Over the last five years, the modular construction market has grown significantly. In 2020, it was valued at around $76.9 billion and is expected to reach $157.5 billion by 2027, growing at an annual rate of about 10.4%. The demand for modular construction has been especially strong in North America. In the U.S., the market was worth $7.8 billion in 2019, and it’s projected to grow to $13.5 billion by 2026. In terms of adoption, the residential sector has led the way. In 2021, approximately 3% of new homes in the U.S. were built using modular methods, while the figure was around 10% in the UK. The UK government plans to increase this number in the coming years.
One of the main benefits of modular construction is its ability to speed up project timelines. Compared to traditional methods, modular construction can shorten the building process by 30-50%, with some projects completed in just 60-90 days. Since much of the work is done off-site in factories, this approach also reduces construction waste by up to 90%, helping to lower the carbon footprint by 20-40%.
In 2024, with the rise of technologies like BIM (Building Information Modeling) and 3D printing, the efficiency of both design and production in modular construction continues to improve. While challenges remain in logistics and regulatory adjustments, modular construction is increasingly being used in sectors like residential, healthcare, and commercial buildings, becoming an essential trend in the future of construction.
The Integration of Robotics and Automation
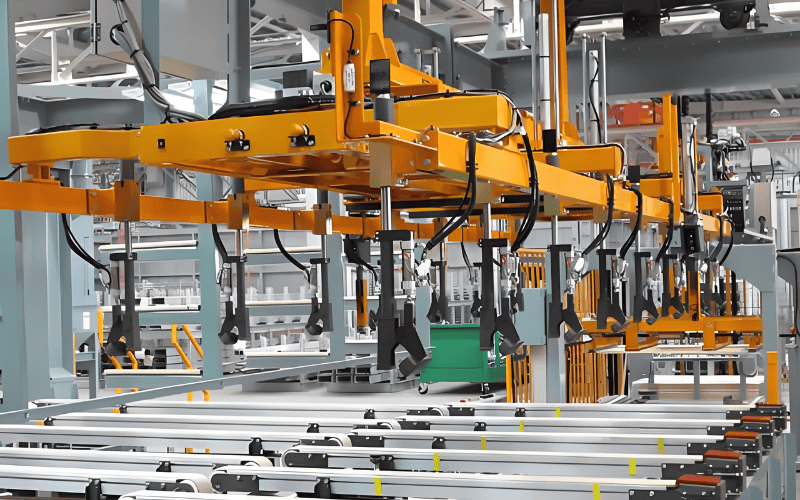
One of the biggest changes in modular construction is the use of robotics and automation. These technologies speed up the production of building materials, improve precision, and allow for greater customization. For example, ICON uses the Vulcan 3D printer to create building modules, which has significantly cut labor costs and construction times. According to McKinsey, robotics can boost construction efficiency by 30-40% while reducing human errors and waste.
This isn’t just about new technology—it’s a shift in how construction is done. Robots can work around the clock without human intervention, lowering the chances of mistakes. They also allow for precise customization of building components based on specific needs, making the entire process faster and more flexible.
Modular Construction as a Solution for Social Housing
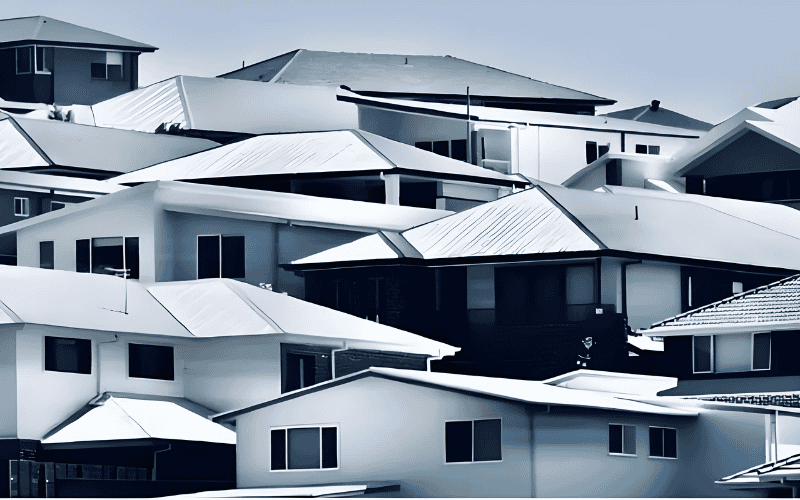
The global housing crisis is growing, especially in large cities, where slums and inadequate housing remain major issues. According to UN-Habitat, around 1 billion people live in unsafe housing worldwide. In response, more countries are adopting modular construction to quickly build affordable housing.
