Prefabricated Warehouse Buildings are made with pre-built modules that are quickly assembled on-site, saving both time and money. They’re perfect for quick construction and can be tailored to meet different storage requirements. While they suit most needs, some adjustments may be needed for specific situations. Knowing this helps you get the best value out of your investment.
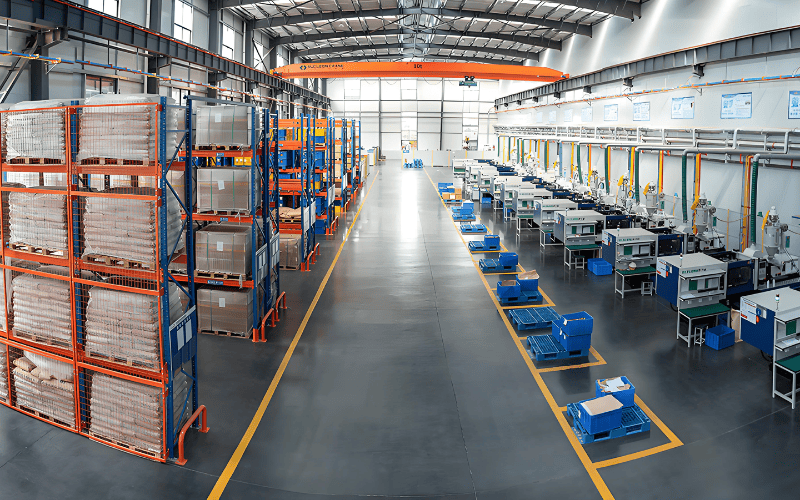
Why Prefabricated Steel Warehouses Have Gained Popularity in Recent Years
The rise of prefabricated steel warehouses makes sense. With e-commerce booming and space needs growing fast, traditional builds just can’t keep up. These warehouses are quick to build, flexible, and customizable—making them a popular choice for many businesses.
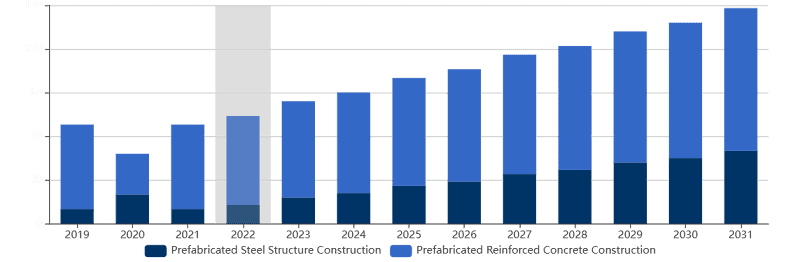
source: cognitivemarketresearch.com/pre-engineered-buildings-market-report
Rapid Market Growth: The prefabricated steel structure market is projected to nearly double by 2031, reflecting increasing demand for fast and efficient non-residential buildings.
Outpacing Concrete Solutions: Steel structures consistently surpass prefabricated concrete in adoption rates, highlighting their flexibility and quicker installation.
Key Growth Period: The most significant expansion is forecasted between 2027 and 2031, driven by industrial and commercial construction needs like warehouses and factories.
8 Pros of Prefabricated Warehouse Buildings
Prefabricated warehouse buildings offer a wide range of advantages, from cost efficiency and fast installation to durability and environmental benefits. These features make them a top choice for contemporary storage and industrial solutions.
1. Lower Transportation Costs
Prefabricated steel structure components are flat-packed for efficient use of transport space. This reduces the number of containers and trips required, cutting costs significantly. It also enables delivery to remote locations. For instance, flat-packing can cut shipping volume by as much as 50% compared to conventional materials.
2. Reduced Labor Costs
The standardized components are mass-produced in factories, minimizing time and cost for custom designs. Simplified assembly reduces manpower requirements, enabling a small team to efficiently complete installation. A 1,000-square-meter warehouse, for instance, can be assembled by just five workers in under a month.
3. Lightweight Construction
Steel offers high strength and flexibility with a weight of just 20% of brick-and-mortar structures. The entire rigid framework resists extreme weather, such as typhoons with wind speeds of up to 70 m/s, while maintaining structural integrity.
4. Wide Spans Without Columns
Steel structures are designed for large spans, allowing for open spaces without internal columns. This maximizes usable space, making it ideal for storage and logistics facilities. Spans can exceed 60 meters without compromising stability.
5. Environmentally Friendly & Energy Efficient
Prefabricated warehouses integrate energy-saving features like insulated panels, solar roofing, and natural lighting systems. These features can cut heating, cooling, and lighting energy usage by up to 30%, reducing both operational costs and carbon emissions.
6. Fast Installation
Prefabricated components require no on-site material storage. When delivered, they’re ready to assemble, cutting project timelines by 30–50% compared to traditional builds. This speed also mitigates risks like theft of stored materials during construction.
