Thinking about setting up a shipping container on your property—whether it’s a home, office, shop, or something in between? One thing that often gets overlooked (but really shouldn’t) is the foundation. Whether you’re placing a single unit or stacking up a full-on container home, the right base keeps everything level, secure, and safe from the elements.
This article is built for anyone working with shipping container buildings, whether it’s temporary or here to stay. We’ll break down when you actually need a foundation, the different types available, and how to choose the right one based on your soil, site, and building goals.
How Do I Know If My Shipping Container Needs a Foundation?
Before diving into types and costs, let’s start with the basics: does your container actually need a foundation?
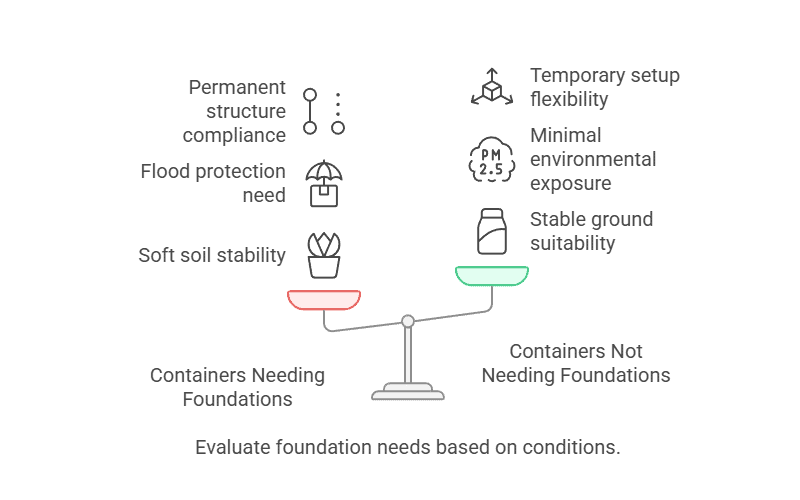
A good foundation does more than just hold weight—it keeps your container level, dry, and firmly in place. In many situations, a proper foundation isn’t optional—it’s essential. Here’s when you absolutely need one:
- Soft or unstable soil requires a foundation to prevent the container from sinking, leaning, or shifting over time.
- In wet or flood-prone areas, you need a raised or sealed foundation to protect the container from rust, corrosion, and long-term water damage.
- Multi-story container buildings must have a solid foundation to safely distribute weight and resist horizontal movement.
- In high-wind or seismic zones, anchoring your container to a sturdy base is critical to prevent tipping or structural failure.
- If your container is considered a permanent structure, many local codes require a fixed foundation for legal approval and long-term stability.
That said, some setups don’t necessarily need a full foundation. For example:
- Short-term structures, like pop-up shops or seasonal kiosks, can sit on temporary supports.
- Portable site offices placed on compacted, stable ground often do just fine without permanent anchoring.
- Basic storage units on crushed gravel or paver pads may only need basic leveling to stay functional.
In these cases, lightweight or removable base solutions can still give you the support you need—without going overboard.
Understanding the Soil Before Choosing a Container Foundation
Before picking a foundation type, you need to get familiar with what’s under your feet. The soil you’re building on directly affects how well your foundation performs—and how long it lasts.
At its core, foundation performance comes down to how your container’s weight transfers into the ground. A fully built-out container with insulation, finishes, and furniture can weigh several tons, and if the ground can’t handle that load properly, things start to shift, sink, or crack.
Here are four key soil-related factors to keep in mind:
- Soil Type & Load Capacity: Not all soil holds weight the same. Clay expands when wet, sand tends to shift, and rock offers solid support. Each one needs a different foundation approach to stay stable.
- Skin Friction: This refers to how much grip the soil has on your foundation’s surface—especially important for pile or screw foundations that rely on vertical friction to stay in place.
- Settlement Risk: Loose or poorly compacted soil will settle over time, which can cause uneven support under your container. That’s when doors stick, floors tilt, and structural stress builds up.
- Soil Expansion and Contraction: In cold climates, the freeze-thaw cycle can cause soil to heave, pushing the foundation up and down seasonally. If your foundation isn’t designed to handle that, it can crack or shift.
Understanding these soil conditions helps you choose the right foundation type, not just based on budget—but based on what will truly hold up in your environment.
