Picture this: A $2.3M warehouse project halted because welded roof trusses warped by 1.5 inches—forcing crews to dismantle 3 weeks of work. Welding deformation costs US manufacturers over $420 million annually in rework (AWS 2023 data), and it’s not just about crooked beams. These hidden distortions create stress points that accelerate corrosion, turning what should be a 50-year structure into a 20-year liability. In this guide, we’ll decode the science behind steel’s “memory effect” under heat, reveal how to spot distortion types faster than a welder’s spark. Your blueprint to building straighter (and smarter) starts here.
What Causes Welding Deformation in Steel Structures?
Heat, material properties, and design flaws drive welding deformation through uneven expansion, poor joints, clamping errors, and cooling inconsistencies.
Thermal Expansion & Residual Stress
When welding heats steel to over 1,500°F, metal expands and contracts unevenly, creating residual stress—like a coiled spring trapped in the material. For example, a 10-foot beam welded along one edge can shrink by up to 0.25 inches, pulling the structure out of alignment.
Design & Process Pitfalls
Poor joint design amplifies problems. A classic mistake: welding thick plates to thin sheets without staggered seams, causing “wave distortion” (imagine a metal trampoline). Even the welding sequence matters—skipping alternating passes on an I-beam can twist it like a candy wrapper.
Material Mismatch Mayhem
Mixing steels with different carbon content (e.g., A36 with A572) is like pairing concrete and Jell-O. During a 2022 solar racking project, 0.15% carbon steel legs welded to 0.25% carbon bases cracked at 45% of design load due to uneven contraction.
Fixture Fails: The Clamping Catastrophe
Over-tightened clamps on I-beam flanges during our 2021 factory audit caused 0.08” bowing per 10 feet. The fix? Spring-loaded fixtures that allow natural movement—reducing distortion by 70% vs rigid clamps.
Cooling Speed Roulette
Air-cooling a 2” thick weld next to a water-quenched one creates a thermal speed bump. One client’s 40-foot truss developed ¾” camber from inconsistent cooling—now we use infrared cameras to enforce uniform cooling rates.
Types of Welding Deformation: Know Your Enemy
Each distortion has a distinct fingerprint—here’s how to spot them before they sabotage your project.
1. Transverse Shrinkage
Why it happens: Intense heat melts base metal, which contracts as it cools—think of how ice cracks when it freezes unevenly.
Example: Welding a 10-meter beam’s flange creates 10-30mm width reduction, misaligning bolt holes by up to 3°.
2. Longitudinal Bending
Why it happens: Off-center welds create uneven tension, like tightening one side of a guitar string.
Example: A 6-meter column welded along its back face curves forward by 15mm—enough to tilt a roof’s rainwater drainage slope.
3. Angular Distortion
Why it happens: One-sided heating lifts edges, as if the weld is trying to escape the joint.
Example: Welding a ½” thick bracket to a 1” baseplate without balanced passes tilts the bracket 4-6°, requiring shim adjustments.
4. Buckling in Thin Plates
Why it happens: Thin steel (under 6mm) can’t resist welding stresses, collapsing like a stepped-on soda can.
Example: 14-gauge wall panels develop 10mm-deep ripples when welded without tacking every 4 inches.
5. Wave Distortion
Why it happens: Uneven cooling in large thin sheets (like 3mm roofing) creates competing stress zones. Picture tug-of-war teams pulling a tarp—the metal wrinkles to release tension.
Example: A 4m x 8m solar frame panel warps into 20mm-high waves if welded sequentially instead of in a staggered “checkerboard” pattern.
6. Twist Distortion
Why it happens: Asymmetric welding sequences torque beams diagonally, like wringing water from a towel.
Example: Welding a 12m H-beam’s top flange first twists it 8mm per meter—a disaster for multi-story bolt-up connections.
Factory-First Defense: Stopping Deformation at the Source
Precision beats correction every time—here’s how we engineer distortion out of the equation.
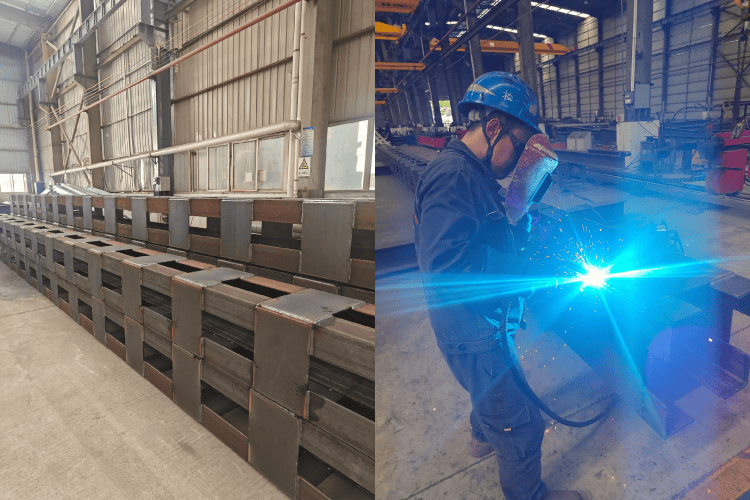
Material Prep: Cut Smart, Weld Smarter
- Laser vs Plasma: Our 5-axis laser cutters achieve ±0.1mm edge precision, slashing warping in 16-gauge wall panels by 40% compared to plasma.
