Have you ever wondered why some buildings can be completed in just a few months or even weeks, while others take years? The answer may lie in “modular construction”. Modular construction is a fast, environmentally friendly and efficient construction method that has gained more and more attention in the past few years, especially in industries that need to expand space quickly, such as schools, hospitals and commercial places.
We know that high quality and high efficiency are not opposites, but can be perfectly combined. Through innovative modular construction solutions, we not only shorten the construction period, but also ensure the stability and durability of the structure. If you are considering modular construction, or are curious about how it is done step by step, let us take you through this magical process.
Step 1: Preparation before building a modular building
Site selection and site survey
Choosing the right site is key to the success of a modular building project. Understanding the soil quality, topography and surrounding infrastructure will help ensure that the building can be installed smoothly. We provide professional consultation and advice to help clients understand how to choose the ideal construction site.
Soil types suitable for construction
Ideally soils should have high bearing capacity, good stability, adequate drainage and compaction, and soil types should avoid excessive organic matter content or expansive soils.
Soil Type | Explanation |
Rocky Soil | Strong and stable, ideal for heavy loads and foundations. |
Gravel | Excellent drainage and high load-bearing capacity. |
Sandy Soil | Good drainage, easy to compact, but may need stabilization. |
Stable Clay | Non-expanding, stable, good for foundations if moisture is controlled. |
Loam | Balanced mix, stable, good drainage, ideal for most construction. |
Cohesive Soil | Holds together well, good for foundations when compacted properly. |
Design and engineering planning
The special feature of modular building design is the splicing of each module, so the connection between modules must be considered during the design phase. Our engineering team works closely with clients to ensure that the building scale, function, layout and access to systems (such as electricity, water supply and drainage) meet the requirements. By using advanced BIM technology, modules can be accurately manufactured and assembled quickly.
Obtaining necessary building permits
Ensuring that all building permits and approval documents are in place before the project officially starts is a crucial step. Our team will start processing relevant permit applications at the beginning of the project, helping clients prepare relevant documents, ensuring that the project complies with local regulations and building standards, and avoiding any unnecessary delays.
Infrastructure preparation
We provide detailed technical solutions and guidance to ensure that the project party can smoothly carry out land leveling, infrastructure preparation and other tasks, so as to be fully prepared for the subsequent module installation.
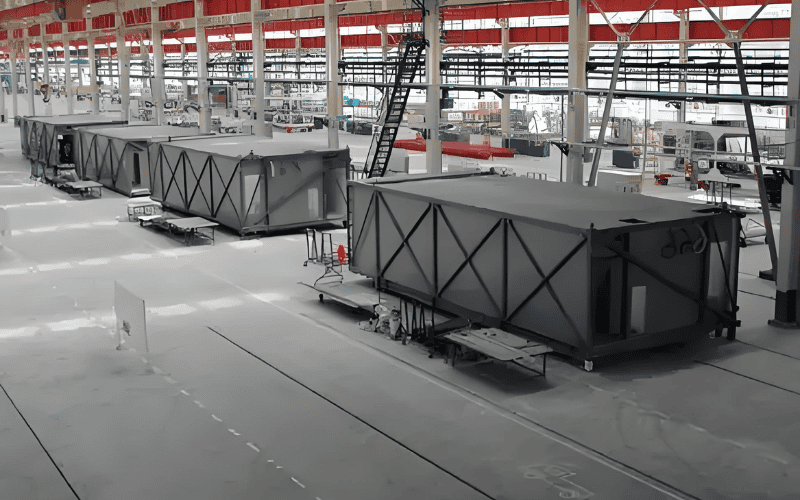
Step 2: Construction of modular buildings in the factory
During the production process of modular buildings, all components are completed in a strictly controlled factory environment.
First, the steel structure frame of the module is precisely welded and assembled according to the design drawings.
Next, components such as walls, roofs and floors are quickly completed in standardized production lines. The installation of the wall includes not only the fixing of external materials, but also the layout of the internal structure, ensuring that each module has a complete functional foundation when it leaves the factory.
As the modular structure is gradually completed, the layout of facilities such as electrical systems, water supply and drainage pipes, and air conditioning pipes is also carried out simultaneously. This series of work is completed in the factory, which not only saves time on-site construction, but also ensures the quality and accuracy of construction to the greatest extent.
Through a highly integrated production process, each component of the module has reached the best construction state in the factory. Our manufacturing process strictly follows international quality standards to ensure that each module has high strength, durability and excellent seismic resistance, and can be smoothly connected and used in subsequent on-site assembly.
Step 3: Transporting the modular building
We use a set of efficient and safe transportation methods to ensure that modular buildings are transported smoothly and safely from the manufacturing base to the construction site.
