Choosing the right hay storage building is critical to farm operations, not only for the quality of the hay, but also for long-term cost-effectiveness. There are many factors involved in planning and building a hay storage building, from size and design to climate and regulatory requirements, every detail needs to be carefully considered.
We will take a deep dive into the key factors to consider when choosing a hay storage building to help you make the most appropriate decision and ensure the long-term value of your investment.
Main Types of Hay Storage Buildings
There are several options for hay storage buildings, each suitable for different needs and budgets. Here are some common types of hay storage buildings with their pros and cons:
Steel Buildings
Advantages:
- Durability: Steel structures are highly resistant to wind, snow, and fire, and can withstand harsh weather conditions.
- Low Maintenance Costs: Unlike wood, steel is less prone to moisture, corrosion, or pest damage, reducing maintenance costs.
- Quick Construction: Prefabricated components of steel structures can be quickly assembled, reducing construction time.
Disadvantages:
- Higher Initial Cost: Steel buildings generally require a higher upfront investment compared to wood structures.
- Thermal Expansion: While steel is strong, temperature fluctuations can affect the internal temperature and humidity control of the building.
Recommendation: Ideal for long-term investment, especially for farms that need high durability and low maintenance costs. Steel buildings are perfect for hay storage, particularly in harsh climates.
Wood Frame Buildings
Advantages:
- Lower Initial Cost: Wood frame buildings typically have a lower upfront cost compared to steel structures, making them more suitable for farms with limited budgets.
- Aesthetic Appeal: Wood structures offer a natural, rustic look, ideal for farms that prioritize the appearance of their buildings.
Disadvantages:
- High Maintenance: Wood is prone to rot, moisture damage, and pest infestations, which require regular maintenance and protection.
- Susceptible to Weather: Wood structures are less durable than steel, particularly in extreme weather conditions like wind or snow.
Recommendation: Suitable for farms with a limited budget and mild climate. If maintenance is not an issue and the natural look is important, wood frame buildings are a good choice.
Pole Barns
Advantages:
- Simple Structure: Pole barns are known for their simple design and quick construction, making them ideal for large-scale hay storage.
- Good Ventilation: Pole barns usually provide excellent airflow, which helps keep hay dry.
- Highly Flexible: The design and size can be tailored to meet the specific requirements of the farm.
Disadvantages:
- Moderate Durability: While effective for hay storage, pole barns are not as durable as steel structures, especially in humid regions.
- Potential Maintenance: Wooden posts and other wood components may suffer from moisture damage, requiring regular checks and treatment.
Recommendation: Ideal for farms that need large space for hay storage and have a limited budget. If the local climate is not excessively humid, pole barns provide an economical and practical solution.
Fabric Buildings
Advantages:
- Lower Cost: Fabric buildings are generally less expensive than steel structures.
- Mobility: These structures are versatile and can be relocated or expanded according to requirements.
- Quick Construction: Fabric buildings are fast to build and can typically be completed in a short time.
Disadvantages:
- Poor Durability: Fabric materials are less durable than steel and are more vulnerable to weather and external conditions.
- Poor Insulation: Fabric structures perform poorly in extreme temperatures, making them unsuitable for very cold or hot climates.
Recommendation: Suitable for farms on a budget that don’t require high durability and need a quick, movable building.
The best building for hay storage depends on various factors, including budget, climate, maintenance needs, and intended use. If you’re in a region with harsh climates and want to minimize maintenance, a steel building is the best option. For those with limited budgets, wood frame or pole barns may be more suitable. If flexibility and fast construction are essential, a fabric building is also worth considering.
What is the best building for storing hay?
The best building for storing hay is typically a steel building due to its durability, low maintenance, and resistance to weather conditions. However, if budget is a concern, a pole barn can also be a good choice, offering a balance of cost and functionality.
