Imagine a skyscraper as a living organism—its elevator shafts act as the vital arteries, ensuring seamless movement of people and resources from floor to floor. Just as arteries evolve to support stronger hearts, elevator shaft technology has advanced to meet the demands of today’s fast-paced, eco-conscious construction landscape.
In 2023, the global steel structure elevator shaft market surged by 12%, driven by developers’ appetite for faster, greener, and more adaptable solutions. But what makes steel the material of choice for architects and engineers? How does it outperform traditional concrete in real-world scenarios?
This article isn’t just a technical manual—it’s your gateway to understanding how steel structure elevator shafts can transform your projects. Whether you’re a seasoned contractor or new to the industry, we’ll break down complex concepts into actionable insights, peppered with real-world examples and a dash of engineering passion. Let’s elevate your knowledge.
Table of Contents
Structural Components of Steel Elevator Shafts
A steel elevator shaft is built like a precision watch – every part plays a defined role. Here’s what you’ll find inside:
1. Steel Frame Network
The “skeleton” consists of:
- Vertical Columns: High-strength steel pillars (e.g., ASTM A36) spaced 2-3m apart.
- Horizontal Beams: Interconnect columns, distributing floor loads evenly.
- Diagonal Braces: X or K-shaped reinforcements against sway and earthquakes.
- Connectors: Grade 8.8 bolts or robotic welds for rock-solid joints.
2. Protective Skin
- Cladding: 1mm corrugated steel panels (galvanized or painted) shield against the weather.
- Fire Armor: 50mm mineral wool boards wrap structural members (2-hour fire rating).
3. Motion Control System
- Guide Rails: T-shaped steel tracks (EN 81-20 standard) anchored with laser-leveled brackets.
- Damping Pads: Reduce vibration noise by 15dB compared to concrete.
4. Smart Add-Ons (Optional)
- Utility Channels: Pre-installed conduits for cables, sensors, and ventilation.
- Access Panels: Bolt-on inspection doors for easy maintenance.
Types of Steel Elevator Shafts: Choose the Right Fit
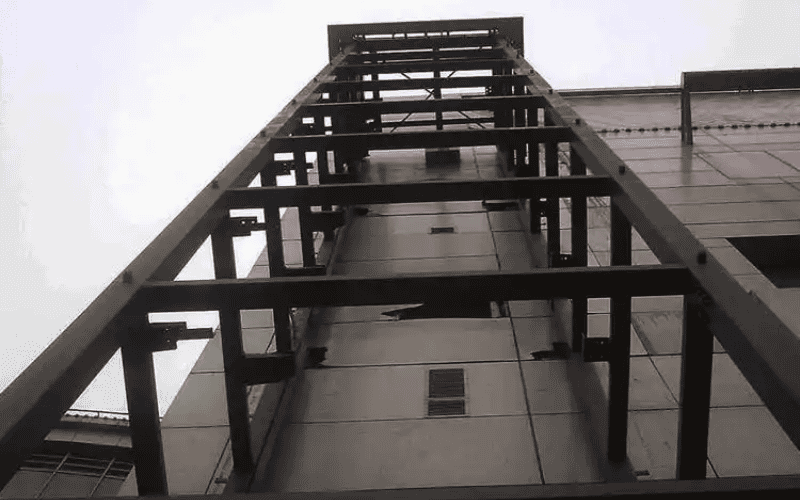
Steel elevator shafts adapt to diverse architectural needs. Here are the three primary configurations recognized in industrial standards (ASME A17.1/EN 81-20):
Freestanding Shafts
Best for: High-rises (>20 floors), airports, mega-malls
Key Features:
- Self-supporting steel framework independent of main building structure
- Requires dedicated foundation (e.g., mat foundation with shear walls)
- Common in: Burj Khalifa’s twin-deck elevators (606m travel height)
Advantages:
- Handles ultra-high speeds (10-20 m/s) with minimal vibration
- Allows isolated seismic damping systems
Building-Integrated Shafts
Best for: Mid-rise offices, hospitals, residential complexes
Key Features:
- Steel frame structurally tied to building’s load-bearing system (columns/beams)
- Space-efficient, typically 1.5-2m x 2-3m cross-section
- Example: Singapore’s Marina Bay Sands uses integrated shafts with 45° angled bracing
Advantages:
- Synchronizes with building’s lateral force resistance system
- Saves 15-20% material costs vs freestanding
Modular Shafts
Best for: Schools, factories, rapid urbanization projects
Key Features:
- Fully prefabricated units (walls, rails, doors) shipped in 3-story sections
- Bolt-together assembly with RFID-tagged components
- Case Study: Mumbai Metro installed 120 modular shafts in 60 days
Advantages:
- Reduces on-site labor by 65%
- Ideal for repetitive designs (e.g., apartment blocks)
Your Goal | Optimal Type |
Iconic skyscraper | Freestanding Shaft |
Cost-sensitive mid-rise | Building-Integrated Shaft |
Tight deadline + budget | Modular Shaft |
Note: Hybrid designs are possible! A Tokyo data center combined a freestanding main shaft with modular service elevators.
