The construction industry is facing growing pressure to reduce waste, speed up projects, and adapt to ever-evolving demands. Modular construction offers a smarter, more efficient solution, cutting material waste, shortening timelines, and providing flexibility that traditional methods can’t match.
As Tom Hardiman, Executive Director of the Modular Building Institute, pointed out in a recent podcast, the industry has tripled its market share over the past seven years, driven by growing demand in sectors like healthcare, education, and housing. With its benefits of speed, efficiency, and sustainability, modular construction is becoming a key solution to address housing shortages.
While challenges like regulatory barriers remain, the potential for modular construction to reshape the future of building is undeniable. The future of building is modular—let’s explore why.
Sustainability Benefits
Traditional construction methods often lead to significant material and energy waste, with frequent on-site cutting generating large amounts of hard-to-recycle scraps. In contrast, modular construction improves material efficiency by around 30%, especially with resources like wood, steel, and plastic. This factory-based approach ensures that materials are used more effectively, reducing waste and optimizing resources.
Additionally, many modular construction companies are adopting clean energy solutions. For example, our factories are now installing solar panels on the rooftops, using renewable energy to power production and further lowering carbon emissions. This approach aligns with our innovative solar power warehouse designs, which integrate renewable energy systems directly into the building, offering clients sustainable and cost-effective solutions.
Another major benefit of modular buildings is their durability. Steel modular buildings, like the ones we produce, can last up to 50-70 years—well beyond the 50 years typical for brick-and-mortar structures. This extended lifespan reduces the need for frequent demolition and rebuilds, helping cut down on resource waste and construction debris.
Related Reading: Modular Construction: Driving Innovation in Renewable Energy
Speed and Efficiency
- Faster Construction
Modular construction can speed up building timelines by as much as 50%. In controlled factory environments, components are pre-built, cutting down on delays and inefficiencies typical in traditional construction. For example, hospitals and schools can be completed in months, not years—a crucial factor in emergencies like pandemics. - Parallel Construction
With modular building, site preparation and module production happen simultaneously, slashing the overall project timeline. This “overlap” between different stages means that construction transitions more quickly from breaking ground to full occupancy. - Optimized Resource Use
Precision in material measurement and cutting reduces waste, leading to lower costs and less environmental impact. Factory-controlled conditions make better use of materials. A study published in the Sustainability journal found that in China, modular construction methods reduced wood formwork usage by 87% and water consumption by 70% compared to traditional building methods.
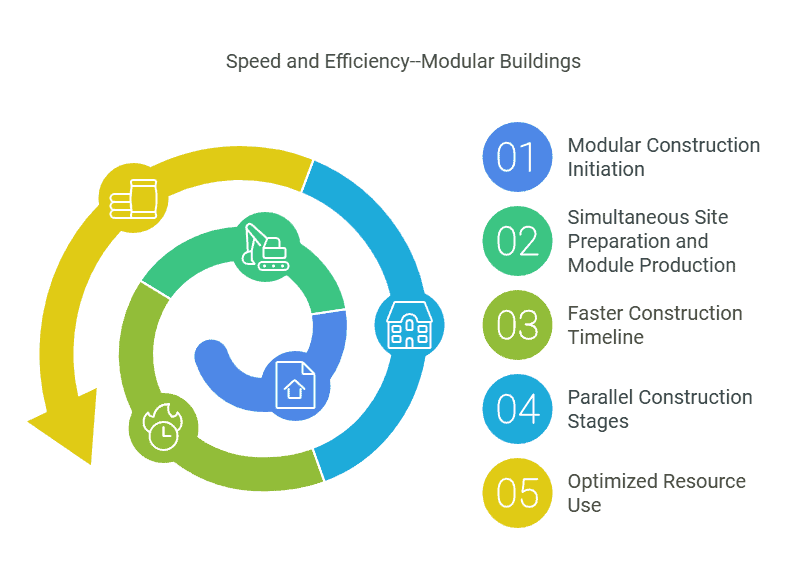
Flexibility and Adaptability
Modular construction is super flexible, letting buildings be reconfigured or upgraded as needs change. It can quickly respond to market shifts or user demands, delivering great conversion rates and long-term value for owners.
Modular buildings offer clear advantages over traditional hybrid structures, especially in fast-growing cities:
In cities driven by resources, like mining towns, populations shift with the industry. Modular buildings can be moved, reassembled, and ready to go—no need to leave them abandoned like traditional buildings. It’s a smart way to manage urban resources.
During urban renewal, modular construction blends right into old neighborhoods. Whether it’s a temporary shopping spot or a community center, these buildings go up fast and can be moved when needed. It’s all about staying in sync with the fast pace of the city.
In crowded city centers, small spaces often go to waste. Modular buildings can be custom-fit into these areas—think coffee stands or news kiosks—giving life to those “forgotten” corners. Traditional construction can’t pull that off.
Efficient Quality Control
In modular construction, factory-controlled environments keep things steady with consistent temperature and humidity, so materials perform better. The molds used are super precise, ensuring everything fits perfectly with minimal errors.
Quality control is tight: welds are tested, and concrete samples are checked for strength during production. This catches problems early, unlike traditional construction, where material sourcing can be hit or miss. Modular builders either manage this in-house or team up with trusted partners, so quality is always high. This translates to fewer repairs in the future and a higher return on investment.
