Steel structure warehouses are gaining popularity due to their cost-effectiveness, durability, and versatility, making them an ideal storage solution for businesses. But we get it—when you’re about to invest in such a major project, there’s much to consider. How can you keep costs in check while getting a reliable, high-quality warehouse? What factors really drive the price up?
In this article, we’ll break down 5 key cost-affecting factors and show you how to manage them. We’ll highlight the benefits of choosing steel structure warehouses and introduce you to our solutions that could save you both time and money. Let’s dive straight into the details that matter most!
5 Key Factors That Influence Steel Structure Warehouse Costs
When you’re planning to build a steel structure warehouse, price is often a top concern. The reality is, there are numerous elements that can drive the costs above what you might expect. Understanding what causes these price increases can help you make more informed choices and prevent unexpected expenses later. Let’s explore the main factors that impact the price.
1. Raw Materials
- Steel Prices: Steel makes up 60-70% of the total cost, and its price can swing based on supply and demand. Things like production delays or transport issues can lead to price hikes, which might throw off your budget a bit.
- Material Quality: Opting for higher-quality materials, like stainless steel or galvanized steel, can cost more upfront, but they’ll pay off in the long run by making your warehouse more durable and better able to handle the elements. This means a longer lifespan and fewer maintenance headaches down the road.
2. Factory Design Complexity
- Simple vs. Complex Designs: Simple designs with standard structures are easier on the budget, needing less engineering and labor. For example, we offer prefabricated warehouses with specific lengths, widths, and heights, which streamline the process. But complex designs—like multi-level layouts, custom roofs, or heavy-duty steel frames—can add 15-30% to costs. These projects need more engineering, better materials like galvanized steel, and more time to build, all of which bump up the price.
3. Foundation and Site Conditions
- Foundation System for Steel Structures: Steel buildings typically use reinforced concrete slabs or piles for their foundations. If the soil’s unstable or needs extra work, like deep piling, the foundation costs can go up, depending on how tricky the ground is.
- Site Accessibility: Logistics costs can add up if the site’s tough to get to or has rough terrain. You might need special vehicles or equipment to move materials, which can push your overall expenses higher.
4. Accessories and Customization
- Insulation and Cladding: Steel panels don’t really keep the heat in or out that well. But if you upgrade to better insulation or custom cladding, it’ll make a big difference in comfort—keeping things cozy in winter and cool in summer. Yes, it costs a bit more, but it can really help lower energy bills in the long run.
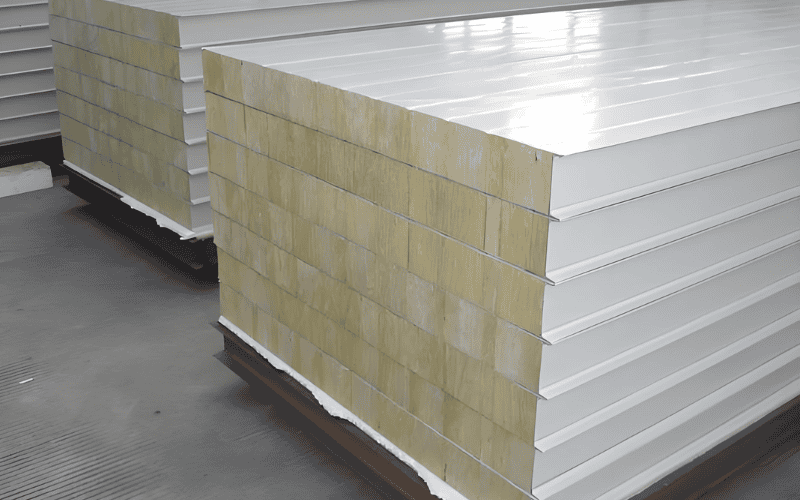
- Smart Features: Adding smart tech like climate control, automated lighting, or advanced security systems might bump up your costs at first, but these systems can save you money over time by boosting efficiency and cutting down on energy usage.
5. Permitting and Regulatory Compliance
- Permits and Zoning: Permit fees can range from $1,000 to $10,000, and delays can increase costs. We’re here to help by preparing the right documents to meet local regulations and speed up the approval process.
- Sustainability Standards: If you’re aiming for LEED or other certifications, there might be extra costs. We can support you with eco-friendly designs and energy-efficient materials to meet these goals and save in the long run.
By understanding these cost factors, you’ll be in a better position to manage your project’s budget while ensuring long-term value and durability for your warehouse.