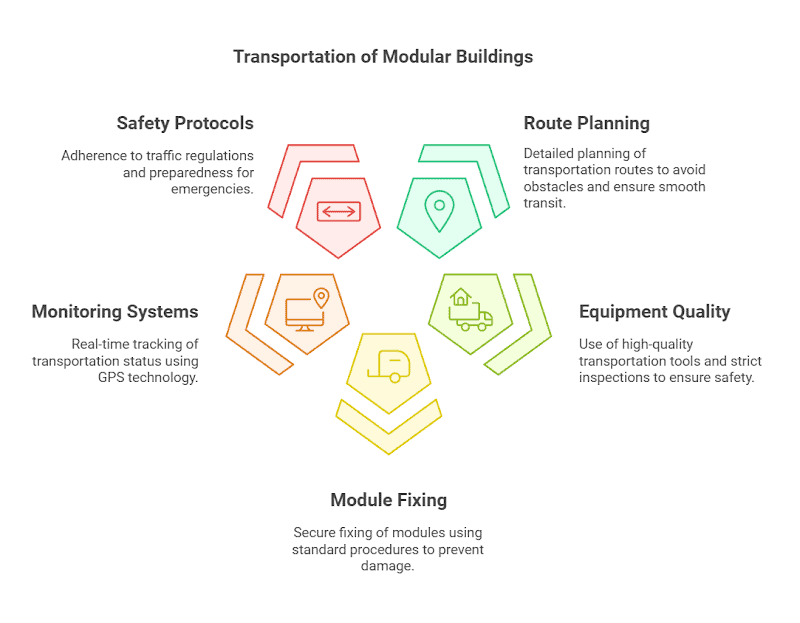
Step 4: On-site assembly and installation of modular buildings
After the modules are transported to the construction site, the installation process officially begins.
First, connect each module one by one according to the design requirements, ensure that the interface between each module is firm, and integrate the necessary electrical, plumbing and HVAC systems. Through the design of modular buildings, all key interfaces are reserved to ensure a smooth assembly process.
SteelPRO Group provides professional remote guidance to ensure that customers can follow the correct steps to install modular buildings. Our engineering team provides customers with real-time help and problem solutions through video conferencing, technical support platforms and detailed operation manuals, helping them to complete on-site installation efficiently and safely, ensuring precise control of building quality and construction period.
Step 5: Acceptance of modular buildings
We use a strict quality management system to ensure that each module has undergone multiple rounds of rigorous inspection and testing during the factory production process. This includes quality inspection of building materials, structural stability testing of modules, and functional inspection of electrical and plumbing systems.
Our engineering team will assist customers in completing the final self-inspection process through detailed documents and video guides. Customers can make final quality confirmation based on the acceptance criteria and checklists we provide. We also provide remote technical support to ensure that customers can get timely and effective help if any problems arise after installation.
Modular building construction safety tips
- Develop a safety plan and set clear warning signs.
- Inspect equipment, comply with load limits, and ensure clear lifting paths. Operators must be certified.
- Check foundation stability and reinforce module connections.
- Use safety gear, set up protective nets, and ensure platform stability.
- Inspect electrical equipment, standardize cable laying, and comply with regulations.
- Implement emergency measures for severe weather, ensure proper drainage.
- Set up evacuation routes and conduct regular safety training.
- Conduct quality checks, identify hidden risks, and ensure compliance with safety standards.
Advantages & Challenges of Modular Construction
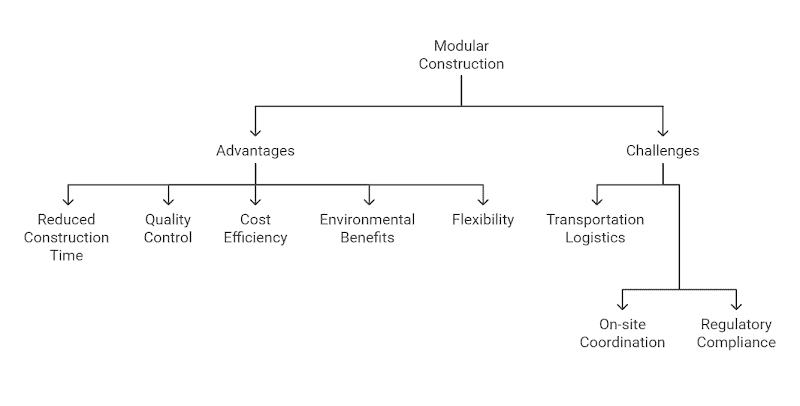
Modular Building Supplier: Build Faster and More Efficiently!
We specialize in modular buildings that combine speed, quality, and sustainability, such as modular homes, modular offices. With more than a decade of experience in steel structure design, fabrication, and delivery, we guarantee that your project will be completed on time and with the highest quality.
Our modular building solutions can also be tailored to your specific needs, providing you with a reliable, cost-effective, and environmentally friendly option. From professional site selection advice to the assembly of modular steel structures, we handle every detail so you can focus on what matters most.
Contact SteelPRO Group to make your modular building project a reality!