In the world of steel structures, the main beams, columns, and frames often get most of the attention. However, the often-overlooked stamped metal parts play a crucial supporting role behind the scenes. While they aren’t the primary load-bearing components of a steel structure, these parts are essential for improving functionality, reducing costs, and speeding up construction.
Understanding the basics of metal stampings can help you better plan your projects, optimize designs, and manage costs. In this article, we’ll explore their definition, functions, applications, types, and material choices, giving you a quick overview of how they fit into steel structures.
What Are Stamped Metal Parts?
Stamped metal parts are metal components made using the stamping process. This method involves using molds and presses to shape metal sheets into the desired form and size. The stamping process is known for its efficiency, precision, and suitability for large-scale production, which makes metal stamping parts widely used across various industries, including steel construction.
Key Features:
- High Precision: The mold design ensures consistent dimensions for each part, making it ideal for applications that require tight tolerances.
- Thin-Walled Design: Stamped parts are typically made from thin metal sheets, which keeps them lightweight while still providing enough strength for non-load-bearing needs.
- Cost-Effective: Compared to machining or casting, stamping results in less material waste and higher production efficiency, making it perfect for mass production.
💎Stamped Metal Parts and Steel Structures
In steel construction, metal stampings are used as supporting components rather than the primary load-bearing elements. Their main function is to support, connect, or enhance the primary structure. For example, a simple angle bracket or support may seem insignificant, but these small details are crucial in maintaining the overall stability and functionality of the steel structure.
Why Use Stamped Metal Parts in Steel Structures?
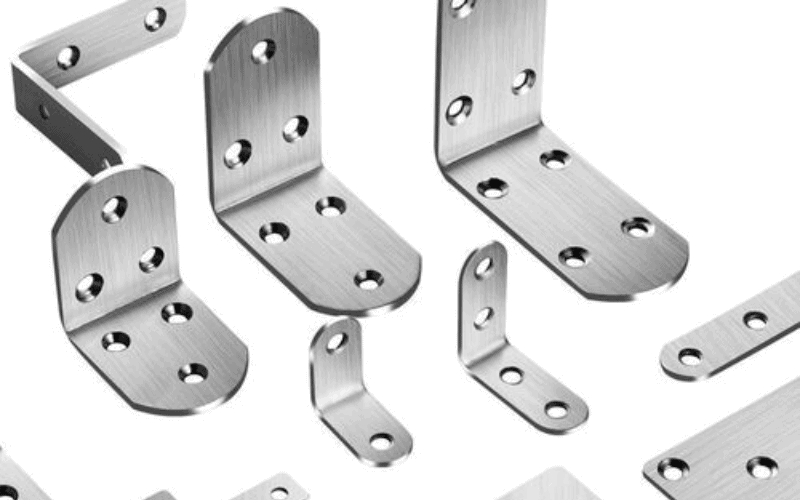
While metal stamping parts may not be the core components in steel structures, their role is far from insignificant. Here are the key functions and benefits they bring to steel construction:
Key Functions:
- Connection and Fixing: Parts like bolt washers, angle brackets, and connector plates are used to securely join different sections of the steel structure.
- Lightweight Support: Components like brackets and reinforcement ribs provide additional stability or support for lighter structures.
- Aesthetics and Protection: Items such as decorative panels and dust covers not only enhance the appearance but also protect the structure from environmental elements.
Core Advantages:
- Cost-Effective: The stamping process is highly efficient in material use and suited for mass production, which helps significantly reduce manufacturing costs.
- Fast Delivery: With high production efficiency, stamped metal parts can be quickly delivered, making them ideal for time-sensitive projects.
- Flexible Design: Stamping can create complex shapes, such as ventilation holes or custom fasteners, allowing for a wide range of design possibilities.
By providing these functions and advantages, stamped metal parts contribute to greater efficiency, lower costs, and increased design flexibility in steel structure projects.
When & Where Are They Used?
