The Commonwealth Bank of Australia (CBA) recently announced an important strategy to solve Australia’s growing housing crisis by strongly supporting prefabricated construction technology.
As the first bank to join the Australian Prefabricated Building Association (prefabAUS), CBA not only provides the necessary financial support for this innovative industry, but also plans to launch a series of policies to simplify the purchase process of prefabricated houses, thereby accelerating the supply of high-quality, sustainable housing.
This move not only brings new hope to Australia’s housing market, but also provides innovative solutions to solve the long-standing housing shortage problem.
Prefabricated construction: an innovative solution to the housing crisis
Prefabricated construction is a construction method that prefabricates house modules in a factory and then transports these modules to the site for assembly. Compared with traditional on-site construction methods, prefabricated construction has significant advantages: short construction period, high efficiency, less material waste, consistent construction quality, etc. For example, it usually takes 10 to 12 weeks to complete a prefabricated house, while traditional on-site construction methods may take 18 months or even longer.
However, although prefabricated construction is technically quite mature, its promotion in Australia faces many obstacles. One of the biggest challenges is financing. Due to the lack of standardized contracts and financing processes, it is difficult for homebuyers and manufacturers to obtain support from banks.
To address this problem, CBA chose to join prefabAUS and began to promote the development of standard contracts for the field of modern methods of construction (MMC). This move will help break down financing barriers and inject new vitality into the prefabricated construction industry.
CBA’s new policy: lowering the threshold for home purchases
In order to advance the progress of prefabricated buildings, CBA intends to introduce a groundbreaking policy within this quarter. According to this new policy, homebuyers will be eligible to receive upfront payments amounting to as much as 60% of the total contract price, prior to the installation of the house on the designated land.
For customers who choose prefabricated manufacturers approved by CBA, this proportion can even be increased to 80%. This move will greatly reduce the financial pressure on homebuyers and help more people afford prefabricated houses.
By simplifying the financing process, CBA’s new policy not only reflects its support for innovative construction technology, but also reflects the bank’s deep understanding of Australia’s housing crisis. By lowering the threshold for home purchases, CBA hopes to encourage more homebuyers to choose prefabricated houses, thereby accelerating housing supply and easing market tensions.
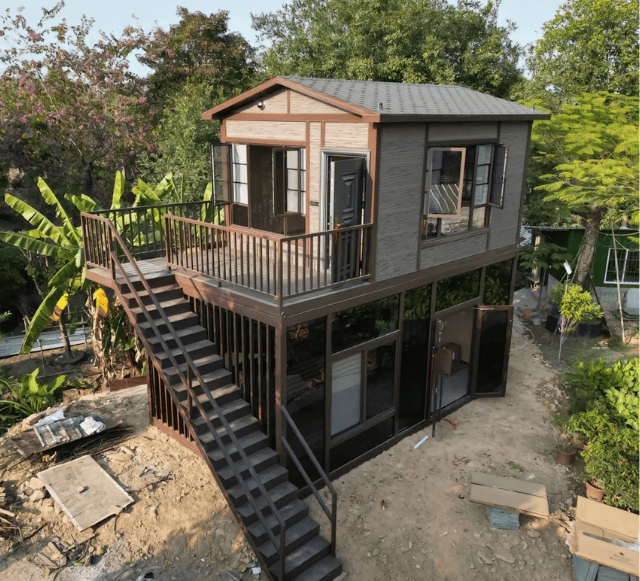
Advantages and potential of prefabricated buildings
The advantages of prefabricated buildings go far beyond speeding up construction. It has many advantages, such as high efficiency, sustainability and environmental friendliness.
First of all, factory production can reduce material waste generated during the construction process, and through more precise quality control, it ensures higher consistency and construction quality.
In addition, due to the high standardization of the production process, the construction speed of prefabricated buildings is greatly improved, and the complexity of on-site construction is reduced, thereby reducing the overall cost.
From an environmental perspective, prefabricated buildings are more in line with the requirements of sustainable development than traditional construction methods. Factory construction reduces construction waste, and prefabricated modules can be produced in a more environmentally friendly environment, greatly reducing carbon emissions during construction. This series of advantages makes prefabricated buildings not only cost-effective than traditional buildings, but also less environmentally friendly.
Although Australia’s prefabricated construction industry started late, with the gradual improvement of industry standards, the growth of market demand and the support of financial institutions, prefabricated buildings have great potential for future development.
Take Sweden as an example, 80% of homes are built by prefabricated construction, while Australia currently has a relatively low proportion. With the support of financial institutions such as CBA and the promotion of policies, Australia’s prefabricated construction market is expected to usher in rapid growth.
Industry collaboration: driving innovation and scale
The collaboration between CBA and prefabAUS is not only a combination of finance and the construction industry, but also an important step in promoting innovation and scale in the construction industry.
By supporting the promotion of prefabricated construction technology, CBA is helping the Australian construction industry move towards modernization. At the same time, prefabricated construction companies, such as Modscape, are also actively expanding their production capacity and using advanced construction technology to accelerate the delivery of residential projects.
Modscape’s new production line at Essendon Fields in Melbourne can complete 8 house modules per day, which provides strong support for the construction of large-scale residential projects. This efficient production model can not only meet Australia’s growing housing demand, but also provide more choices for homebuyers, especially in areas where there is a social and economic need for a large number of affordable homes.
The future of prefabricated construction: going mainstream
This move by CBA has undoubtedly injected new vitality into Australia’s housing market. As prefabricated construction technology continues to mature and financing thresholds are gradually lowered, more and more Australian homebuyers may choose this efficient and environmentally friendly way of building houses. With the increase in policy support, prefabricated construction is expected to become the mainstream construction method in the future.
The rise of prefabricated buildings means new opportunities for the steel structure industry. As a vital component of prefabricated buildings, steel structures will play an increasingly important role in future residential construction.
The high strength, flexibility and sustainability of steel structures make them an indispensable part of prefabricated buildings. By actively embracing this trend, steel structure companies can not only better meet the market demand for housing, but also occupy a place in this wave of architectural innovation.