As the global construction industry’s demand for efficient, environmentally friendly and sustainable building solutions continues to grow, the prefabricated steel structure market is facing unprecedented development opportunities.
According to the latest report from Future Market Insights[1], the global prefabricated building system market is expected to grow from US$12.22 billion in 2025 to US$22.64 billion in 2035, with a compound annual growth rate (CAGR) of 6.3%.
Among them, the North American market has become the world’s second largest prefabricated building system market due to its rapid industrialization and urbanization.
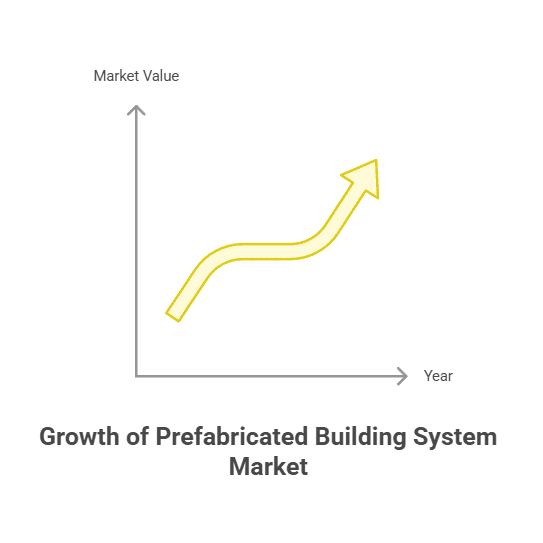
Development of prefabricated buildings in different regions
North America
- North America, particularly the United States and Canada, is at the forefront of adopting prefabricated building systems globally.
- With the acceleration of urbanization and population growth, the construction market has an urgent need for faster and more cost-effective construction methods. Furthermore, governments have enacted numerous incentive policies aimed at fostering sustainable development, thereby accelerating the growth of prefabricated buildings.
- The green building market in the United States is particularly fast, and the popularity of green certification standards such as LEED has made prefabricated buildings the preferred environmentally friendly option.
Asia Pacific
- China, India, and Southeast Asian nations are undergoing rapid urbanization, resulting in a swiftly increasing demand for prefabricated buildings.
- The Chinese government’s support policies for prefabricated buildings are constantly strengthening, especially in the fields of old city renovation, new urban infrastructure construction and public housing.
- The Indian and Southeast Asian markets benefit from the growing construction demand and labor cost issues, and prefabricated buildings provide them with a low-cost and high-efficiency alternative.
Europe
- The application of prefabricated buildings in the Western European market is growing rapidly, especially in countries such as the United Kingdom, Germany, France and Switzerland.
- Most European countries are promoting sustainable and green building practices, and prefabricated buildings are widely favored for their low energy consumption, low waste and environmental protection characteristics.
- Especially in the Nordic region, the application of prefabricated wood structures and modular residential systems has become the mainstream of residential construction.
