Table of Contents
What Is Beam Splice in Steel Structures?
In steel construction, beams are key structural components that support and transfer loads. However, due to transportation limits, design requirements, or site conditions, a single beam may not always be long enough for the job. That’s where beam splicing comes in.
Simply put, a beam splice is a technique used to connect two steel beams so that they function as one continuous unit. Think of it like “LEGO for steel structures” – carefully designed connections bring multiple sections together into a strong, unified whole.
What Does Splicing Mean in Construction?
In construction, splicing refers to the process of joining two structural elements together to create a longer or stronger member. This technique is widely used in steel, concrete, and wood structures to extend material length, optimize load transfer, and enhance stability.
For steel structures, splicing is essential for overcoming manufacturing and transportation limitations, reducing costs, and ensuring structural integrity. Whether it’s a steel beam, column, or reinforcement bar, splicing plays a crucial role in modern construction, enabling large-span designs and complex architectural forms.
Key Functions of Beam Splicing
- Extending Beam Length – When a single beam isn’t long enough to span the required distance, splicing allows for extension.
- Optimizing Transportation – Instead of struggling with oversized beams, sections can be transported separately and assembled on-site.
- Accommodating Complex Designs – Beam splicing is essential for special structures like curved beams or varying cross-section designs.
Basic Components of a Beam Splice
A steel beam splice typically consists of:
- Splice Plates – Steel plates that connect the beams, usually attached to the web or flanges.
- Fasteners – Bolts or welds that secure the splice plates to the beams.
- Reinforcement Elements – Stiffeners or additional support to improve stability in the splice zone.
What Is a Splice Joint in Steel Structures?
A splice joint is a specific type of connection used to join two structural members—such as steel beams—into a continuous load-bearing unit. This joint is designed to effectively transfer bending moments, shear forces, and axial loads while maintaining the structural integrity of the beam. In steel structures, splice joints can be either bolted, welded, or hybrid connections, each chosen based on project requirements and site conditions.
By ensuring a well-designed splice joint, engineers can optimize strength, durability, and cost efficiency while maintaining seamless load transfer across the splice zone.
Beam Splice vs. Traditional Single Beam
Compared to a continuous, single-piece beam, beam splicing offers:
- Flexibility – The ability to adjust the splice location and method as needed.
- Cost Efficiency – Reduces material waste, lowers transportation costs, and simplifies installation.
- Engineering Adaptability – Ideal for long-span structures and complex architectural designs.
Why Beam Splicing Matters
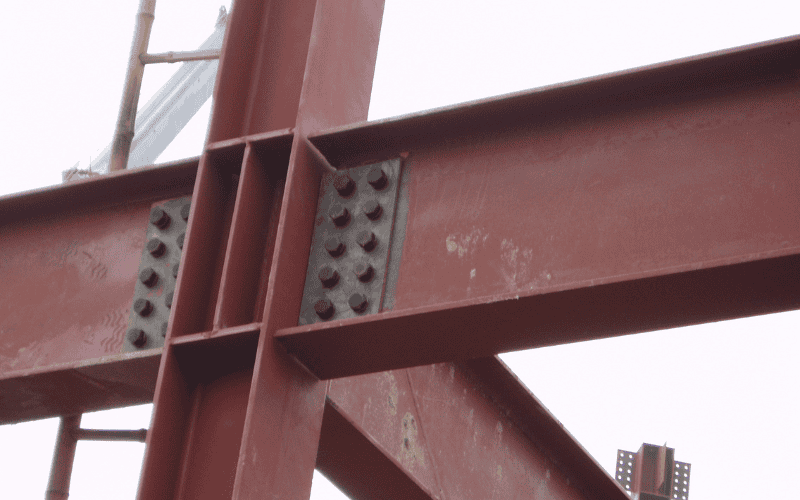
Beam splicing is a key technique in steel construction. It’s not only important for the practical side of projects but also plays a big role in the steel industry as a whole. Here are the main reasons why beam splicing is so valuable:
- Safety: Keeping Structures Stable and Reliable
- Good splicing designs help spread the load evenly, avoiding stress buildup that could cause parts of the beam to fail.
- A well-done splice can make the joint just as strong and stable as a single, continuous beam—and sometimes even better.
- Beam splicing helps distribute dynamic loads (like wind or earthquakes) more evenly, boosting the structure’s resistance to fatigue.
- Cost-Effective: Lowering Costs and Saving Materials
- Splicing allows shorter beams or leftover material to be reused, which helps lower costs and reduce waste.
- By breaking beams into sections for transport and splicing them on-site, you can save on transportation and installation costs.
- Using standardized splicing techniques can speed up production and reduce manufacturing expenses.
