Once you’ve decided that modular construction is the right approach for your building project, the next big question is: which modular solution is the best fit? The choices can seem overwhelming, but don’t worry—we’re here to guide you every step of the way. With years of experience in modular building solutions, we’re here to help you make an informed decision that perfectly suits your needs.
What Modular Construction Solutions Are Available?
Once you’ve chosen modular construction, the next step is selecting the right solution. There are multiple types, each tailored to meet specific requirements. Here’s a quick rundown:
Steel Structure Modular Construction:
- Key Features: Strong, lightweight, fast to build, and capable of large spans. Perfect for quick projects.
- Best For: Factories, warehouses, multi-story buildings, and commercial spaces that need a lot of room and fast construction. For example, steel modules are often used in logistics centers for large, quick-to-build storage areas.
- Potential Downsides: Steel modular construction can sometimes be more susceptible to corrosion if not treated properly. However, with modern coatings like galvanization, epoxy coatings, and powder coating, along with anti-corrosion treatments, we ensure that all our steel structures are well-protected and long-lasting.
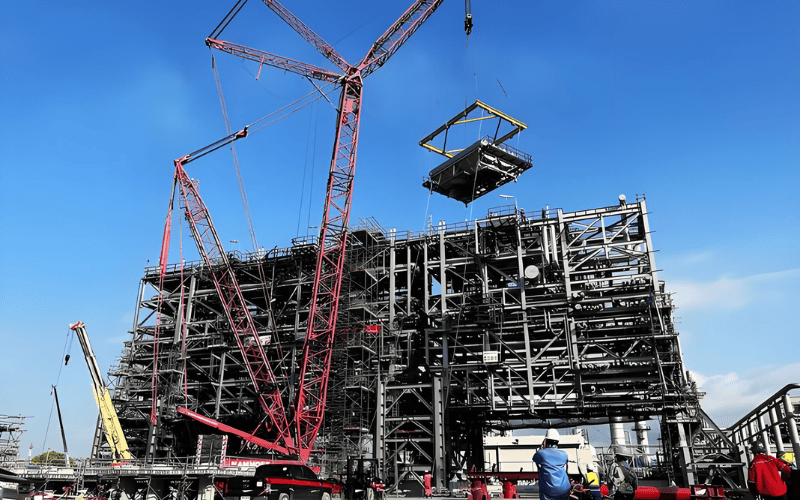
Concrete Modular Construction:
- Key Features: Very stable, durable, great sound and heat insulation, and fire-resistant. Concrete modules provide a solid foundation.
- Best For: Projects where safety and long-term durability are critical, like high-rises, schools, and hospitals. A good example is the Edinburgh International Conference Centre in Scotland, which used concrete modular construction for its expansion, ensuring high durability and fire resistance.
- Potential Downsides: Concrete modules are heavier and more challenging to transport and install, which can lead to higher costs and extended timelines. Steel, being lighter and quicker to assemble, is often the better choice for time-sensitive projects. Our steel structures ensure faster builds without compromising strength.
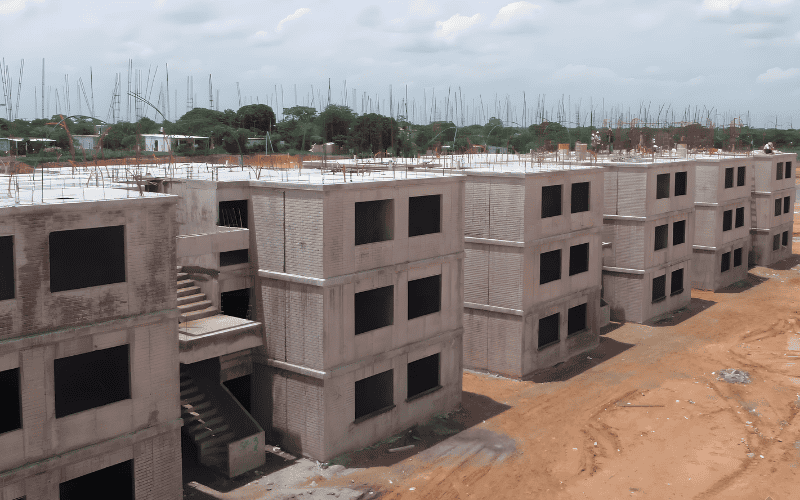
Steel-Concrete Hybrid Modular Construction:
- Key Features: Combines steel’s speed with concrete’s durability, offering flexibility in design.
- Best For: Projects needing both strong structure and flexibility, like offices and kindergartens. A great example is the Vancouver International Airport terminal expansion, which used a steel-concrete hybrid to balance both speed and stability in the construction of new office spaces.