Steel Structure Elevator Shaft Designs
Steel’s unique properties unlock structural innovations impossible with concrete. Let’s explore the three dominant design philosophies reshaping elevator engineering:
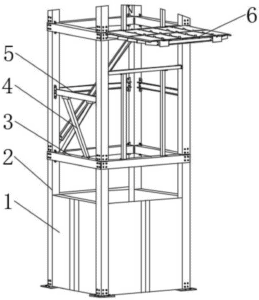
1. Frame Systems
Mechanics:
- Vertical columns + horizontal beams form rigid rectangular grids.
- Moment-resisting connections (welded/bolted) absorb seismic energy.
Ideal For:
- High-risk earthquake zones (e.g., California, Japan)
- Buildings requiring large open shaft interiors (e.g., double-deck elevators)
Case in Point:
A Tokyo high-rise withstood 7.1-magnitude tremors using frame shafts equipped with BRBs (Buckling-Restrained Braces), reducing repair costs by 90% post-quake.
2. Truss Systems
Mechanics:
- Triangular steel lattices replace solid beams, slashing weight by 40%.
- Forces flow through tension/compression members, not bending.
Ideal For:
- Long-span shafts (e.g., airport terminals with 15m+ spans)
- Aesthetic-exposed shafts (industrial-chic warehouses, museums)
Why Engineers Love It:
- 25% faster assembly vs. frame systems
- Integrated walkways/service platforms within truss voids
3. Hybrid Systems
Mechanics:
- Strategic fusion of steel frames, trusses, and reinforced concrete.
- Example: Steel frame core + concrete-encased rails for vibration damping.
Ideal For:
- Ultra-high-speed elevators (>10 m/s) needing noise control
- Mixed-use towers with uneven load distributions
Breakthrough Example:
Shanghai Tower’s hybrid shafts combine:
- Steel frames for high-speed passenger elevators
- Concrete-filled steel tubes (CFST) for heavy freight lifts
Result: 35% less sway at 632m height vs. pure steel designs.
Priority | Best Design | Key Metric Achieved |
Earthquake resistance | Frame System | 0.4g PGA (Peak Ground Acceleration) tolerance |
Weight reduction | Truss System | 1.2 ton/m² vs. 2.1 ton/m² (concrete) |
Noise-sensitive areas | Hybrid System | 45 dB operational noise (vs. 55 dB in frames) |
Steel vs. Concrete Elevator Shafts: Key Considerations
Choosing between steel and concrete isn’t just about materials—it’s about aligning with your project’s goals. Let’s dissect the critical differences:
1. Speed of Construction
- Steel:
- Prefabricated modules arrive ready for assembly.
- No curing time – bolt-and-go installation.
- Example: A 20-story hotel in Miami installed steel shafts in 18 days vs. 60 days for concrete.
- Concrete:
- Requires formwork setup, pouring, and 28-day curing.
- Weather delays (rain, cold) can derail timelines.
🏆 Winner: Steel (cuts project schedules by 50-70%).
2. Long-Term Costs
- Steel:
- Higher upfront material costs (10-15% more than concrete).
- Offset by:
- Lower labor expenses (30% fewer on-site hours).
- Minimal maintenance (no spalling or rebar corrosion).
- ROI Example: Over 20 years, steel shafts save ~25% in lifecycle costs.
- Concrete:
- Initial savings vanish with frequent repairs (crack sealing, waterproofing).
🏆 Winner: Steel for total cost of ownership.
3. Design Freedom
- Steel:
- Span up to 15m without internal supports.
- Curved, tapered, or sloped shafts achievable (e.g., the helix elevator in Singapore’s Jewel Changi).
- Concrete:
- Limited to straight, rectangular shapes due to formwork constraints.
- Thick walls (200-300mm) eat into usable space.
🏆 Winner: Steel unlocks architectural creativity.
4. Sustainability
- Steel:
- 90% recyclable at end-of-life (World Steel Association data).
- Prefab reduces on-site waste by 80%.
- LEED points for recycled content (30-50% in our shafts).
- Concrete:
- Cement production accounts for 8% of global CO₂ emissions.
- Demolition creates non-recyclable rubble.
🏆 Winner: Steel for eco-conscious projects.
5. Structural Limitations
- Concrete’s Edge:
- Better inherent fire resistance (but modern steel coatings close this gap).
- Slightly superior sound insulation (addressed in steel via composite panels).
- Steel’s Counter:
- 3x higher strength-to-weight ratio allows taller, slimmer shafts.