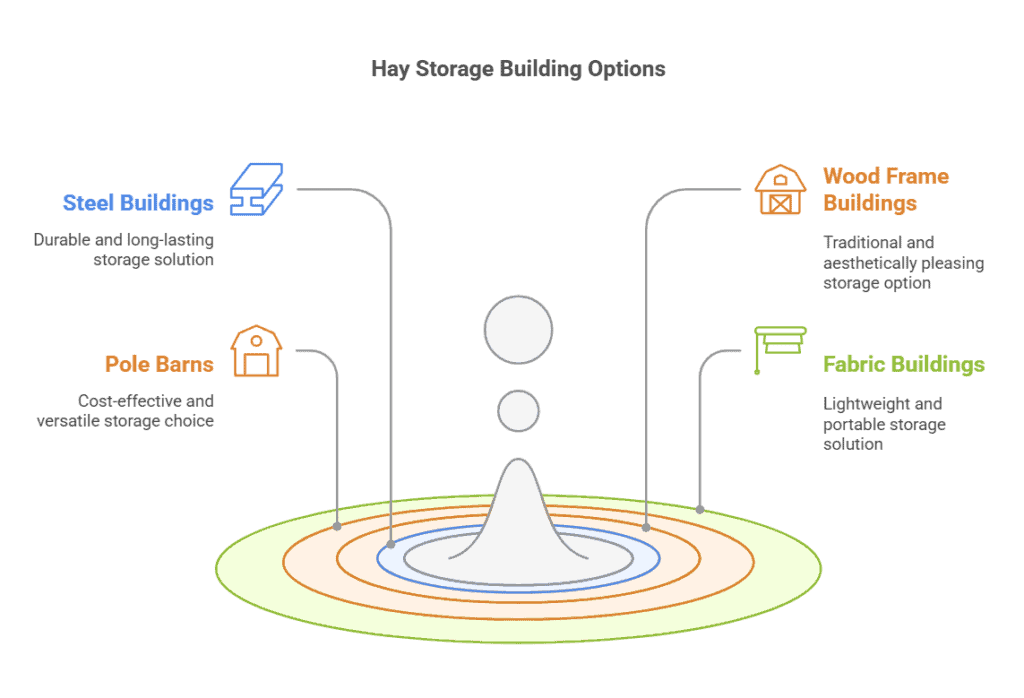
Key Factors to Consider When Choosing a Hay Storage Building
A. Size and Capacity
- Storage Needs: The storage capacity should match your hay production and livestock requirements. Estimate the amount of hay you produce annually and ensure the building can accommodate it, considering the type of bales (round or square) you’ll store.
- Future Expansion: Plan for future growth. Your storage needs will likely increase as your farm expands, so it’s wise to design the space with the potential for future expansion.
- Height and Width: Sufficient ceiling height and width are necessary for easy stacking and movement of hay. This guarantees optimal space utilization and facilitates easier accessibility.
B. Location and Climate
- Site Preparation: Prepare the site by leveling the land and ensuring a stable foundation. This will prevent future structural issues and ensure stable storage conditions.
- Climate: Choose a building design that suits your climate. In areas with high humidity or extreme temperatures, ensure the structure has proper insulation and ventilation to protect the hay from moisture and mold.
- Building Location: Locate the building near your hay production area to reduce transportation time. Avoid areas that are low-lying and susceptible to flooding to prevent water damage to both the hay and the structure.
C. Building Design and Features
- Roof Style:
The roof style plays a significant role in hay storage. A gable roof offers sufficient ventilation space, making it ideal for regions with high rainfall or snowfall. The monitor roof, with its raised central section, allows for better airflow and is ideal for larger buildings. Both styles aid in minimizing moisture accumulation inside, which is essential for the preservation of hay. - Sidewall Height:
Adequate sidewall height is essential for efficient stacking and easy access for equipment. Taller walls provide more storage capacity and flexibility when stacking hay bales, ensuring you maximize the available space without difficulty. - Doors and Access:
The type and placement of doors are crucial for the smooth loading and unloading of hay. Sliding doors or overhead doors allow for wide openings and easy movement of bales, reducing the effort required during daily operations. Proper placement of doors should facilitate access to both the interior and exterior of the building. - Flooring Options:
The selection of flooring impacts the simplicity of maintenance and the overall wellbeing of the stored hay. Gravel offers superior drainage, ensuring the base remains dry, albeit it may necessitate frequent upkeep. Concrete floors, on the other hand, are durable and easy to clean, but they may not allow for quick drainage if not properly sloped.
D. Material and Durability
- High-Quality Materials:
Using high-quality materials in construction ensures the long-term performance and durability of the building. Choosing materials that are weather-resistant, durable, and low-maintenance will reduce ongoing costs and extend the life of your storage building. - Steel vs. Wood:
Steel structures are typically more durable and require less maintenance than wooden structures, which may have a lower initial cost but require regular maintenance to prevent rot, pests, and weather-related damage. Steel provides exceptional durability against the elements, rendering it a more favorable long-term investment, particularly for farms situated in severe climates. - Roof Materials:
For roofing, opt for waterproof and insulated materials such as metal roofing or premium asphalt shingles. These materials help prevent moisture infiltration and temperature fluctuations inside the building, maintaining a dry and consistent environment for hay storage.
E. Construction Time and Cost
- Initial Investment vs. Long-Term Savings:
Although steel buildings typically have a higher initial investment compared to wood or fabric buildings, they offer significant long-term savings due to their low maintenance and durability. Steel structures are more resistant to weather damage, reducing the need for frequent repairs and upkeep, which ultimately saves money over time. - Factors Affecting Cost:
The price of a hay storage building fluctuates based on several factors:- Size: Larger buildings necessitate more materials and labor, thereby elevating costs.
- Features: Special features such as insulation, advanced ventilation systems, and custom doors or windows can add to the overall cost.
- Customization: Custom-built buildings tailored to specific needs, such as unique roof styles or specialized equipment access, often come at a higher price point.
