On average, modular homes range from 20,000 to 80,000 pounds, but this can go higher or lower depending on the type of home you choose.
Understanding the weight is not just about numbers—it impacts everything from transportation costs to foundation requirements. In this article, we’ll dive into the key factors that influence modular home weight, including construction materials, number of modules, and custom features. We’ll also cover how weight is calculated and why it matters for installation and legal regulations.
What is the average weight of a modular home?
The average modular home weighs between 20,000 and 80,000 pounds, but this can vary depending on the type of home and structure.
- Tiny homes are typically the lightest, weighing as little as 10,000 pounds. These compact homes are ideal for those seeking a minimalist lifestyle or a small space.
- Single-module homes typically weigh between 15,000 and 30,000 pounds, depending on their size and features.
- Double-wide homes weigh around 30,000 to 60,000 pounds, and some are even heavier, especially if they include custom features or steel framing.
- Multi-story modular homes are the heaviest, sometimes exceeding 80,000 pounds, due to the increased number of modules and increased structural complexity.
What Affects the Weight of a Modular Home?
Several factors contribute to the weight of a modular home, and each of them plays a crucial role in determining how much your home will weigh. Let’s dive into the key elements that influence weight, from construction materials to custom features.
1. Construction Materials Used
The materials chosen for the home’s structure are a primary factor in its overall weight.
- Steel-framed homes are typically the heaviest due to steel’s density and strength. Steel framing offers superior durability and can withstand harsher weather conditions, but it comes with added weight.
- Wood-framed homes are lighter since wood has a lower density compared to steel. While wood framing is more cost-effective, it may not offer the same strength as steel and may require additional support, especially for larger homes.
- SIP (Structural Insulated Panels), which are used for walls and roofs, consist of an insulating foam core sandwiched between two structural boards (often OSB or plywood). The thickness of the foam core directly influences the panel’s weight. SIPs are often used in energy-efficient designs, but they can add weight compared to traditional wood framing, especially in thicker wall systems (e.g., 8 to 10 inches).
- Off-frame construction (where the home is built directly on its foundation, not on a steel or wood chassis) can sometimes result in a lighter module. Off-frame designs usually eliminate the need for a heavy transportation chassis, reducing the total weight.
In general, the type of framing material and its thickness (for example, thicker steel or wood beams) will dictate how much the modular home weighs.
2. Number of Modules or Stories
The weight of the home increases with the number of modules or stories.
- A single-story home with one module is typically lighter, as it requires fewer structural supports. These homes tend to have a lower center of gravity, which can make transportation and foundation installation easier.
- A multi-story modular home, on the other hand, is considerably heavier because it requires additional structural supports for the upper floors. These homes usually involve a larger framework, additional steel reinforcement, and specialized lifting equipment for transport and installation. For example, a two-story home will weigh much more than a single-story one of the same square footage due to the load-bearing capacity required for the upper level.
More modules added to a home for greater space (such as a double-wide or triple-wide) results in more materials and heavier load-bearing structures, further increasing the weight.
3. Roof Type, Insulation, and Wall Thickness
Several elements related to the roof, insulation, and wall construction influence the weight:
- Roof type: A pitched roof with beams, trusses, and extra support materials will weigh more than a flat roof. The added structural beams, rafters, and insulation needed for a sloped roof increase the overall weight.
- Insulation: The thickness and type of insulation material affect the weight as well. For instance, spray foam insulation is denser and heavier compared to fiberglass batt insulation. A thicker layer of insulation improves energy efficiency but adds weight.
- Wall thickness: The thickness of exterior walls contributes to weight. Modular homes with thicker walls (such as those incorporating 2×6 framing for additional insulation) will be heavier than those with thinner walls. Double-wall construction (where two layers of walls are used for extra durability and insulation) also adds considerable weight.
4. Customizations and Features
Custom elements like flooring, cabinetry, and bathroom/kitchen units can significantly impact the weight.
- Flooring: Heavy materials like ceramic tile, marble, or hardwood flooring will add substantial weight compared to lighter materials like laminate or vinyl. A 1,000 square foot floor of ceramic tiles can add more than 10,000 pounds to the weight of your home.
