Imagine the Eiffel Tower swaying gently in the wind or the Sydney Opera House resisting seismic waves. These iconic steel structures don’t just rely on raw strength—they depend on hidden “joints” that work like biological ligaments, transferring forces seamlessly between beams, columns, and floors.
At the heart of these connections lies a humble yet mighty hero: the shear plate. Often overlooked but indispensable, this unassuming steel plate acts as a silent guardian against sideways forces that threaten to tear buildings apart.
In this article, we’ll unpack how shear plates become the ultimate team players in steel structures—no engineering degree required. You’ll discover:
- Why are shear plates the “handshake” between steel members?
- How they turn chaotic forces into orderly teamwork.
- Practical insights for both technical and non-technical readers.
Ready to see steel structures in a whole new light? Let’s dive in! 🚀🚀🚀
Table of Contents
3 Essential Concepts to Know Beforehand
Before we explore shear plates, let’s demystify three foundational ideas—think of them as the “ABCs” of steel connections.
1. Shear Force
Imagine cutting a piece of paper with scissors. The blades don’t push straight down; they slide past each other, creating a sideways “slicing” force. That’s shear force—a sneaky, parallel action that tries to slide one part of a structure against another.
Why it matters in buildings:
- Wind gusts pushing sideways on a skyscraper.
- Earthquake waves shaking a bridge’s supports.
- Heavy machinery vibrating a factory floor.
Picture a steel beam bending like a diving board. Shear force is what causes its internal layers to slide like a deck of cards (but steel, thankfully, doesn’t fold that easily!).
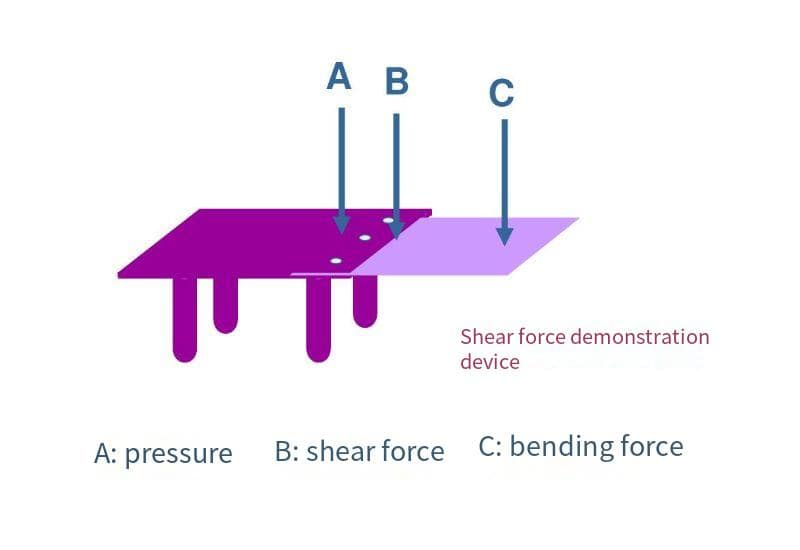
2. Shear Connection
A shear connection is like a handshake between steel members—it lets beams, columns, and braces share loads without slipping apart. Unlike rigid welds or flimsy pins, shear connections strike a balance: they allow some flexibility while keeping forces under control.
Think of Lego blocks. The studs on top and tubes underneath create a shear connection—they lock bricks together horizontally but can still be pulled apart vertically. In steel structures, shear plates and bolts play the role of those studs and tubes, but way stronger!
3. Yield Strength (Fy)
All materials have a limit. For steel, Fy (yield strength) is the stress level where it stops behaving like a spring (returning to its original shape) and starts permanently deforming.
- Stretch a rubber band gently—it snaps back (elastic behavior).
- Stretch it too far—it becomes loose and stays deformed (plastic behavior).
Why engineers care:
Shear plates are designed to operate below Fy, ensuring they handle forces without warping. For example, Grade 50 steel (Fy = 50 ksi) is a common choice, balancing strength and ductility.
