When you think of iconic landmarks like the Eiffel Tower or the Golden Gate Bridge, one thing stands out: steel. It’s the material that shapes not only our most impressive monuments but also the everyday buildings around us.
Steel structures constitute the fundamental support of contemporary architecture, providing unparalleled strength, adaptability, and swiftness in construction processes. However, one may ask, what precisely defines a steel structure, and why has it emerged as the preferred option for builders across the globe?
In this article, we’ll break down the key components, advantages, applications, and future of steel structures—showing you why steel is more than just a building material, it’s the foundation of our urban future.
What is a Steel Structure?
Steel structure is a construction system primarily composed of steel components that provide support, stability, and durability. It is widely used in buildings, bridges, and industrial facilities due to steel’s exceptional mechanical properties, including high strength, ductility, and resistance to environmental stresses. Steel’s versatility makes it suitable for both large-scale and smaller projects, offering long-lasting performance and design flexibility.
Steel Structure Basics: Composition
Composition of Steel in Structures: Types of Steel
Steel used in construction is typically categorized into different types based on its composition and the addition of alloying elements. Each type possesses distinct characteristics tailored to meet particular construction requirements.
- Carbon Steel: Carbon steel, which primarily consists of iron and carbon, is the most frequently utilized type in steel structures. It is known for its strength and affordability but can be susceptible to corrosion over time without proper treatment.
- High-strength low-alloy (HSLA) steel: This type of steel has high strength and good corrosion resistance and is suitable for structures that need to bear large loads.
- Weathering steel: Weathering steel is widely used in bridges and building exterior structures due to its good corrosion resistance and weathering resistance, especially for environments exposed to severe weather conditions.
- Cold-formed steel: Steel formed by cold working, usually used for lightweight structures, has high strength and good toughness, and is suitable for small and medium-sized buildings and reinforcement purposes.
- Structural steel: Structural steel is used for load-bearing frames, providing high strength and stability. It is a common type of steel in buildings, bridges and other large structures.
- Stainless Steel: Renowned for its outstanding corrosion resistance, stainless steel is often used in environments exposed to harsh weather conditions or chemicals. It is commonly utilized in the construction of bridges, building facades, and various exterior applications where robust durability is paramount.
Main Components of Steel Structures:
The components of a steel structure all play a vital role in ensuring the strength, stability and efficiency of the overall design.
- Steel Beams: These horizontal members support loads and provide stability across wide spans. Steel beams are essential for creating expansive floor plans and open spaces in buildings.
- Steel Columns: Vertical components that carry the weight of the structure. Steel columns are used to transfer loads from beams and slabs to the foundation, allowing for tall, multi-story buildings.
- Steel Trusses: Triangular frameworks used to support large spans, especially in roofs and bridges. They are engineered to evenly distribute loads, offering robust support while optimizing material usage.
- Connections: The joints and fastenings that link various steel members. These can include welded joints, bolted connections, or rivets, each chosen based on the specific design and structural requirements of the project.
Steel Structure Systems
Steel structure systems are essential components in modern steel construction, providing stability and durability. Here are the key systems that make up a steel structure:
Steel Structure Foundation: Supports the building by transferring loads from the structure to the ground, often using steel piles or beams.
Steel Floor System: Composed of steel beams and decking, this system supports floors, offering strength and lightweight properties.
Steel Grid Structures: A network of steel members forming a stable structure, ideal for large open spaces with minimal material use.
Steel Structure Bracing System: Provides lateral stability to resist forces like wind or earthquakes, using diagonal braces made from steel.
Steel Truss System: A triangular steel framework used to support roofs and bridges, offering strength with minimal material.
Steel Roof System: Involves steel purlins, beams, and decking to form a durable and lightweight roof that resists environmental forces.
Steel Framing System: The skeleton of the building, consisting of steel columns, beams, and braces, providing primary structural support.
Light Gauge Steel Framing System: A cost-effective, lightweight framing system used in residential and low-rise buildings, featuring pre-fabricated steel studs and tracks.