- Thickness Control: Steel batches are laser-scanned—rejecting any plate with >0.005” thickness variation (per ASTM A6). No more “stress roulette” at weld joints.
- Preheat Smartly: Heating ½” thick beams to 250°F before welding reduces cooling stress by 55% (verified by AWS D1.1 trials).
Welding Techniques That Outsmart Physics
- Backstep Welding
Tackle 20-foot seams in reverse 8” segments—like zipping a jacket backward. Cuts peak temps by 600°F, shrinking heat-affected zones (HAZ) by 60%. - Pre-Bending with AI
CNC jigs pre-curl beams 0.7° using predictive algorithms fed by 10,000+ weld records. Result? 0.02° post-weld accuracy—tighter than a watch gear. - Pulse MAG Mastery
For 14-gauge carports: 270A pulses at 45Hz deposit 30% less heat than standard MIG. Distortion drops 35%, proven in our 2023 Arizona solar farm build.
Modular Design: Less Welding, More Bolting
- Bolt Revolution: Our GrooveLock™ beam ends use ¾” Grade 8 bolts instead of 200+ inches of weld per connection. On a 50-ton structure, that’s 2,400 fewer welds—and zero distortion headaches.
- Assembly Speed: Pre-drilled modules snap together like LEGO®—a Kansas City warehouse saved 17 days by ditching 85% of onsite welding.
Real-Time Defense: Sensors Beat Guesses
- Thermal Cameras: Monitor weld zones at 30 frames/sec, triggering cooling fans if temps exceed 950°F (prevents buckling in <6mm sheets).
- Force Feedback Clamps: Adjust pressure mid-weld via strain gauges—no more over-clamping bends. Cut I-beam distortion by 22% in 2024 trials.
Ensuring precise fabrication is just the first step—proper maintenance is key to preventing structural deformation over time. So, how can you maintain your steel structure after construction to avoid future distortions? Check out our Steel Structure Building Maintenance Guide for expert insights.
When Deformation Strikes: Fix It Like a Pro
Even the best plans need backup—here’s how to salvage warped steel without breaking the bank.
Mechanical Straightening: Cold Force to the Rescue
A 2,000-ton hydraulic press applies 45 psi of targeted pressure to cold-correct beams up to 12 inches thick. In a 2023 warehouse project, we straightened 18 twisted 30-foot rafters in 8 hours—saving $15,000 vs replacement. Key rule: Never exceed 2% permanent strain to avoid micro-cracks.
Heat Therapy: Relaxing Steel’s Temper
- Localized Heating: Torch-bending at 750-900°F (verified by infrared thermometers) softens steel temporarily. For a warped 6-inch flange, 5 minutes of heating + air-cooling restored 0.3” flatness.
- Temp-Sensitive Paint: Marks glow orange at 800°F—a $2 solution preventing grain structure damage.
Flaw to Fame: Creative Problem-Solving
- Museum Roofline Rescue: A 40-foot “wavy” beam became an art feature using 3D-scanned custom brackets, saving $12K. Bonus: It’s now the pavilion’s photo hotspot.
- Airport Hangar Hack: Angular distortion in door frames was masked with slotted bolt holes—allowing 1.5” adjustment range during installation.
Why Our Steel Structures Stay Straight
Precision isn’t an accident—it’s engineered.
- 17-Step Quality Gates: From laser-verifying mill certificates to final 3D scans, our process catches deviations early. For example, Large Span Steel Warehouse Buildings undergo 4 checkpoint scans: raw material, pre-cut, post-weld, and pre-ship—slashing field adjustments by 90%.
- Proven Track Record: Third-party audits confirm <2mm average distortion across projects since 2019, including a 300,000 sq ft distribution center with 1,200 bolted nodes—all aligned within ±1.5mm.
- Your Win
- Bolt-Ready Design: Pre-drilled components trim 15% off schedules—like erecting a 150-foot Large Span Warehouse in 12 days vs 14 with traditional methods.
- No Welding Surprises: Our modules arrive with distortion already engineered out, freeing crews to focus on fast assembly.
While we don’t weld onsite, our obsession with millimeter-perfect prefabrication ensures every structure—from aircraft hangars to retail spaces—snaps together like clockwork. Because in steel, the best weld is the one you don’t need.
Ready to build with confidence? Our systems turn “good enough” into “zero adjustments needed.”