In the modern housing market, manufactured homes are gaining more and more attention. Compared with traditional brick and mortar houses, they are favored for their affordable prices, fast construction speed and flexible design options.
So, what are manufactured homes? How are they different from the traditional homes or modular homes we are familiar with? In this article, we will take you through the definition of manufactured homes, their advantages, and whether they are worth investing in.
What is a manufactured home?
A manufactured home is a residential unit constructed in a factory, adhering to the federal standards (HUD Code) established by the U.S. Department of Housing and Urban Development (HUD). It is sometimes called a “mobile home”. Unlike traditional homes built on site, its main structure is completed in the factory, transported to the final location on a steel chassis, and permanently installed on the foundation.
According to the law, only houses produced after June 15, 1976 and with a red HUD certification label can be called “manufactured homes”. Previous similar products were called “mobile homes” with lower quality standards and safety.
Manufactured Homes vs. Mobile Homes vs. Modular Homes: Key Comparisons
Manufactured Homes vs. Mobile Homes
Aspect | Manufactured Home | Mobile Home |
Legal Standards | Complies with modern federal building codes (e.g., HUD Code) | Follows outdated pre-1976 industrial standards |
Structural Safety | Steel chassis + wind-resistant anchoring | No mandatory wind resistance; wooden chassis possible |
Mobility | Permanently fixed to a foundation after delivery | Retains wheels for easier relocation |
Property Type | Can be classified as real estate (if permanently anchored) | Typically classified as personal property (like vehicles) |
Design Updates | Continuously improved (e.g., 2020 solar panel pre-installation rules) | Design standards frozen post-1976 |
Key Takeaway:
Mobile homes are predecessors to manufactured homes but differ significantly in safety and legal status. For example, manufactured homes reduce fire evacuation time by 37% compared to mobile homes (based on UL smoke spread tests).
Manufactured Homes vs. Modular Homes
Aspect | Manufactured Home | Modular Home |
Regulatory System | Complies with federal prefab housing codes | Meets international building codes (e.g., ISO 22487) |
Construction | Fully factory-built; only utilities connected on-site | Built in modules, assembled and welded on-site |
Design Approval | Limited to standardized layouts | Customizable (requires structural engineer certification) |
Foundation | Allows temporary anchoring | Requires permanent concrete or pile foundations |
Cross-Border Use | Restricted by origin country standards (e.g., width ≤4.3 meters) | Modules can be shipped globally via containers |
Case Example:
Modular homes enable multi-story designs through “unit stacking” (e.g., a 12-story modular apartment project in Europe), while manufactured homes are typically limited to two stories due to transport size constraints.
Related Reading: Modular vs manufactured vs mobile
Manufactured Home Prices
The prices of manufactured homes can vary widely based on factors such as size, design, materials utilized, and the level of customization available. Generally, a manufactured home costs between $40,000 and $150,000, though luxury or custom-designed manufactured homes can cost more. Compared to traditional brick homes, manufactured homes are typically more economical and faster to construct.
Factors that influence price
Home size: The width, length, and number of rooms in a home all directly affect the price. Generally, double-wide homes are priced higher than single-wide homes.
Design and materials: The complexity of a home’s design and the materials used can have a significant impact on price. High-end materials (like hardwood floors, natural stone) and highly customized designs can drive up prices.
Customization options: Additional features in the kitchen, bathrooms, and exterior styling can also add extra costs. Customization options can make prices fluctuate widely, depending on individual needs.
Shipping and installation: The costs associated with shipping and installation can also fluctuate depending on the specific geographic location. If the home is shipped farther or installation requires more on-site work, the cost will increase.
Despite the reasonable price, the total cost of a manufactured home still takes into account the purchase of the land and other long-term maintenance costs.
