When considering light steel framing for your construction project, it’s natural to ask: “What are the real benefits? What challenges should I expect? And, is it truly the right choice for my needs?” Let’s get straight to the point.
The Pros:
- Lightweight and Strong
- Streamlined Construction
- Durable and Low-maintenance
- Flexible and Space-Saving Design
- Eco-Friendly and Sustainable
- Resilient in Extreme Conditions
- Modern Technology Compatibility
- Water-Tight and Air-Tight
The Cons:
- High Thermal Conductivity
- Higher Initial Costs
- Limited On-Site Adjustments
- Reliance on Supplementary Materials
- Energy-Intensive Production
Sounds simple enough, right? But here’s the twist: Many of the things you might think are drawbacks of light steel framing are actually misconceptions. For example: “Steel will rust.” “Steel is noisy.” “It’s only for industrial use.”
If you’ve ever been unsure about whether light steel framing is right for your project, stick around. We’re about to clear up misconceptions, dive deeper into its advantages, and give you all the facts you need to make an informed decision.
The Pros of Light Steel Framing
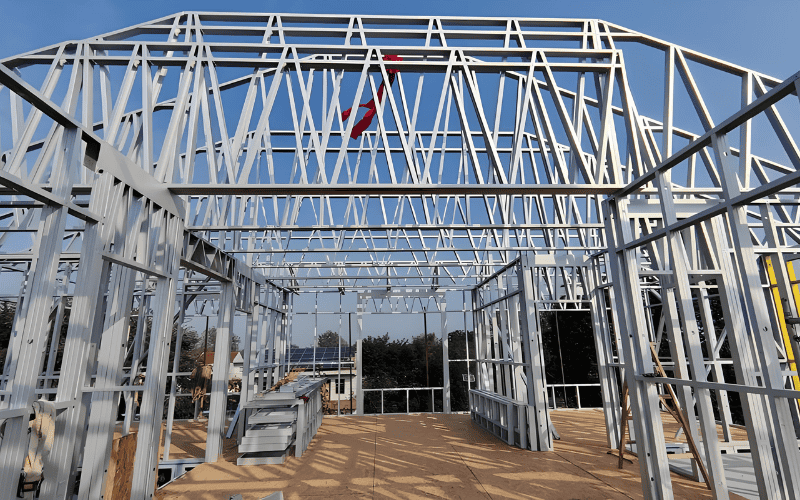
1. Lightweight and Strong: Save Money and Build Faster
Light steel framing is approximately 30% lighter than timber, yet significantly stronger. This combination means easier transportation, quicker installation, and less labor on-site. For owners, it translates into lower costs and faster project completion.
2. Streamlined Construction: Speed and Precision
Thanks to its modular, prefabricated design, light steel framing ensures fast, efficient construction with minimal errors. Factory-made components reduce delays and provide better control over timelines and budgets, making it a great choice for projects that demand speed and reliability. It’s even ideal for temporary structures like modular housing or site offices.
3. Durable and Low Maintenance: Built to Last
Steel resists fire, moisture, pests, and decay, offering long-lasting protection with minimal upkeep. Treated with protective coatings, it performs exceptionally well in humid or coastal areas, cutting down on repair costs. Plus, its durability means it can be reused or recycled, providing both environmental and economic benefits at the end of its lifecycle.
4. Flexible and Space-Saving Design: Get the Most Out of Your Building
Light steel framing supports open layouts and adaptable designs, perfect for modern homes or high-rise buildings. Its slim yet strong walls maximize usable interior space, which is especially valuable in urban projects. Additionally, its flexibility allows for easy future expansions, like adding new floors or extending wings, with minimal disruption.
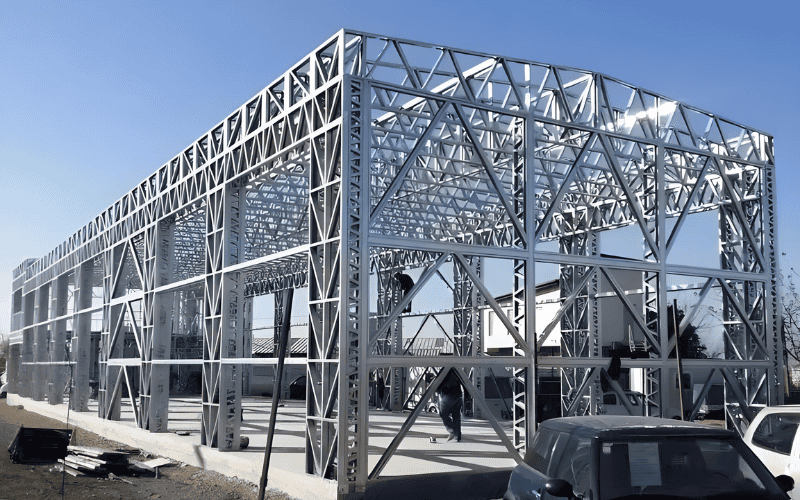
5. Eco-Friendly and Sustainable: A Green Choice for Builders
Steel is 100% recyclable, and many light steel framing projects use up to 85% recycled materials. This significantly reduces waste during production and construction, making it a top choice for eco-conscious builders. Its ability to be repurposed or recycled at the end of its lifecycle also adds long-term economic and environmental benefits.
