Warehouse design and build is more than just creating a large space to store goods—it’s about optimizing efficiency, workflow, and operational costs. A well-planned warehouse design ensures that storage, equipment, and processes work together seamlessly, improving productivity and reducing unnecessary expenses. Before getting started, it’s essential to carefully assess your specific needs and objectives to create a warehouse design and build plan that aligns with your business goals.
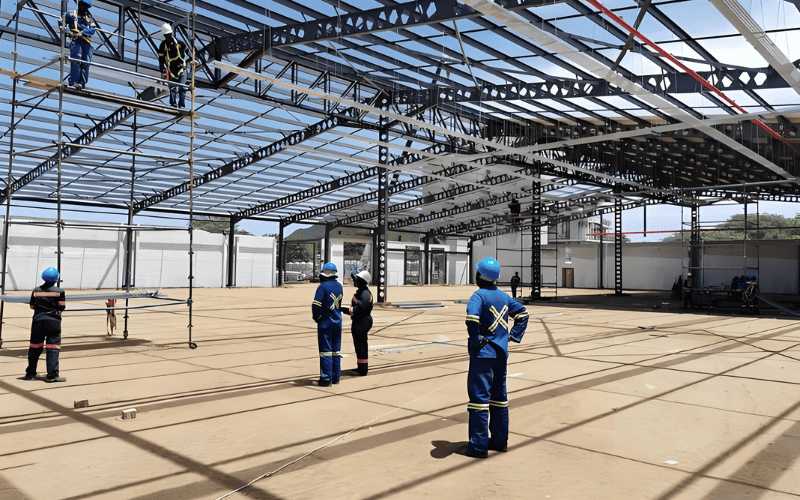
Our design principles focus on:
- Ergonomics of racking systems and equipment.
- Maximizing storage capacity and space efficiency.
- Streamlining material flow to minimize handling time.
- Flexibility for future growth and changes.
- Real-time inventory tracking for better management.
- Minimized worker interference for improved safety and productivity.
We will outline proven design strategies and essential requirements to ensure your warehouse operates efficiently and can scale for future growth. Let’s dive into how these principles are applied in practical, high-performance warehouse designs.
How to Plan Your Warehouse Project Before You Start
Planning your warehouse project is all about making the right choices early to ensure efficiency and future growth. Let’s dive into the key areas to consider.
Height and Clearance Considerations
Bay Spacing
Steel structure warehouse bay spacing typically ranges from 20 to 40 feet. We can also provide up to 50 feet for heavy machinery and large-scale operations. More space means easier movement and less clutter.
- Tip: In earthquake prone areas, seismic requirements should be considered in interval design. A smaller interval can improve the stability of the structure and reduce deformation under earthquake action
Framed Openings
Make sure framed openings are big enough for the largest vehicles or equipment that will pass through. It’s all about smooth access. When designing openings, ensure proper reinforcement, like extra support beams, to maintain the frame’s load-bearing capacity.
- Tip: The eaves height should be at least 2 feet above the highest framed opening to ensure proper clearance.
Load Considerations
- Live Load: The weight of people, equipment, and movable items.
- Dead Load: The weight of the structure itself, including walls, roofs, floors, and other permanent components.
- Snow Load: Based on your region’s snowfall, this will impact roof design.
- Wind Load: The wind pressure that the building must withstand, determined by location.
- Seismic Load: If you’re in an earthquake-prone area, the building must be designed to resist seismic forces.
Tip: Cargo distribution in a warehouse is often uneven, so design for the worst-case scenario to ensure the structure can handle the maximum possible load.
Codes and Permits
- Building Codes: Check your region’s local codes for load-bearing requirements, structural standards, and safety measures.
- Fire Rating: Your warehouse should meet fire-resistance standards. Confirm the required fire rating for walls, ceilings, and floors.
- Permits: Typically, you’ll need permits for construction, zoning, and occupancy. Apply through your local building authority or zoning office.
Site Analysis
Choose a location with strong, stable soil that can support the foundation. Poor soil may require deeper or more expensive foundations, like piles or drilled shafts, so an initial site survey is essential.
- Tip: A perc test checks soil drainage and helps assess the risk of swampy conditions. This is particularly important for areas with septic systems or water runoff concerns.
- Tip: Have a county health inspector oversee the perc test to ensure accuracy. Also consider water tables, soil type, and weather impact on long-term foundation stability.
Warehouse Building Design Effective Layouts
A well-planned warehouse design layout is key to maximizing efficiency, optimizing space, and ensuring smooth operations. Choosing the right warehouse layout design can streamline material flow, reduce congestion, and improve overall productivity. Here are four common warehouse design and layout options for steel warehouses:
U-flow Layout
In this layout, storage is in the center, with receiving and shipping at both ends. Material flows in a U-shape, reducing congestion. Ensure enough space at the corners for smooth transitions.
