Modular buildings offer quick construction, cost savings, and flexibility, but to keep them running smoothly, regular maintenance is a must. Proper care ensures the structure stays durable, safe, and efficient for years. In this article, we’ll provide 5 simple tips to help you safeguard your investment and prevent costly repairs. Keeping your modular building in great shape doesn’t have to be hard—just a few simple steps can make a world of difference. Stay ahead of the game and keep your building strong, reliable, and secure.
1. Correctly Set Up HVAC Systems
A properly functioning HVAC system is crucial for ensuring comfort and air quality in modular buildings. Here’s how to ensure it’s set up properly:
- Accurate Load Calculation: Calculate the load based on your building’s size, usage, and climate. For example, an office building with lots of people and equipment needs more cooling than a storage facility, which needs more ventilation.
- Choose the Right HVAC Equipment: After the load calculation, pick the right HVAC unit. Small modular buildings may need a split-type air conditioner, while larger, multifunctional buildings (offices, dining, lodging) work better with a centralized chilled water system. Make sure the unit meets peak demand without excess capacity to avoid energy waste.
Set your heating no higher than 72°F and cooling no lower than 68°F. This balance ensures comfort and energy efficiency.
By carefully planning and selecting the right system, you can maintain a comfortable and energy-efficient environment year-round.
2. Clean Your Modular Building
Regular cleaning of your modular building is crucial not only for aesthetic reasons but also for long-term maintenance. Here’s what you need to keep in mind:
Exterior Cleaning: Identify the building’s material first. For glass curtain walls, use a soft scraper and neutral glass cleaner. For metal panels, use a mildly acidic cleaner (no more than 5%) to prevent corrosion.
High-Rise Cleaning: For multi-story buildings, use specialized equipment like suspended scaffolds or rope access (spider-men). Workers must have proper certification and safety gear. Clean top to bottom to let dirt and water fall naturally, avoiding re-contamination.
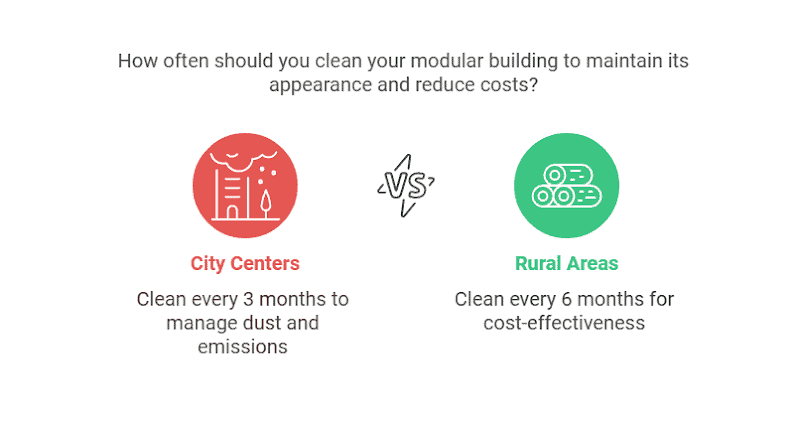
By following these steps, you’ll not only keep your building looking great but also protect it from damage caused by dirt, pollutants, and environmental wear.
3. Pay Attention to Your Roof
Keeping an eye on your modular building’s roof is essential for long-term performance and safety. Here’s what you should focus on:
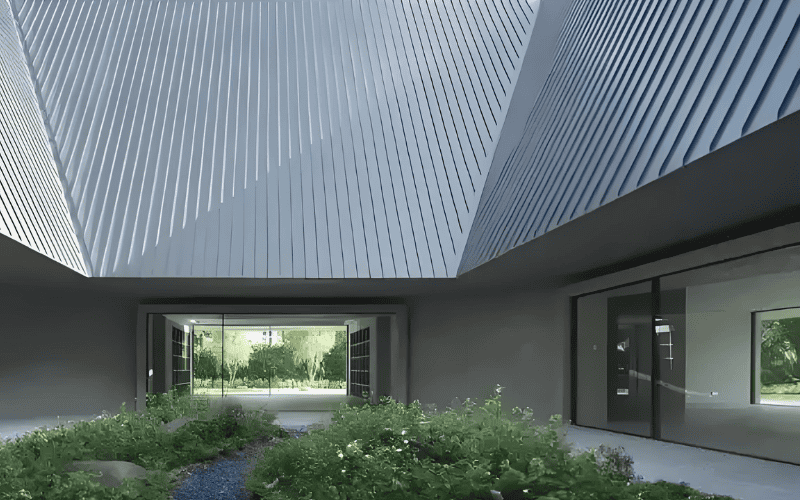
After storms, hail, or strong winds, check for holes, tears, or damage that could weaken the structure. Before climbing, wear a hard hat, non-slip shoes, and a harness attached to a solid part of the building, like a steel beam. For steeper roofs, use ropes and climbing hooks.