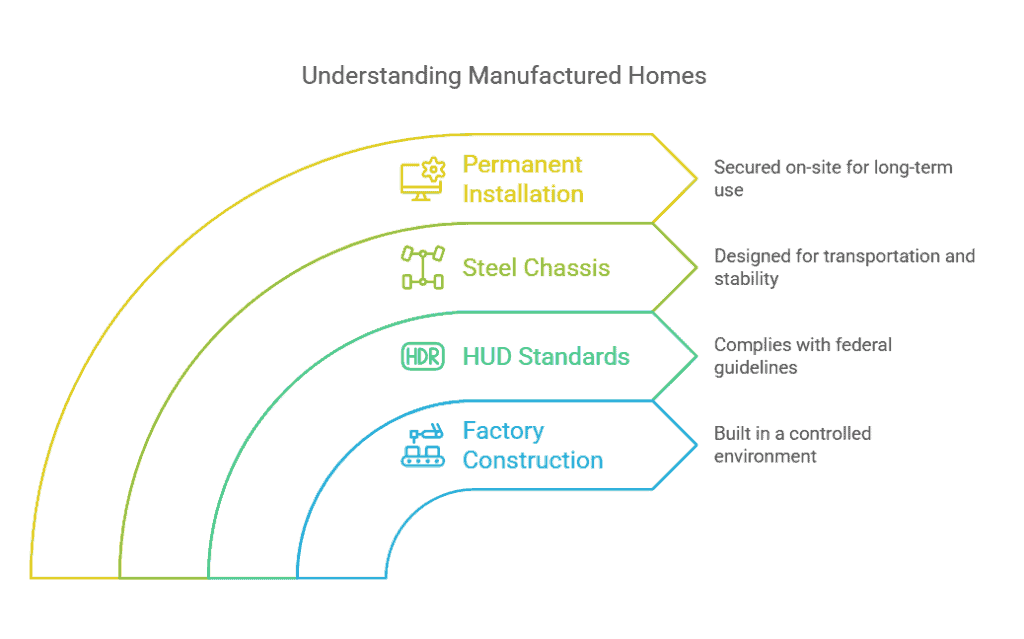
Manufactured Home Financing: Is a Manufactured Home a Good Investment?
Yes, manufactured homes can be a good investment option, especially for families looking for an affordable and quick move-in.
1. How to get a loan for a manufactured home?
Financing for manufactured homes is usually more complicated than for conventional homes. First, most manufactured home loans are obtained through personal loans or Federal Housing Administration (FHA) loans. The FHA offers loan programs for manufactured homes that allow borrowers with lower down payments and lower credit scores to apply for loans. However, the loan application and approval process may take longer, and the loan interest rates are usually higher.
In addition, if you choose to build a manufactured home as a permanent fixed structure (such as placing it on land and connecting it to public facilities), you may be eligible for a conventional home loan (i.e., a home mortgage loan), which usually has more favorable loan terms.
2. Differences from conventional home loans
Manufactured home loans usually have some additional requirements and restrictions compared to conventional home loans. Manufactured home loans are subject to HUD Code standards, and borrowers are also required to provide proof of the home’s portability (if applicable), that is, whether the home can be transferred. Lenders may also take into account the age and structural integrity of the home to ascertain that it fulfills habitability requirements.
3. Difficulties and considerations for manufacturing home financing
Credit requirements: Applicants for manufactured home loans may face stricter credit requirements than traditional home loans. Certain lenders may impose stricter credit score requirements, particularly when the loan amount is substantial.
Higher loan interest rates: Since manufactured homes are generally of lower value, lenders may consider them to be higher risk and therefore charge higher interest rates.
Home depreciation: Manufactured homes generally depreciate faster in value in the market than traditional homes, which may result in a heavier asset burden for loan applicants.
Land requirements: If you plan to purchase a manufactured home and permanently place it on a piece of land, you need to ensure that the land has appropriate infrastructure (such as water and electricity facilities) and that there is no dispute over the ownership and use of the land, otherwise financing will be affected.
Advantages and Disadvantages of Manufactured Homes
Advantages:
- Cost-effectiveness: Manufactured homes are usually cheaper than traditional homes and are suitable for families with limited budgets.
- Fast Construction: Since most of the construction work is completed in the factory, the construction period of manufactured homes is shorter.
- Flexible Customization: Offer a diverse range of design and layout options to cater to varying needs and preferences.
- Lower Maintenance Costs: Use modern building materials and energy-saving technologies to reduce long-term maintenance costs.
- Mobility: If not fixed to the land, manufactured homes have a certain degree of mobility.
Disadvantages:
- Lower Real Estate Value: Manufactured homes usually depreciate quickly and have a lower long-term value.
- Difficulty in Financing: Financing conditions are strict and loan interest rates are high.
- Low Market Acceptance: In some areas, manufactured homes may not be widely accepted.
- Durability Issues: May face high repair and maintenance costs after long-term use.
- Land Requirements: If you want to permanently settle, you need to ensure that the land meets the requirements, adding additional costs.
When Does It Make Sense?