- Cabinetry and Fixtures: High-end custom cabinetry and features made from dense materials (e.g., solid wood vs. MDF) will add weight. Additionally, specialized fixtures like heavy stone countertops in kitchens or bathrooms contribute to the overall weight.
- Appliances and Bathroom/Kitchen Units: Large appliances (like refrigerators, ovens, and washers) and heavy bathroom fixtures (like bathtubs or stone sinks) also contribute to the weight. These features may not be part of the initial build but could be incorporated later, adding to the final weight.
5. Main Dimensions
The overall size of the modular home is a key factor in determining weight. Larger homes with more square footage or rooms require more materials, and thus, will weigh more.
- Larger homes with more rooms, like a four-bedroom home, will be heavier due to the increased need for framing, insulation, and finishes.
- Floor plan configuration also matters; for example, open concept layouts that use large beams or support columns will weigh more than homes with traditional internal load-bearing walls.
- The height of the home impacts the materials used in the construction. Multi-level homes will require extra steel supports or reinforced wood framing, further increasing the weight.
In short, the larger the home, the more materials are needed, and the heavier it will be. This is a crucial factor when considering transportation logistics and ensuring your foundation can handle the load.
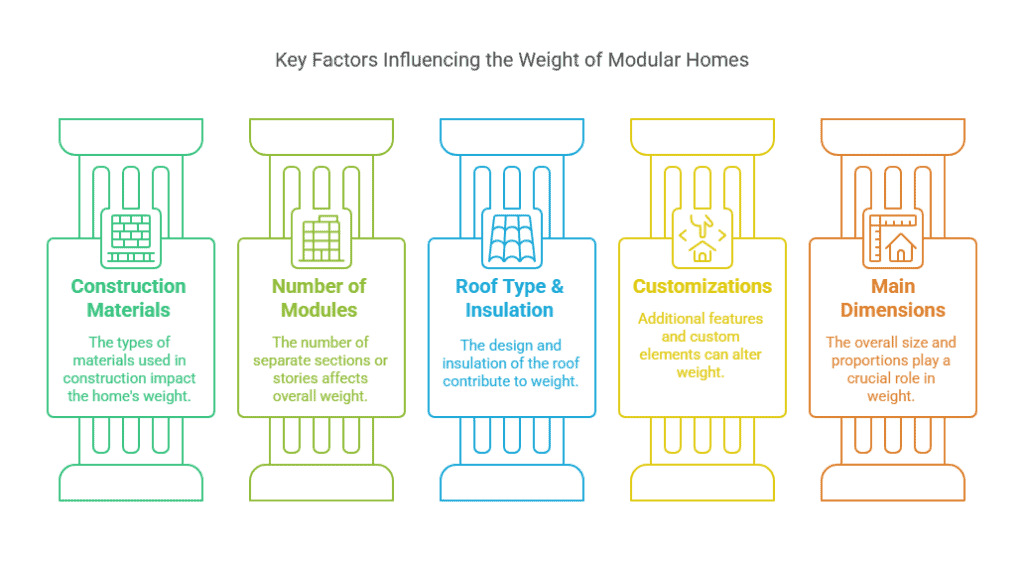
Why Does the Weight of a Modular Home Matter to You?
Understanding the weight of your modular home is not just about the numbers on the scale. The weight influences several practical aspects of the building process, from transportation and delivery to installation and long-term structural integrity. Here’s why it matters:
1. Impact on Transportation and Delivery Costs
The weight of a modular home directly affects how much it will cost to transport. Heavier homes require larger, specialized transport vehicles that can handle the load. This means that delivery costs for a steel-framed or multi-module home will typically be higher than those for a lightweight, wood-framed unit.
Additionally, weight affects the transportation route. Roads with weight restrictions or narrow bridges may require special permits or route planning, adding more time and costs to the delivery. Transport companies may also need to use escort vehicles to ensure safe travel, especially for larger or heavier homes.
The weight of the module has a direct impact on the transport vehicle needed.
- For light modules (e.g., tiny homes or single modules with wood framing), a standard flatbed truck or trailer may suffice.
