Have you ever envisioned owning a house that is both environmentally friendly and worry-free? Today, prefab homes are sweeping the world with their advantages of “fast construction and flexible design”, becoming an ideal choice for many people. But in the face of a variety of quotations, a core question always lingers in mind: how much does a prefab house cost?
The answer is not simple. The cost of prefab houses is far from being generalized as “factory assembly line production” – from the choice of basic materials to the distance of transportation, from the price per square foot to the hidden site fees, each item may double your budget.
This article will dismantle the “iceberg” of costs for you, reveal the 9 major factors that affect the price, and share practical tips for saving costs. Whether you are a first-time homebuyer who is careful about budgeting or a building enthusiast who pursues personalization, this guide can help you make a wise decision.
Prefab house cost breakdown – what’s included? what’s not included?
Items included in prefab house quotes
Material costs: The construction cost of a prefab house first includes the cost of the materials used. Depending on the type of house, the materials can be wood, steel, concrete, etc. Usually, prefabs with steel and concrete structures are relatively expensive, while wood structures are more economical.
Design and customization costs: Standardized designs are usually less expensive, while customized designs (such as special sizes, personalized layouts, and high-end interiors) will add additional costs.
Transportation and logistics costs: Transportation costs are affected by distance, logistics complexity, and traffic conditions. Long-distance transportation or remote areas may incur additional costs.
Construction and installation costs: Installation costs include assembling prefabricated components, connecting pipes and facilities, etc. Prefab houses are usually installed faster than traditional buildings, so the construction costs are relatively low.
Additional facility costs: Some additional facilities, such as electricity supply, water supply pipes, heating systems, etc., will also increase the cost of prefab houses. The cost of these facilities will differ based on the particular design and requirements.
Common Expenses Not Included
- Land Cost: You will need to pay for the purchase or lease of land, and the price varies greatly depending on the location.
- Site Preparation: This entails removing vegetation, grading the land, paving roads, and so forth, which costs about $5,000-$20,000.
- Local Approvals and Taxes: Building permits, environmental assessment fees, property taxes, etc. The specific amount depends on local regulations.
- Long-term Maintenance Costs: Additional budget is required for roof repairs and pipe replacements, among other things.
- Additional Decoration and Equipment: Some additional decoration and equipment, such as furniture, appliances, and outdoor landscaping, are usually not included in the construction cost of prefabricated houses.
Cost Per Square Foot Range
Economy ($50-$150/square foot): Mostly container homes or small units, using basic materials such as light steel and standard insulation.
Mid-range ($150-$250/square foot): Common in modular homes, including some custom designs and energy-saving windows.
High-end ($250+/sq. ft.): Fully custom designs with high-end materials (like reclaimed wood), solar systems, or smart home devices.
Cost-Benefit Analysis of Prefabricated Homes
While prefabricated homes may necessitate a greater upfront investment, the long-term cost savings they offer are evident.
Time saved: Prefabricated homes are much faster to build than traditional homes, with most of the work done in the factory and significantly less on-site construction time. This means that you can not only move in earlier, but also save on temporary accommodation and management costs.
Energy efficiency and sustainability: Prefabricated homes use environmentally friendly designs and efficient insulation materials, which can significantly reduce energy consumption. Many prefabricated homes are also equipped with green technologies such as solar panels, which can save electricity bills and reduce carbon footprint in the long run.
Return on investment: Prefabricated homes generally have a higher long-term value. Due to their energy-saving, environmentally friendly and modern features, prefabricated homes may have better appreciation opportunities in the secondary market, making them an attractive investment option.