- Sustainability: Supporting Green Building
- Splicing reduces material waste and transportation needs, helping to lower carbon emissions.
- Well-spliced beams last longer, meaning fewer repairs or replacements, and less overall resource use.
- Splicing makes it easier to reuse beams during renovations or demolitions, supporting a circular economy in construction.
- Flexibility: Overcoming Design and Building Challenges
- Splicing lets us create longer spans that would be impossible with single beams—ideal for large buildings like sports stadiums or airports.
- It allows for more creative designs, like curved or tapered beams, making it easier to build unique structures.
- Transporting and splicing beams on-site gives construction teams more flexibility, improving overall efficiency.
Where Should a Steel Beam Be Spliced? And Where Should It Be Avoided?
Choosing the right splice location is crucial in steel construction. It affects not only the structural integrity but also the feasibility and cost of installation. So, where should a beam splice be placed, and which areas must be avoided?
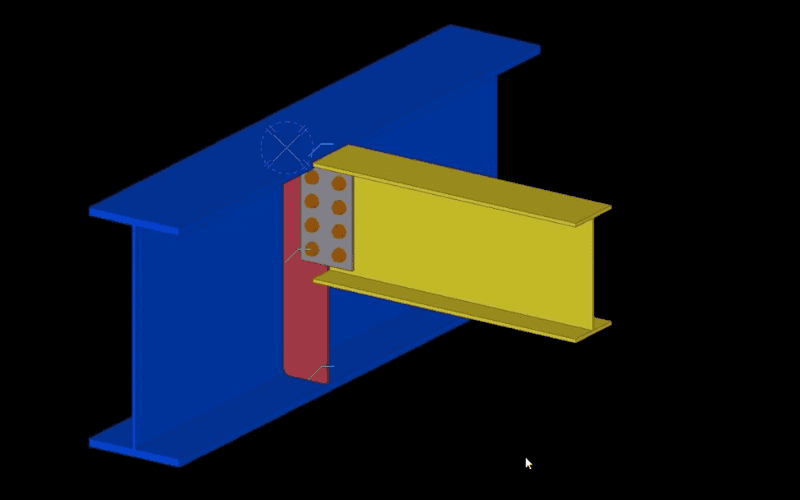
👍Recommended Splice Locations
A beam splice should be positioned in areas with lower stress to ensure the beam remains strong and stable after connection. The best locations for splicing include:
- Within the first third of the span near the support – In simply supported beams, bending moments are lower near the supports. A common practice is to place splices between 1/4 to 1/3 of the span from the support.
- Areas with low shear force – Shear forces are generally highest at the beam’s ends and lower in the midspan. Avoiding high-shear zones reduces the risk of connection failure.
- Compliant with design codes – Always follow industry standards like AISC or GB 50017 to ensure the splice location meets safety and performance requirements.
Special Case: Load-Bearing Beams
If the beam being spliced is a primary load-bearing beam, extra precautions must be taken. Load-bearing beams handle significant forces, so their splices need additional reinforcement. In these cases:
- Use thicker splice plates or additional stiffeners to strengthen the joint.
- High-strength bolts or full-penetration welds are preferred to ensure proper load transfer.
- Non-destructive testing (e.g., ultrasonic testing) is often required to verify the splice’s integrity.
👎Locations to Avoid for Beam Splicing
Certain areas should never be used for beam splicing, as they can compromise structural strength and long-term performance. These include:
- High-stress zones – Avoid locations near connections, cantilever ends, or any area with complex stress distribution. Splicing in these areas can lead to excessive stress concentration and failure.
- Regions subject to frequent dynamic loads – In structures like bridges in seismic zones or industrial buildings with vibration loads, splicing can lead to fatigue failure over time.
- Special design-sensitive areas – Locations, where protective coatings (fireproofing, corrosion resistance) are critical, should be free from splices, as they can disrupt the coating’s continuity and durability.
When Is Beam Splicing Needed?
Beam splicing is widely used in modern steel construction, often driven by structural requirements or cost considerations. Here are some common scenarios where beam splicing is essential.
Structural Considerations
- Long-Span Structures – In large public buildings such as airports, stadiums, and exhibition centers, beam lengths often exceed manufacturing or transportation limits. Splicing allows multiple beam sections to be connected, meeting the demands of long-span designs.
- Transportation Constraints – Road transport regulations often restrict the maximum length of steel beams. To overcome this, beams are manufactured in shorter sections, transported separately, and then spliced on-site. This method not only solves logistical issues but also reduces transportation costs.
- Renovation and Reinforcement – In structural upgrades or repairs, beam splicing is used to replace damaged sections or extend existing structures.
Cost-Driven Considerations
- Standardized Production – Manufacturing shorter beam sections in a standardized process and splicing them as needed can reduce fabrication costs and minimize material waste.