6. Resilient in Extreme Conditions: Stability You Can Count On
Light steel framing is designed to withstand earthquakes, hurricanes, and other harsh conditions. Its flexibility absorbs shocks during seismic events, making it a reliable choice in regions like Japan or New Zealand. Strong connection systems also ensure stability in high winds, while its ability to support long spans without extra support makes it perfect for large commercial buildings, industrial spaces, and even bridges.
7. Modern Technology Compatibility: Smarter Building Solutions
Light steel framing works seamlessly with tools like Building Information Modeling (BIM), allowing for precise designs and reduced on-site conflicts. This integration streamlines project execution and ensures high-quality results.
8. Water-Tight and Air-Tight: Perfect for Specialized Needs
The non-porous nature of steel makes it ideal for structures requiring water-tight or air-tight properties. Whether it’s pipelines, reservoirs, or energy-efficient buildings, light steel framing ensures superior sealing and lasting performance.
Misconceptions About Light Steel Framing
Before diving into the actual disadvantages, let’s address some common myths. You might be surprised to learn that some of the ‘downsides’ of light steel framing aren’t true—or at least not as problematic as they seem.
“Steel Is Too Expensive”
While initial costs may be higher, steel’s long-term durability, pest resistance, and lower maintenance needs often save money in the long run. Studies show steel-framed buildings can cut maintenance costs by 20%-30% over their lifespan compared to wood-framed structures.
“Steel Frames Will Rust”
Modern steel frames come with advanced rust-preventive measures, like galvanization or zinc-aluminum coatings, making them highly resistant to corrosion. Regular inspections and proper design further ensure long-term durability.
“Steel Frames Make Buildings Less Stable”
Engineered for strength, light steel structure is highly stable, even in seismic-prone areas. Its ductility helps absorb shocks during earthquakes, reducing the risk of structural failure. In fact, it’s a top choice in earthquake-resistant construction.
“Light Steel Framing Is Only for Industrial Buildings”
Not true. Light steel framing is widely used in homes, offices, schools, and even modular housing projects. Its flexibility, sustainability, and speed make it a versatile solution for all kinds of buildings.
“Steel Framing Interferes with Signals”
Steel framing doesn’t block Wi-Fi or mobile signals. Issues with signal interference are more often caused by dense walls or reflective surfaces, not the steel itself. Proper design ensures strong, uninterrupted signals.
“Steel Framing Is Noisy”
Concerns about noise arise during construction or due to poor installation. With proper assembly and insulation, steel-framed buildings are no noisier than those made of wood or concrete, ensuring a comfortable living or working environment.
Related Reading:
Is Steel Good for Soundproofing? This Might Not Be What You Think
The Cons of Light Steel Framing
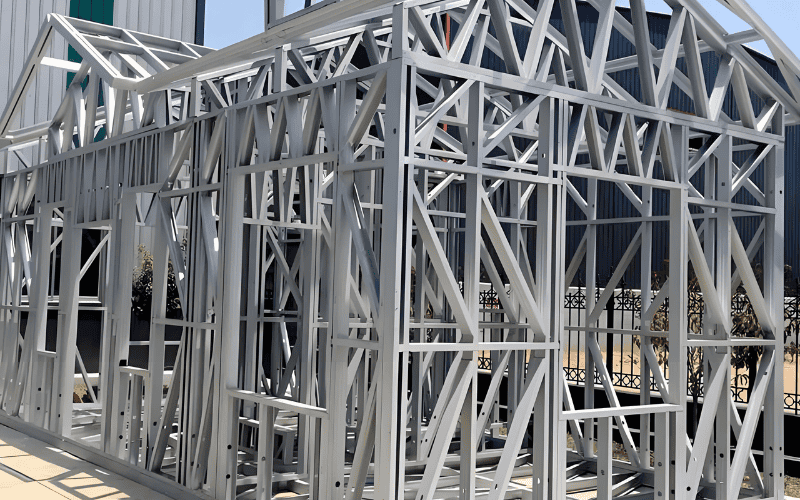
1. High Thermal Conductivity: Watch Your Energy Costs
Steel transfers heat easily, which can make buildings warmer in summer and cooler in winter. Without proper insulation, energy costs may rise.
Solution: Use advanced insulation like thermal breaks or reflective barriers to enhance efficiency.
2. Initial Costs: Think Long-Term
Light steel framing typically costs 20%-30% more upfront compared to timber, especially in smaller projects. However, its durability and low maintenance can save money over time.
Solution: Weigh upfront expenses against long-term benefits, especially for projects with long lifespans.
3. Limited On-Site Adjustments: Precision Is Key
Prefabricated steel components are precise but hard to modify on-site. Last-minute changes may cause delays or extra costs.
Solution: Thorough pre-construction planning and accurate measurements are crucial.