Scenario | Recommendation | Rationale |
Short-term housing (<5 years) | ★★★☆☆ | Low upfront cost but high resale depreciation |
Retirement living (owned land) | ★★★★☆ | Aging-friendly design + low maintenance |
Rental investment (high-demand area) | ★★★★☆ | 7%-10% annual ROI, outperforming traditional |
Permanent family home (no expansion plans) | ★★☆☆☆ | Design limits may hinder future needs |
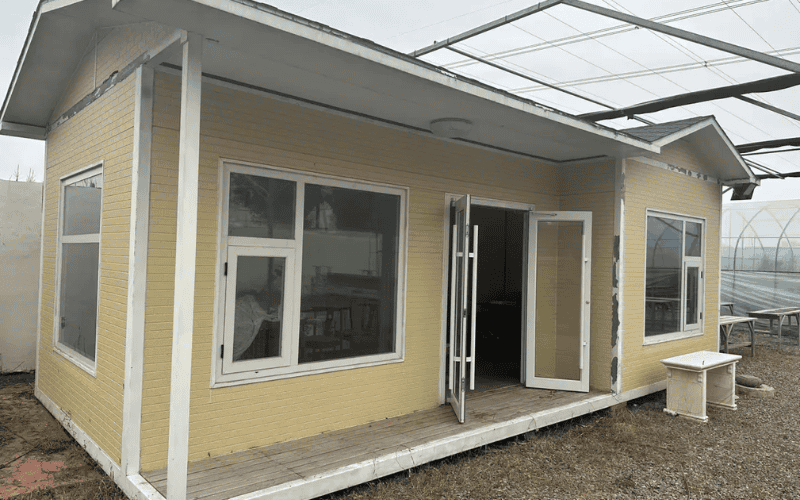
The construction process of manufactured homes
- Design and customization
- The construction process of manufactured homes begins with design. Custom options such as the layout, style, and materials of the home are selected based on customer needs. The design stage usually provides a standard design from the manufacturer, but it can also be customized to meet individual needs.
- Factory prefabrication
- Once the design is determined, the various parts of the home are prefabricated in the factory. This includes walls, roofs, floors, and other structural elements. Factory production allows for higher quality control and faster construction.
- Transportation and transportation preparation
- Once the parts of the home (such as modules or entire homes) are completed, they are transported to the designated location. The integrity and safety of the home need to be ensured during transportation, especially for large double-wide homes.
- Site preparation
- Before the home arrives at the installation site, the land needs to be prepared, including clearing, leveling, and setting the foundation. It is usually necessary to ensure that the land meets local building requirements and connect the required infrastructure (such as water and electricity).
- Home installation
- Once transported to the site, the home will be installed using equipment such as cranes. For single-wide homes, it is usually placed directly on the foundation; for double-wide homes, the modules need to be spliced together. The entire installation process typically concludes within a matter of days.
- Connection and commissioning
- After the installation is completed, the plumbing, electricity and water supply systems of the house need to be connected and commissioned. Make sure all equipment is functioning properly, including air conditioning, heating systems, etc.
- Final inspection and acceptance
- After the installation and commissioning are completed, the manufacturer will conduct a final inspection of the house to ensure that it complies with HUD Code and other local building standards. After all inspections are completed, the house can be delivered to the owner.
History of Manufacctured Housing
1. Origin and Development of Manufactured Housing
Manufactured housing originated in the early 20th century and was originally designed to address housing shortages, mainly to meet housing needs after World War II. In the 1950s and 1960s, manufactured housing became widely used in suburban areas of the United States and became an affordable option. As technology advanced, manufactured housing gradually evolved into today’s modern version.
2. Key Legal and Technological Advances
In 1976, the United States implemented the Home Construction Act (HUD Code), which set strict building standards for manufactured housing and improved quality, durability, and safety. Technically, with the adoption of new materials and energy-saving technologies, modern manufactured housing has significantly improved in environmental protection and comfort.
3. Popularity of Manufactured Housing in the United States and Around the World
In the United States, manufactured housing is widely used, especially in the Southwest and South, where about 20% of households choose to live in manufactured housing. Globally, manufactured housing has gradually become popular in Canada, Australia, and some European countries, but in some countries, due to cultural and regulatory restrictions, the penetration rate is low. With the growing demand for affordable housing, the market for manufactured homes is anticipated to continue its expansion.
FAQs
1. How long does a manufactured home last?
The lifespan of a manufactured home is typically 30 to 50 years, depending on the quality of the home’s construction, maintenance, and the climate conditions of the area where it is located. Regular care and maintenance can prolong the lifespan of a manufactured home.
2. Are manufactured homes safe?
Yes, modern manufactured homes are very safe. Since the implementation of the Home Construction Act (HUD Code) in 1976, manufactured homes must follow strict building standards to ensure the structure, durability, and safety of the home. Manufactured homes are designed to meet national safety requirements in terms of fire and wind resistance, which can effectively protect occupants.
3. What should I pay attention to when buying a manufactured home?
When buying a manufactured home, you should pay attention to the following aspects:
- Choose the right manufacturer: Make sure the manufacturer has a good reputation and complies with compliant construction standards.
- Check the quality and structure: Carefully check the building materials and construction quality of the home to ensure that it meets HUD Code requirements.
- Understand land issues: Confirm land ownership, infrastructure access (such as water and electricity), and whether it complies with local building regulations.
- Financing options: It’s important to comprehend loan rates and financing terms to ensure that the loan aligns with your financial circumstances.
- Long-term maintenance: Assess the maintenance needs of the home and make a long-term maintenance plan.