- Efficient Material Use – Leftover beam segments from other projects can be repurposed through splicing, optimizing material usage, and lowering costs.
Special Design Considerations
- Complex Architectural Forms – In structures with curved beams, tapered beams, or irregular designs, splicing is often necessary to achieve the desired shape.
- Extreme Environments – For projects in deep-sea platforms, high-altitude bridges, or other challenging conditions, beam splicing helps accommodate construction constraints and environmental challenges.
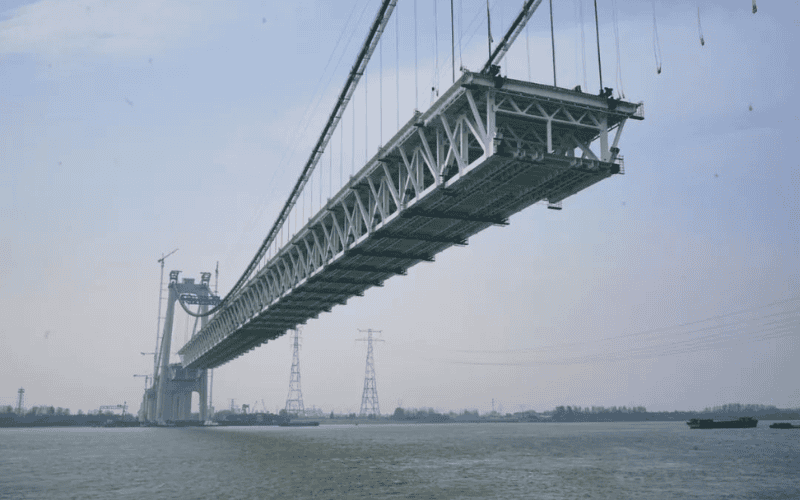
Four Main Types of Beam Splicing Methods
The choice of beam splicing method directly impacts structural performance, construction efficiency, and cost. Depending on project requirements and site conditions, the four most common beam splicing methods are:
Splicing Method | Best Suited For | Advantages | Disadvantages |
Bolted Splice | – Fast installation, removable structures (e.g., temporary frames, equipment supports) – Sites with difficult welding conditions | – Quick and easy installation – Removable for maintenance or modifications – Works well in remote or high-altitude sites | – Weaker fatigue resistance, unsuitable for areas with frequent dynamic loads – Requires precise hole alignment, increasing fabrication cost |
Welded Splice | – High-strength, permanent connections (e.g., high-rise buildings, bridge girders) – Projects requiring high structural integrity | – Strong and seamless connection – No additional fasteners, providing a clean appearance – Works well for complex beam profiles | – Slower construction, requires skilled welders and equipment- Welding residual stress may affect structural performance, requiring post-treatment – Sensitive to environmental conditions (wind, rain, etc.) |
Hybrid Splice (Bolting + Welding) | – Heavy-load, complex structures (e.g., industrial plants, heavy-duty platforms) – Projects needing both strength and installation flexibility | – Combines high strength with flexible installation – Suitable for situations where both dynamic and static loads coexist | – More complex process and higher cost – Requires careful coordination of bolt pre-tensioning and welding sequence |
Innovative Methods (e.g., Mechanical Locking) | – Specialized environments (e.g., offshore platforms, high-altitude bridges) – Projects demanding ultra-fast and precise installation | – Fast installation with high precision – No need for bolts or welding, reducing site constraints – Modular design allows for easy transport and assembly | – Expensive and less widely adopted – Requires extremely high design and manufacturing accuracy |
How to Properly Splice Steel Beams: 6-Step Standardized Process
Steel beam splicing is a high-skill task with complex procedures. To ensure that the spliced steel beams meet design requirements and safety standards, a standardized construction process must be followed. Below are the 6 key steps in the steel beam splicing process:
Step 1: Design Phase
- Load Calculation
- Calculate the forces acting on the steel beam (including bending moment, shear force, axial force, etc.).
- Determine the load transfer requirements in the splice area.
- Connection Method Selection
- Choose the appropriate splicing method (bolted, welded, or hybrid connection) based on load types, construction conditions, and cost considerations.
- Related Reading: Steel Connections in Steel Structure Buildings: Types, Uses, Design
- Drawing Confirmation
- Create detailed splice design drawings, including splice plate dimensions, bolt arrangement, weld requirements, etc.
- Communicate with the construction team to ensure the drawings are practical and feasible.
Step 2: Material Preparation
- Beam End Treatment
- Prepare the beam ends by beveling or milling them to ensure the splicing surfaces are smooth and fit together precisely.
- Splice Plate Fabrication
- Manufacture the splice plates according to the design specifications, ensuring they meet the required dimensions, thickness, and material properties.