For example, the UK government has pledged to build 100,000 modular homes by 2030, and Ymere Housing Association in the Netherlands is using modular buildings to provide affordable housing in city centers. These projects significantly reduce construction time and cost. Similarly, New York City is launching several modular social housing projects to provide homes for low-income residents.
Governments are increasingly recognizing the cost-effectiveness and speed of modular construction. It’s no longer seen as just a “cheap” solution—modular buildings are proving to be a high-quality, sustainable way to meet the growing demand for affordable housing.
Smart Modular Buildings: Combining IoT and Sustainable Design
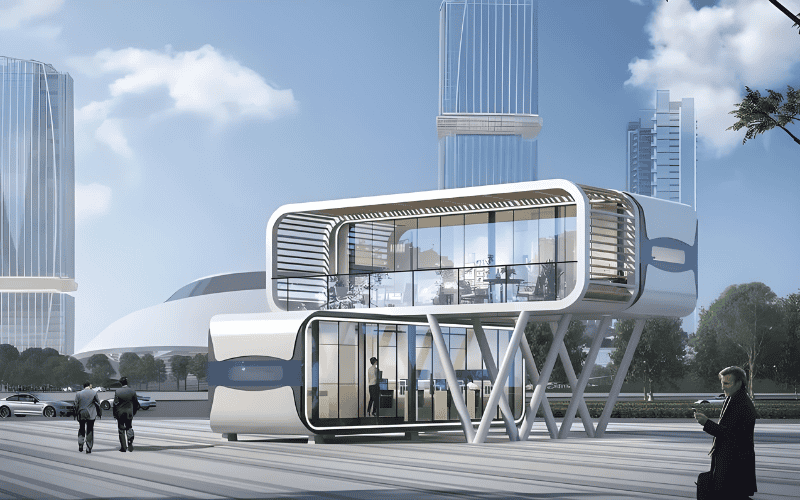
Smart modular buildings are the future of construction. With advancements in Internet of Things (IoT) technology, more modular buildings are incorporating smart systems to improve energy efficiency, comfort, and safety. Features like smart thermostats, security systems, and automated energy management are becoming common in modular homes.
According to Global Market Insights, the global smart building market will reach $240 billion by 2027, with smart modular buildings playing a key role. At the same time, many modular projects are following sustainable design standards, like LEED certification, to reduce carbon emissions and improve energy efficiency.
By combining green design with smart technology, modular buildings are not only helping conserve energy but also enhancing residents’ quality of life. For example, Modular Living has developed smart housing units that include temperature control systems and solar panels, showing how technology and sustainability can work together to create better, more energy-efficient living spaces.
