As the UK faces a growing housing crisis, Housing Minister Angela Rayner has set an ambitious target of building 1.5 million homes by the end of this Parliament, but the question remains: how can this be achieved amid a severe shortage of skilled construction workers? Experts believe the solution may lie in an approach that proved successful nearly 80 years ago: prefabricated homes.
The Prefab Success Story
In the aftermath of the Second World War, Britain faced a housing crisis caused by widespread bomb damage and a rapidly growing population. The government responded by introducing prefabricated homes, officially known as Emergency Factory Made Houses (EFMs). These one-storey bungalows, equipped with modern amenities like indoor toilets, fitted kitchens, and gardens, were designed to be quick, affordable, and efficient to produce. Between 1945 and 1949, over 156,000 prefab homes were erected, providing temporary yet comfortable housing for thousands of families.
Originally intended to last just a decade, many of these homes have stood the test of time, with around 8,000 still in use today. Their success demonstrated how innovative construction methods could address urgent housing needs.
Britain’s Modern Housing Crisis: A Growing Challenge
Fast forward to 2024, and Britain is once again grappling with a housing shortage. A combination of factors, including a rising population, a lack of skilled construction workers, and the diversion of labour to major infrastructure projects like HS2 and Hinkley Point, has made traditional housebuilding methods insufficient to meet demand.
Angela Rayner’s target of 1.5 million new homes seems increasingly unattainable. The construction industry requires 17,000 new recruits annually—three times the current rate—to keep up with demand. The labour shortage has been further exacerbated by Brexit, the COVID-19 pandemic, and an aging workforce. Additionally, the government’s net zero targets will require retrofitting millions of homes, creating even more demand for skilled workers.
Why Modular Homes Are the Answer
In this context, prefabricated homes—now known as modular homes—offer a compelling solution. These homes are constructed in factories using assembly-line techniques, significantly reducing the need for on-site labour and cutting construction time to just a few weeks. Modular homes also require fewer workers, as automation and streamlined processes can produce homes at a lower cost than traditional methods.
Advantages of Modular Construction
Speed: Modular homes can be built in a fraction of the time compared to traditional construction. While a conventional home might take 6-12 months to complete, modular homes can be ready in as little as 8-12 weeks.
- Cost-Effectiveness: Factory production reduces waste and allows for bulk purchasing of materials, lowering overall costs.Factory production minimizes waste and enables the purchase of materials in bulk, leading to reduced overall costs.
- Sustainability: Modular construction generates less waste and can incorporate energy-efficient designs, aligning with the government’s net zero goals.
- Quality Control: Constructing in a controlled factory environment guarantees enhanced precision and uniformity in building quality.
Despite these benefits, the modular housing industry has faced challenges in gaining popularity in the UK. Previous government attempts to promote modular construction ended in failure, with companies like Legal & General abandoning their ventures due to a perceived lack of demand. This is puzzling, given the urgent need for 1.5 million new homes and the growing population driven by immigration.
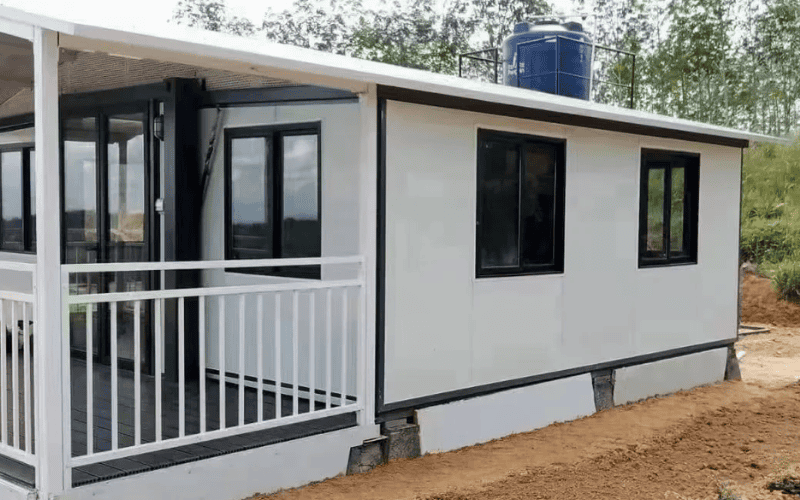
Public Perception: The Barrier to Adoption of Modular Home
One of the key challenges facing modular homes is public perception. Just as post-war prefabs were initially dismissed as “not real houses,” modern modular homes face similar skepticism. Many people associate prefabrication with low-quality, temporary structures, despite significant advancements in design and technology.
However, modern modular homes are far from the basic prefabs of the 1940s. Today’s modular homes can be customized to include high-end finishes, spacious layouts, and cutting-edge smart home technology. They are durable, energy-efficient, and designed to meet modern living standards.
The Development of Prefabricated Houses Around the World
While the UK has been relatively slow in adopting modular construction, other countries have achieved notable success in embracing it.
Sweden: Approximately 84% of detached homes in Sweden are prefabricated. The country has perfected the art of modular construction, with factories producing high-quality, sustainable homes that are assembled on-site in days.
Japan: In Japan, a substantial proportion of new housing consists of modular homes. Companies like Sekisui House and Daiwa House have pioneered innovative designs, including earthquake-resistant structures and energy-efficient homes.
United States: Modular construction is gaining popularity in the US, particularly in urban areas where housing demand is high. Companies like Factory OS and Veev are leading the charge, delivering affordable, high-quality homes at scale.
These examples illustrate that modular construction is not only feasible but also capable of being expanded on a larger scale. By learning from these success stories, the UK could overcome its housing crisis and set a new standard for sustainable, efficient homebuilding.
The Role of Government and Industry in Promoting Prefabricated Housing
To unlock the potential of modular homes, both the government and the construction industry must take decisive action:
Government Support: The government should provide funding and incentives to encourage the growth of modular housing. This could include grants for modular homebuyers, tax breaks for manufacturers, and streamlined planning permissions for modular developments.
Industry Collaboration: Construction companies, architects, and engineers must work together to standardise modular designs and improve public perception. Showcasing successful modular projects could help change attitudes and demonstrate the benefits of this approach.
Workforce Training: Investing in training programmes for modular construction workers will be essential to scale up production. This could include partnerships with vocational schools and apprenticeship schemes.
Time to Embrace Prefabrication
Prefabricated homes once provided a lifeline for a nation in crisis. Today, modular homes could offer a similar solution, delivering affordable, high-quality housing at the speed and scale required to address Britain’s housing shortage. For Angela Rayner and the government, the message is clear: it’s time to take a leaf out of Labour’s 1945 playbook and embrace the potential of prefabrication.
The housing crisis demands bold action, and modular homes could be the key to unlocking a brighter future for millions of Britons. The question is: will the government seize this opportunity, or will it continue to procrastinate as the crisis deepens?
For more insights on housing solutions and government policies, stay tuned to our blog.