- Potential Downsides: The hybrid approach can increase complexity and costs, as it requires integrating both steel and concrete systems. But with our expertise in both materials, we ensure smooth integration, delivering a cost-effective solution with the benefits of both materials.
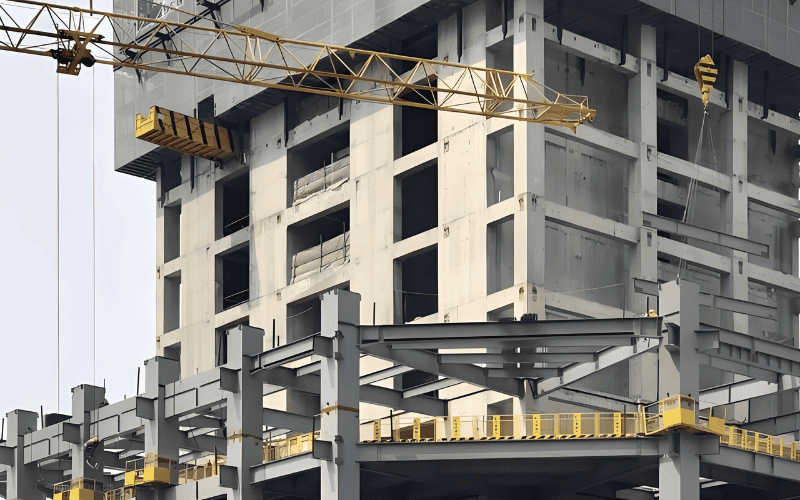
Lightweight Steel Modular Construction:
- Key Features: Light, easy to transport, great seismic resistance, and flexible design.
- Best For: Small to mid-sized projects that need quick setup and aesthetic appeal, like residential buildings or pop-up stores.
- Potential Downsides: While lightweight steel modules are flexible, they may not provide the same level of thermal insulation as concrete. To address this, we can offer custom insulation options that match your climate needs, ensuring comfort and energy efficiency.
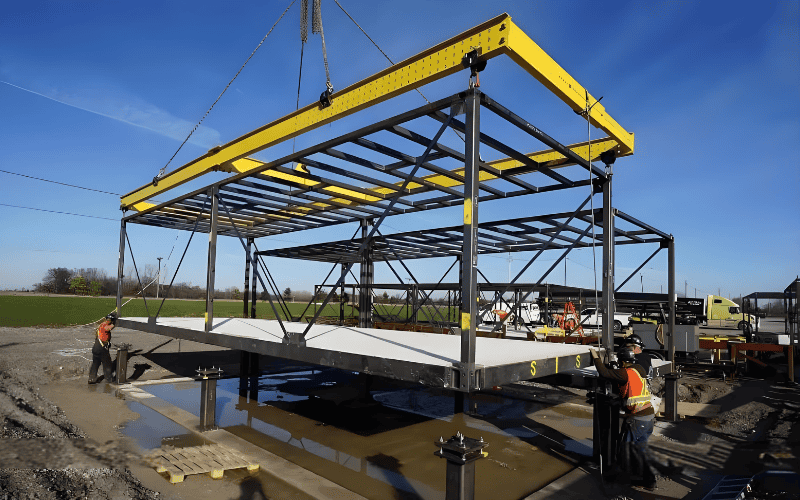
Each solution offers its advantages—speed, durability, or flexibility—so selecting the right one depends on the specific needs of your project.
Assessing Your Project’s Needs
Determining the specific requirements of your project is the first step in choosing the right modular solution. The more clearly you define what you need, the easier it becomes to build a structure that fits perfectly.
Function and Purpose
Every project has its own unique requirements. For a residential project, think about how many bedrooms or bathrooms you need, plus any special features like a home office, accessible living spaces for seniors or those with disabilities, or outdoor areas.
For commercial projects, the layout matters: open spaces or partitioned offices? Do you need large conference rooms or customer-facing areas? Retail spaces should consider display areas, storage, and how to manage foot traffic effectively.
If you’re building for industrial or warehouse use, pay attention to things like load-bearing capacity, wide entry doors for machinery, and the importance of good ventilation.
Size and Space Constraints
The shape and size of your plot of land will impact how you design the modular building. Narrow city lots may require a long, linear design, while open country plots offer more freedom to arrange the modules.
Keep zoning laws and setback requirements in mind, as they dictate how far a building must be from property lines. These regulations could affect the overall space available for your modular structure.
Budget Considerations of Your Project
Balancing your budget with the right modular solution requires careful planning—consider both upfront costs and long-term savings to make the best choice for your project.
