and Solutions
In colder regions, the presence of frozen ground can significantly impact footing design. Frost heave, which occurs when water in the soil freezes and expands, can cause footings and foundations to lift, potentially damaging the garage structure. Therefore, the following considerations must be made in footing design:
- Depth of the frost line: Footings must be designed to be below the frost line, which varies depending on the climate. In colder regions, the frost line typically needs to be at least 36 inches (91 cm) deep, or even deeper, to prevent frost heave from affecting the foundation.
- Use of special materials and techniques: In frozen ground areas, reinforced footings may require additional steel reinforcement or heating systems (such as under-slab heating pipes) to maintain consistent soil temperature and prevent frost-related issues.
- Waterproofing and drainage: In freeze-thaw regions, it is especially important to incorporate effective drainage systems. Excessive water accumulation near footings increases the risk of freeze-thaw cycles and frost heave. Installing drainage pipes and ensuring the soil around the foundation remains dry can significantly reduce the risks posed by frozen ground.
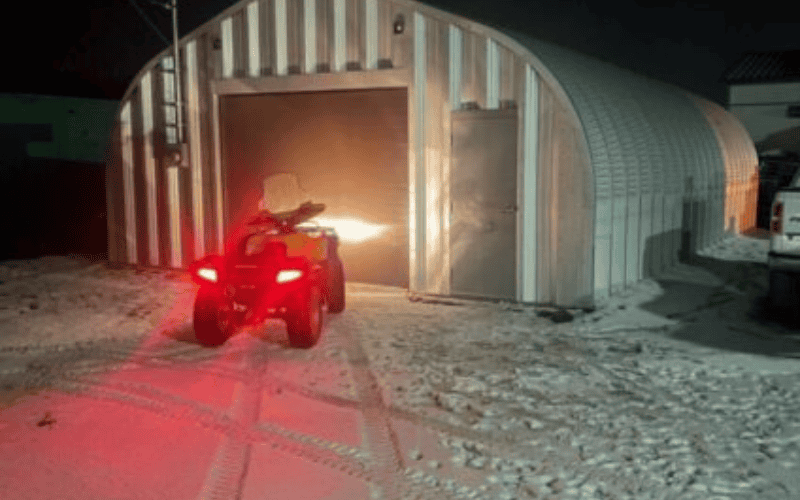
Types of Footings for Steel Garage
Several types of footings are used depending on the size and design of your steel garage. Here’s an easy-to-understand breakdown of the most common ones:
- Strip Footings:
This is one of the most common footing types. It’s used to support long walls or other major load-bearing parts of the structure. Strip footings are typically cost-effective and spread the weight evenly along the length of the garage.
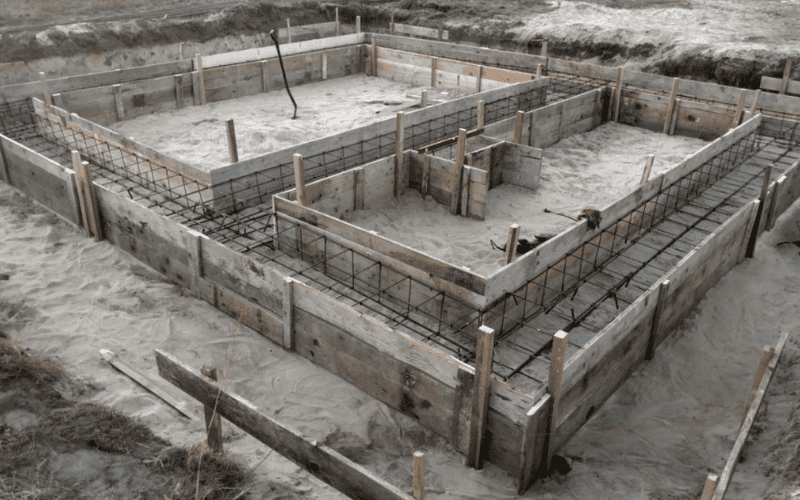
- Isolated Footings:
If your garage has several columns, each column would need an isolated footing. These footings support individual load-bearing columns and are often used for larger garages with multiple support beams.
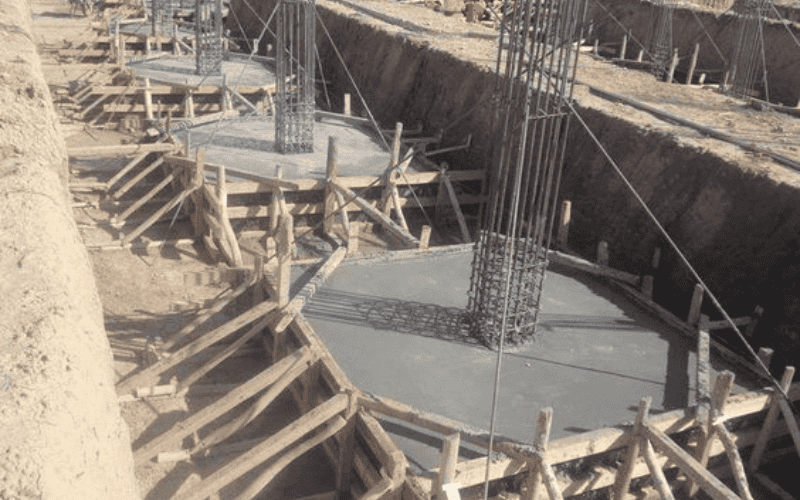
- Slab-on-Grade Footings:
This type of footing involves pouring a single slab of concrete for the entire base of the garage, effectively spreading the load over the entire floor. It’s commonly used for garages that are on level, stable ground, and where no basement or underground layer is needed.