- Bolt Hole Fabrication
- Use high-precision equipment to process bolt holes, ensuring consistency in hole placement and diameter.
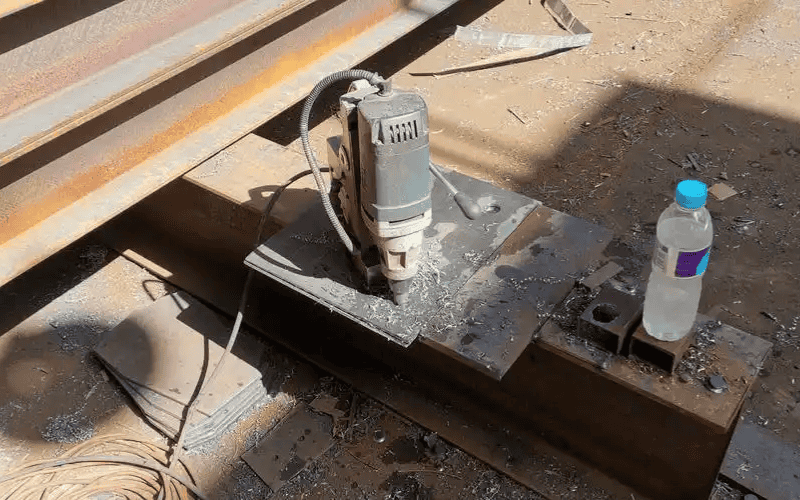
Step 3: On-Site Alignment
- Temporary Support Setup
- Set up temporary supports in the splice area to ensure the beam remains stable during the splicing process.
- Laser Alignment
- Use laser calibration equipment to precisely align the steel beams, ensuring accurate alignment at the splice ends.
- Pre-Splice Inspection
- Before proceeding, inspect the match between splice plates, bolt holes, and weld bevels to ensure there are no errors.
Step 4: Connection Construction
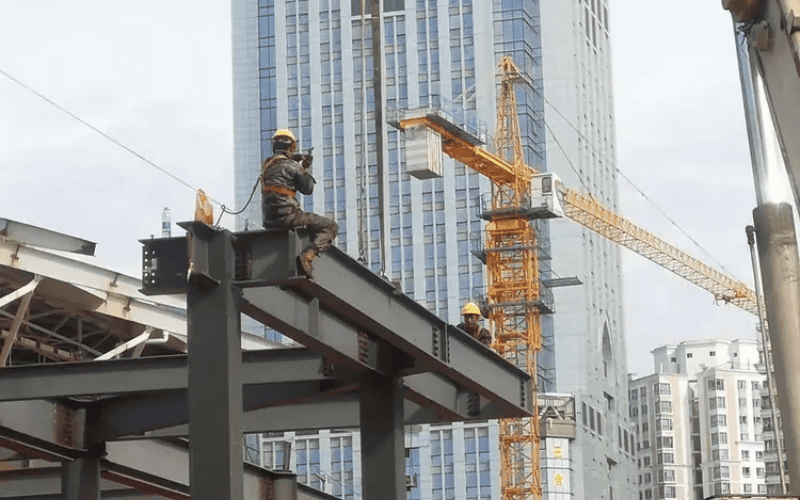
- Bolted Splice
- Tighten bolts in the correct sequence and to the specified torque values to ensure the connection’s strength.
- Welded Splice
- Follow an optimal welding sequence (e.g., welding from the center to the edges) to minimize residual welding stress.
- Control welding parameters (current, voltage, speed) to ensure high-quality welds.
- Hybrid Connection
- Pre-tighten bolts first, followed by welding to ensure the combined effect of both connection methods.
Step 5: Quality Inspection
- Ultrasonic Testing
- Perform non-destructive testing (e.g., ultrasonic testing) on the welds to check for cracks, porosity, or other defects.
- Torque Verification
- Verify the pre-tension of bolts to ensure they meet design specifications.
- Deformation Monitoring
- Inspect the splice area for any deformation to ensure the overall straightness of the steel beam.
Step 6: Corrosion Protection
- Weld Seam Grinding
- Grind the weld seams to ensure a smooth surface for coating application.
- Coating Restoration
- Apply corrosion protection coatings to the splice area, ensuring its durability matches that of the original steel beam.
- Fireproofing
- Apply fireproof coatings or wraps to the splice area based on design requirements.
We Are Here With You
We understand that steel structure projects can come with many questions. If you’re unsure about beam splicing or any other aspect of your project, feel free to reach out to us for a free consultation. Our team is here to offer expert advice and guidance. When you’re ready, we’d be happy to discuss how we can support the successful execution of your project—from design to installation. Contact us today to get started.