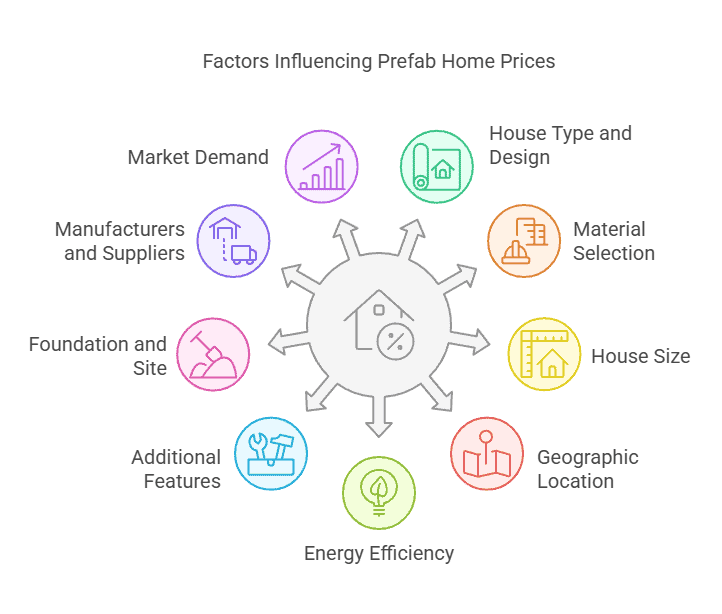
9 Key Factors Affecting the Price of Prefab Homes
1. House Type and Design Complexity
Standardized housing types (such as modular or panelized homes) are less expensive, while fully customized designs (such as curved walls, special structures) can significantly increase costs.
2. Material Selection
Lightweight steel frames are more durable than traditional wood but more expensive, and the price difference between composite flooring and solid wood flooring can be 30%-50%.
High-end insulation materials (such as aerogel) are 2-3 times more expensive than ordinary glass wool.
3. House Size
The total cost increases with the size of the area, but the unit price per square foot may decrease (a benefit of large-scale production). For example:
- 800 square foot cabin: unit price $200 → total price $160,000
- 2,000 square foot home: unit price $180 → total price $360,000
4. Geographic Location
- Shipping costs: For every additional 100 miles from the factory, shipping costs may increase by $1,000-$3,000.
- Local regulations: Some areas require higher earthquake or wind resistance standards, resulting in higher material or design costs.
5. Energy efficiency ratings
Homes that meet LEED or Passivhaus standards will cost 10%-20% more upfront, but the long-term energy savings will offset the cost.
6. Additional features
- Solar panels: $15,000-$25,000
- Smart home system: $5,000-$10,000
- Custom cabinets or high-end bathroom fixtures: The cost may double.
7. Foundation and site conditions
- Flat land installation costs about $5,000-$10,000, and sloped land requires additional reinforcement, which can cost $20,000+.
- Soil testing or special drainage systems: $2,000-$5,000.
8. Manufacturers and Supplier
Prestigious brands (such as Dvele or Blu Homes) have a premium of about 15%-30%. The prices of raw materials, including steel and wood, are influenced by the supply chain. In 2023, the fluctuation of wood costs in North America will cause the price of prefabricated houses to increase by 5%-10%.
9. Market demand and seasonal changes
Prices may rise during peak demand periods, such as spring and summer, and may be more competitive in autumn and winter when demand is lower. In addition, as the market demand for environmentally friendly buildings increases, prefabricated houses using green building materials and technologies may have additional costs.
Different Types of Prefab Homes and Cost Variations
Standard Prefab Homes vs. Custom Prefab Homes
- Standard Prefab Homes
- Cost Range: $80-$150 per square foot.
- Features: Use pre-designed floor plans (e.g., single-story cabins, three-bedroom family homes) with limited material and layout options.
- Advantages: Shorter production time (2-3 months), no additional design fees, ideal for budget-conscious buyers or urgent needs.
- Custom Prefab Homes
- Cost Range: $200-$400+ per square foot.
- Features: Fully personalized designs (e.g., curved glass walls, multi-story structures) with premium materials (e.g., titanium-zinc alloy roofs).
- Additional Costs:
- Design Fees: $5,000-$20,000 (3%-8% of total cost).
- Rush Production Fees: 10%-15% cost increase for shortened timelines.
Modular vs. Non-Modular Prefab Homes
- Modular Prefab Homes
- Cost Range: $120-$250 per square foot.
