What is a Prefab House?
A prefabricated house refers to a dwelling where its components, including modules and panels, are produced in a factory setting before being transported to the desired location for assembly.
This construction method is different from traditional on-site construction. The components of prefabricated houses can be precisely manufactured in the factory, thereby improving construction accuracy and construction efficiency, reducing construction time and costs.
In this way, the workload on the construction site is greatly reduced, and only quick assembly is required without tedious on-site construction. For SteelPRO Group, the steel structure prefabricated houses we provide not only ensure strength and durability, but also achieve high standards of construction quality while saving time and cost.
Main types of prefab homes
Based on the structure and construction method, prefabricated houses can be divided into the following main types:
1. Modular Homes
- Description: Modular homes are made from multiple prefabricated modules (sections) that are constructed in a factory. The modules are then transported to the site and assembled.
- Benefits:
- Fast construction with over 90% of the work done in the factory.
- High quality with less influence from weather.
- Flexible design, with modules that can be stacked or combined for different configurations.
- Uses: Common for permanent residences, vacation homes, hotels, and apartments.
2. Panelized Homes
- Description: This type involves prefabricated panels (walls, floors, roofs) produced in a factory and assembled on-site.
- Benefits:
- High flexibility for customization on-site.
- Easier to transport as panels are smaller than full modules.
- Suitable for customized residential or commercial buildings.
- Uses: Typically used for single-family homes or rural houses.
3. Pre-engineered Steel Homes
- Description: These homes use a steel frame as the main structural component, with prefabricated steel panels or composite materials for walls and roofs.
- Benefits:
- Extremely durable and resistant to wind, seismic activity, and fire.
- Short construction times with easy expansion and modification.
- Cost-effective in mass production.
- Uses: Common in warehouses, industrial buildings, commercial structures, and modern homes.
4. Precast Concrete Homes
- Description: Precast concrete panels or sections are fabricated in a factory and then assembled at the construction site.
- Benefits:
- Highly durable, fire-resistant, and weather-resistant.
- Efficient for high-rise buildings and offers a high level of construction quality.
- Faster construction due to minimal wet work on-site.
- Uses: Suitable for multi-story apartments, commercial buildings, and residential projects.
5. Shipping Container Homes
- Description: Container homes are made by repurposing shipping containers into living or working spaces, often stacking or connecting them to form a structure.
- Benefits:
- Low cost and environmentally friendly.
- Strong structure, ideal for temporary or permanent housing.
- Highly portable and flexible, great for disaster relief or mobile housing.
- Uses: Popular for vacation homes, office spaces, emergency shelters, and small housing units.
6. Mobile Homes (Tiny Homes)
- Description: Small, prefabricated homes placed on a movable chassis, allowing them to be relocated.
- Benefits:
- Highly flexible, can be moved easily.
- Affordable and well-suited for individuals or small families.
- Great for temporary or long-term living on a budget.
- Uses: Often used for camping, mobile offices, small housing units, and temporary housing.
7. 3D Printed Homes
- Description: 3D printing technology is used to create the structure of a home, usually with concrete or biodegradable materials.
- Benefits:
- Very fast construction—some homes can be built in days.
- Reduces material waste and increases sustainability.
- Customizable designs for unique or futuristic structures.
- Uses: Likely to be a major solution for affordable housing, disaster relief, and environmentally-friendly building in the future.
Advantages and Disadvantages of Prefabricated Houses
Advantages | Disadvantages |
Faster Construction – Quick assembly in the factory. | Limited Design Flexibility – Less custom design. |
Cost-Effective – Lower cost due to efficient manufacturing. | Financing Challenges – Harder to get loans, lower resale value. |
Quality Control – Consistent quality with fewer defects. | Transportation Costs – High delivery costs for remote areas. |
Customizable – Flexible design options. | Location Restrictions – Not suitable for all climates/terrains. |
Energy Efficient – Better insulation and energy-saving features. | Durability Concerns – May not last as long in harsh conditions. |
Eco-Friendly – Sustainable materials, less waste. | Stigma – Perceived as lower quality by some. |
Portability – Some types (e.g., mobile homes) are easy to move. | Building Codes – May not meet local regulations. |
Application of Prefab Houses
Residential Homes | Affordable Housing |
Vacation Homes | Sustainable Communities |
Student Housing | Military Housing |
Temporary Offices | Healthcare Facilities |
Commercial Spaces | Disaster Relief Housing |
Main Materials of Prefabricated Houses
The material of prefabricated houses selection is key to the safety, comfort, and energy efficiency. SteelPRO PEB focuses on high strength, durability, and environmental adaptability.