Different Types of Container Foundations
Choosing the right foundation depends on your location, soil type, container setup, and long-term plans. Let’s walk through the most common types of container foundations, how they’re built, and when they make the most sense.
Container Pier Foundation
A pier foundation uses vertical concrete or steel columns positioned under each corner (and sometimes midpoints) of the container.
This type is ideal for sloped or uneven sites, moderate climates, and soil with good drainage. It’s especially popular for off-grid cabins and light residential use because it lifts the container off the ground for better airflow. Pier foundations are considered semi-permanent to permanent, depending on the material and anchoring.
Installation:
Piers are either cast in place using concrete footings or installed as steel helical piles drilled into the ground. Each pier must align precisely with the container’s corner castings. The container is typically secured using anchor bolts embedded in the piers or welded steel plates. If mobility is needed, twist locks can also be used—but these require precise placement and only connect at the corners.
Container Slab Foundation
A slab foundation is a solid concrete pad that supports the entire footprint of the container.
This is a go-to choice for permanent buildings in wet or soft-soil environments, as it offers excellent stability and protects the container from ground moisture. It’s also a good option for commercial or residential setups that require a finished floor. Slabs are fully permanent and typically more expensive than piers or pads.
Installation:
The site is excavated and leveled, followed by a layer of compacted gravel for drainage. A moisture barrier and steel reinforcement mesh are placed before the concrete is poured. Once cured, the container is either bolted down using embedded anchors or welded to surface plates.
Container Strip Foundation
Strip foundations are long concrete footings that run along the container’s load-bearing sides.
They’re ideal for residential container homes in areas with moderately stable soils, where a full slab isn’t needed but piers alone aren’t enough. This foundation type uses less concrete than a slab and is considered permanent.
Installation:
Excavate trenches along the container’s long sides. After placing formwork and reinforcement, pour concrete into the strips. Embedded anchor bolts or plates are positioned before the concrete sets. The container is then lowered and fixed directly onto the strips using bolts or welds.
Container Pile Foundation
Pile foundations use deep-set steel or concrete columns driven into the earth to anchor the container.
This method is best suited for coastal areas, flood-prone regions, or soft, unstable soils where surface foundations won’t hold. It’s a fully permanent and engineered solution, often used for large or elevated structures.
Installation:
Piles are driven deep until they reach stable ground. Concrete pile caps or steel plates are installed at the top. The container is then placed and secured with bolts or welds, typically at each corner and any mid-span supports.
Container Raft Foundation
A raft foundation is a thick, reinforced concrete slab that “floats” over weak or expansive soil.
It spreads the load across a larger area, making it perfect for soft or shifting soils where even weight distribution is crucial. Raft foundations are fully permanent and often used in residential or institutional builds.
Installation:
The entire area is excavated and compacted. A waterproof membrane and steel reinforcement are laid before pouring the concrete slab. Containers are placed once the slab has cured, then anchored using embedded bolts or connection plates.
Container Skid Foundation
Skid foundations are long steel or heavy timber beams that run underneath the container, similar to sled runners.
They work well for temporary or mobile setups, especially on firm, compacted ground. Skids are semi-permanent and often used for site offices or mobile units.
Installation:
Place the skids directly on a gravel or block base. The container is mounted on top and either welded or bolted to the skids. This setup can be moved relatively easily with the right equipment.
Container Pad Foundation
Pad foundations use individual concrete pads or blocks positioned under each container corner.
Best for flat sites with solid ground, this is a low-cost, semi-permanent solution often used for temporary housing or storage. While simple, it still needs proper leveling and alignment to avoid shifting.
Installation:
Compact the ground and place precast or poured-in-place pads. Ensure all pads are level. The container is then placed on top and secured via bolts or twist locks attached to steel base plates.
Container Jack Foundation
Jack foundations use adjustable steel jacks to support and level each container corner.
They’re great for sloped sites, frequent relocations, or projects that require height adjustments. Jacks are a temporary solution and work best when paired with ground plates or pads for stability.
Installation:
Set the jacks on firm ground or steel plates. Raise or lower each jack until the container is perfectly level. Lock in place and secure using twist locks or temporary straps.
Container Screw Foundation
Screw foundations involve large steel screws that are twisted deep into the ground, acting like heavy-duty anchors.
This type is best for fast installations, medium-load projects, and areas with moderate to firm soil. Screw foundations are semi-permanent, require minimal excavation, and are ideal for light container homes or cabins.