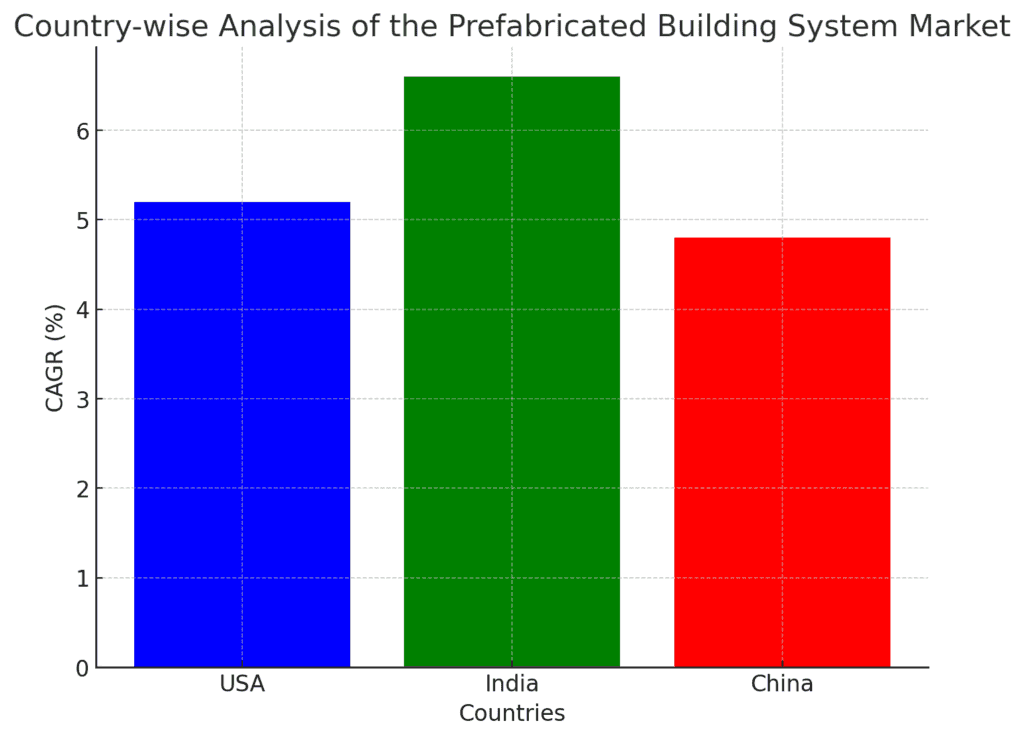
The driving force behind the growth of prefabricated buildings: why this trend is irreversible
The growth of prefabricated building systems can be attributed to several intertwined factors:
1. Cost-effectiveness
Traditional construction methods require a lot of labor and time, while prefabricated buildings can greatly shorten the construction cycle and reduce the time of on-site construction through factory prefabrication.
Manufacturing building components in a factory setting enhances quality control measures and diminishes material waste. Due to the reduction of labor costs and construction time, the overall project cost is significantly reduced.
2. Urbanization and population growth
The acceleration of global urbanization and the increasing demand for housing and infrastructure in densely populated areas are an important reason for the growth of prefabricated buildings.
In large and emerging cities, prefabricated buildings can quickly provide a large number of standard residential and commercial spaces to meet the needs of urban expansion and infrastructure construction.
3. Environmental protection and sustainability
Increasingly stringent environmental regulations and increasing requirements for sustainable buildings make prefabricated buildings the best choice to meet these challenges.
In comparison to traditional buildings, prefabricated buildings can drastically minimize construction waste and energy consumption by utilizing recyclable materials for component production. Factory-manufactured building components further decrease carbon emissions from on-site construction activities, aligning with the worldwide trend towards green building practices.
4. Technological progress and manufacturing optimization
With the continuous advancement of manufacturing technology, especially in automation, robotics, 3D printing and building information modeling (BIM), the precision and flexibility of prefabricated buildings have been significantly improved.
Digital design makes the production of building components more precise, thereby improving the quality and safety of buildings. In addition, the design of modular buildings allows flexible adjustments according to demand, greatly improving the adaptability of the system.
5. Government policy support
Governments around the world have introduced policies to encourage green buildings and sustainable development, especially providing incentives such as tax exemptions and subsidies for low-carbon and energy-saving buildings, promoting their application in residential and public buildings.