- Structural Materials
- Steel: The core material for its high strength, earthquake resistance, and durability. Steel ensures stability in extreme climates and reduces maintenance costs.
- Insulation and Soundproofing
- SIPs (Structural Insulated Panels): Improve thermal insulation and reduce heat loss, while also providing excellent soundproofing. Ideal for energy efficiency and creating a quiet, comfortable environment.
- Surface Materials
- Exterior Walls & Roofs: We offer steel, which provides windproof, waterproof, and fireproof features, making it suitable for various climates. SteelPRO designs offer both durability and customizable aesthetics.
This summary highlights the key materials SteelPRO uses to ensure strong, energy-efficient, and adaptable prefabricated homes.
The Construction Process of Prefab Homes
The construction process of prefabricated houses is divided into design and planning, factory manufacturing, transportation and construction, and quality control. We offer comprehensive assistance to guarantee the efficient and precise completion of every step.
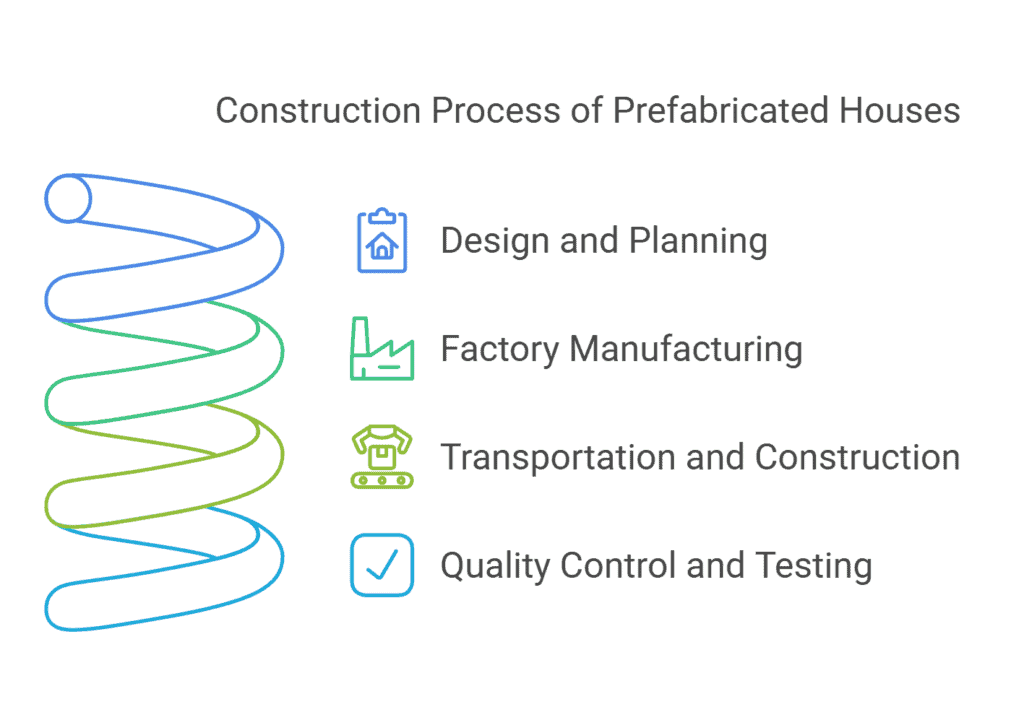
- Design and planning: The design of prefabricated houses is usually completed before factory production. We offer customers flexible customization options, tailoring the house’s size, layout, structure, and other features to meet their specific requirements. Whether it is a simple single-story house or a complex multi-story building, our design team will work closely with customers to ensure that every detail meets expectations.
- Factory manufacturing: During the production stage of prefabricated houses, all parts of the house (such as walls, roofs, floors, etc.) are manufactured in the factory. We utilize high-strength steel and state-of-the-art production techniques to guarantee that each component meets rigorous standards.
