What holds skyscrapers, stadiums, and bridges together? The answer lies in the precision and strength of welding technology. In steel structures, welding is more than just a process—it’s the vital link that ensures durability, safety, and performance.
From high-rises to industrial facilities, steel forms the backbone of modern construction. But here’s the real challenge: ensuring every weld is perfect and every joint is rock solid.
This article takes you inside the key welding technologies behind steel structures, highlighting the challenges, and why quality control and safety are so critical to their strength and reliability. Whether you’re an engineer, construction pro, or just curious, let’s jump into the essentials of steel welding and see how it’s shaping the future of construction!
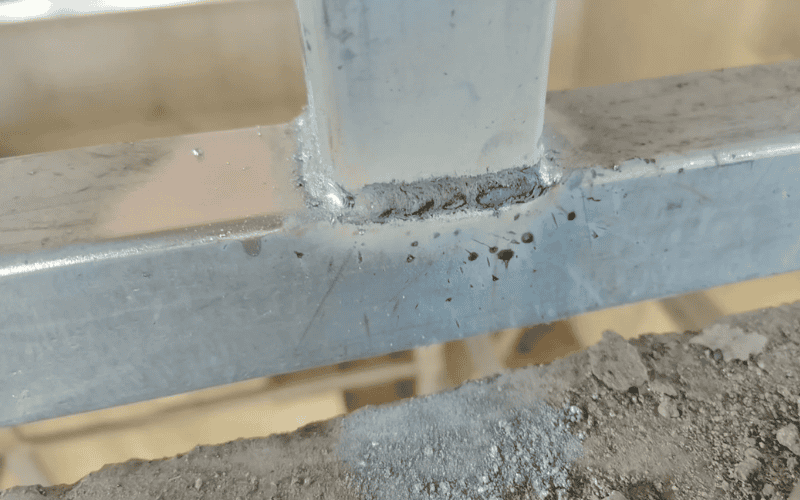
Types of Welding in Steel Structures
Arc Welding
Arc welding is one of the most widely used techniques in steel structure construction. It works by generating an electric arc between an electrode and the base metal, melting and fusing the materials together.
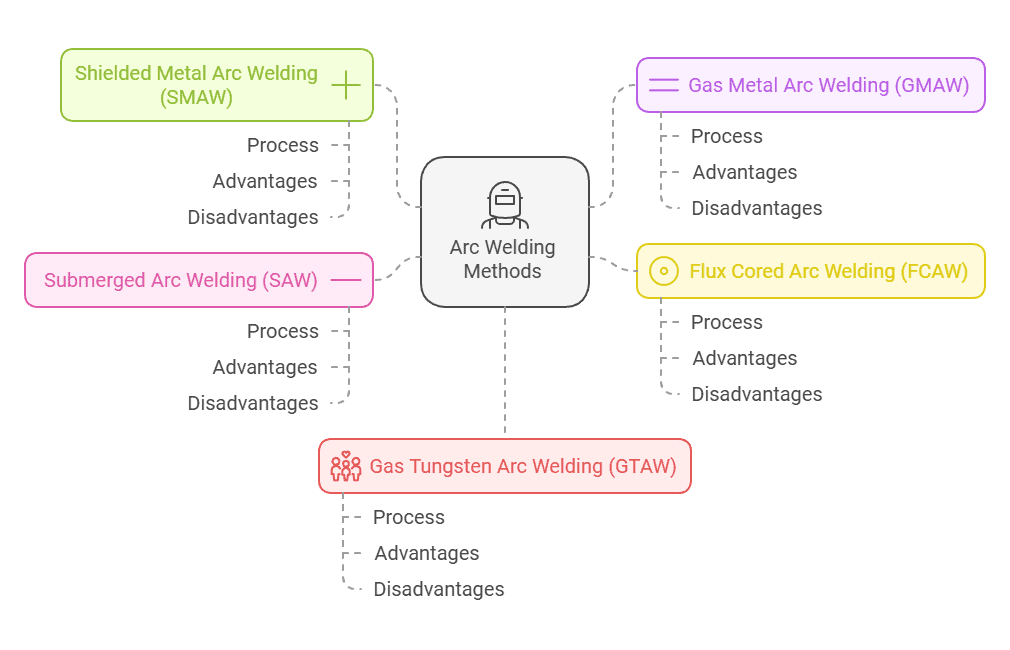
Shielded Metal Arc Welding (SMAW)
How It Works: An electric arc forms between the electrode and the base metal, while the electrode’s coating generates a protective gas shield. This method is preferred for its simplicity and effectiveness.
- Advantages: SMAW is versatile and works with various steel types. It’s portable for on-site use and has low equipment costs.
- Disadvantages: However, it has slower speeds, needs frequent electrode replacements, and can cause slag inclusions if not properly cleaned.