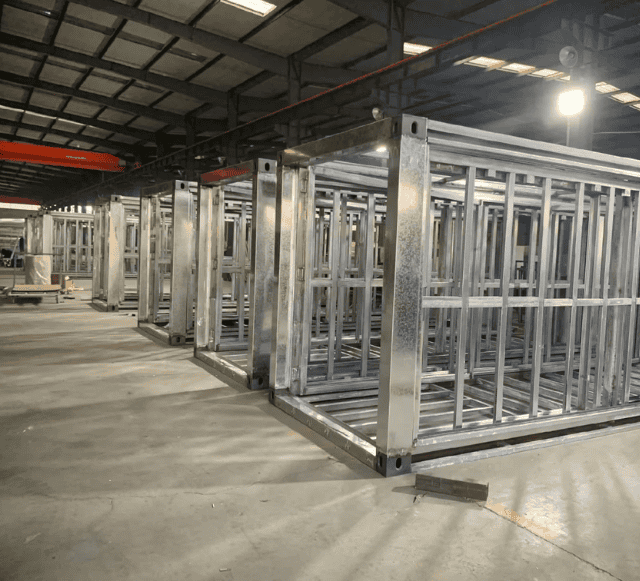
Key bottlenecks and obstacles facing prefabricated buildings
Despite the rapid growth of the prefabricated building market, it still faces some key challenges in its development.
1. Transportation and logistics costs
Building components often need to be transported from the factory to the construction site, and the transportation process may be affected by factors such as road conditions and traffic, thereby increasing logistics costs. Some large or specially designed building components are easily damaged during transportation, which also increases risks and costs.
2. Technical Difficulties and Quality Control
Although technological advances have improved the quality of prefabricated buildings, some technical difficulties still exist. For example, the joint processing between modules, the connection problems between different materials, and the challenges of adaptability to the building environment.
3. Market Awareness and Acceptance
As a new type of construction method, many consumers and builders have little knowledge of prefabricated buildings. Especially in some traditional construction markets, prefabricated building systems may face the problem of low acceptance. To solve this challenge, it is necessary to enhance consumer trust through more case demonstrations and market education.
How technological innovation drives breakthroughs in the prefabricated building industry
In order to solve the challenges faced and promote the further development of prefabricated building systems, technological innovation plays a key role.
1. Intelligent Manufacturing and Digital Design
Digital design, building information modeling (BIM) and 3D printing technology are driving revolutionary changes in the design and production methods of prefabricated buildings. BIM technology can accurately plan every detail of the building through three-dimensional modeling and information integration, thereby reducing errors in production and improving the accuracy and quality of the building.
2. New building materials
The research and development of new building materials is crucial to improving the performance of prefabricated buildings.
Materials such as ultra-high performance concrete (UHPC) and cross-laminated timber (CLT) not only enhance the structural strength, but also improve the environmental performance of the building.
The application of new materials such as composite materials and lightweight high-strength concrete makes prefabricated buildings more durable, energy-efficient and beautiful.
3. Integration of environmental protection technology
Future prefabricated buildings will pay more attention to the integration of environmental protection and energy efficiency.
Integrating green technologies such as solar photovoltaic systems, intelligent temperature control systems, and rainwater collection systems will enable prefabricated buildings to provide living space while minimizing the negative impact on the environment.
4. Modular design and intelligent systems
Modular design not only improves the construction efficiency of prefabricated buildings, but also makes buildings more flexible and can be quickly adjusted according to different needs.
The integration of intelligent building systems, such as smart homes and automated control systems, will further enhance the modernization level of prefabricated buildings.
Prefabricated buildings are moving towards an efficient, intelligent and green future
The prefabricated construction system will exhibit wider development prospects in the future.
Global Growth: Prefabricated buildings will continue to grow across regions like Asia, Europe, and North America, addressing housing shortages, infrastructure needs, and public projects in emerging markets.
Smarter & Greener: Future prefabricated buildings will integrate intelligent technologies and green materials, enhancing energy efficiency, comfort, and sustainability.
Ongoing Innovation: Technological advancements will drive improvements in modular accuracy, assembly ease, and building durability, making prefabricated structures safer and more adaptable to complex needs.
[1] Nikhil Kaitwade. (2024). Prefabricated Building System Market Outlook 2025 to 2035 [Report].
https://www.futuremarketinsights.com/reports/prefabricated-building-system-market