During the design, production, installation and use process, if not properly controlled, steel structures may have some quality problems, affecting the safety and service life of the structure. We will introduce common quality problems in steel structures and their preventive measures to help you better understand and deal with these challenges.
10 common quality problems and causes of steel structures
1. Material quality problems
Problems: steel strength does not meet the standard, chemical composition is not qualified, surface defects (such as cracks, rust), etc.
Reason: material procurement is not standardized, supplier quality control is not strict, or steel is not selected according to design requirements.
2. Welding quality problems
Problems: Weak welds, pores, slag inclusions, cracks, incomplete penetration or weld nodules, etc.
Reason: welding process is not standardized, welder technology is not up to standard, or welding environment (such as humidity, temperature) is not suitable.
3. Installation accuracy problems
Problems: large component installation deviation, loose bolt connection, node misalignment, etc.
Reason: inaccurate construction measurement, non-standard installation process, or construction is not carried out according to design drawings.
4. Anti-corrosion and fire prevention problems
Problems: the anti-corrosion coating on the surface of the steel structure falls off, the thickness is insufficient, or the fire-retardant coating does not meet the fire resistance requirements.
Cause: The anti-corrosion and fireproofing process is not standardized, the material quality is not up to standard, or the construction environment does not meet the standards.
5. Deformation problem
Problem: The steel structure is deformed by bending, twisting, etc. during transportation, installation or use.
Cause: Insufficient design strength of components, improper transportation or hoisting, or excessive external load.
6. Connection problem
Problem: Bolts are loose, fall off, or high-strength bolts do not meet the preload requirements.
Cause: Unqualified bolt quality, non-standard installation process, or failure to perform tightening inspection as required.
7. Fatigue problem
Problem: Fatigue cracks occur in steel structures under long-term cyclic loads.
Cause: Fatigue strength is not fully considered in the design, or the load exceeds the design range during use.
8. Design problem
Problem: Unreasonable structural design leads to stress concentration, insufficient stability or uneven load distribution.
Cause: Design calculation errors, failure to fully consider actual use conditions, or lax implementation of design specifications.
9. Environmental impact issues
Problem: Steel structures are prone to rust in humid and corrosive environments, or lose strength at high temperatures.
Cause: No effective anti-corrosion measures were taken, or steel suitable for environmental conditions was not selected.
10. Construction management issues
Problem: Lax quality control during construction leads to accumulation of quality problems.
Cause: Irregular construction management and lack of effective quality supervision and testing mechanisms.
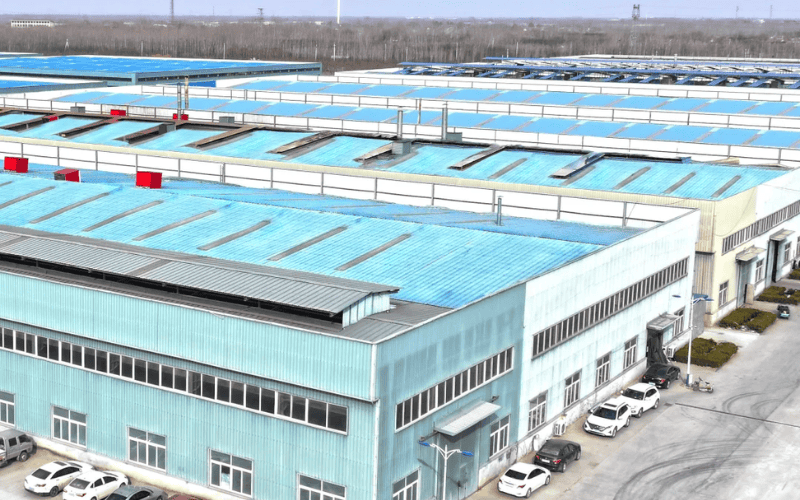
How to ensure the quality of steel structure?
The quality of steel structure is the core of building safety and durability. To guarantee that every project attains the highest standards, we rigorously oversee every stage, from material selection to the completion of construction. The following are the key measures we take in actual work:
1. Material selection
Steel grade: We select steel grades that meet the design requirements, such as Fe 415, Fe 500, etc., to ensure that the strength and performance of the steel can meet the project requirements.
Specifications and performance: All types, specifications and performance of steel strictly comply with national standards to ensure the consistency of materials.
Surface inspection: Before the material enters the site, we will carefully check the surface of the steel to ensure that there are no defects such as cracks, slag inclusions, and delamination to avoid affecting the overall quality due to material problems.
2. Design and drawing review
Drawing review: Before construction, our technical team will conduct a detailed review of the design drawings to ensure that they meet national standards and project requirements.
Technical disclosure: Before construction, we will fully communicate with the design team and the construction team to clarify the technical requirements and ensure that every link can be executed as planned.
3. Welding and connection quality
Welding process: We strictly follow the BS EN ISO 3834 standard to ensure that every weld meets the highest quality requirements.
Welder qualifications: All welders hold valid qualification certificates to ensure the professionalism and reliability of welding operations.
Connection quality: We use high-strength bolts and ordinary bolts, and check the connection quality through hole trimming equipment to ensure that each connection point is firm and reliable.
4. Anti-corrosion and fire-proof coating
Anti-corrosion coating: We sandblast the steel surface to ensure that the coating adheres firmly and the anti-corrosion effect is optimal.
Fire-proof coating: According to the design requirements, we apply fire-proof coating in layers to ensure that the fire resistance limit of the steel structure meets the standard and provide additional safety for the building.