Metal Cladding Systems: Used as the outer protective layer, metal panels offer weatherproofing and a modern aesthetic while ensuring durability.
Each of these systems contributes to creating strong, flexible, and durable steel buildings for a wide range of applications.
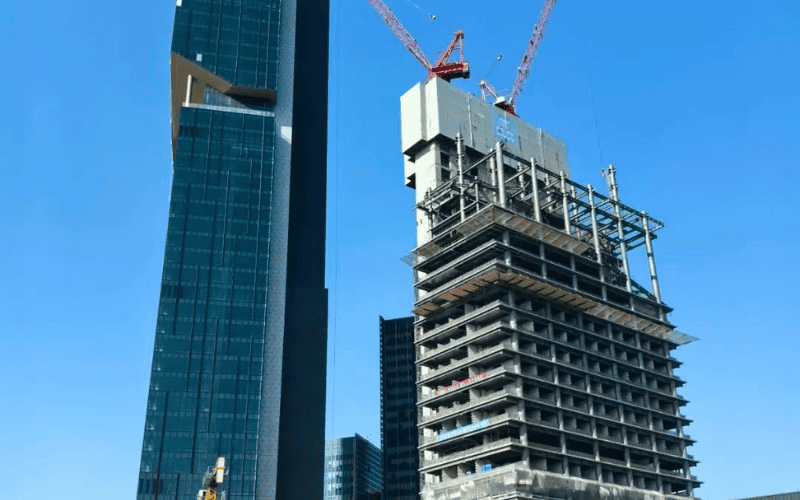
Types of Steel Structure
Frame structure
A frame structure comprises vertical columns and horizontal beams, forming a rigid framework that supports the building’s weight. It is stable and strong, suitable for large-span designs, and is cost-effective and fast to construct. Common applications include commercial buildings, warehouses, bridges, and industrial facilities.
Truss structure
Truss structure is made up of multiple triangular units connected together, using the rigidity of the triangles to evenly distribute the load. It is lightweight yet strong, capable of spanning large areas, and efficient in terms of material utilization. Truss structures are widely used in roofs, bridges, large industrial buildings, and towers.
Arch structure
Arch structure uses curved beams to transfer loads through compression and can support heavy objects. It has strong long-span support capacity, beautiful structure, and can effectively withstand huge vertical loads. Common applications include bridges, stadiums, large-span buildings, and exhibition halls.
Shell structure
Shell structure is a thin, curved steel structure that is often used to construct large-area roofs or shells. It uses less material, is light, and has a high load-bearing capacity, and can cover a large area. Shell structures are commonly used in buildings such as domes, exhibition halls, theaters, and airport terminals.
Space frame structure
A space frame structure is a three-dimensional structure consisting of multiple nodes and beams that can evenly distribute loads in all directions. It can span a large range of space without supporting columns, has a flexible structure and strong earthquake resistance. Space frames are widely used in stadiums, exhibition centers, large shopping malls, and industrial plants.
Portal frame structure
Portal frame structures are composed of rigid frames and beams to form a large span space and are widely used in industrial buildings. This structure is simple and fast to construct, making it very suitable for rapid construction of large spaces. It is commonly found in places such as industrial plants, warehouses, agricultural facilities, and hangars.
Tension structure
Tension structures use steel cables or flexible materials to bear and distribute loads through tension, and are usually suspended in design. Lightweight and flexible, they can meet temporary or aesthetic requirements. Tension structures are commonly used in tents, stadiums, temporary exhibitions, and roof structures.
Lattice structure
Lattice structures are composed of crossed steel members to form a light and strong frame. Its advantages are efficient material use, light weight, wind resistance, and ability to withstand high-load environments. Lattice structures are commonly used in fields such as power towers, transmission towers, bridges, and pylons.