- Heavier modules (such as those with steel frames or larger sizes) will require specialized transport vehicles with higher load capacities. These vehicles are equipped to handle the extra weight and ensure safe transport.
- The size and weight of the transport vehicle also impact the type of roads that can be used. Heavier modules may require permit approvals for oversized loads, and routes might need to be adjusted based on bridge or road weight limits.
Ensuring that the transport vehicle is correctly chosen for the module’s weight is vital to avoid delays, additional costs, or potential damage during transport.
2. Crane Lifting and Installation Setup
When your modular home arrives at the site, the weight also impacts how it will be lifted and installed. Heavier homes require larger cranes with greater lifting capacities to move them into position. The setup and logistics for lifting can be more complicated, especially if your home is multi-story or consists of multiple modules.
For example, a two-story modular home will require a more complex installation process compared to a single-story home. Cranes may need to lift individual modules higher or use a multi-stage lifting process, adding both time and cost to the installation.
3. Foundation Design and Soil-Bearing Capacity
One of the most important factors influenced by a modular home’s weight is the foundation. The heavier the home, the more robust the foundation must be to support it. This means that for heavier homes, the foundation needs to be designed to handle greater soil-bearing loads.
For example, a double-wide modular home with a steel frame may require a concrete slab foundation or pier and beam foundation with reinforced supports, whereas a lighter, wood-framed modular home may only need a simpler, less expensive foundation system. If your site has soft or unstable soil, the weight of the home will be a significant factor in determining whether additional foundation reinforcements, like deeper footings or additional supports, are needed.
4. Permitting and Structural Safety Standards
Local building codes and permitting regulations often take weight into account. Some areas have weight restrictions for transportation, and depending on your location, there may be limits on the load-bearing capacity of foundations or structural elements.
Additionally, structural safety standards require that modular homes, particularly heavier ones, meet specific guidelines to ensure long-term stability and safety. Local authorities will often require detailed plans from engineers to ensure the home’s foundation and structure can support the weight over time, especially in areas prone to earthquakes, heavy winds, or extreme weather.
In some cases, heavier modular homes may also require more stringent inspections and certifications, which can increase costs and delays during the permitting process.
How Much Does a Single Module Typically Weigh?
A single module is typically the basic unit of a modular home, and its weight depends on its dimensions and materials. A single module, usually about 14 to 16 feet wide and 40 to 60 feet long, typically weighs between 10,000 to 30,000 pounds.
Transport Weight vs. Installed Weight
There’s a key difference between the transport weight of a module and its installed weight. The transport weight refers to the weight of the module when it is being moved to the site. It includes the module itself and any additional transportation-related materials, such as the frame for transport.
Once the module arrives at the site and is installed, the installed weight might be slightly less. This is because the transportation frame and other temporary materials used to stabilize the module during delivery are removed. However, the difference is typically minimal. The installed weight is what matters most for foundation and structural planning.
Understanding this distinction is crucial when planning the foundation design and transportation logistics.
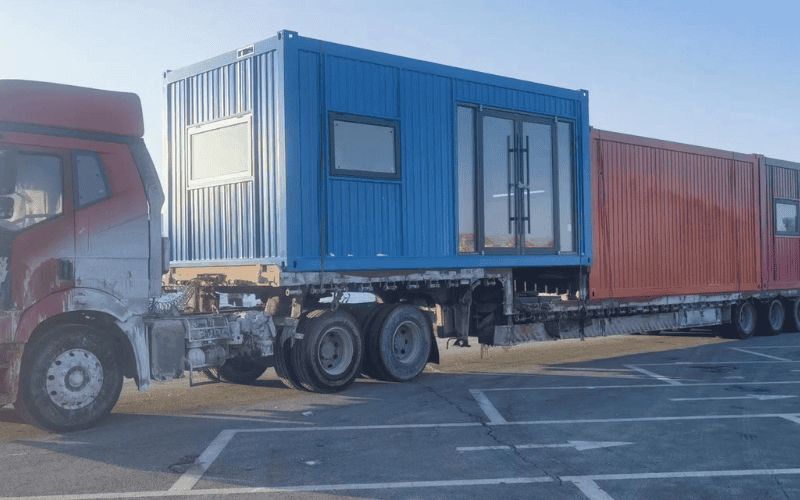
How Is Modular Home Weight Calculated or Verified?
