What exactly is a steel truss system? It’s a strong framework made up of interconnected steel members that work together to support and distribute loads efficiently. These systems play a crucial role in providing structural integrity while reducing material usage, making them ideal for large, open spaces. You’ll find steel truss structures in a variety of applications, from bridges to rooftops, creating durable and reliable designs.
In this article, we’ll dive into the different types of steel trusses, the design principles that make them so effective, and how our expertise ensures your project is built to last.
What Is a Steel Truss?
A steel truss is a triangulated system of interconnected structural elements, often called an open web girder. Its smart design provides exceptional strength while using less material, making it perfect for structures that need large, open spaces.
So why are steel trusses so popular? They offer a high strength-to-weight ratio, resist moisture and pests, and require minimal maintenance. Most importantly, they create wide, column-free interiors, making them a go-to choice for warehouses, aircraft hangars, and other large commercial buildings.
Types of Steel Truss Systems
Understanding the different types of steel trusses is essential for selecting the right system for your project. Each variety has distinct features that make it ideal for certain uses, and selecting the appropriate design can greatly influence efficiency, expenses, and durability.
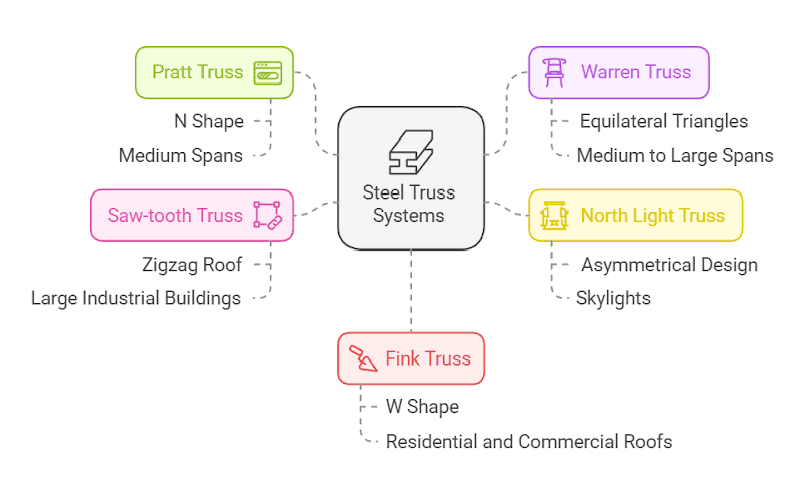
Pratt Truss
The Pratt Truss has this cool “N” shape, where vertical members handle compression and diagonal ones manage tension. It’s a design that really spreads out the loads efficiently, making it perfect for medium-span structures like bridges and roofs, usually ranging from 20 to 50 meters. What’s fantastic is that it’s easy to construct, saving both time and expenses.
But for longer spans, you might run into issues with more joints and members, which can affect cost-efficiency. To keep it performing at its best, maintaining consistent spacing between joints and optimizing diagonal angles helps balance loads and reduce material stress.
Warren Truss
The Warren Truss is made up of equilateral triangles and alternating diagonal members, which means it doesn’t need any vertical supports. It’s fantastic at evenly distributing loads, making it great for medium to large-span structures like bridges and industrial buildings, spanning anywhere from 30 to 100 meters.
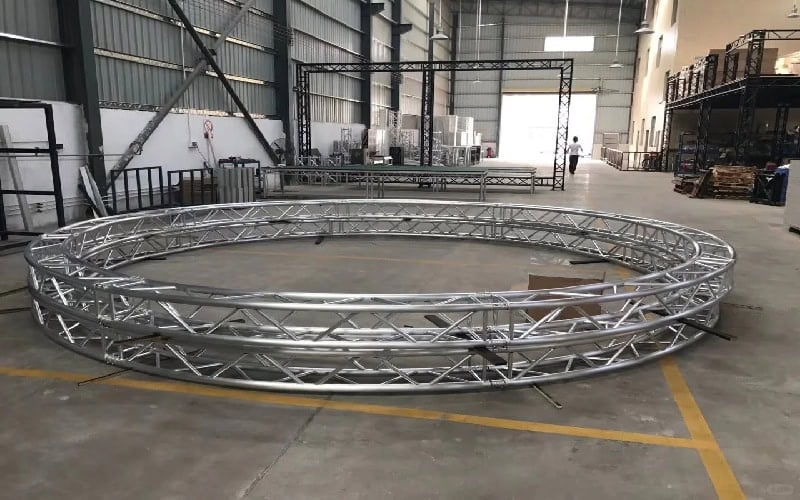
The design is light and sleek, which fits well with modern architecture. That said, its more complex joints and the need for stronger materials can make it a bit tricky. By carefully optimizing joint connections, such as using bolted or welded connections to reduce stress concentrations, and selecting higher-grade steel with better tensile strength, the design ensures both maximum load distribution and long-term durability.
