Warehouses play a crucial role in supply chains, ensuring that goods are stored, sorted, and distributed efficiently. However, not all warehouses are the same. Choosing the right type of warehouse can significantly impact costs, operational efficiency, and customer satisfaction.
In this blog, we’ll break down different types of warehouses and help you determine which warehouse best suits your business needs.
Let’s dive in!
What Is a Warehouse & Why Does It Matter?
A warehouse is a facility used to store goods before they are sold, distributed, or processed. But warehouses are more than just storage spaces—they are essential for managing supply chains, optimizing inventory flow, and meeting customer demands efficiently.
Choosing the right warehouse impacts:
- Storage costs (reducing wasted space and unnecessary expenses)
- Shipping speed (ensuring fast and efficient distribution)
- Operational efficiency (helping businesses manage stock levels better)
- Customer satisfaction (getting products delivered quickly and in good condition)
Understanding different types of warehouses will help you select the best one for your business needs.
Warehouse Types by Ownership
1. Private Warehouses
✅ What They Do:
- Owned and operated by a single company for exclusive use.
- Provide full control over operations but require significant investment in infrastructure and maintenance.
✅ Best For:
- Large businesses with predictable, high-volume inventory needs.
- Companies looking for long-term cost savings and operational control.
2. Public Warehouses
✅ What They Do:
- Rented by multiple businesses, offering flexible storage options, and generally managed by third-party logistics providers (3PLs).
✅ Best For:
- Small and medium-sized businesses with fluctuating or seasonal inventory needs.
- Companies seeking cost-effective, short-term storage solutions.
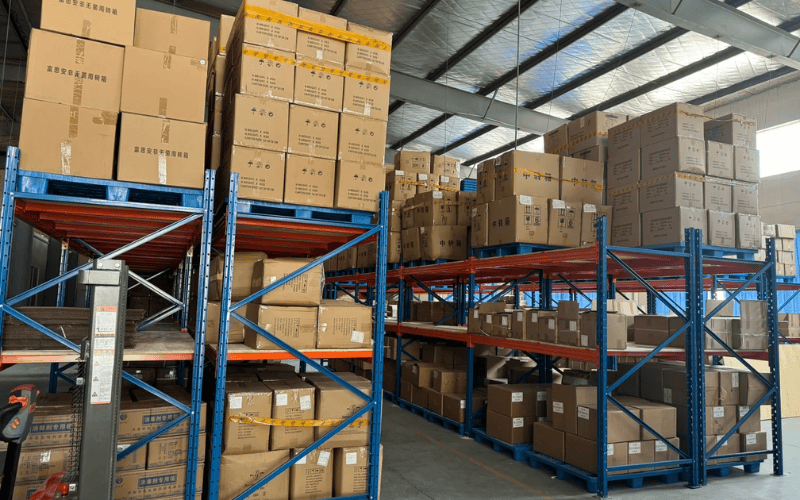
3. Contract Warehouses
✅ What They Do:
- A hybrid model between private and public warehouses.
- Businesses sign long-term agreements with warehouse providers, often with dedicated space and services.
✅ Best For:
- Companies with stable, ongoing storage needs but without the capital to build or maintain their own facility.
- Businesses looking for dedicated storage services without the long-term commitment of full ownership.
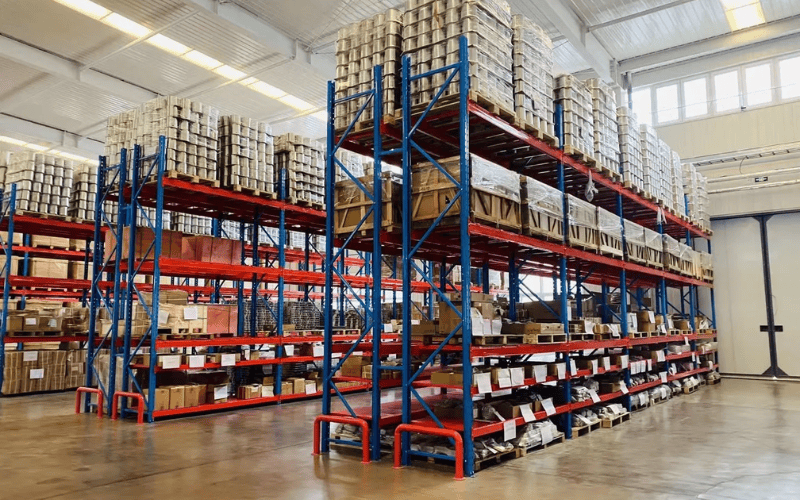
4. Cooperative Warehouses
✅ What They Do:
- Owned and shared by multiple businesses to reduce costs, leveraging economies of scale.
✅ Best For:
- Small retailers, independent brands, and agricultural cooperatives that need to lower storage costs.
- Companies that benefit from shared resources and collective purchasing power.
Warehouse Types by Storage Needs
5. General Storage Warehouses
✅ What They Do:
- Store goods in bulk, often for manufacturers, wholesalers, or retailers.
- Used for raw materials, finished products, or excess inventory. Usually equipped with shelving, pallets, and forklifts for handling goods.