Understanding how the weight of a modular home is calculated or verified is crucial for proper planning, transportation, and installation. There are several methods used to estimate and confirm the weight, and each plays a role in ensuring the home is properly prepared for delivery and setup.
1. Per-Square-Foot Estimation vs. Engineering Specs
The most basic method to estimate the weight of a modular home is through per-square-foot estimation. This involves calculating the weight based on the square footage of the home and using a general weight range for the construction materials. For instance, a typical modular home can weigh between 20 to 30 pounds per square foot, depending on the materials used (steel vs. wood vs. SIP panels). This method provides a quick ballpark figure but may not be as precise as engineering specs.
For more accurate calculations, modular home manufacturers often use engineering specifications. These specs take into account the specific materials used, the size of the modules, the type of foundation, and even the roofing and insulation. The engineering team will provide a detailed breakdown of the expected weight for each module and the home as a whole.
2. Who Provides This Information?
The manufacturer of the modular home is typically the primary source of weight data. They will provide weight estimates based on the design specifications of the home. Manufacturers will often have standardized weight ranges for various models, especially if they produce many similar units.
However, for more complex or custom designs, the architect or engineer involved in the planning and design of the modular home will be able to provide a more precise weight estimate. These professionals calculate the weight based on the materials and design specifications provided by the manufacturer.
3. Tools or Documentation to Look for When Planning
When planning for your modular home, it’s essential to ask for the following tools or documents to ensure accurate weight estimation:
- Design specifications: These will include detailed information on materials used, dimensions, and any custom features that may affect weight.
- Structural engineering reports: If the home is custom-built or includes special features, you may need an engineering report that specifies the expected weight and load distribution.
- Weight calculation sheet: Some manufacturers provide a detailed sheet outlining the estimated weight per module, per square foot, and for the entire structure. This can be particularly helpful for logistics and foundation planning.
- Transport weight info: For large homes, ask for transportation weight details that include any additional factors, such as temporary supports used during transport.
Having these documents on hand can help ensure your home is properly prepared for installation and any weight-related considerations are addressed.
4. Legal Regulations Regarding Weight Limitations for Transport or Installation
Local legal regulations play a significant role in the transportation and installation of modular homes. Many areas have specific weight limits for transport vehicles, especially for oversized loads. Before transport, it’s crucial to verify:
- Road weight restrictions: Certain roads, bridges, and tunnels may have weight limits, requiring special routing or permits for your modular home delivery.
- Permit requirements: If the home exceeds the standard weight limits, you may need to apply for oversized load permits. This process involves providing details on the weight, dimensions, and route to local authorities.
- Installation site regulations: Depending on the area, you may also need to ensure that the foundation or soil can support the weight of the home. Some local building codes and zoning laws may impose specific requirements for structural weight limits in residential areas, particularly in flood-prone or unstable soil regions.
Be sure to discuss these regulations with your transportation company and installation contractor to avoid delays or legal issues during the home delivery and setup process.
Take the Next Step Toward Your Modular Home
If you’re ready to take the next step and explore modular homes tailored to your specific needs, we’re here to help. We at SteelPRO PEB specialize in high-quality modular homes, including modular dorms, modular townhomes, multi-family modular homes, and more. These homes are designed with durability, efficiency, and ease of installation in mind. Contact us today to start building your dream home, or learn more about how we can help you plan a smooth, worry-free build process.
FAQs
How much does a mobile home weigh?
A mobile home typically weighs between 15,000 to 35,000 pounds, depending on its size and materials.
How much does a manufactured home weigh?
A manufactured home usually weighs between 20,000 to 50,000 pounds, with the weight varying based on the number of sections and construction materials.
How much does a trailer home weigh?
A trailer home generally weighs between 5,000 to 10,000 pounds for smaller, single-section units, and can go up to 30,000 pounds for larger models.