How to Control Steel Structure Warehouse Construction Costs
Building a steel structure warehouse is a big investment, but you can definitely keep costs in check with the right approach. Here’s how:
Plan Your Budget Early
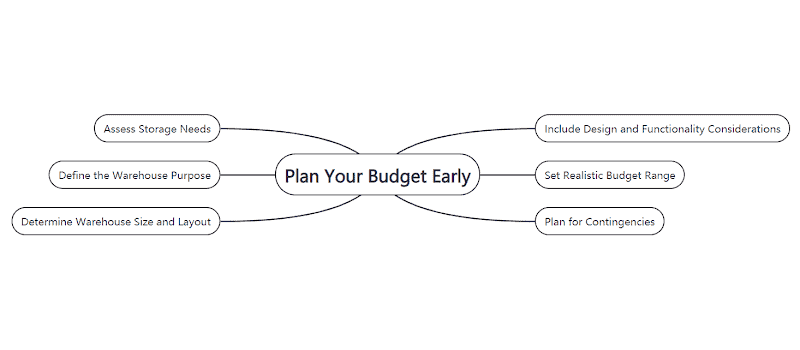
Start by assessing your storage needs, the warehouse’s purpose, size, and functionality. Setting a clear budget range at this stage is crucial to guide your decisions moving forward. Here’s a step-by-step process to make sure you cover all the key aspects when planning your budget:
- Assess Storage Needs:
- What kind of goods will you store? (e.g., perishable goods, heavy machinery, or retail products)
- Do you need specific temperature or humidity control?
- Will you need space for machinery or equipment?
- Define the Warehouse Purpose:
- Is the warehouse for long-term storage, manufacturing, or distribution?
- Will there be high traffic or multiple shifts working in the warehouse?
- Determine Warehouse Size and Layout:
- Estimate how much space you need (square footage).
- Consider the layout: Will you need wide aisles for forklift access or multiple levels for storage?
- Include Design and Functionality Considerations:
- Are there any custom features you need, such as reinforced flooring or special storage racks?
- Would you benefit from energy-efficient features like natural lighting, insulation, or solar panels?
- Set Realistic Budget Range:
- Include costs for materials, construction, and any custom requirements.
- Consider additional costs like permits, inspections, and possible site preparation.
- Plan for Contingencies:
- Allocate a portion of your budget (typically 5-10%) for unforeseen expenses or adjustments in the project’s scope.
Planning early with this structured approach can ensure that your budget is realistic, and it helps you avoid unexpected costs down the road.
By carefully considering these factors, you can make more informed decisions and stay within your budget from start to finish.
Efficient Design
Going for prefabricated components can save you up to 40% in construction time, which means lower labor and material costs. We’ll help you optimize the layout to reduce unnecessary space and complexity, keeping things budget-friendly.
Benefits of Choosing Steel Structure Warehouses
Steel structure warehouses are the top choice for businesses seeking cost-effective, reliable storage. Steel structures offer advantages that save time, money, and hassle.
Lower Maintenance Costs
Steel warehouses are low-maintenance. Steel resists rust, warping, and pests, so you won’t need to worry about repairs as often.
Energy Efficiency
Modern steel buildings use insulation materials and natural light design to help reduce energy costs, sometimes saving up to 30%.
Recycling and Reusability
Steel’s recyclable, so when you’re done with the building, it can be reused, helping to offset part of your initial costs and keep things eco-friendly.
Increased Storage Efficiency
Steel designs let you maximize your space. Our large-span steel warehouses give you more room without support columns, so you get better storage access.
Scalability and Flexibility
ouses are easy to expand or adjust as your needs change—perfect for business use.
Faster Construction Timeline
Steel warehouses go up fast. With prefabricated components, you can cut construction time by 40%, so you’ll be using your warehouse sooner!
Related Reading: Advantages of industrial warehouse buildings
Why Choose Us for Your Steel Structure Warehouse?
We’re a direct manufacturer with our own steel mill, so we offer competitive prices on peb structure steel warehouses and more. From planning to building, we manage all aspects to ensure your project stays on schedule and within budget. Whether it’s a steel warehouse with solar energy or a clear-span steel warehouses design, our flexible solutions are built to last, making them perfect for businesses.
Frequently Asked Questions
Why Do Steel Structures Have High Maintenance Costs?
Steel structures generally have low maintenance costs due to their durability, but if not properly coated or if exposed to harsh conditions, rust and corrosion can increase long-term upkeep.
Is the Initial Cost of a Steel Structure Warehouse Higher Than Other Types of Warehouses?
The initial cost can be higher than traditional buildings, but the savings in construction time, labor costs, and long-term maintenance usually offset the investment.
Will Choosing a Pre-engineered Steel Structure Warehouse Save Me Money?
Yes, opting for pre-engineered steel structures can save you money on both materials and labor, as they are faster to assemble and often require less customization compared to fully custom designs.