4. Dependence on Supplementary Materials: Adds Complexity
Steel frames need additional materials like drywall, insulation, and sheathing for full functionality, which can increase project complexity.
Solution: Integrated wall systems can simplify construction and save time.
5. Environmental Impact of Production: Recyclability Balances It Out
Steel production requires significant energy, raising concerns about its environmental footprint. However, steel’s recyclability and durability help offset this over time.
Solution: Opt for suppliers using recycled steel and ensure end-of-life recycling of components.
Factors to Consider Before Choosing Light Steel Framing
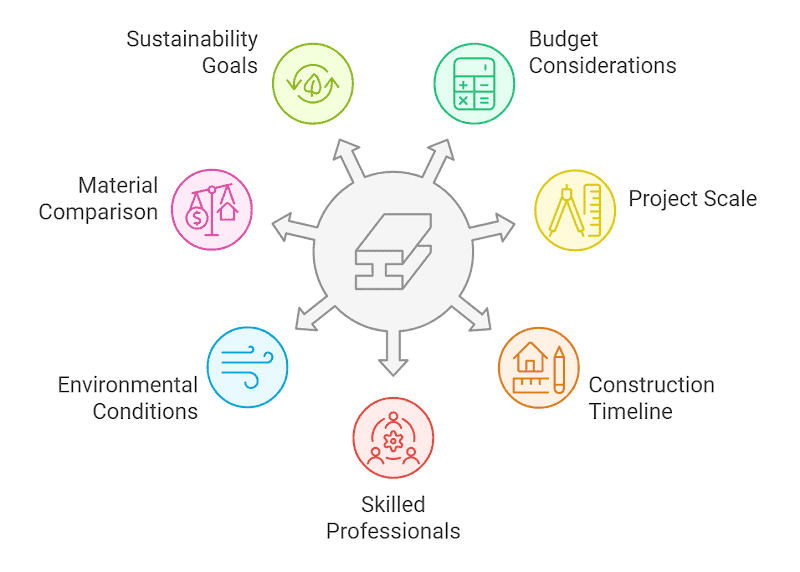
1. Budget: Balancing Initial Costs and Long-Term Savings
Why It Matters: Light steel framing often has higher upfront costs compared to wood or concrete. However, its durability, pest resistance, and reduced maintenance costs can offset these expenses over time.
How to Assess:
- Calculate material, labor, and supplementary material costs (e.g., insulation, drywall).
- Compare long-term savings from reduced repairs and maintenance.
- Ask: Am I planning for a short-term or long-term investment?
2. Project Scale and Complexity: Is It a Good Fit for Your Needs?
Why It Matters: Light steel framing is ideal for projects requiring precision, large spans, or modular construction. For small or highly customizable projects, the prefabrication process may feel restrictive.
How to Assess:
- For large-scale projects: Evaluate the benefits of prefabrication and speed.
- For small projects: Ensure the design flexibility aligns with your needs.
- Ask: Does my project require the structural strength or design flexibility of steel framing?
3. Construction Timeline: How Important Is Speed?
Why It Matters: Light steel framing can reduce construction time by 30%-50% compared to traditional methods, making it ideal for time-sensitive projects.
How to Assess:
- Determine if a fast project completion is critical for your goals.
- Consider whether prefabrication and modular installation can align with your schedule.
- Ask: Will saving time on-site reduce overall costs or disruptions for my project?
4. Access to Skilled Professionals: Is the Right Team in Place?
Why It Matters: Steel framing requires precision during design, prefabrication, and installation. Inexperienced teams may lead to delays or costly errors.
How to Assess:
- Research contractors experienced with light steel framing.
- Confirm that your team has access to specialized tools and expertise.
- Ask: Do I have access to professionals who can handle the complexity of steel framing?
5. Environmental Conditions: Match the Material to Your Climate
Why It Matters: Steel performs well in fire-prone, pest-infested, or high-humidity areas but requires proper insulation in extreme climates.
How to Assess:
- Evaluate local climate challenges like moisture, temperature extremes, or fire risks.
- Ensure that the chosen steel framing includes protective treatments like galvanization.
- Ask: Does my project location benefit from steel’s durability and resistance?
6. Material Comparison: Is Steel the Right Choice Over Alternatives?
Why It Matters: Light steel framing offers unique advantages, but every material has trade-offs. For example:
- Compared to Wood: Steel is more durable and resistant to pests but less flexible for on-site changes.
- Compared to Concrete: Steel is faster to install but may require additional insulation.
How to Assess:
- Compare key criteria like cost, durability, energy efficiency, and speed for your project.
- Ask: What material best fits my priorities—cost, timeline, or performance?
7. Sustainability Goals: Are You Prioritizing Eco-Friendly Construction?
Why It Matters: Steel is highly recyclable, and its durability reduces waste over the building’s lifecycle. However, its production can be energy-intensive.
How to Assess:
- Look for suppliers that use recycled steel and sustainable manufacturing processes.
- Evaluate the building’s full lifecycle environmental impact.
- Ask: Does this material align with my sustainability objectives?