North Light Truss
The North Light Truss has a unique asymmetrical design: a steep slope on one side, a gentle slope on the other, and skylights on top. This lets in plenty of natural light while still keeping things stable, making it a great choice for industrial facilities and warehouses, usually spanning between 15 to 40 meters.
It’s an excellent method to reduce energy expenses and improve the workplace atmosphere. The only downside? Its more intricate design might increase the time and cost of your project. But with strategic skylight placement along the steeper slope and reinforced framing around openings, you can get the best of both worlds—plenty of light and solid structural performance.
Saw-tooth Truss
The Saw-tooth Truss takes things up a notch by combining multiple North Light Trusses to create that iconic zigzag roof. It’s perfect for large industrial buildings and exhibition halls, usually spanning 30 to 80 meters, offering tons of natural light without compromising stability.
The best part? It’s super efficient when it comes to lighting and space use, making it an eco-friendly option. However, the detailed design and construction process can drive costs up. By adjusting the spacing and angle of the saw-tooth profile, you can really maximize efficiency.
Fink Truss
The Fink Truss features a characteristic “W” pattern formed by diagonal members within triangular sections, ensuring even load distribution. It’s often used in residential and commercial roofs, typically spanning 10 to 30 meters, thanks to its lightweight and cost-effective design. For larger spans, though, the longer members can make it less economical. With careful adjustment to the angle and spacing of the diagonal members, you can maximize both load-bearing capacity and material efficiency.
As a leading steel truss manufacturer, we offer customized designs tailored to your specific needs, meeting various span, load, and functional requirements. And these are just a few of the many steel truss types we can provide!
Design Principles of Steel Truss Systems
Creating a steel truss system combines art and science, demanding thorough knowledge of engineering principles, material properties, and practical performance. Here are the key considerations that ensure a truss system is not only functional but also efficient and durable.
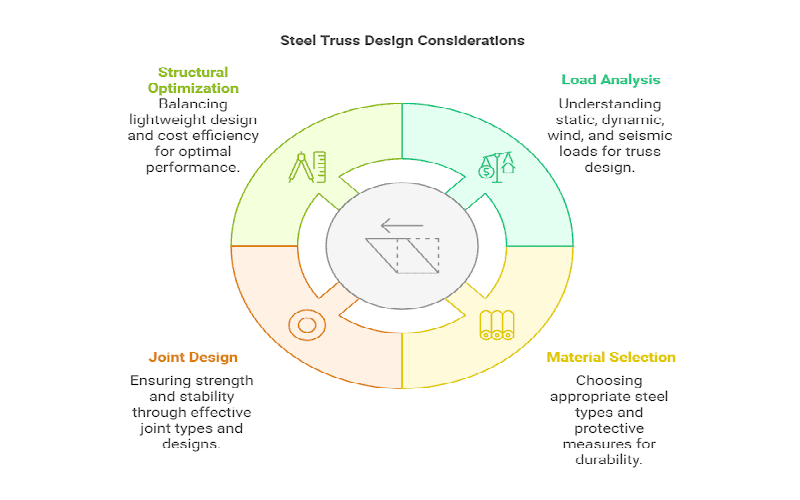
Load Analysis
Static and Dynamic Loads
The foundation of any truss design lies in accurately distinguishing between static (permanent) loads, such as the weight of the structure itself, and dynamic (temporary) loads, like moving vehicles or equipment. This differentiation is essential for maintaining long-term structural integrity and functionality.
Wind and Seismic Loads
Environmental forces like wind and earthquakes can place immense stress on a truss system. To ensure resilience, designs must incorporate features that counteract these forces effectively.
For wind loads, aerodynamic shapes and reinforced bracing systems are often employed to reduce wind resistance and distribute pressure evenly.
In seismic zones, we recommend using advanced modeling tools, such as finite element analysis (FEA), to simulate environmental conditions and refine designs for maximum durability.