- Features: Built in factory as complete modules (e.g., rooms with pre-installed utilities), assembled on-site.
- Advantages:
- 30%-50% faster on-site construction.
- High precision, 60% fewer defects compared to traditional builds.
- Additional Costs: Special permits for oversized module transport increase fees by 20%-40%.
- Non-Modular Prefab Homes (Panelized or Component-Based)
- Cost Range: $80-$180 per square foot.
- Features: Shipped as wall/roof panels and assembled on-site with utilities connected afterward.
- Advantages: Greater flexibility for complex terrains or small-scale expansions.
- Additional Costs: Higher on-site labor costs (25%-35% of total budget).
Cost Comparison by Material Type
Material | Cost Range (per sq.ft.) | Features & Long-Term Costs |
Light Steel Frame | $100-$200 | High wind/earthquake resistance, 50+ year lifespan, but requires extra insulation (+$5-$10/sq.ft.). |
Wood Frame | $80-$160 | Traditional choice, easy to modify, but needs pest/rot prevention (annual maintenance: $500-$1,000). |
Precast Concrete | $120-$220 | Superior soundproofing/insulation, ideal for hot/humid climates, but heavy transport increases fees by 15%-25%. |
Shipping Container | $50-$130 | Low initial cost, but retrofitting (windows/insulation/structural reinforcement) can double total costs. |
The construction process of prefabricated houses and their cost
The construction process of prefabricated houses includes several key stages, and the costs of each stage affect the total cost.
Design contract (5%-10% of total cost): This is the beginning stage, where you reach a design agreement with the manufacturer. Standard designs are cheaper, and custom designs will increase costs, accounting for 5% to 10% of the total cost.
Factory production (50%-60% of total cost): All parts are produced and assembled in the factory, usually accounting for 50% to 60% of the total cost.
Transportation (5%-15% of total cost): The cost of transporting the components of the prefabricated house from the factory to the construction site is usually 5% to 15% of the total cost. The cost will be higher when the distance is long and the logistics are complicated.
On-site installation (20%-30% of total cost): This includes infrastructure construction, installation and facility connection on site, accounting for 20% to 30% of the total cost.
The impact of timeline on cost
Fast construction can save loan interest and other expenses, but if expedited production is required, additional costs may be added. Expedited production involves higher expenses, such as accelerated factory production, special shipping and installation arrangements. Therefore, balancing fast delivery with cost is key.
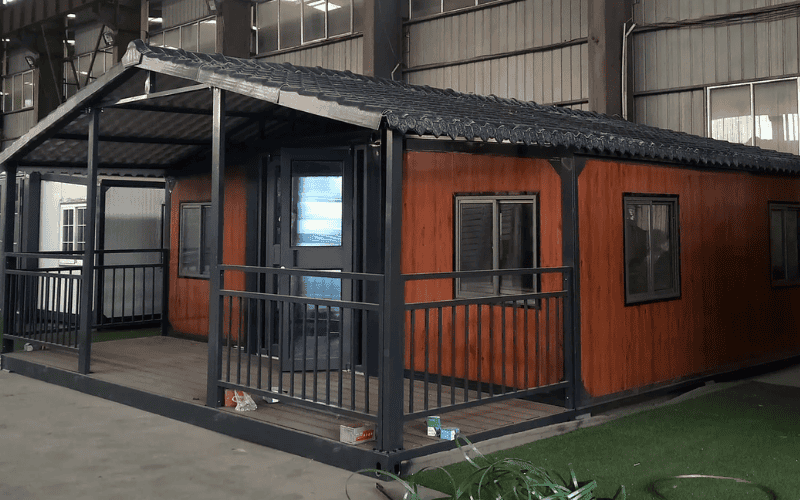
How to Quickly Estimate Prefab Home Costs
Step 1: Determine Basic Parameters
- Size: Measure your desired home size (in square feet).