Related Reading: Steel Warehouse Buildings Installation
7. Customizable Design Options
We offer prefabricated warehouse solutions customized to suit a wide range of needs. Our layouts include T-, L-, U-shaped, and Straight-line Flow layout designs, offering flexibility for various applications. Roofing options, such as lean-to, gabled, curved, flat, and multi-gabled roofs, can be selected based on functional and aesthetic preferences.
For walls, we offer finishes like PebSeam, PebWall, SEAMLOCK, Roll-Formed, and Snap-Lock. Additionally, clients can choose from high-quality materials, including galvanized or stainless steel, ensuring durability and adaptability to specific requirements.
8. Long Lifespan
Our prefabricated steel warehouses are engineered to withstand heavy snow, high winds, and seismic activity, ensuring excellent load resistance. Compared to traditional brick-and-mortar structures, they offer superior corrosion resistance and better fire resistance, extending their lifespan to 50 years or more with proper maintenance.
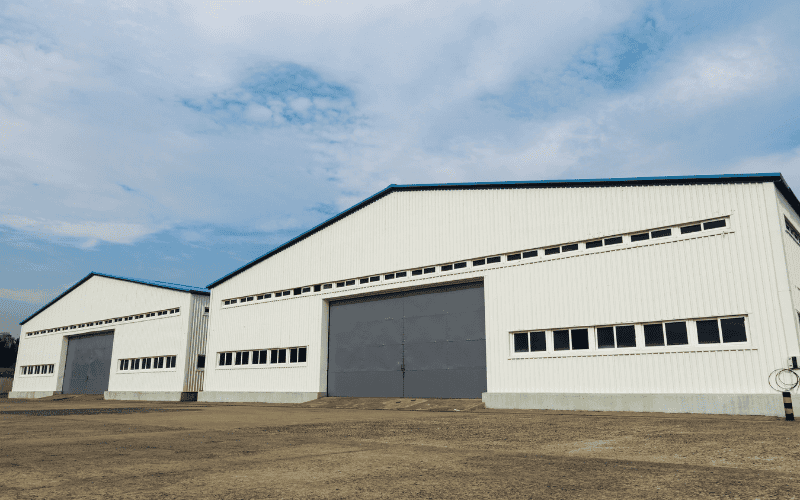
These benefits position prefabricated warehouse buildings as an efficient and scalable solution for modern businesses, balancing cost, durability, and functionality.
Cons of Prefabricated Warehouse Buildings
While prefabricated warehouse buildings and modular warehouses offer many benefits, they also have challenges that can be addressed with thoughtful design and solutions.
1. Poor Ventilation
Steel structures’ tight seals can reduce air circulation, leading to moisture buildup, condensation, or even mold in humid or fluctuating climates. Don’t worry—we’ve got this covered! Our solutions include natural or mechanical ventilation systems, like exhaust vents in roofs and walls, ensuring proper airflow and keeping your goods safe and dry.
2. High Thermal Conductivity
Steel’s heat conductivity can cause indoor temperatures to fluctuate, making good insulation a must. We offer spray foam and sandwich panels for superior thermal resistance. For example, our 100mm R15 insulation works as well as a 1-meter-thick brick wall, keeping your warehouse cool in summer and warm in winter.
3. Building Extension Limitations
Extending prefabricated steel buildings is easiest along their length, as it must align with the ridge direction, which limits width expansions. We plan for future growth upfront, designing modular layouts that make lengthwise extensions a breeze. This way, your building grows with your business.
4. Susceptibility to Brittle Fracture
Steel can sometimes be prone to brittle fractures in low temperatures or lamellar tearing in thick plates. We handle this with smart material choices and careful design, ensuring your building stays strong and reliable, no matter the conditions.
Choose Our Prefabricated Warehouse Buildings
Steel and modular warehouses offer fast construction, cost efficiency, and durability, making them ideal for modern business needs. Our designs cut costs while offering flexible spaces that can easily accommodate future expansions. Our warehouses deliver better seismic resistance, corrosion protection, and long-term value than concrete structures, such as our large span steel warehouse buildings.
With years of experience, we ensure every warehouse meets top engineering and environmental standards. Choose us for a durable, sustainable solution that supports your business growth.
Common Questions That You May Concerned About
1. Are Prefabricated Warehouses Suitable For All Industries?
Yes, they are versatile and can be tailored for industries like logistics, manufacturing, agriculture, and retail with specific design and layout requirements.
2. How Long Does It Take To Construct A Prefabricated Warehouse?
Construction is much faster than traditional methods, with most projects completed in 30–50% less time, depending on the size and complexity.
3. Can Prefabricated Warehouses Be Relocated?
Yes, modular designs allow easy disassembly and relocation, making them perfect for businesses with evolving needs or temporary storage solutions.
4. Are Prefabricated Warehouses Environmentally Friendly?
Yes, they use recyclable materials and energy-efficient features like solar roofing and natural lighting to reduce their carbon footprint.
5. What Maintenance Is Required For Prefabricated Warehouses?
Minimal maintenance is needed, focusing on regular inspections for corrosion, structural integrity, and ventilation system performance to ensure longevity.