What is a Shear Plate?
A shear plate is a flat, rectangular steel plate with pre-drilled bolt holes, typically welded or bolted at the intersection of beams and columns. Think of it as a metal handshake that binds steel members together while resisting sideways forces.
Key features:
- Material: Usually made of Grade 50 steel (Fy = 50 ksi) for optimal strength-to-weight ratio.
- Geometry: Thickness ranges from 12–25 mm (more on this later!), with bolt holes spaced to match standard connection designs.
- Placement: Nestled discreetly in beam-column joints, often hidden behind fireproofing layers.
😋 Fun fact: A standard shear plate for mid-rise buildings is about the size of an A3 sheet of paper—small enough to handle, strong enough to anchor a bus!
Why Use Shear Plates?
Imagine a steel beam welded directly to a column. At first glance, it seems rock-solid. But when shear forces hit—like during an earthquake—the concentrated stress at the weld can cause cracks to spiderweb outward. It’s like taping two sticks together; the joint becomes the weakest link.
Shear plates solve three critical challenges:
- Stress Distribution: They spread shear forces across a wider area, like distributing weight on a snowshoe instead of a high heel.
- Controlled Deformation: Bolted connections allow slight movement, absorbing energy during extreme events (unlike brittle welds).
- Modularity: Pre-fabricated plates speed up construction—no waiting for on-site welding or curing.
Data-Driven Impact:
In a 2023 shake-table test by the Steel Construction Institute, connections with shear plates survived 30% higher lateral loads than welded joints before failure. That’s the difference between a building swaying safely and collapsing catastrophically.
💡 Pro Tip: Shear plates also simplify retrofitting. Need to reinforce an old warehouse? Bolt new plates instead of tearing out old welds—a cost-saving masterpiece!
How Does a Shear Plate Work?
A shear plate acts like a friction-based handshake between steel members. Here’s the principle in three steps:
- Clamp Force: High-strength bolts are tightened to “hug” the shear plate against the beam and column. This creates massive friction between the surfaces—like squeezing a stack of paper so hard you can’t pull the sheets apart.
- Force Redistribution: When shear forces try to slide the beam sideways, the friction resists the movement, distributing the load evenly across the bolt holes.
- Fail-Safe: Even if friction is overcome (rare in proper designs!), the bolts shift into “bearing mode,” pressing against the plate’s holes like a pin in a hinge. This dual-action defense is why shear plates are so reliable.
Material Matters:
- The plate’s steel grade (e.g., Grade 50) ensures it stays rigid under pressure.
- Bolt pre-tension is calibrated to millimetre precision—too loose, and friction fails; too tight, and the steel could deform.
💡 Pro Tip: Engineers often add anti-slip coatings (like grit blasting) to the plate’s surface. It’s like adding treads to a tire—maximizing grip without changing the core design.
The Golden Formula: Shear Capacity (V = 0.6×Fy×A)
Every shear plate has a “breaking point”—the maximum shear force it can handle before failing. Engineers calculate this using a deceptively simple formula:
V = 0.6 × Fy × A
Let’s decode the variables:
- V: Shear capacity (the plate’s “force limit” in kips or kN)
- Fy: Yield strength of the steel (its “stress tolerance” in ksi or MPa)
- A: Effective shear area (the plate’s “force-carrying zone” in in² or mm²)
Fy – Steel’s Personality Test
- Think of Fy as the steel’s “stress threshold.” For example, Grade 50 steel (Fy = 50 ksi) starts to permanently deform at 50,000 pounds per square inch.
- Higher Fy = Stronger plate, but less ductility (like a stiff vs. stretchy rubber band).
A – The Real Estate of Force Transfer
- A isn’t just the plate’s total area—it’s the net area excluding bolt holes. Imagine cutting Swiss cheese: the cheese (steel) around the holes (bolts) does the actual work.