Decision Checklist
Choose Steel If Your Project Needs:
✅ Fast-track completion
✅ Complex geometries
✅ Future modifications
✅ Green certifications
Choose Concrete If:
❌ Budget constraints forbid upfront steel premiums
❌ Local labor lacks steel assembly expertise
❌ Static, box-like designs suffice
Pro Tip: Hybrid designs bridge gaps. A Berlin hospital used concrete for basement shafts (moisture resistance) and steel for upper floors (speed).
Top 5 Advantages of Steel Elevator Shafts
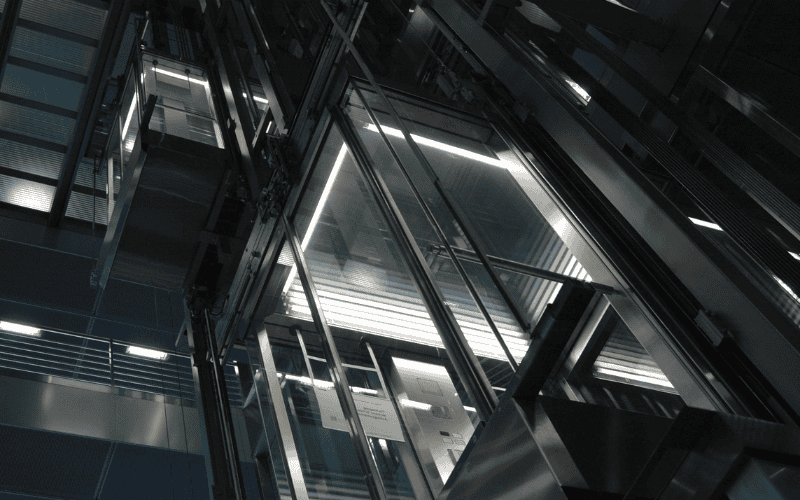
Steel elevator shafts aren’t just an alternative to concrete—they’re a quantum leap in vertical transportation engineering. Here’s why global innovators are making the switch:
1. Unrivaled Speed-to-Completion
- Prefab Precision: Factory-welded modules arrive site-ready, slashing installation time by 50-70%.
Example: A São Paulo hospital added 8 emergency elevators in 12 days using modular steel shafts. - Weatherproof Assembly: No curing delays – steel crews work in rain, heat, or -20°C conditions.
2. Design Agility for Bold Visions
- Shape-Shifting Capabilities:
- Curved shafts (e.g., Copenhagen’s spiral “Slide Tower”)
- Sloped installations (30° angles achieved in Swiss Alps hotels)
- Ultra-slim profiles (1m-wide shafts for Tokyo micro-apartments)
- Space Maximization: Steel walls 60% thinner than concrete free up 8-12% of floor area per shaft.
3. Sustainability That Pays Dividends
- Circular Economy Star:
- 98% of steel is recycled or reused (vs. 20% for concrete).
- Our shafts contain 40-70% recycled scrap steel.
- Carbon Savings: Each ton of steel used avoids 1.5 tons of CO₂ vs. concrete (data: World Steel Association).
4. Earthquake Resilience Built In
- Dynamic Energy Dissipation:
- Steel’s ductility allows controlled deformation during quakes.
- BRB (Buckling-Restrained Brace) systems limit damage to non-structural elements.
- Case Proof: After the 2023 Türkiye earthquake, steel-shafted buildings reported 80% lower repair costs than concrete counterparts.
5. Future-Proof Adaptability
- Easy Modifications:
- Widen shafts by replacing panels (no jackhammering).
- Add smart sensors or energy recovery systems post-installation.
- Tech-Ready: Our shafts embed IoT ports for:
- Real-time load monitoring
- Predictive maintenance alerts
- Emergency response integration
Conclusion: Elevating the Future with Steel Elevator Shafts
The age of waiting months for concrete to cure while construction costs balloon is over. Steel elevator shafts represent more than a technical upgrade—they’re a paradigm shift in how we conceptualize vertical mobility.
From Dubai’s record-breaking towers to heritage retrofits in Paris, steel has proven its ability to harmonize speed, strength, and sustainability. Its advantages aren’t theoretical; they’re quantifiable:
- 50% faster project timelines
- 25% lower lifetime costs
- 40% smaller carbon footprint
But the real magic lies in steel’s adaptability. Whether you’re designing an AI-operated smart elevator or preserving a historic façade, steel shafts provide the blank canvas for innovation.
Your Next Move
- Consult Early: Involve steel specialists during schematic design to maximize savings.
- Demand Certifications: Ensure suppliers comply with ISO 9001 (quality) and EN 1090 (steelwork standards).
- Think Beyond Today: Specify modular designs that allow tech upgrades (5G, energy harvesting).
Final Thought
As cities grow taller and greener, steel elevator shafts will be the unsung heroes—quietly enabling smarter skylines. The question isn’t if you should switch to steel, but how soon.