Stamped metal parts have a wide range of applications in steel structures. Here are some typical examples:
- Industrial Buildings: Equipment brackets, pipe fittings, lightweight fencing, and similar components.
- Commercial Buildings: Curtain wall connectors, decorative trims, ceiling grid parts, and other fittings.
- Infrastructure: Cable trays, ventilation system covers, signage bases, and more.
- Residential Projects: Lightweight stair treads, balcony railing components, and other accessories.
📌Usage Guidelines
- Non-Load-Bearing or Low-Load Areas:
Stamped metal parts are typically used in areas that don’t bear heavy loads, such as connectors, decorative elements, or lightweight supports. - Used in Conjunction with Main Structure:
These parts are usually welded or bolted to the main steel framework, helping to ensure the overall stability of the structure.
Common Types of Stamped Metal Parts
Stamped metal parts come in various forms, each with its own specific use in steel construction. Here are some of the most common types and their typical applications:
Type | Typical Use | Example Shapes | Manufacturing Method | Connection Method |
Brackets | Reinforcing beam-column joints, equipment mounting | L-shaped/U-shaped brackets, angle plates | Precision stamping, bending | Welding, bolting |
Covers | Pipe protection, aesthetic enhancement | Perforated covers, decorative trim | Stamping, punching | Bolted, snap-fit |
Supports | Stabilizing light frames, securing temporary structures | Z-channel fittings, reinforcement ribs | Stamping, cutting | Welding, bolting |
Clips | Securing cables/pipes, panel fasteners | Spring clips, snap-fit fasteners | Stamping, spring forming | Self-locking, snap-fit |
Shims | Adjusting alignment or height differences | Thin metal sheets, standard round shims | Stamping, cutting | No connection, placed directly |
End Plates | Beam-column connections, structural reinforcement | Square, rectangular plates | Laser cutting, stamping | Welding, bolting |
End Caps | Pipe closure, protecting steel surfaces | Pipe caps, column end covers | Stamping, hot forming | Direct fitting, adhesive |
Plugs | Waterproofing, dust protection, blocking holes | Plastic/metal plugs | Injection molding, stamping | Insertion, press-fit |
Though these parts vary in shape and function, they are all efficiently and precisely manufactured using the stamping process, offering a wide range of solutions for steel construction projects.
Common Materials of Stamped Metal Parts
The material selected for stamped metal parts directly affects their performance and lifespan. Here are some common materials and their suitable applications:
- Low Carbon Steel: Cost-effective and easy to process, ideal for indoor dry environments like connectors or brackets.
- Galvanized Steel: Zinc coating provides rust protection, making it suitable for outdoor or humid environments, such as curtain wall connectors or fencing accessories.
- Stainless Steel: Highly resistant to corrosion and strong, perfect for high-corrosion environments like chemical plants or coastal buildings.
- Aluminum Alloy: Lightweight, corrosion-resistant, and aesthetically appealing, used for decorative parts or lightweight applications, such as curtain wall trims or signage bases.
- Copper Alloy: Strong corrosion resistance and good electrical conductivity, ideal for electrical connectors or other specialized parts.
- High-Strength Steel: Designed for heavy load and strength requirements, commonly used in equipment supports or structural joints.
- Alloy Steel (e.g., Chromium-Molybdenum Steel): Excellent heat and wear resistance, suitable for high-strength load-bearing applications.
📝 Material Selection
- Outdoor/Humid Environments: Galvanized steel or stainless steel is recommended, especially for building exterior connections or fences, offering corrosion protection.
- High Strength Requirements: For parts carrying heavy loads, such as industrial equipment supports, high-strength steel (e.g., Q345 steel) or alloy steel is ideal.
- Lightweight Requirements: For components that need to be lightweight, such as decorative parts, aluminum alloy is recommended due to its corrosion resistance and lightweight.
- Extreme Environments: For highly corrosive environments (e.g., chemical plants or coastal regions), stainless steel (such as 304 or 316) should be selected to ensure durability.
By choosing the right material, you can ensure that stamped metal parts perform optimally and have a long service life in steel structures.