- Type: Choose a prefab type (this sets the cost per sq.ft):
- Budget-Friendly (shipping container/panelized): $50-$150
- Mid-Range (modular): $150-$250
- High-End (full custom): $250+
Step 2: Calculate Base Cost
- Formula: Base Cost = Size (sq.ft) × Cost per sq.ft
- Example: Modular home (1,500 sq.ft × $180) → $270,000
Step 3: Add Extra Expenses
- Transportation: Estimate $3-$8 per mile (e.g., 200 miles → $1,500-$4,000).
- Upgrades:
- Solar panels: +$15,000
- Smart home system: +$5,000
- Hidden Costs (10%-25% of total budget):
- Land, site prep, permits (e.g., reserve $30,000).
Step 4: Use Quick Estimate Tools
- Online Calculator: Enter size, type, and ZIP code for instant quotes (e.g., HomeAdvisor).
- Contact Manufacturers: Most offer free preliminary quotes (provide floor plans for accuracy).
Cost per Square Foot Reference Table
Type | Low | Mid-Range | High |
Shipping Container | $50 | $90 | $130 |
Modular Home | $150 | $200 | $250 |
Custom Luxury Home | $300 | $400 | $500+ |
One-Line Summary:
Total Cost ≈ (Size × Cost per sq.ft) + Transportation + Upgrades + Land & Hidden Fees
The price difference of prefab houses in different regions around the world
Region | Country/Area | Prefab Home Price Range (per sq.ft.) | Remarks |
North America | USA | $100 – $300 | Higher on the East and West Coast, lower in other areas |
Canada | $100 – $300 | Higher transportation costs arise due to the vast expanse of land and low population density | |
Europe | Germany | $150 – $350 | Higher costs due to strict energy efficiency standards |
Eastern Europe | $100 – $280 | 20%-30% lower than Western Europe | |
Asia | China | $50 – $120 | Lower costs due to economies of scale |
Japan | $200+ | Higher costs due to earthquake-resistant design requirements |
How to reduce the cost of prefab houses
Reducing the cost of prefabricated houses not only helps save budget, but also ensures that the project is successfully completed within the specified budget. Here are a few effective ways:
Choose standardized designs
- Using conventional modules and designs can speed up production and reduce manufacturing costs, while avoiding the increased costs due to personalized needs.
Choose the right building materials
- Choosing the right materials can avoid unnecessary expenses without sacrificing the quality and durability of the house, helping you complete the construction within the budget.
Rational planning and design
- During the design process, try to avoid complex and overly personalized designs. By simplifying the design and rationally planning the structure and function of the house, you can avoid unnecessary costs and ensure efficient use of the budget.
Compare quotations from different suppliers and manufacturers
- Choose competitive suppliers and manufacturers. When choosing a supplier, pay attention not only to the price, but also to the supplier’s reputation, quality and service. By comparing prices with multiple suppliers and optimizing procurement plans, you can reduce procurement costs while ensuring quality.
If you are looking for cost-effective prefabricated houses, as a leading Chinese manufacturer, we offer prefabricated house options with obvious price advantages. Whether you prefer a standard design or have customized requirements, we can offer you high-quality solutions, such as prefab guest house, prefab office, prefab home, etc. Contact us for more details and start your prefab house project!
FAQs
Can prefabricated homes be financed?
Yes. Most prefabricated home buyers can finance their homes through loans, installment payments, etc.
How much does a 2,000 square foot modular home cost?
A 2,000 square foot modular home typically costs between $150,000 and $400,000, depending on the design, materials, and location.
How much does a 1,500 square foot modular home cost?
A 1,500 square foot modular home usually costs between $120,000 and $350,000, with variations based on design and customization.
Prefab house cost per square foot?
The average cost per square foot for a prefabricated house varies between $50 and $300, depending on factors such as materials, design, and location.
Small prefab house cost?
Small prefab houses can cost anywhere between $10,000 and $100,000, depending on the size, materials, and customization level.
How much does a prefab house cost in the UK?
In the UK, the price of a prefabricated house generally falls between £80,000 and £200,000, contingent upon its size, design, and location.
What is the cheapest type of house to build?
The cheapest type of house to build is usually a tiny home or modular home, as they are compact, use fewer materials, and have shorter construction times.