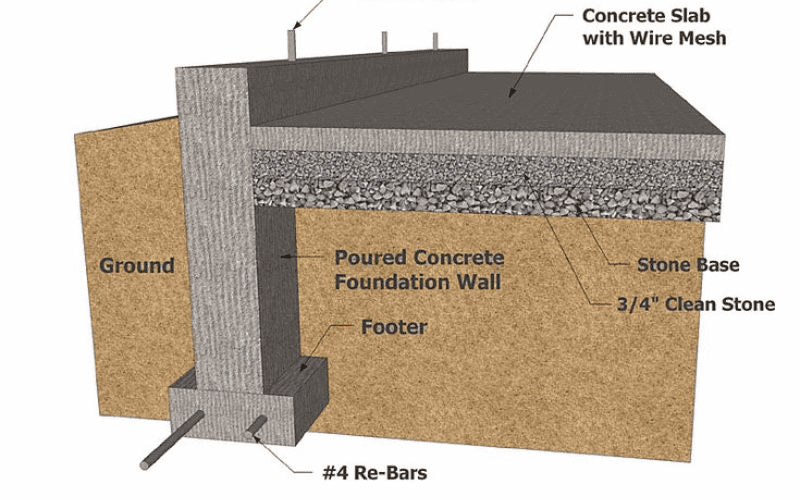
- Deep Footings:
If your garage is built on soft or unstable soil, deep footings may be necessary. These are designed to reach deeper into the ground, where the soil is more stable, ensuring a secure foundation that can handle the weight of the structure.

Steel Garage Footing Requirements
To ensure the stability of your steel garage, footings must meet certain requirements. These include:
- Size and Depth:
Generally, footings need to be at least 12 inches deep. However, depending on the size and weight of your garage, as well as the local soil conditions, you may need deeper or wider footings for added stability. - Reinforcement with Steel:
Steel reinforcement (rebar or mesh) is often used in footings to increase their strength and prevent cracking. This helps ensure the foundation can support the garage for many years without issues. - Concrete Strength:
The concrete used in footings must be strong enough to bear the weight of the garage. Typically, the concrete should be at least 2500 psi (pounds per square inch) in strength, though more demanding structures may require higher-strength concrete (e.g., 4000 psi). - Freeze-Proofing:
In colder climates, footings need to be deeper than the frost line to prevent damage caused by freezing and thawing cycles in the soil. This is important for ensuring the garage stays stable during winter months. - Drainage:
Proper drainage around the foundation is crucial to prevent water from accumulating around the footings, which could lead to structural damage over time. Ensuring that the ground slopes away from the garage and that water doesn’t pool around the base will prolong the life of your garage.
How to Plan Footings for Your Steel Garage
Planning footings for your steel garage is a crucial step to ensure a stable and safe structure. Here are the key steps to follow:
- Consult a Professional
It’s always a good idea to work with a structural engineer or contractor who can help you design the right footings for your garage based on the specific soil conditions and garage size. They can ensure everything is in compliance with local building codes and regulations. - Assess Soil Conditions
Before starting, it’s important to evaluate the soil conditions on your property. If the soil is soft or unstable, deeper or reinforced footings may be required. A soil test can help you determine what type of footings are best for your location. - Determine the Size and Load of Your Garage
The size of your garage and the weight of what you plan to store inside will influence the size and depth of the footings. Larger or heavier garages require stronger, more robust foundations. - Understand Local Building Codes
Different areas have different requirements when it comes to footings and foundation design. Make sure you know the local regulations, especially if you’re in an area prone to freezing temperatures or earthquakes. Meeting these codes is critical for the safety and longevity of your garage. - Budget and Timeline
Footing construction can add to your overall project cost and timeline. Be sure to factor in the cost of excavation, materials, reinforcement, and pouring concrete. Planning ahead can help prevent delays and unexpected expenses.
FAQs
1. Can I use a concrete slab as a footing, or do I need separate footings for my steel garage?
A concrete slab alone cannot replace footings. Footings are crucial for distributing the weight of the structure evenly across the ground and preventing settling. While a slab can provide a solid floor, footings are typically needed to support the perimeter and foundation of the steel garage, especially in unstable soil conditions.
2. How deep do the footings need to be for different sizes of steel garages?
The depth of footings depends on factors such as soil conditions, local building codes, and the size of the garage. Generally, footings should be at least 12 inches deep for small garages, with larger structures requiring deeper footings (up to 24 inches or more). For areas with freezing temperatures, footings must extend below the frost line to avoid frost heave.
3. What are the risks of not having proper footings for my steel garage?
Without proper footings, your steel garage could experience uneven settling, which can cause structural damage, misalignment of doors and windows, and even collapse in extreme cases. Inadequate footings can also lead to cracks in the concrete slab, compromising the overall stability of the building.
4. Do I need to hire a professional to assess my soil before installing footings?
Yes, it’s recommended to have your soil assessed by a professional, especially if you are building in an area with poor soil conditions or where frost heave is a concern. A soil test can determine the best type of footings for your garage and ensure that your foundation is designed to support the weight of the structure properly.
5. How long does it take to install footings for a steel garage?
The installation time for footings varies depending on factors such as the size of the garage, soil conditions, and weather. Generally, the process can take anywhere from a few days to a week. This includes excavation, pouring the concrete, and allowing it to cure. If additional steps like soil stabilization or frost protection are required, the timeline may be extended. It’s important to plan accordingly and ensure all permits and inspections are in place to avoid delays.
6. Can Prefab Steel Garages use standard footings?
Yes, prefab steel garages typically require standard footings, but the exact type and size depend on factors like soil conditions, local building codes, and garage dimensions. Prefabricated designs usually include guidelines for footing construction to ensure proper support.