- Formula: A = Plate thickness × Effective width
The 0.6 Mystery Factor
- This safety multiplier accounts for real-world imperfections: minor misalignments, residual stresses, and conservative design practices.
- Fun analogy: It’s like a “buffer zone” on your car’s speedometer—even if it says 100 mph, you shouldn’t push it beyond 60 for long-term safety.
Engineer’s Cheat Sheet
Sample Calculation:
- Plate: Grade 50 steel (Fy = 50 ksi), thickness t = 0.5 in, effective width w = 6 in.
- A = 0.5 × 6 = 3 in².
- V = 0.6 × 50 × 3 = 90 kips (≈ 400 kN).
🎯 Translation: This plate can handle a shear force equivalent to lifting nine SUVs!
💡 Pro Tips:
- Always apply a safety factor (typically 1.5–2.0) to V for final designs.
- Bolt strength and spacing also impact capacity—never ignore connection details!
Shear Plates and Shear Connection
A shear plate is never a solo act—it’s the star player in a shear connection ensemble. Here’s how the team works together to keep structures rock-solid:
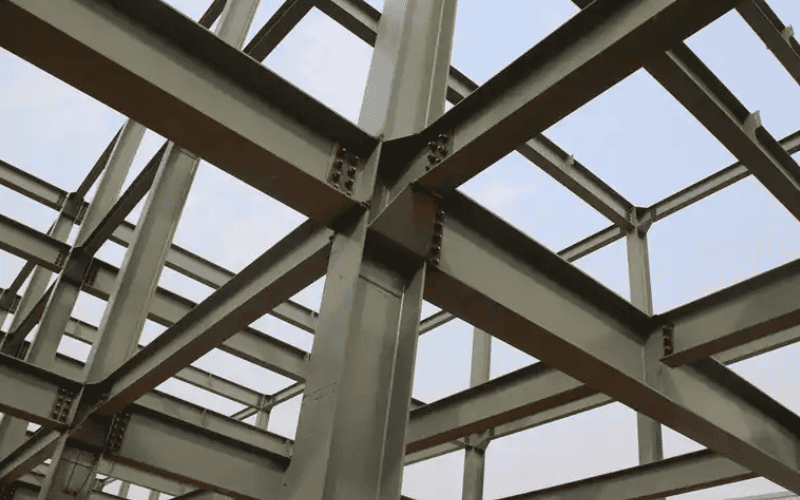
1. High-Strength Bolts
- Role: Apply clamping force to “activate” the shear plate’s friction grip.
- Material: Grade 8.8 or 10.9 bolts (the “Olympic weightlifters” of fasteners).
- Fun fact: A single M24 bolt can exert over 50,000 lbs of pre-tension—enough to lift a humpback whale calf!
2. Anti-Slip Coatings
- How they work: Grit blasting or sprayed metal coatings roughen the plate’s surface, increasing friction like sandpaper on ice.
- Pro tip: Coatings can boost shear capacity by up to 20%—a cost-effective upgrade!
3. End Plates
- Function: Welded to beam ends, they act as “bridges” that transfer forces smoothly into the shear plate.
- Design nuance: Thicker end plates = better load distribution (think of a wide snowshoe vs. a stiletto heel).
4. Stiffeners
- What they are: Vertical steel ribs welded to the shear plate or column.
- Why they matter: Prevent local buckling under extreme loads—like bookends keeping a shelf from sagging.
📌 In action, that is, when a steel beam meets a column:
- Beam end plate presses against the shear plate.
- Bolts clamp them together, activating friction.
- Stiffeners keep the column web from crumpling.
- Anti-slip coating ensures no sneaky sliding.
Shear Plate vs. Shear Key vs. Anchor Plate
Both shear plate and shear key include “shear,” but they’re as different as a wrench and a screwdriver. As for shear plate and anchor plate, both often use thick steel plates and bolts, and are critical for load transfer. It’s easy to get lost.
Let’s settle the debate once and for all.