✅ Best For:
- Manufacturers storing production materials or wholesalers holding extra stock.
- Businesses that don’t require rapid turnover or specialized handling.
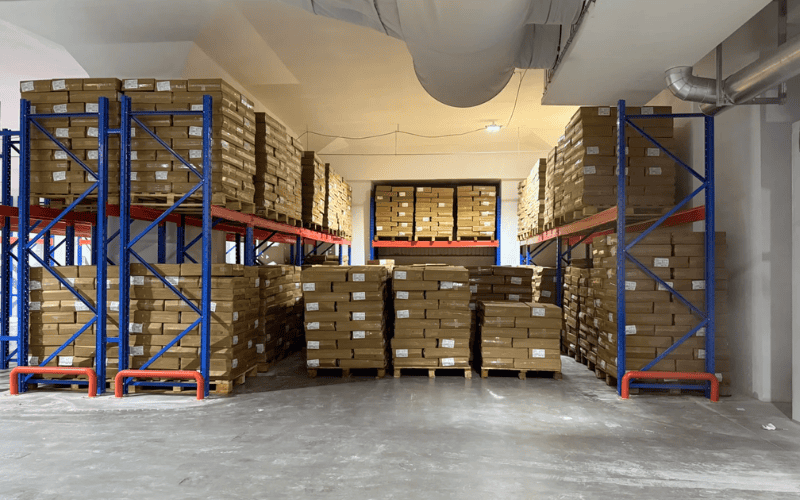
7. Climate-Controlled Warehouses
✅ What They Do:
- Maintain a stable temperature, humidity, and sometimes other environmental factors to protect sensitive goods from temperature extremes or moisture damage.
✅ Best For:
- Food and beverages (e.g., dairy, seafood, frozen foods).
- Pharmaceuticals and vaccines.
- Cosmetics and high-end perfumes.
- Fine art, antiques, and rare collectibles that require specific climate conditions.
8. Hazardous Material Warehouses
✅ What They Do:
- Store dangerous materials under strict safety regulations, with specialized safety features such as ventilation, fire suppression, and secure containment.
✅ Best For:
- Chemicals, flammable materials, and gases.
- Pharmaceuticals with hazardous components.
- Explosives, radioactive materials, or other highly regulated products.
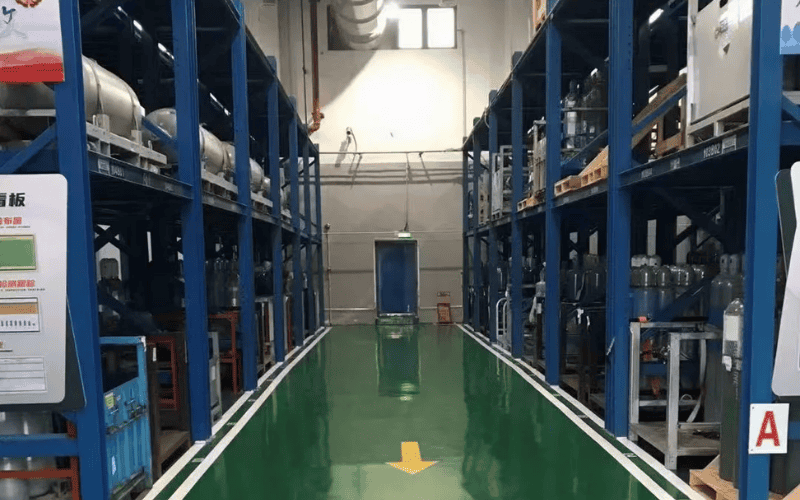
9. Bonded Warehouses
✅ What They Do:
- Store imported goods before customs duties are paid.
- Allow businesses to defer taxes until goods are sold, helping to improve cash flow and reduce upfront costs.
✅ Best For:
- Import/export businesses dealing with international logistics.
- Companies looking to manage customs duties and reduce upfront tax expenses.
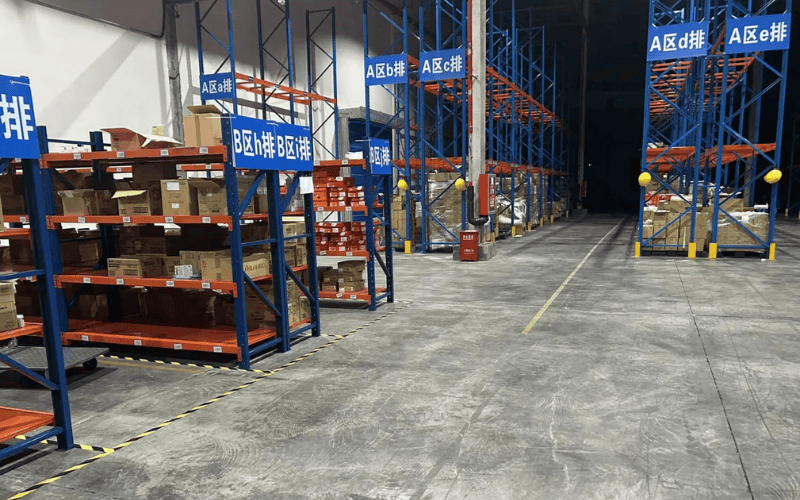
Warehouse Types by Operational Process
9. Fulfillment Centers
✅ What They Do:
- Process e-commerce orders by picking, packing, and shipping goods.