Ideal for: Manufacturing facilities, assembly lines, or warehouses needing quick, controlled access.
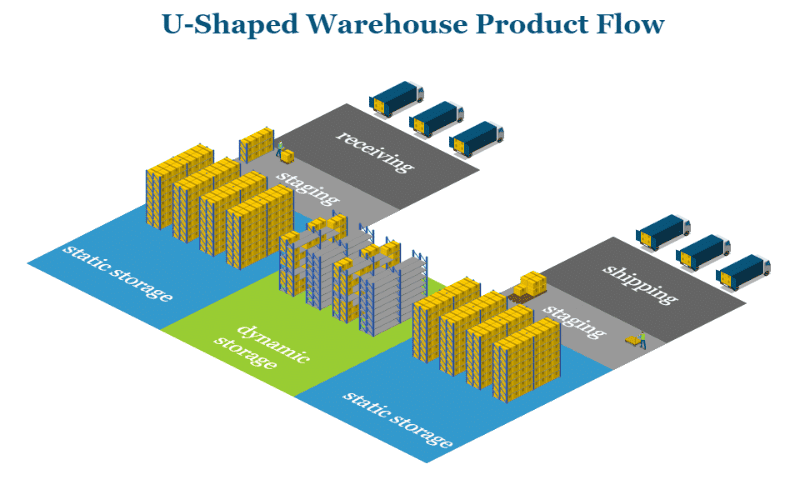
T-flow Layout
Receiving and shipping are placed at opposite ends, with storage in the middle. This layout minimizes cross-traffic, streamlining material handling.
Ideal for: Distribution centers, cold storage, and high-volume warehouses.
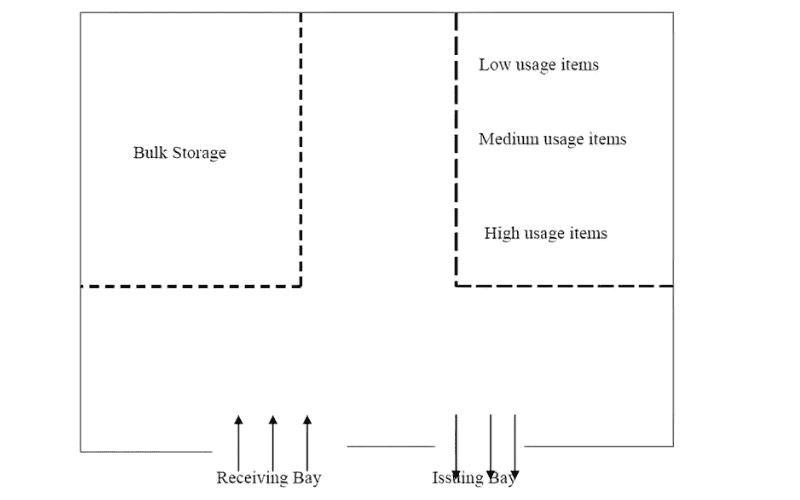
L-shaped Layout
Storage is positioned along two perpendicular walls, forming an L-shape. This warehouse layout design helps separate receiving, storage, and shipping zones while ensuring clear aisles for smooth material movement.
Ideal for: Warehouses with diverse product types, distribution centers, or facilities requiring distinct zones for different operations.
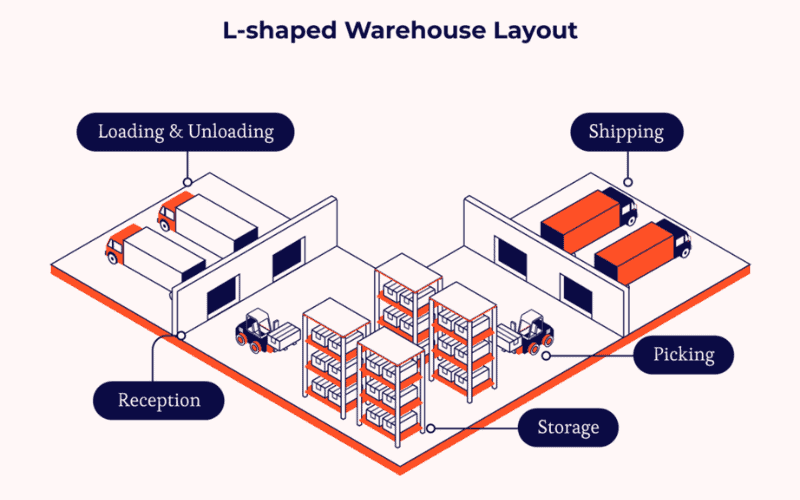
Straight-line Flow Layout
Workstations, storage, and aisles are arranged along one path, making inventory tracking and material flow straightforward.
Ideal for: E-commerce, order fulfillment, and high-turnover warehouses.