Upfront Costs
The initial project cost is typically the primary consideration. The cost of each modular unit varies based on its size, complexity, and degree of customization. A basic modular unit may cost less, but customization for a more complex project—like adding specific finishes or advanced technology—can increase the price.
It’s also crucial to consider transportation costs for delivering the modules from the factory to your site. Site preparation (foundation, utilities, etc.) can add up too, so it’s essential to budget for these as well.
Additionally, keep in mind that steel prices can fluctuate. To prevent budget surprises, it’s smart to add an extra 10-20% to your overall budget to cover potential price fluctuations in materials.
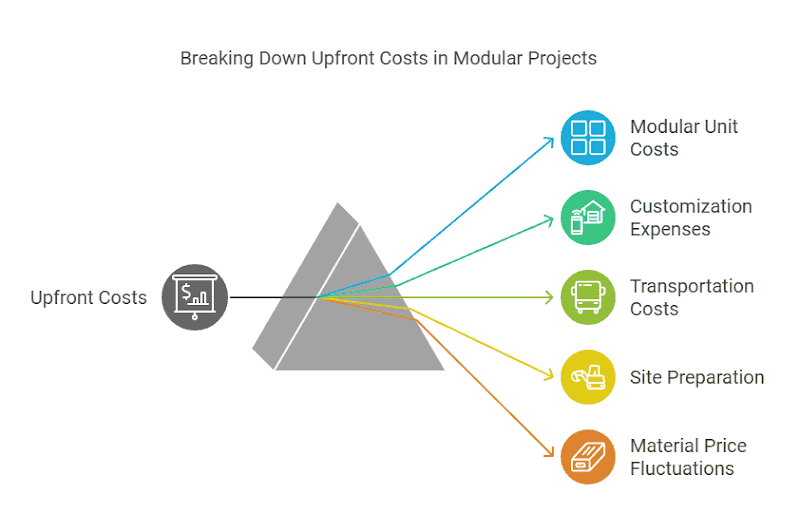
Maintenance
Different building materials impact your long-term maintenance costs. For example, modular buildings with metal cladding usually need less frequent painting than wood-clad ones. However, while metal doesn’t require paint touch-ups as often, you’ll still need to inspect regular checks for any signs of corrosion, sealant wear, or water damage around joints and seams are crucial to avoid costly repairs down the road. Pick materials that match your maintenance plans and budget, and consider the local climate to help guide your decision.
Long-Term Savings
Modular buildings can save on labor costs because much of the construction happens off-site. They generally enable faster occupancy, resulting in a quicker return on investment. Keep in mind that although upfront costs may appear higher for high-quality modular solutions, the long-term savings in time and money can be substantial.
Assessing the Quality and Standards You Need
Getting the quality right means more than meeting basic requirements—it’s about ensuring your modular building will stand the test of time.
- Manufacturing Standards: It’s important to choose a modular solution that follows trusted certifications like ISO. These standards ensure that safety, durability, and environmental practices are top-notch at every step. We stick to these exact standards, so you can be sure your building meets the highest quality.
- Material Procurement: Always choose a supplier who uses high-quality materials—it’s a must for long-term performance. At our factories, we only use top-tier steel that’s tested for strength and durability. This ensures that your building will be durable and reliable, regardless of its application.
- Quality Assurance Process: Ensure the supplier you choose has a rigorous quality control system in place. From the first inspection of raw materials to the final check before delivery, we ensure everything is in perfect condition. This careful attention to detail guarantees that your building arrives fully prepared to perform at its best.
How Customizable Do You Need It?
Modular buildings provide varying levels of customization based on the manufacturer. Some suppliers provide quick, cost-effective “cookie-cutter” designs, while others offer fully tailored solutions. Consider how much customization you need to meet your specific vision.
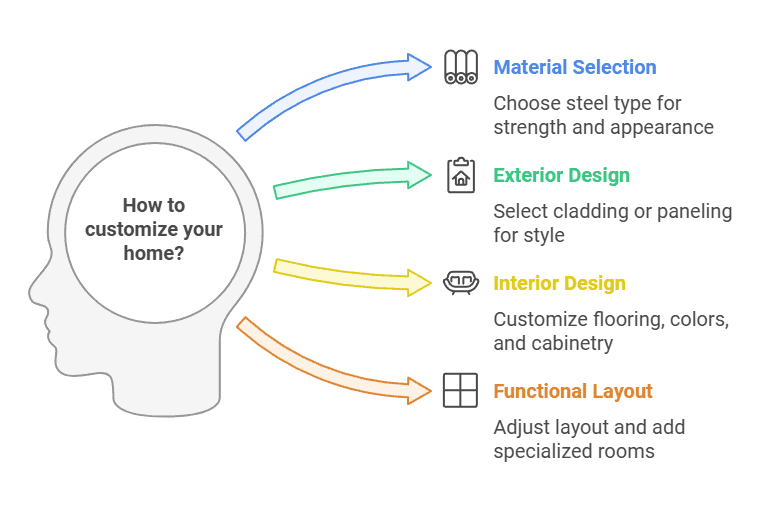
For material customization, the type of steel you choose affects both strength and appearance. Low-alloy high-strength steel is durable and tough, while carbon steel offers strength at a lower cost. Galvanized steel resists rust, and weathering steel develops a natural patina over time, ideal for outdoor settings.