- Often run by third-party logistics (3PL) providers with the use of advanced automation, AI, and robotics to handle high-volume, time-sensitive orders quickly.
✅ Best For:
- E-commerce businesses like Amazon sellers, subscription box services, and retailers needing fast nationwide or international shipping.
- Companies requiring rapid order fulfillment and distribution.
10. Distribution Centers
✅ What They Do:
- Act as a hub where goods are sorted and then sent to retailers or customers.
- Store inventory temporarily before shipping it to its final destination.
✅ Best For:
- Large retailers like Walmart, Target, and Home Depot.
- Brands that supply multiple retail outlets or large-scale distribution networks.
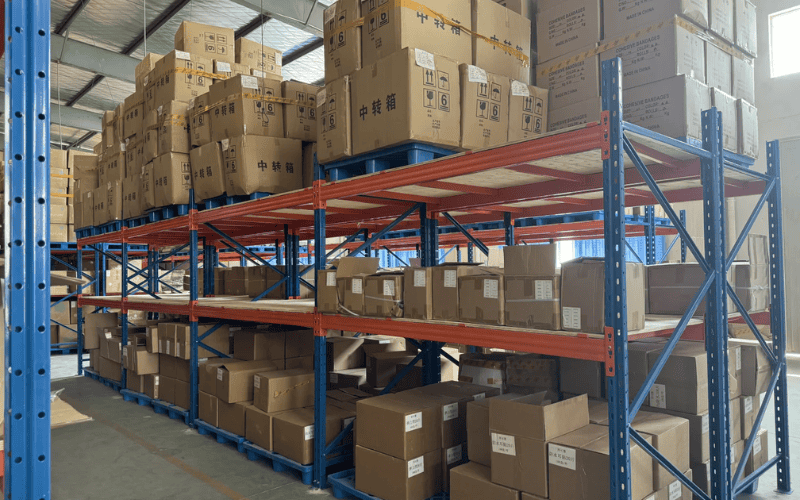
11. Cross-Docking Warehouses
✅ What They Do:
- Minimize storage time by immediately transferring inbound goods to outbound trucks or shipping methods, bypassing long-term storage.
- Accelerates the delivery process, especially for products that need quick turnover.
✅ Best For:
- Perishable goods (e.g., fresh food, flowers) that require minimal storage time.
- Large retailers managing high-demand or just-in-time inventory.
- Logistics companies optimizing supply chain efficiency and reducing warehousing costs.
12. Reverse Logistics Warehouses
✅ What They Do:
- Handle returns, repairs, recycling, refurbishing, or disposal of products.
- Specialize in managing product returns, repairs, and recycling processes in a controlled manner.
✅ Best For:
- E-commerce businesses managing product returns, particularly in high-volume retail.
- Electronics retailers dealing with defective returns or warranty claims.
- Businesses managing product recalls or refurbishing used goods for resale.
How to Choose the Right Warehouse: Key Questions to Ask
1. What Are Your Storage Needs?
- Question: What types of goods are you handling (e.g., perishables, hazardous materials, bulky items)?
- Answer:
- Match your goods to specialized facilities:
- Temperature-controlled warehouses for perishables like food or pharmaceuticals.
- Bonded warehouses for internationally traded goods requiring customs oversight.
- High-security warehouses for sensitive or hazardous materials.
- Verify if permits/licenses (e.g., FDA, OSHA) are required.
- Match your goods to specialized facilities:
2. Where Is Your Customer Base Located?
- Question: How close is the warehouse to your customers?
- Answer:
- Proximity reduces delivery times and costs.
- Prioritize regions with high customer density or strategic transport links (e.g., ports, highways).
3. How Accessible Are Transport Networks?
- Question: Does the warehouse offer easy access to key logistics routes?
- Answer:
- Ensure connectivity to highways, railways, airports, or seaports.
- Evaluate delivery flexibility (e.g., same-day shipping, cross-docking).
4. What Technology Does the Warehouse Use?
- Question: Are advanced systems like WMS (Warehouse Management Systems) or automation in place?
- Answer:
- Opt for tech-enabled warehouses if you need:
- Real-time inventory tracking.
- Automated order fulfillment (e.g., robotics, AS/RS).
- Integration with your ERP or e-commerce platforms.
- Opt for tech-enabled warehouses if you need:
5. How Secure Is the Facility?
- Question: What security measures protect your inventory?
- Answer:
- Look for 24/7 surveillance, access controls, fire suppression systems, and insured storage.
- Review the warehouse’s liability policies for theft/damage.
6. What Level of Service Do They Provide?
- Question: Can the warehouse scale with your business and handle peak demands?
- Answer:
- Test responsiveness: Contact their support team to gauge communication speed.
- Ask about value-added services (e.g., kitting, labeling, returns management).
- Check reviews or request client references.