Gas Metal Arc Welding (GMAW)
How It Works: A continuous wire electrode is fed through a welding gun, and a shielding gas, like argon or CO₂, safeguards the weld pool from contamination.
- Advantages: GMAW is fast and provides smooth, clean welds, making it great for automated systems.
- Limitations: It’s sensitive to wind, making outdoor use harder, and requires a gas supply, which adds to the setup cost.
Flux Cored Arc Welding (FCAW)
How It Works: FCAW utilizes a tubular wire filled with flux, which supplies additional protection and alloying elements during the welding process.
- Advantages: It’s perfect for thick materials with excellent penetration and high deposition rates, and can be used outdoors without extra shielding gas.
- Disadvantages: However, FCAW has higher costs for flux-cored wires and creates more spatter, requiring more cleanup.
Submerged Arc Welding (SAW)
How It Works: In SAW, the arc is submerged under granular flux, protecting the weld pool from contamination.
- Advantages: It’s great for thick materials, offering deep penetration, high speeds, and high-quality welds with minimal defects.
- Disadvantages: SAW is limited to flat or horizontal positions and needs specialized equipment, which can be cumbersome.
Gas Tungsten Arc Welding (GTAW)
How It Works: Known as Tungsten Inert Gas (TIG) welding, GTAW utilizes a non-consumable tungsten electrode and an inert gas, such as argon, to protect the weld pool from contamination.
- Advantages: Renowned for producing high-precision, clean welds without spatter, GTAW is ideal for thin materials and critical applications.
- Disadvantages: The catch? It’s slower than other methods and requires skilled operators to get those perfect results.
Welding Materials for Steel Structures
The quality of welding materials directly impacts the strength and durability of steel structures. Here’s what you need to know:
Electrodes and Wires
- Types and Selection: Electrodes and wires are chosen based on the steel grade to ensure chemical compatibility and mechanical performance.
- Diameter Impact: The diameter of the electrode or wire affects welding current, deposition rate, and weld size.
Flux
- Role in Welding: Flux protects the weld pool from oxidation, removes impurities, and can add alloying elements to improve weld properties.
- Types: Acidic, basic, and neutral fluxes are available, each suited for specific electrodes and base metals.
Shielding Gases
- Types: Inert gases (like argon) and active gases (like CO2) are commonly used.
- Selection: The choice of gas depends on the welding method and material. For example, argon is ideal for stainless steel, while CO2 is cost-effective for carbon steel.
Key Points to Follow for Welding Materials
To ensure the highest quality welds, strict adherence to material handling and usage guidelines is essential. Here are the must-follow practices:
1. Storage and Moisture Control:
Electrodes and flux should be stored in dry, well-ventilated areas to prevent moisture absorption. Low-hydrogen electrodes (e.g., E5015, E5016) require baking at 300°C~350°C before use to prevent hydrogen-induced cracking.
2. First-In, First-Out Principle:
To avoid degradation, always use older welding materials first. This ensures their quality and effectiveness are maintained over time.
3. Material Compatibility:
Never use rusted electrodes or mix acidic and basic electrodes. Select welding materials that match the chemical composition and mechanical properties of the base metal.
4. Special Considerations:
For thick plates or low-temperature environments, always opt for low-hydrogen electrodes or wires known for their excellent crack resistance.
Key Welding Techniques for Steel Structures
Welding Procedure Qualification: The First Step to Ensuring Welding Quality
Why is Welding Procedure Qualification Necessary?
Without proper qualification, even the smallest inconsistency can lead to weak joints or structural failures.
How to Conduct Welding Procedure Qualification?
- Trial Welding: We start with test welds to simulate real conditions, ensuring the parameters perform as expected and making adjustments if needed.
- Performance Testing: After the trials, we test for strength, toughness, and other key properties to verify the procedure meets standards and can handle project demands.
- Documenting the Procedure: Once confirmed, we record the welding methods and parameters in a detailed file to guide future welds and maintain consistency across the project.
Controlling Welding Distortion: Keeping Structures Straight and Strong
Welding distortion is a common challenge, but it can be effectively controlled with proper techniques.
What Causes Distortion?
During welding, localized heating and cooling cause the steel to expand and contract, leading to warping or bending. If left unchecked, this can compromise both the appearance and structural integrity.
Our Approach to Control:
- Optimized Welding Sequence: By carefully planning the order of welds, we minimize heat buildup and stress concentration.
- Preheating and Post-Heating: We preheat the steel to reduce temperature differences and follow up with post-weld heat treatment to stabilize the structure.
- Reinforced Design: Adding stiffeners or using rigid fixtures helps counteract de
Managing Residual Stresses: Tackling the Hidden Threat
Residual stresses are like silent enemies—they’re invisible but can lead to cracks or even catastrophic failures if not addressed.
What Are Residual Stresses?