Cable suspension structures
Cable suspension structures suspend loads through steel cables and are suitable for large-span designs. They can support ultra-long spans, are structurally stable, and have unique visual effects. Cable suspension structures are commonly used in buildings such as suspension bridges, large-span roofs, and airport terminals.
Steel Structure Design
Designing steel structures involves several key engineering principles to ensure the building is safe, efficient, and functional. These principles help engineers calculate the appropriate sizes for steel members and determine how they should be connected.
- Mechanical Design: The ultimate objective is to guarantee that the steel components can endure the forces acting upon them. Mechanical design includes the calculation of internal forces such as tension, compression, shear, and bending that affect steel members under different loads.
- Load Calculation: Steel structures must be designed to accommodate a variety of loads, including dead loads (the weight of the structure itself), live loads (like people and furniture), wind loads, and seismic forces. Accurate load calculations are crucial for determining the suitable size and strength of steel beams, columns, and connections.
- Stability Analysis: Structural stability is crucial in preventing collapse or deformation. Engineers conduct stability analyses to assess factors like buckling in columns, bending in beams, and torsion in members under stress. The goal is to design the structure so that it can resist external forces without losing stability.
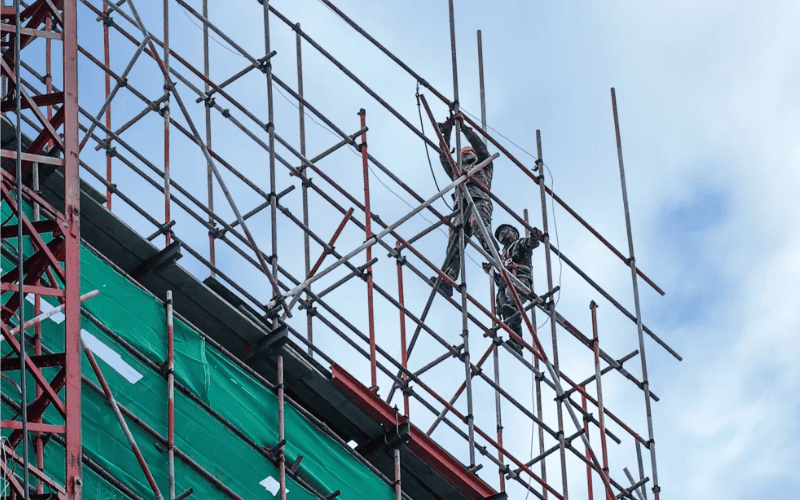
How Steel Structures Are Made
Steel structures are built using a highly organized and standardized process that ensures each component is precisely manufactured, assembled, and installed. From the production of raw steel to the final on-site installation, several key stages are involved in the creation of a steel structure. These stages are governed by strict industry standards to ensure safety, efficiency, and durability.
Standards Followed in Steel Structure Manufacturing
Steel structure manufacturing follows internationally recognized standards and codes to ensure the safety and quality of the materials and construction process. These standards include:
- ISO Standards: The International Organization for Standardization (ISO) establishes worldwide standards for steel materials, testing methodologies, and structural design. These guidelines cover everything from steel grades to testing methods.
- ASTM Standards: The American Society for Testing and Materials (ASTM) provides specifications for steel materials and construction practices, ensuring the materials meet specific performance criteria like strength, flexibility, and durability.
- EN Standards: The European Standards (EN) are another set of codes that guide the design, manufacturing, and construction of steel structures in Europe, focusing on safety, quality control, and structural integrity.
These standards guarantee that the steel employed in construction meets the necessary requirements and that the completed structure can endure the forces it will encounter throughout its entire lifespan.
Manufacturing Process: Steel Production, Shaping, and Processing
The process of creating steel structures begins with the production of raw steel, which is then shaped, processed, and prepared for construction.
Steel Production
Steel begins as raw iron, which is refined in a blast furnace to remove impurities. It is then combined with carbon and alloying elements to create different types of steel (e.g., carbon steel, alloy steel, stainless steel) that meet the requirements of the intended application.