- Transportation and construction construction: After manufacturing, the parts are transported to the construction site for assembly. We ensure safe and intact transportation and provide remote technical support to assist customers in completing the assembly work smoothly. Because they are pre-manufactured components, the construction period is greatly shortened, and the complexity and uncertainty of the construction site are greatly reduced.
- Quality Control and Testing: SteelPRO Group always adheres to strict quality control throughout the construction process. From the procurement of raw materials to the production of each component, to transportation and assembly, we carry out strict quality checks. All components are tested in detail to ensure that they meet high standards in terms of durability, earthquake resistance, wind resistance, etc.
Maintenance of Prefab Houses
Proper maintenance helps extend the lifespan of prefabricated houses and ensures they remain energy-efficient and comfortable.
- Regular Inspections: Check for any signs of wear, such as cracks in the walls or roof, and ensure the structure remains secure.
- Cleaning: Regularly clean the exterior, windows, and gutters to prevent dirt buildup and ensure proper drainage.
- Roof and Insulation: Inspect the roof for damage or leaks, and maintain insulation to ensure energy efficiency.
- Pest Control: Keep an eye out for pests, especially in wooden structures, and treat any infestations early.
- HVAC System Maintenance: Regularly service heating, ventilation, and air conditioning systems to keep them running efficiently.
- Exterior Coatings: Repaint or treat exterior surfaces to protect against weathering and corrosion, especially for metal and wooden components.
The Difference Between Prefabricated Houses and Modular Houses
Prefabricated homes are a broad category of homes built using prefabricated components, which can include paneling, steel framing, shipping containers, or modular methods. A modular home is a type of prefabricated home made from fully constructed modules that are transported and assembled on site.
All modular homes are prefabricated, but not all prefabricated homes are modular. The main difference is that modular homes are delivered nearly complete and require minimal on-site work, while prefabricated homes vary in construction methods and assembly processes.
Related Reading: Prefab Home vs Modular Home
Historical Background of Prefab Homes
The history of prefabricated houses is long and has gone through several important stages of development:
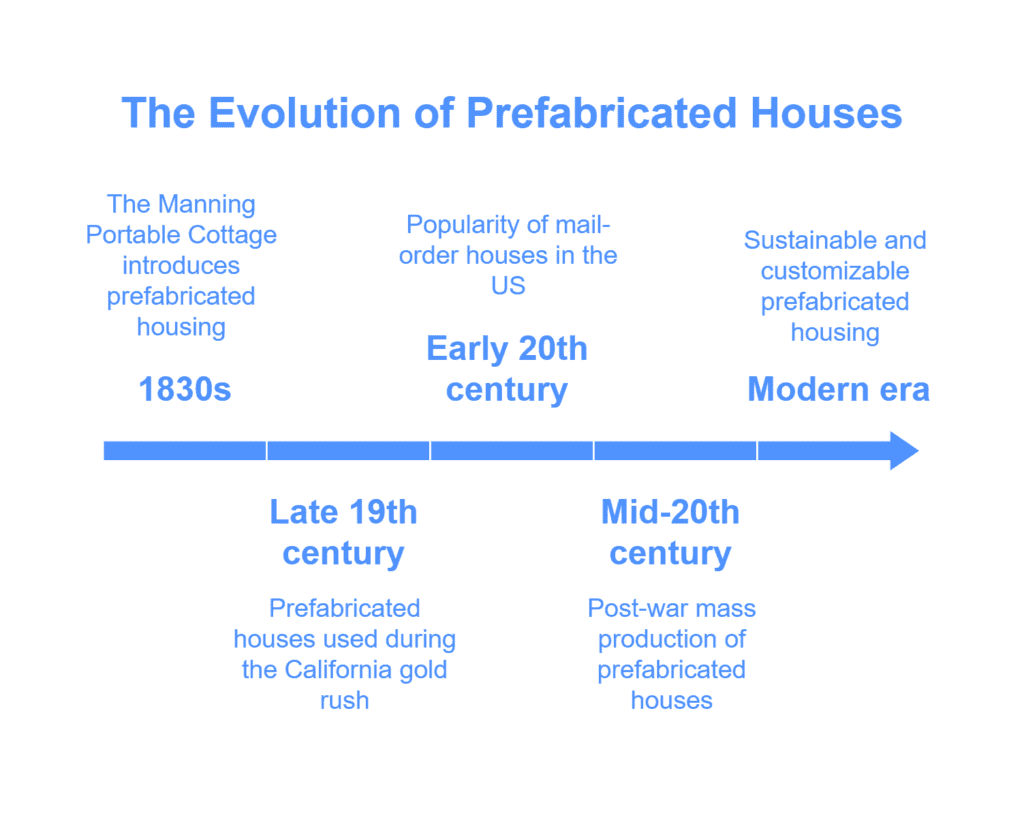
Early 19th century – the first prefabricated house
The earliest prefabricated house appeared in the 1830s, the Manning Portable Cottage designed by British craftsman H. John Manning. This disassembled and reassembled house provided a convenient living solution for immigrants and opened the history of prefabricated houses.