Round 1: Shear Plate vs. Shear Key
Feature | Shear Key | Shear Plate |
Primary Role | Resists shear in concrete structures | Resists shear in steel structures |
Shape | Toothed or trapezoidal concrete blocks | Flat steel plate with bolt holes |
Material | Concrete (often pre-cast) | Structural steel (e.g., Grade 50) |
Installation | Embedded in concrete pours | Bolted/welded to steel members |
Typical Use Case | Dams, bridge abutments, foundations | Beam-column joints, steel frames |
Round 2: Shear Plate vs. Anchor Plate
Feature | Shear Plate | Anchor Plate |
Primary Force | Resists horizontal shear | Resists vertical uplift/tension |
Location | Beam-column joints, beam webs | Column bases, embedded in concrete |
Design Focus | Bolt friction + bearing capacity | Anchor rod embedment + pullout strength |
Failure Mode | Bolt shear/plate buckling | Concrete cone breakout |
Why Shear Plates Are Revolutionizing Construction
The Rise of Modular & Prefab Construction
Shear plates are the unsung heroes of the modular building boom. Their bolt-and-go design aligns perfectly with off-site fabrication:
- Speed: A shear plate connection takes minutes to bolt, vs. hours for welding.
- Precision: Factory-drilled holes eliminate on-site guesswork.
- Scalability: Identical plates can be mass-produced for skyscrapers or schools.
Case in point: A 2024 Dubai high-rise project cut steel erection time by 40% using pre-assembled shear plate modules.
Sustainability Meets Strength
In an era of green building, shear plates quietly support circular economy goals:
- Less Waste: No welding spatter or off-cuts.
- Reusability: Bolted plates can be disassembled and reused—unlike welded joints.
- Material Efficiency: Optimized thickness reduces steel consumption without compromising safety.
Pro Tip: Pair shear plates with recycled steel (e.g., A992) to shrink your project’s carbon footprint.
Seismic Resilience Without the Complexity
Modern codes like AISC 341 prioritize ductile connections in earthquake zones. Shear plates deliver:
- Controlled Yielding: Bolts allow gradual energy dissipation, preventing sudden failures.
- Ease of Inspection: Cracked welds are hard to spot; loose bolts are obvious.
Real-World Proof: After the 2023 Turkey earthquakes, retrofitted buildings with shear plates showed 80% less damage than welded counterparts.
Cost Efficiency: The Silent Game-Changer
- Labor Savings: Skilled welders cost $100+/hour; bolting crews are cheaper and faster.
- Error Reduction: Pre-drilled plates minimize field mistakes (no “oops” moments with a torch!).
- Insurance Perks: Some insurers offer lower premiums for bolted connections due to proven seismic performance.
Conclusion
Shear plates are more than just unassuming slabs of steel—they are the invisible choreographers of structural stability. From battling hurricane winds to absorbing seismic shocks, these plates ensure that every beam, column, and brace works in harmony. Their genius lies in their simplicity: by mastering friction, distributing forces, and embracing modularity, they embody the essence of smart engineering.
As cities grow taller and climates more unpredictable, shear plates will continue to evolve—embracing innovations like sensor-equipped bolts and AI-optimized designs. Yet their core mission remains unchanged: to hold our world together, one bolted connection at a time.
Next time you walk past a steel-framed building, remember: hidden within its joints are the silent guardians that let humanity defy gravity, one shear plate at a time.
Easter Egg: The Medieval “Shear Plates” of Notre-Dame
Long before modern engineering, medieval builders used a clever trick akin to shear plates in Notre-Dame Cathedral’s roof. Wooden beams were joined using iron cramps (metal straps) embedded in the stone—a primitive “friction grip” system that distributed forces and prevented collapse. Sound familiar?
When the cathedral’s spire burned in 2019, restorers found these 800-year-old cramps intact, proving that even ancient builders understood the power of force distribution. Notre-Dame’s secret? A rudimentary ancestor of today’s shear plates—because great engineering, it turns out, is timeless.