Forming
After production, the steel is processed into forms that can be utilized. This includes rolling the steel into plates, beams, or columns of varying sizes and shapes. These forms are essential for the structural elements of the building.
Cutting and Shaping
Steel components are then cut and shaped according to precise measurements using advanced cutting techniques, such as:
- Laser cutting: High precision cuts for intricate designs.
- Plasma cutting: Efficient for thicker steel plates.
- Water jet cutting: Used for very fine and accurate cutting.
Welding and Bolting
Once the steel parts have been shaped, they are assembled through welding or bolting:
- Welding: Used for permanent, strong joints, particularly for beams, columns, and connection points.
- Bolting: Often used in the construction of steel structures, bolted connections allow for easier assembly and disassembly if needed.
On-Site Assembly: Prefabricated Components and Installation
Once the steel components have been fabricated, they are transported to the construction site for erection and assembly. This process is meticulously overseen to guarantee the efficient and precise construction of the steel structure.
- Prefabricated Components: Steel members like beams, columns, and trusses are typically prefabricated in factories before being transported to the site. This methodology accelerates the construction process and guarantees high quality by minimizing the need for on-site fabrication.
- Transportation and Delivery: The prefabricated steel parts are carefully transported to the construction site using cranes, trucks, or specialized transport vehicles. Careful handling is crucial to avoid damage during transportation.
- On-Site Installation: Steel parts are assembled on-site, usually with cranes and hoists. Workers carefully position the components and use bolted or welded connections to secure them in place. This process is tightly coordinated to guarantee the safe and efficient construction of the structure.
Common Technologies Used in Steel Structure Manufacturing
Advances in technology have revolutionized the steel structure manufacturing process, improving both accuracy and efficiency. Some of the most commonly used technologies include:
- BIM Technology: Building Information Modeling (BIM) enables the development of a digital representation of the steel structure prior to the commencement of construction. This 3D model includes detailed information about materials, dimensions, and assembly instructions, helping engineers plan and visualize the project more accurately.
- 3D Modeling: 3D modeling software allows engineers and architects to visualize and test the design of steel structures in a virtual environment. This process helps identify potential issues early, improving both safety and cost-efficiency.
- Automated Production: Automation in steel fabrication, such as robotic welding and automated cutting machines, speeds up the manufacturing process while improving precision. Automated systems guarantee that each steel component adheres to rigorous quality standards, thereby minimizing human error and enhancing consistency.
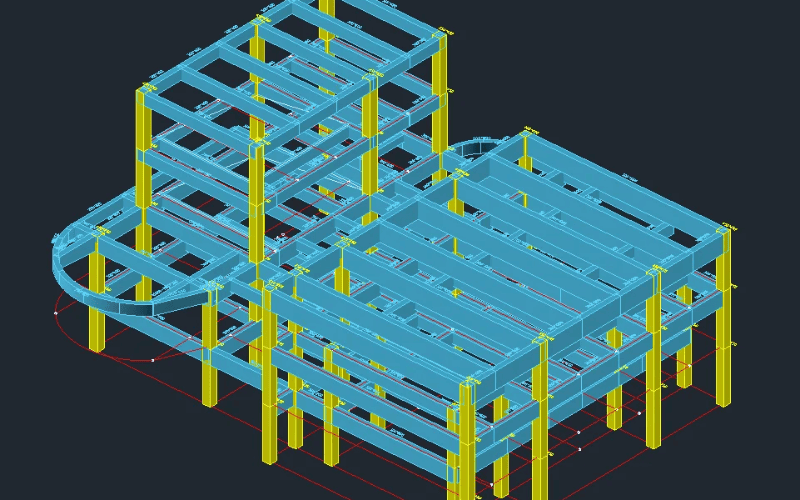
Advantages of Steel Structures
High Strength and Durability
Steel structures provide exceptional strength-to-weight ratios, rendering them ideal for applications that require heavy loads. Steel is resistant to corrosion and weathering, ensuring long-term durability, even in extreme environments like coastal areas or industrial zones.