5. Installation and construction quality control
Installation process: From the installation of foundation anchor bolts to the hoisting of steel columns and steel beams, we strictly follow the specifications to ensure that every step is accurate and correct.
Calibration and adjustment: We use a level and theodolite to calibrate the verticality and horizontality of the steel structure to ensure the overall stability of the building.
6. Documentation and Traceability
Material Certificates: We keep detailed records of the quality certification documents for each batch of steel, bolts, coatings and other materials to ensure that every piece of material is well documented.
Inspection Reports: We provide complete inspection reports, including welding inspections, coating inspections, installation inspections, etc., to ensure that every link is strictly checked.
Before leaving the factory, we ensure that
- All materials and quality documents are complete and compliant to ensure that each component delivered is safe, reliable and durable.
- The steel surface is free of cracks, rust, and slag inclusions, and the welding quality meets the BS EN ISO 3834 standard.
- The thickness of the anti-corrosion and fire-retardant coating meets the standard, 150 microns outdoors and 125 microns indoors, to ensure long-term protection.
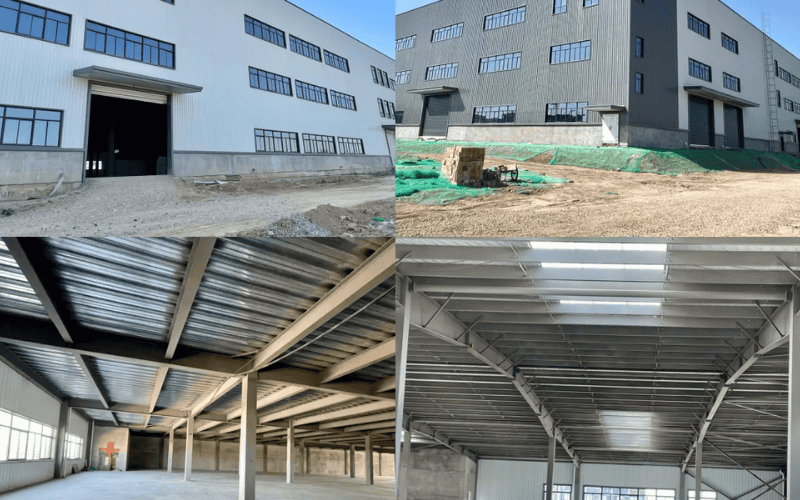
How do customers check the quality of steel structures by themselves after receiving the goods?
When customers receive steel structure products, quality inspection is an important part of ensuring that the products meet the requirements and safety standards. Here are some basic steps that customers can follow to check the quality of steel structures by themselves:
1. Appearance inspection
- Surface treatment: Check whether the surface of the steel structure has rust, cracks, scratches or other obvious defects. Pay special attention to the uniformity of the coating to ensure that the anti-corrosion coating is intact and prevent the steel from being corroded by oxidation.
- Welding quality: Check the appearance of the welding part, and the weld should be smooth and uniform. The welded part should be devoid of defects such as cracks, pores, and incomplete penetration.
- Parts identification: Check whether the parts are identified and numbered according to the requirements of the drawings to ensure that they can match the design documents.
2. Size and tolerance inspection
Use a tape measure or laser rangefinder to check whether the dimensions of each steel structure component meet the design requirements. Including length, width, thickness, etc.
- Angle and verticality: Use a level and angle ruler to check the angle and verticality of the steel structure to ensure the flatness and stability of the structure.
3. Strength and durability inspection
- Weight inspection: Check whether the material of the steel structure meets the standards by weighing or comparing with the design weight. In particular, important load-bearing components must ensure that they are strong enough.
- Material inspection: Suppliers can be asked to provide material warranty or material certificate to ensure that the type and quality of the steel meet the specified standards.
4. Connection inspection
- Bolt connection: Check whether all bolts and connectors are tightened in place and there is no looseness. The type and specification of the bolts should be consistent with the design.
- Welding and riveting points: For welding or riveting parts, their quality should be checked to ensure that the connection is stable and without any defects.
5. Trial assembly and splicing
- Assembly test: A small range of trial assembly can be carried out to ensure that there are no problems with the docking and connection of steel structure components, and there are no obvious errors at the connection.
- Splicing test: Splice the main components to check whether they match, install smoothly, and whether the matching clearance between the components is reasonable.
6. Anti-corrosion and anti-rust inspection
- Coating thickness: Check the thickness of the coating through a coating thickness gauge to ensure that the coating meets the design requirements and has sufficient anti-corrosion protection.
- Anti-corrosion test: For some key parts, simple corrosion tests can be carried out, such as salt spray tests on the surface of components.
7. Material certification and inspection report
Require suppliers to provide material inspection reports, including the chemical composition and mechanical properties of steel. Confirm that the quality of steel meets relevant standards.
8. Use environment and structural adaptability inspection
According to the environment (such as humidity, large temperature difference, strong corrosion, etc.), check the adaptability of the steel structure and whether materials or protective measures suitable for the environment are used.
Attention!
When customers receive steel structure products, they must complete the inspection within a short period of time so as to find problems in time and communicate with the supplier to solve them. For important or complex structures, you can consider having a professional third-party agency conduct inspections to ensure that the product quality meets the relevant building standards and safety requirements.
High Quality Steel Structure Supplier
Want to ensure your steel structure will stand the test of time? We combine expert design, precision manufacturing, and rigorous quality inspections to ensure that the structure is not only safe but also durable.
Whether you are planning a new project or upgrading an existing one, our experienced team will provide you with a custom solution to meet your unique needs. Contact us today to discuss your project and get a custom quote – we will ensure your steel structure is in perfect condition from start to finish!