Selecting the right warehouse design and layout depends on your space, traffic patterns, and storage needs. A well-thought-out plan ensures smoother operations and better efficiency for long-term success.
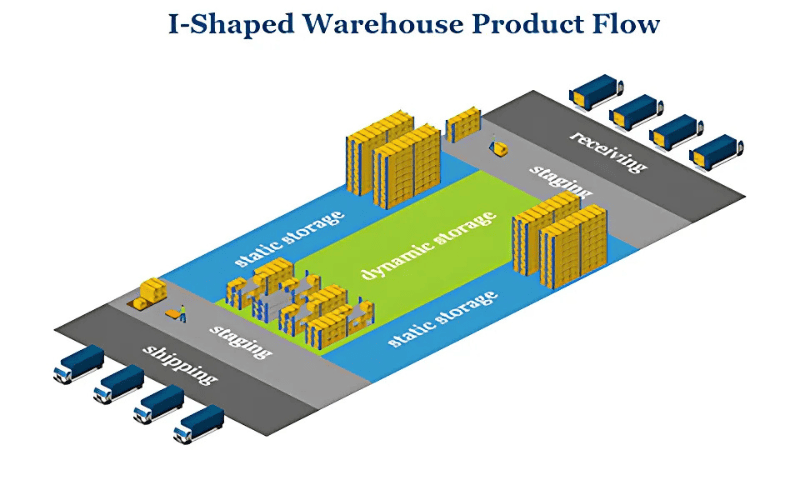
Warehouse Building Design
When designing a warehouse, several key factors determine its functionality and efficiency. The correct height, space, and other design elements are crucial for efficient operations and long-term sustainability. Here are our suggestions based on industry standards for steel structure buildings:
Warehouse Area Design
When designing the area of your warehouse, the size should allow for efficient space utilization and ease of movement. For general guidelines, the minimum recommended area for small-scale warehouses should be around 500 square meters (5,380 square feet). Larger warehouses designed for high-volume storage should exceed 2,000 square meters (21,530 square feet) to allow for sufficient operational space.
Warehouse Building Width
The width of the warehouse is directly tied to the operations inside. To ensure enough space for movement of goods, machinery, and personnel, a standard warehouse width should be between 15–30 meters (49–98 feet).
Warehouse Building Height
The minimum height for a warehouse should not be less than 6 meters (20 feet), depending on the type of goods being stored. Higher ceilings allow for better stacking and easier operation of handling equipment.
Warehouse Building Floor Design
Floor design must account for load-bearing capacity and material handling. A reinforced concrete floor with proper drainage and leveling will ensure smooth operations.
Warehouse Door Design
In addition to standard personnel doors, warehouses typically include various types of overhead doors, such as sectional or roll-up doors. Door dimensions should accommodate the size of vehicles and loads passing through.
Canopy Design
A canopy should be installed at loading docks or entrances to protect from the elements. The width should be at least 2.5 meters, and the height should not be less than 5 meters above the ground.
Warehouse Roof System Design
For optimal use of space and energy, we recommend steel warehouses with shallow-sloped roofs. These roofs not only ensure proper water drainage but are also ideal for integrating solar panels, maximizing energy efficiency. We specialize in steel warehouses designed to accommodate solar energy solutions, combining practicality with sustainability.
Related Reading: Steel Roof System: Composition & Design Points
Wall Options Design
Choosing the right wall material and insulation is crucial for durability and energy efficiency. Options such as steel cladding, insulated panels, or brick walls depend on your specific needs. We offer customizable wall panels to meet your requirements, ensuring both performance and aesthetics.
Warehouse MEP Systems
When designing a warehouse, it’s important to integrate crane and HVAC systems with the steel structure to ensure optimal functionality.
For cranes:
- Consider crane systems in the early design phase, ensuring beams, columns, and roof trusses can support the crane’s weight and movement.
- Make use of vertical space by placing storage in areas that allow the crane to move freely across the entire warehouse.
For HVAC systems:
- Position HVAC units in areas that don’t interfere with crane operations.
- Ensure HVAC equipment is easily accessible for maintenance and repairs, avoiding locations that would complicate future servicing.
If you want to learn about the structural design of steel structure warehouses, please read: Steel Warehouse Structure: Key Design Features and Characteristics
Expert Warehouse Building Manufacturer
If you’re facing challenges with warehouse design or seeking a reliable partner to handle both your steel structure needs and design requirements, we are here to help. As a leading steel structure manufacturer, we provide high-quality, prefabricated components and customized design solutions tailored to your specific needs. Our expertise ensures your warehouse will meet today’s operational demands and be adaptable for future growth.
Visit our project page to see more of our successful steel structure warehouse designs. Let us help you bring your warehouse vision to life with efficient, cost-effective, and scalable solutions.