Material Selection
Types of Steel
The choice of steel is pivotal. High-strength alloys, such as ASTM A572 or A992, are often preferred for their superior durability and load-bearing capacity. These materials form the foundation for trusses designed to withstand heavy loads and challenging conditions.
Corrosion and Fire Protection
Steel’s Achilles’ heel is its vulnerability to corrosion and fire. Applying protective coatings, such as galvanization or epoxy, and fire-resistant treatments ensures the truss system maintains its integrity over time, even in challenging conditions.
For fire protection, we recommend the following approaches:
- Intumescent coatings: These expand under high heat, creating a protective insulating layer that slows the impact of fire.
- Fire-resistant boards or sprays: These materials can be applied to steel surfaces to provide additional insulation and slow down heat transfer.
- Encasement with concrete or gypsum: Encasing steel members in fire-resistant materials like concrete or gypsum significantly enhances their fire resistance.
- Use of fire-rated steel alloys: Certain steel grades are specifically designed to maintain strength at higher temperatures, offering inherent fire resistance.
By combining these methods, steel truss systems can achieve the necessary fire protection to meet safety standards and ensure long-term performance.
Related Reading:Fire Prevention for Steel Structures: Classifying, Protection, Maintaining
Joint Design
Types of Joints
Joints are the critical points where forces converge, making their design pivotal to a truss system’s performance. Welded joints provide unmatched strength and rigidity, ideal for structures requiring high load-bearing capacity, such as bridges or industrial facilities. Bolted joints, by contrast, provide flexibility and easy assembly, making them ideal for modular or temporary structures such as event stages. Well-designed joints guarantee structural stability, durability, and dependable performance in all conditions.
Strength and Stability
A truss’s strength depends entirely on its weakest joint. Properly designed joints ensure that loads are evenly distributed, preventing stress concentrations that could lead to failure. This is especially important in structures subjected to dynamic or uneven loads.
Structural Optimization
Lightweight Design
Contemporary engineering heavily depends on sophisticated software tools to maximize material efficiency. By strategically reducing weight without compromising strength, designers can create trusses that are both efficient and cost-effective. This is particularly important for large-span structures where every kilogram saved translates to significant cost savings.
To achieve an effective lightweight design, we recommend focusing on three key areas:
- Material selection: Using high-strength, low-weight alloys like ASTM A913 or A992 steel ensures durability while minimizing mass.
- Geometric optimization: Advanced software, such as finite element analysis (FEA), helps identify areas where material can be reduced without affecting performance.
- Efficient load paths: Designing trusses to direct loads along the most efficient paths reduces the need for excess material.
By combining these strategies, lightweight trusses can achieve optimal performance, reducing both material costs and environmental impact without sacrificing strength or safety.
Cost Efficiency
Balancing structural performance with budget constraints is key to great design. By using innovative materials, efficient fabrication, and precise engineering, we can create truss systems that deliver exceptional value without compromising quality or safety.
Prefabricated steel trusses are one way to achieve cost efficiency. Manufactured in controlled environments, they reduce material waste and labor costs. These trusses also speed up on-site assembly, saving both time and money.
We also recommend modular designs, which standardize components and streamline assembly. This approach lowers production costs while ensuring consistent quality. By combining these strategies, prefabricated steel trusses offer a cost-effective solution that doesn’t sacrifice performance or durability.
Finding Your Steel Truss Systems Building Manufacturer
Steel truss systems continue to shape the future of construction, with advancements in smart design and sustainable practices driving innovation. As a leading steel truss manufacturer, we are committed to delivering high-quality, efficient, and cost-effective solutions tailored to your needs. Our expertise goes beyond trusses to encompass complete steel structure systems, ensuring every component of your project is seamlessly integrated for optimal performance.
Our Expertise as a Steel Truss Manufacturer
- High-Quality Material Supply: Our own steel manufacturing facility ensures that the steel we use meets national standards and project requirements. We can also supply a variety of steel specifications on time, avoiding any delays due to material shortages.
- Comprehensive Engineering Capability: From structural design and load analysis to material selection and joint design, we offer full engineering capabilities. We offer our clients a comprehensive solution, supporting them every step of the way from concept to completion.
Whether you’re planning a bridge, industrial facility, or commercial building, our team is ready to bring your vision to life. Get in touch with us today to discover how we can assist with your next project.