Malleability and Flexibility
Steel’s malleability allows it to be shaped into a variety of forms, offering great design flexibility. It is easy to modify or expand steel structures, making them ideal for projects that may need future adaptation or extension.
Seismic Resistance
Steel structures perform exceptionally well during earthquakes. Their ability to bend and absorb energy, along with their lightweight design, allows them to withstand seismic forces better than other materials, reducing the risk of collapse.
Faster Construction
Steel structures are pre-fabricated off-site, which considerably accelerates the construction timeline. Unlike traditional building methods, the quick assembly of pre-made steel components results in shorter project timelines and reduced labor costs.
Disadvantages of Steel Structures
- High Initial Cost: Steel structures are more expensive upfront compared to other materials like wood or concrete due to the cost of raw steel and fabrication.
- Corrosion Risk: Steel is susceptible to rust and corrosion, particularly in humid or coastal environments, necessitating regular maintenance and the application of protective coatings.
- Thermal Conductivity: Steel conducts heat and cold, which can lead to temperature fluctuations inside buildings unless proper insulation is applied.
- Fire Risk: While steel is fire-resistant, it can lose its strength at high temperatures, making fireproofing treatments necessary for certain applications.
- Complexity in Design and Fabrication: Steel structures often require precise engineering and specialized fabrication, which can add time and complexity to the design process.
Related Reading: Pros & Cons of Steel Buildings
Applications of Steel Structures
Application Area | Specific Applications |
High-rise Buildings | Office buildings, hotels, apartments, commercial skyscrapers |
Large Span Buildings | Sports arenas, airport terminals, exhibition halls, convention centers |
Industrial Buildings | Factories, warehouses, power plants, oil platforms, cold storage |
Bridges | Highway bridges, railway bridges, pedestrian bridges, dam bridges |
Towers | Communication towers, broadcast towers, power transmission towers |
Offshore Platforms | Offshore drilling platforms, wind energy platforms |
Temporary Structures | Storage sheds, temporary exhibition halls, event venues |
Other Specialized Structures | Airport runways, warehouse roofs, stage structures, billboards |
Related Reading: Application of Steel Structures
Challenges and Considerations of Steel Structures
Cost of Steel Structures
While steel structures offer numerous advantages, they come with higher initial material costs compared to other construction methods. Steel itself is more expensive than wood or concrete, and the cost of fabrication and transportation can also add up. Furthermore, regular maintenance, especially in severe environments, can elevate long-term costs owing to the necessity for frequent inspections, treatments, and repairs.
Corrosion Issues of Steel Structures
Steel becomes susceptible to corrosion when exposed to moisture, oxygen, or specific chemicals. To mitigate this, protective coatings such as galvanization, paint coatings, or corrosion-resistant alloys (e.g., stainless steel) are often used. Consistent maintenance and re-coating are essential to guarantee the prolonged lifespan of the structure, particularly in coastal or industrial regions where corrosion rates are elevated.
Environmental Impact of Steel Structures
Steel production is extremely energy-intensive and contributes significantly to greenhouse gas emissions, thereby having an impact on the environment. However, steel is 100% recyclable, which helps reduce its long-term environmental impact. Advances in green steel production, such as the use of hydrogen instead of coal in steelmaking, aim to reduce carbon emissions and improve the sustainability of steel manufacturing.
