When a food processing company evaluated construction plans due to expansion needs, they found that a traditional reinforced concrete workshop required 8 months of construction time and 1,200 tons of steel, while a light steel structure of the same size only needed 4.5 months and 850 tons of steel — saving 28% in material and reducing the construction time by 44%. This is the transformation happening globally in industrial construction: Light steel structures are becoming the preferred choice for modern enterprises due to lower material consumption, faster construction times, and stronger seismic performance.
This article will cut through the marketing jargon and get to the core value of light steel workshops. Whether you are a newcomer to steel structures or a professional seeking a technical upgrade, you’ll find actionable insights to guide your decisions.
Why Choose Light Steel Workshops?
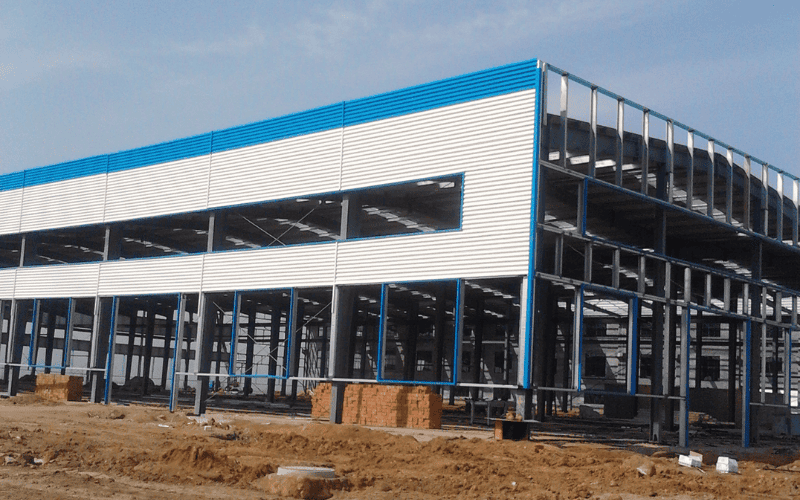
- Economic Efficiency & Material Utilization
- Lighter than traditional steel structures, saving steel material.
- Uses variable cross-section design (adjustable beam height/thickness), maximizing material efficiency.
- Allows for effective strength utilization even after web buckling, reducing component thickness.
- Construction Advantages
- Factory-prepared components and fast installation with bolt connections.
- Reduced civil engineering work, enhancing industrialization and construction speed.
- Seismic & Structural Stability
- Strong seismic performance, can withstand up to a 9-magnitude earthquake.
- The supporting system, with purlins and flying braces, ensures lateral stiffness.
- Wind load is considered for tall buildings or those in high wind zones.
Light Steel Workshop vs. Traditional Steel Structure
To help you better understand the advantages of light steel workshops, we’ll quickly compare the key features of light steel workshops and traditional steel structures as below:
Comparison Criteria | Light Steel Workshop | Traditional Steel Structure |
Steel Usage per m² | 25-35kg (Save 20-30%) | 35-45kg |
Construction Time | 2-4 months (40%+ shorter) | 4-8 months |
Seismic Performance | Can withstand 9-magnitude earthquake | Typically designed for 7-8 magnitude |
Space Renovation Cost | No welding needed for layout changes | Requires cutting and welding, higher costs |
Technical Core of Light Steel Workshops
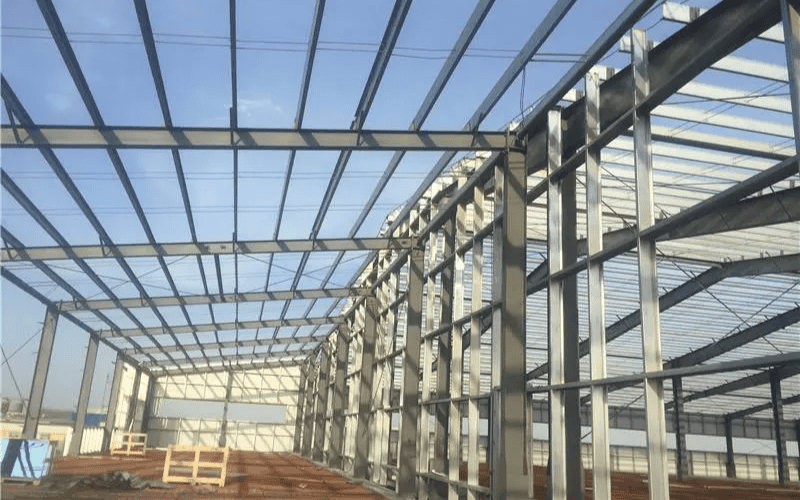
1. Variable Cross-Section Design
Imagine a tree with a thick trunk and a slender top. Light steel workshop beams and columns use a similar tapered cross-section design:
- Thicker steel plates (up to 12mm) at the bottom, where stress is highest.
- Thinner plates (down to 4mm) at the top.
- Result: Steel savings of 31% per steel frame and 18% weight reduction for the entire structure.