During welding, uneven heating and cooling create internal stresses within the steel. Over time, these stresses can weaken the structure.
How We Handle It:
- Heat Treatment: Techniques like annealing or tempering are used to evenly redistribute stresses and restore the steel’s strength.
- Mechanical Methods: We use tools like peening or vibration to relieve localized stress points.
Welding Quality Inspection: From Start to Finish
Quality control is integrated into every phase of our welding process.
- Pre-Weld Checks:
We inspect the base material for surface defects, verify the steel grade, and ensure precise dimensions. Equipment like power sources, wire feeders, and gas systems are also thoroughly checked to avoid any operational hiccups. - During Welding:
Real-time monitoring of current, voltage, and welding speed ensures optimal conditions. Our team also conducts visual inspections to catch issues like incomplete fusion or porosity immediately. - Post-Weld Testing:
We employ advanced non-destructive testing (NDT) techniques, including ultrasonic and radiographic testing, to identify internal defects. For critical joints, destructive tests like tensile and impact testing validate the weld’s mechanical properties.
Safety Precautions for Steel Structure Welding
Welding safety isn’t just about following rules—it’s about safeguarding lives and keeping projects on track without costly delays.
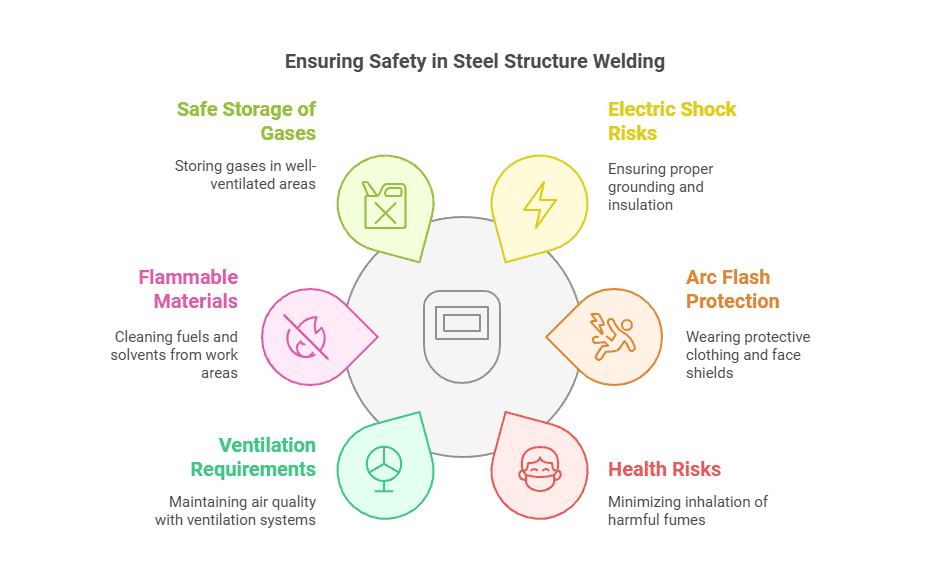
Electrical Hazards
- Electric Shock Risks: Ensuring proper grounding and insulation is essential to prevent accidental contact with live wires. We always verify our equipment connections and insulation to keep everyone safe.
- Arc Flash Protection: Wearing arc-resistant clothing and face shields is a must. This protective gear shields our team from the intense light and heat produced during welding.
Smoke and Gas Exposure
- Health Risks: Prolonged exposure to welding fumes can cause respiratory problems and metal fume fever. We’ve seen how important it is to protect our team’s health by minimizing inhalation of harmful particles.
- Ventilation Requirements: Effective local exhaust ventilation captures fumes at the source, while general mechanical ventilation maintains overall air quality. These systems are vital for maintaining a safe working environment.
Fire and Explosion Hazards
- Flammable Materials in Welding Areas: We make it a priority to clean fuels and solvents from the welding site before starting any project. This simple measure significantly lowers the risk of accidental fires.
- Safe Storage of Welding Gases: Proper storage guidelines for gases like oxygen and acetylene are strictly followed. Keeping these gases in well-ventilated areas away from ignition sources helps prevent dangerous explosions.
Expert Welding Services in Comprehensive Steel Structure Manufacturing
In steel structure construction, the quality of welding determines the integrity of the entire project. By selecting the appropriate welding methods, using top-quality materials, and adhering to best practices, we guarantee that every weld is strong, durable, and dependable.
We operate 15 state-of-the-art welding production lines, supported by a team of skilled professionals with over 20 years of combined experience. Our commitment to excellence ensures we deliver precision and expertise to every project, whether it’s an industrial warehouse building, large span steel warehouse buildings, or prefab gym buildings. With rigorous quality control and a commitment to safety, we deliver top-notch welding services that meet the highest industry standards, ensuring the success and longevity of your steel structures.