- Start with a ground check using binoculars to spot dents, lifts, or discoloration.
- Focus on high-risk areas like the ridge, eaves, vent outlets, and chimneys.
- On the roof, inspect it section by section.
- Begin with the gutters, checking for blockages or damage. For metal roofs, ensure panels are secure and free of corrosion.
Additionally, most modular buildings, like ours, use galvanized steel roofs. The zinc coating boosts the roof’s toughness and helps absorb hail impacts through elastic deformation, but regular checks are still important. Even with these benefits, wear over time can affect roof performance.
4. Avoid Extra Holes in Walls (Interior or Exterior)
It’s crucial to avoid drilling extra holes in the walls of your modular building, whether interior or exterior. Here’s why:
Structural Integrity: Modular walls are engineered with a frame and insulation. Drilling holes can cut through reinforcing steel and disrupt load distribution. Even small holes in load-bearing walls can increase failure risk by up to 30% under stress, like during earthquakes or high winds.
Waterproofing: The exterior walls are sealed to form a strong waterproof barrier. Drilling holes can weaken this layer, increasing the risk of water infiltration by 40-50%, leading to moisture damage, mold, and structural deterioration.
Non-Destructive Alternatives
If you need to install new equipment or run lines in your modular building, here are some non-destructive options:
- Surface-Mounted Conduits: Use surface-mounted conduits for electrical or data lines along walls or ceilings. These are simple to install and can be adjusted or modified later.
- Use Existing Channels: Utilize existing channels in the structure for wiring, plumbing, or data lines to avoid drilling.
- Wireless Technology: For electrical or data needs, explore wireless systems that reduce the need for physical wiring.
- Magnetic Mounts or Clips: For temporary setups, magnetic mounts or adhesive clips can hold cables or equipment without causing damage.
Before making any modifications, always consult the building’s blueprints to understand the wall’s design and avoid unintended damage. Taking these precautions can save you from costly repairs and safety hazards.
5. Check and Seal Your Piping System
Inspect your piping system regularly for leaks or damage. Properly sealed and insulated pipes boost efficiency and prevent energy loss. Watch for mold—if found, call your HVAC contractor for immediate help.
Inspection Schedule: For commercial modular buildings, inspect pipes every quarter. Residential buildings need inspection every six months. Use tools like thermal imaging or leak detectors to check hidden pipes in walls, floors, or ceilings.
Sealing and Insulation: Pipe connections are common leak points. Tighten bolts and apply quality sealant during inspections. For hot and cold pipes, use rubber foam insulation or pipe wraps to reduce heat loss or cold air leakage and maintain efficiency.
Don’t attempt to fix major piping issues yourself. Improper sealing or insulation can cause energy loss, water damage, or system failure. It’s more cost-effective and safer to hire a pro with the right tools and experience to ensure everything is sealed properly and up to code.
Related Reading: 15 Essential Modular Winterizing Tips to Keep Your Home Warm and Safe
Modular Buildings That Make Your Life Easier
By following the 5 tips in this guide, you’ll keep your modular building comfortable, energy-efficient, and cost-effective. We recommend making these best practices part of your regular maintenance routine, as it’s a great way to show your commitment to great facility management. And remember—along with these tips, it’s a good idea to arrange for a professional inspection every 1-2 years. Focus on checking the connections between modules, like loose bolts or cracks in welds, to avoid any surprises down the road.
At SteelPRO PEB, we provide modular products, including temporary modular buildings, with warranties that span decades, giving you peace of mind knowing your investment is fully protected. Whether you need a permanent facility or a temporary solution, we’re here to help. For more tips on modular building maintenance, just reach out! Let’s collaborate to create healthier, more sustainable modular spaces for all.