Installation:
Use machinery to drill the screws into the ground. Attach top plates that align with the container’s corners. The container is then bolted to the screws, usually at the corner castings.
Container Block Foundation
Block foundations use concrete or cinder blocks stacked at container corners and midpoints.
This is a DIY-friendly, temporary option ideal for storage containers or budget builds on flat, dry land. However, it’s not recommended for long-term or multi-unit setups due to limited stability.
Installation:
Level and compact the site. Stack blocks to the needed height and ensure they’re aligned. Place the container carefully and add steel shims if needed for final leveling. Containers can be secured using straps or bolts if necessary.
So, Which One Is Best?
There’s no one-size-fits-all answer—but if you’re looking for stability and longevity, a slab or pile foundation tends to offer the most durable performance. For mobility and ease of installation, screw or pad foundations strike a solid balance. And for those on a tight budget, block or skid setups provide a quick solution, especially for temporary use.
As a prefabricated steel structure container building manufacturer, we don’t supply foundations directly—but we do help our clients match their container design to the right foundation type. We also provide anchor bolts, embedded parts, and other structural connectors to ensure seamless integration between your container and its base.
How to Choose the Right Foundation for Your Shipping Container
Finding the right foundation comes down to matching your site conditions, container purpose, and long-term plans. Here’s how to think it through.
Soil Conditions
Your soil is the first thing to evaluate. Different types behave differently:
- Clay expands when wet and contracts when dry—risking uneven support.
- Sand drains well but can shift under pressure without proper compaction.
- Bedrock offers excellent support but may increase drilling or leveling costs.
If the site has poor drainage, elevating the container and adding moisture protection is essential. In freezing regions, foundations must extend below the frost line to prevent ground movement during freeze-thaw cycles.
Container Purpose
Match the foundation to how the container will be used:
- Temporary use → Skids, jacks, or concrete blocks are often enough.
- Permanent home or office → Go for slab, strip, or pile foundations.
- Relocatable or modular use → Screw piles or steel frames make future moves easier.
Budget and Complexity
Not every project needs a full concrete solution. Consider:
- Tight budget → Crushed gravel + precast pads or blocks
- Mid-range budget → Strip footings or compacted piers, often DIY-friendly
- Higher-end → Slabs or piles, may require heavy equipment and pro installation
Building Codes
Local building regulations can influence your foundation options, especially for permanent structures.
- Some regions mandate a specific foundation type to approve the build.
- If the foundation is permanent, permits are often required—plan for the extra time and cost.
Moisture and Ventilation
Containers sitting directly on the ground are prone to rust and poor airflow. The fix:
- Raise the container at least 10 cm off the ground.
- Use a moisture barrier or ventilation gap in humid or wet climates to prevent long-term damage.
Wind and Seismic Risks
If your site is in an area with strong winds or seismic activity, foundation choice becomes even more important:
- In high-wind zones, use anchor bolts, ground screws, or earth anchors.
- In seismic regions, choose flexible connectors and consider reinforced slab or pile foundations for added safety.
Future Expansion
Planning to stack containers or expand later? Start with a foundation that supports growth. Look for:
- Load capacity rated for two or more levels
- Embedded anchors or plates to simplify future attachment
Quick Reference
- Most affordable → Crushed gravel + concrete blocks
- Most stable → Concrete slab or deep pile
- Most flexible → Screw piles or steel skids
- Best for moisture → Elevated pier with sealed concrete pad
Always choose your foundation based on a combination of soil conditions, building use, and budget—then think long-term about expansion, mobility, and weather protection.
Build a Solid Foundation and Take the Next Step in Your Container Journey
Choosing the right foundation is step one toward a reliable container building—whether you’re creating a simple office or a multi-unit container home. From supporting weight to protecting from moisture and seismic risks, the foundation ensures long-term durability.
At SteelPRO PEB, we specialize in customized prefabricated container homes designed for real-world use. While we don’t provide on-site foundations, we do offer:
- Foundation-friendly structural design
- Connection hardware for anchoring and stability
- Professional support to align your foundation with your build
Now that you know how to pick the right container foundation, you’re ready for the next step. Check out our detailed guide: How to Build a Shipping Container Home: The 10 Most Complete Steps You Should Know
Let’s help you build smarter, stronger, and faster—right from the ground up.