Related Reading:
Modular Construction: Driving Innovation in Renewable Energy
BIM Enhances Modular Construction Design and Efficiency
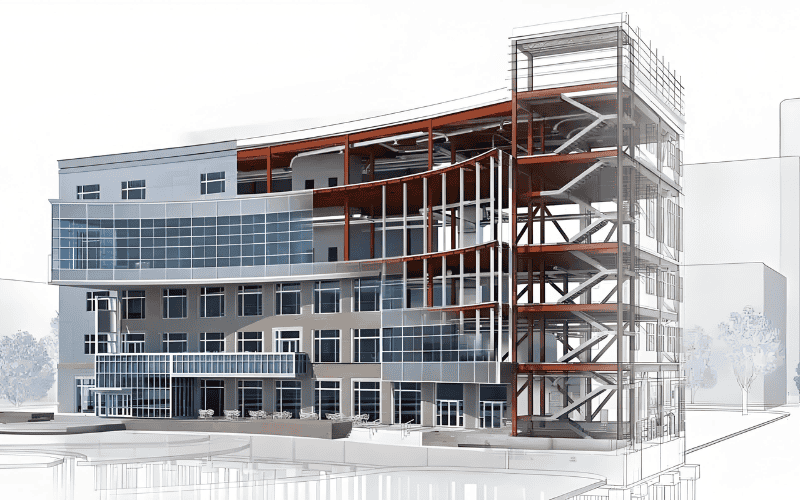
Building Information Modeling (BIM) is transforming the way modular buildings are designed, produced, and constructed. According to Autodesk, BIM can reduce design errors by 30% and cut changes and adjustments during construction by 50%. With BIM, all parties involved—designers, manufacturers, and contractors—can collaborate more efficiently, ensuring that every modular component fits perfectly, reducing both time and cost.
The real advantage of BIM is its ability to allow for a complete virtual design of the project before construction begins. This helps identify potential issues early, optimize designs, and make the production process more efficient. For instance, Katerra uses BIM to enhance accuracy and speed in modular construction while minimizing the need for on-site adjustments. Similarly, the Modular Construction Hub project in the UK has demonstrated how BIM, when combined with modular techniques, can significantly improve productivity and reduce material waste.
The Rise of High-Rise Modular Buildings
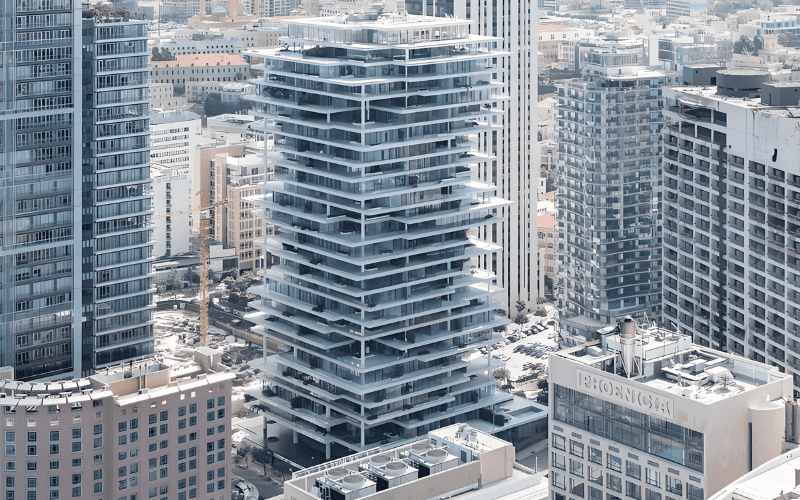
Modular construction is no longer limited to low-rise buildings. Thanks to advances in transportation, manufacturing technology, and structural design, high-rise modular buildings are now becoming a reality. These buildings reduce construction costs and speed up the process, offering a new solution for dense urban areas.
In Brooklyn, the B2 Tower became the world’s tallest modular building, standing 32 stories tall. This project demonstrated that modular technology can be successfully applied to high-rise construction, providing efficient, high-quality buildings. Similarly, in Sydney, a new high-rise modular residential complex is under development, which will push the limits of what modular construction can achieve.
These projects show that modular construction is no longer just for small homes or low-rise buildings—it’s now a viable option for larger, more complex projects, including high-rise buildings.
Summary
Modular construction continues to evolve, driven by technological advancements, growing global demand for affordable housing, and a focus on sustainability. The trends discussed above demonstrate how modular construction is poised to shape the future of the building industry, offering faster, more cost-effective, and environmentally friendly solutions to meet the needs of modern society.