Late 19th century – application in the US gold rush
During the California gold rush in the United States, there was a significant increase in the use of prefabricated houses. A large number of miners needed to quickly build homes, and the efficient construction method of prefabricated houses was very suitable for this demand and became an ideal choice at the time.
Early 20th century – factory production and popularization
After entering the 20th century, prefabricated houses became more popular in the United States, especially through the mail order house (Kit Houses). The materials of these houses were prepared in advance and sent to customers by mail.
Customers only needed to assemble them on site according to the instructions. This type of house is widely used throughout the United States and has become the main way for ordinary families to buy.
Mid-20th century – post-war demand and mass production
After World War II, as demand for housing in the United States and Europe increased dramatically, prefabricated housing quickly became a solution to the housing shortage. Factory production improved efficiency, and standardized design significantly reduced production costs. A large number of prefabricated houses were used to solve housing problems in post-war reconstruction and urbanization.
Modern development – sustainability and customization
Today, prefabricated housing is not limited to simple structures, but covers a variety of designs and materials, used in residential, commercial spaces, and even temporary buildings. Through SteelPRO PEB’s innovative design and high-quality steel structures, our products can help customers achieve more efficient, more durable, and more environmentally friendly building solutions, promoting the sustainable development of modern architecture.
Future Trends of Prefabricated Houses
The future of prefabricated houses will focus on sustainability, using eco-friendly materials and energy-efficient designs.
Smart home features and modular designs will offer more flexibility and convenience. Advances in 3D printing and manufacturing will make construction faster and more affordable, while these homes will also provide affordable housing solutions and energy-efficient living options.
Prefab Homes Supplier
SteelPRO Group has been in the field of steel structure prefabricated houses for many years. Through advanced production technology and professional customized services, we ensure that we provide customers with high-quality, durable and demand-oriented building solutions.
Our high-strength steel structure materials, environmentally friendly technologies and fast delivery capabilities help customers realize their ideal residential or commercial space more efficiently and economically.
We believe that with the continuous advancement of technology, prefabricated houses will be used in a wider range of fields and become the mainstream trend of future construction. SteelPRO Group will continue to innovate and provide more efficient, environmentally friendly and intelligent prefabricated house solutions to help customers better cope with future market challenges.
FAQs
- Where Can I Buy PrefabHouses?
You can purchase high-quality prefabricated houses from SteelPRO PEB, a trusted supplier specializing in steel structure prefab homes. We provide durable, customizable, and energy-efficient solutions to meet your needs. Contact us for more details!
- How Much Do Prefabricated Houses Cost?
The price varies depending on the size, materials, design, and location. Generally, prefabricated houses are more cost-effective than traditional homes. For a personalized quote, reach out to SteelPRO PEB for pricing details based on your project requirements.
- How Can I Finance a Prefab Home?
Financing options include mortgages, construction loans, and personal loans. Some lenders offer specialized loans for prefabricated homes. We recommend checking with local banks or financial institutions to find the best financing option.
- How Long Does It Take to Build a Prefab House?
Construction time depends on the house size and complexity, but prefabricated homes are built much faster than traditional homes. On average, production takes a few weeks, and on-site assembly can be completed in a few days to a few weeks.