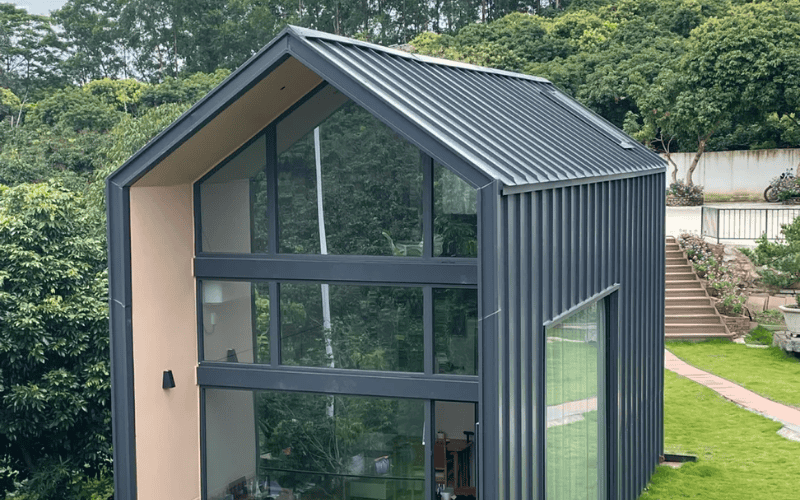
Steel Structure Lifespan and Maintenance
How long can the steel structure last?
Steel structures are renowned for their extended durability, frequently enduring for 50 to 100 years or longer when adequately maintained. The lifespan depends on various factors, including the quality of the materials used, environmental conditions, and maintenance practices. Routine inspections and prompt repairs can considerably prolong the life of a steel structure.
How to maintain steel structure
- Corrosion Protection: Routine re-application of paint or galvanization is crucial to prevent rust and corrosion, particularly in coastal or industrial regions.
- Structural Inspections: Periodic inspections for cracks, wear, and tear, particularly in joints and connections, are necessary to ensure the structure’s safety and integrity.
- Cleaning and Lubrication: Steel components, such as joints and moving parts, require cleaning and lubrication to prevent buildup of debris and to ensure smooth operation.
- Upgrades and Modifications: As building codes evolve, steel structures may need to be upgraded or modified to comply with new regulations or accommodate changes in use.
Related Reading: Steel Structure Maintenance
The Development Process of Steel Structure
Steel Structure History
Steel structures history began to emerge during the Industrial Revolution in the 19th century. The Eiffel Tower (1889) and the Brooklyn Bridge (1883) are iconic examples of early steel constructions. These pioneering projects demonstrated the strength and versatility of steel, leading to its widespread adoption in skyscrapers, bridges, and industrial buildings throughout the 20th century.
With advancements in steel production techniques, such as the Bessemer Process and the development of welded connections, steel structures grew in complexity and scale, supporting the rise of modern architecture and large-scale infrastructure.
Future Trends of Steel Structures
The future of steel structures is marked by innovation in material science and construction technologies. Key trends include:
- High-Performance Steel: Development of stronger, lighter, and more durable steel alloys will enhance the performance and sustainability of structures.
- Sustainable Steel: Initiatives aimed at decreasing the carbon footprint of steel production, such as the development of green steel and the utilization of recycled materials, are anticipated to steer the industry towards greater environmental accountability.
- Smart Steel Structures: The integration of smart technologies, such as sensors and BIM (Building Information Modeling), will allow for better monitoring, maintenance, and optimization of steel structures.
Choose SteelPRO PEB, Gain Quality, Speed & Customized Solutions
At SteelPRO PEB, we stand out by providing high-quality steel buildings that are designed for maximum efficiency, durability, and cost-effectiveness. Our products are customized to satisfy the distinct requirements of each project, whether they are for commercial, industrial, or residential applications.
What Makes Us Different:
- Superior Quality: We employ premium materials and advanced fabrication techniques to guarantee that each structure is constructed for enduring performance.
- Customization: Our team of experts collaborates closely with you to devise a steel structure solution tailored to your precise needs, from the initial concept to the final installation.
- Quick Turnaround: By leveraging our streamlined fabrication and prefabrication processes, we ensure that projects are delivered on time and within budget, minimizing downtime and maximizing your return on investment.
- Full Support: From consulting and design to post-installation services, SteelPRO PEB offers comprehensive support, providing ongoing maintenance and assistance to ensure sustained performance over time.
Choose SteelPRO PEB for your next steel structure project and experience the difference in quality, service, and efficiency that only a true industry leader can provide.