Integration with High-Tech Innovations
Modular construction is now tapping into high-tech solutions like 3D printing, 3D modeling, and smart home devices. These technologies make building faster, more efficient, and tailored to today’s needs.
For example, modular buildings can integrate solar panels and wind turbines. With smart energy systems, these buildings can produce and store their own power. Any extra energy can be fed back into the grid, cutting down on traditional energy use, lowering carbon emissions, and offering both financial and environmental perks. This is where sustainability meets innovation.
Design Innovation in Modular Buildings
Gone are the days of dull, one-size-fits-all designs. Today’s modular buildings are fully customizable, blending style and functionality. Whether you want modern sleekness or a traditional look, modular construction fits any need, from residential to commercial to institutional projects.
Buildings are no longer just boxes. Now, we see dynamic curves and layered designs. Take The Ribbon building—its smooth, flowing lines created with parametric design tools make it both artistic and memorable.
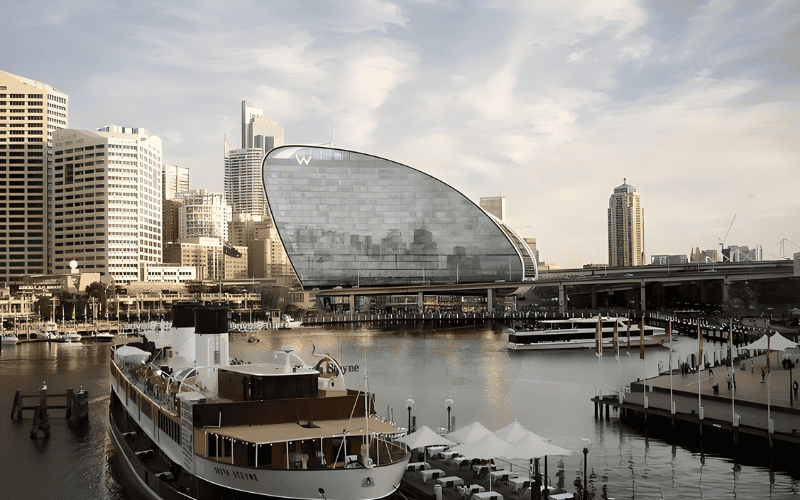
Another example is My Micro, which packs 55 tiny apartments into a small space. Designed with the Mini Tower Concept, it uses four shades of grey brick to maximize the limited 260–360 square feet. It’s a great example of how modular design turns small spaces into functional and stylish living areas. Modular buildings today are proving design has no limits!
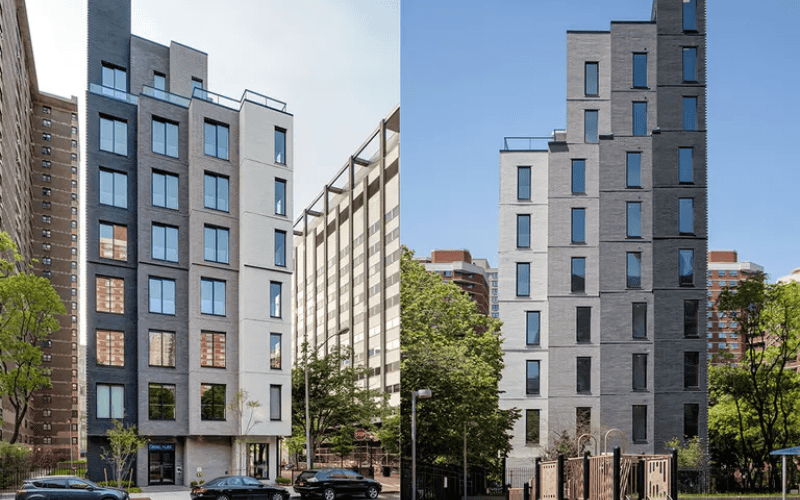
Source: https://www.perplexity.ai/
Link:https://www.perplexity.ai/search/xian-zai-wo-xiang-yao-xie-yi-p-7P.RPaazReeBACPSxmme_w
Challenges Still Ahead for Modular Construction
Modular construction has clear advantages, but some challenges still remain, especially in transportation and logistics. While we’ve developed flexible methods to disassemble large modules into compliant sizes for easier transport, local regulations like height and width limits still create roadblocks. To address this, we need to collaborate across industries—transportation, road management, and construction—to create dedicated transport routes and adapt infrastructure where necessary.
At the same time, delays in communication between suppliers, transporters, and construction sites can cause unnecessary hold-ups. To fix this, better information flow and coordination between all parties is key.
Some designers stick to traditional methods, resulting in conservative designs. However, our talented team has broken these boundaries, combining modern styles and steel structures to create unique modular buildings. We believe the industry should encourage designers to learn about smart manufacturing and parametric design to reshape modular architecture’s aesthetics and functionality.
Modular Buildings Still Have Future Prospects
Modular construction holds a bright future for faster, more sustainable building, but it’s not a one-size-fits-all solution. Some regions or projects may need more time to adapt, and not every building type is suited for this approach. That said, the future of construction is modular, and we’re already seeing it shine through projects like our Modular Apple Cabin and Portable classrooms. The full potential will take time to realize, but we’re excited to be part of that journey!