For the exterior, you have plenty of choices. Metal cladding in various colors gives a modern look, while wood or wall panels offer a traditional style. You can also select your roof design, from flat to sloped, depending on your vision.
Interior customization lets you create the perfect space. Take our Modular Apple Cabin, for example—everything from flooring to wall colors and cabinetry can be customized. Whether you want sleek and modern or warm and cozy, you’re in control.
Finally, functional customization is a huge advantage. We can adjust the layout, adding custom rooms or specialized spaces like a photography darkroom. Whatever your needs may be, we’ll make it work for you.
Timeframe for Your Project
A major advantage of modular buildings is their fast construction speed. While traditional construction can stretch over months, modular buildings can often be completed in just weeks.
If you have a tight deadline—whether it’s for opening a business, preparing a school for the new year, or urgently building emergency shelters—modular construction helps you meet those goals without compromising on quality.
Here’s a general timeline for our modular building projects timelines:
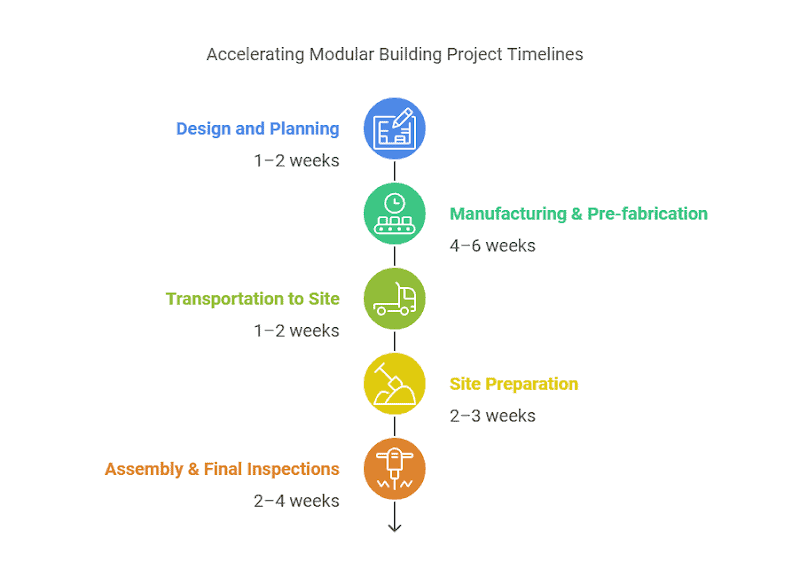
We typically complete projects 20–30% faster than traditional methods.
Location and Site Accessibility
Your project’s location plays a major role in choosing the right modular solution.
Site Accessibility Challenges
Some sites are easy to reach, while others, like narrow or hard-to-access areas, can challenge transporting large modules. Smaller, easier-to-assemble modules may be the best choice if access is limited. These modules are more convenient to transport and don’t require heavy cranes or large trucks.
Choosing the Right Location for Installation
Modular buildings are particularly well-suited for difficult or remote locations. They can be assembled faster and with fewer complications compared to traditional construction, making them ideal for sites with challenging access or terrain. But when planning the installation, you still have to consider both the environment and ground conditions.
For the best results, choose stable, level ground with easy access for transportation. Avoid sites with steep slopes, soft soil, or flooding risks. A sturdy foundation is vital for stability, particularly for larger modules. Additionally, ensure there’s enough space for cranes or lifting equipment to operate smoothly during assembly.
Choosing the Right Manufacturer
Not all modular building suppliers are the same, so choosing one that fits your project’s specific needs is crucial. Look for a manufacturer with proven experience, clear pricing, and strong quality assurance processes. Feel free to ask for references or examples of previous projects.
Remember, the best choice is the one that aligns with your priorities, whether that’s speed, cost, or customization. Take the time to assess your options and make a well-informed decision.
If you have any questions or need customized advice, don’t hesitate to contact us—we’re here to help!