2. Wind and Earthquake Resistance
The structure forms a spatial triangle of stability with purlins and flying braces:
- Horizontal forces are transmitted through the purlins to the column supports.
- Flying braces decompose the load into axial forces, preventing bending.
- Real-life data: In a typhoon with a level 12 wind, lateral displacement was only 1/400 (national standard limit is 1/250).
3. Industrialized Construction
- Factory Prefabrication Process: Cutting machine → Automatic welding → Shot blasting for rust removal → Anti-corrosion coating.
- On-Site Installation Process: 1 day for foundation alignment → 3 days for steel column installation → 2 days for main beam installation → 1 day for purlin installation
In-Depth Answers to 3 Common Questions About Light Steel Workshops
Q1: How long will it last? Will it rust in rainy areas?
Core defense: 1) Hot-dip galvanization (≥275g/m²) + 2) Polyester powder coating + 3) Annual joint inspection
Case: A chemical factory in Zhuhai used its workshop for 17 years, with 85% of the galvanized layer still intact.
Q2: What is the most economical span?
Ideal range: 18-36 meters (for spans over 45 meters, space trusses are needed).
Unconventional solution: A logistics warehouse used a 3-span design (24m×3), reducing column foundation costs by 22%.
Q3: Can it withstand extreme weather?
Typhoon zone solution:
- Purlin spacing reduced to 1.2 meters.
- Roof panels use a 360° standing seam system.
High seismic zone:
- Nodes use energy-dissipating dampers.
- Foundations equipped with seismic isolators.
Hidden Values of Light Steel Workshops
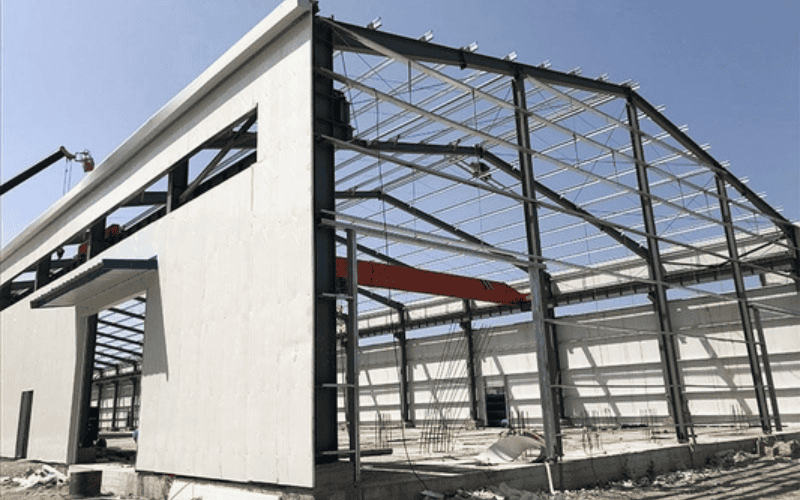
- Environmental Impact Beyond Words
- Steel recycling rate: 92% vs. concrete’s recycling rate of less than 35%.
- Carbon emissions: Light steel buildings emit approximately 53% of the carbon of concrete buildings.
- Production Capacity Flexibility
- Light steel structures can be easily expanded to meet growing production demands without requiring major changes to the existing building.
- The wide, column-free spaces allow for easy adjustments to production lines or equipment.
- Production layouts can be restructured with minimal disruption, reducing the need for costly and time-consuming alterations.
- Expanding or modifying the facility is faster and more affordable, resulting in less downtime and lower costs compared to traditional building methods.
Supplier Selection: Red Flags and Must-Haves
✅ Essential Qualifications Checklist
- First-class steel structure manufacturing qualification in China
- ISO 9001/14001 certification
- Authorized professional structural software (e.g., Tekla/MIDAS)
🚫 Identifying Price Traps
- Beware of “designing by standard drawings” that don’t consider actual wind/snow loads.
- Reject “on-site welding of main components”—all should be prefabricated in the factory.
🔍 Acceptance Inspection Checklist
Inspection Item | Qualified Standard | Tool |
High-strength bolt torque | M24 bolt ≥ 400 N·mI | Digital torque wrench |
Weld quality | No burn marks/slag, height ≤ 3mm | Weld inspection gauge |
Your Next Light Steel Workshop Project Starts Right Here, Right Now
We deliver end-to-end solutions for light steel workshops – from design, manufacturing, and logistics to on-site installation. With in-house factories ensuring strict quality control, we customize solutions based on your blueprints or optimize existing plans. Our certified engineers provide full supervision, helping you save in costs and timelines.
In an unpredictable market, our 20+ years of expertise (backed by 1,000+ domestic and international projects, ISO 9001/14001, and EN 1090 certification) redefine reliability:
✅ Seismic/wind-resistant engineering
✅ Precision prefabrication with zero on-site welding
✅ Sustainable & recyclable designs
✅ And MORE
Schedule a Consultation Today →
Let our team calculate your ROI potential – discover how industrial efficiency translates to real competitive advantages.