- Exploring Financing Options:
Financing options, such as loans or grants, can help manage the upfront cost of construction. Many financial institutions offer specific loans for agricultural projects, while government programs may provide grants or low-interest loans for building or improving farm infrastructure. - Considering Construction Time and Potential Downtime:
Construction time can affect the operational schedule of the farm. For steel buildings, the construction process is typically faster due to prefabricated components, reducing downtime and allowing for quicker use. It’s essential to consider the time required for foundation work and installation, as delays can impact the farm’s hay production cycle.
F. Regulations and Permits
- Understanding Local Building Codes and Zoning Regulations:
Before beginning construction, it’s crucial to understand your local building codes and zoning regulations. These rules govern the type, size, and location of the structure, and non-compliance can result in fines or costly alterations. Consulting with local authorities or a construction expert can aid in ensuring that the building complies with all legal stipulations. - Obtaining Necessary Permits:
Many regions require specific permits for constructing agricultural buildings. These permits may include zoning, environmental impact assessments, and construction permits. Be sure to obtain the necessary permits before starting construction to avoid delays or potential legal issues down the line.
G. Temporary vs. Permanent Structures
- Evaluating the Need for a Temporary or Permanent Solution:
The choice depends on your farm’s needs, budget, and land. Temporary structures are great for short-term storage, especially if your hay production is seasonal. Permanent structures, however, offer long-term durability and stability, making them ideal for ongoing storage needs. - Pros and Cons:
- Temporary Structures:
Pros: Lower cost, quicker setup, portable.
Cons: Less durable, requires more maintenance, not ideal for long-term use. - Permanent Structures:
Pros: Long-lasting, weather-resistant, lower maintenance.
Cons: Higher upfront cost, less flexibility, longer construction time.
- Temporary Structures:
H. Loading and Unloading
- Designing for Efficient Operations:
The design should allow easy loading and unloading by placing doors and ramps in convenient locations to ensure smooth flow. Proper design reduces delays and improves efficiency during busy seasons. - Access and Maneuverability:
Ensure enough space for equipment like forklifts and tractors to move freely. This is crucial for minimizing bottlenecks and speeding up the process.
I. Ventilation and Humidity Control
- Proper Ventilation:
Good airflow is essential to keep the hay dry and prevent mold. Adequate ventilation allows moisture to escape, maintaining an ideal storage environment. - Humidity and Temperature Monitoring:
Keeping humidity and temperature in check is vital for preserving hay quality. Install sensors to monitor conditions and prevent mold growth. - Drainage and Water Control:
Guarantee adequate drainage surrounding the building to prevent water accumulation. This maintains the hay’s dryness and averts structural deterioration. - Land Slope and Flooding Risks:
Select a location with superior drainage and steer clear of low-lying areas susceptible to flooding. This will protect your building and stored hay from water damage.
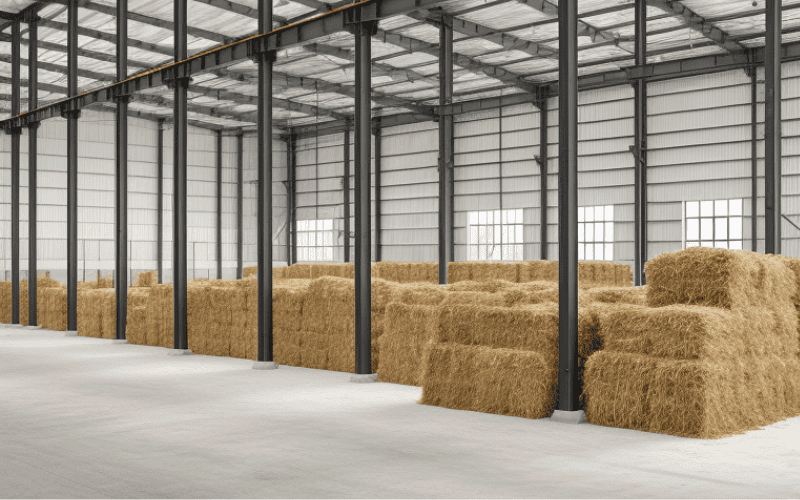
Additional Considerations of Choosing Hay Storage Buildings
- Fire Safety: It is imperative to utilize fire-retardant materials for the building’s structure and adopt appropriate storage procedures to lessen fire hazards. Ensure hay is stored away from heat sources, and keep firefighting equipment accessible.
- Pest Control: To prevent rodent and insect infestations, use pest-proof materials and design features. Performing regular inspections and sealing any openings or cracks in the structure will contribute to maintaining a pest-free atmosphere.
- Insurance: Ensure you possess sufficient insurance protection for your hay storage building. This includes coverage for fire, water damage, and other potential risks that could affect the building or stored hay.
- Disaster-Resistant Design: Take into account the building’s capacity to endure severe weather conditions. Ensure the structure is designed to resist high winds, earthquakes, or other natural disasters, which can protect your hay and building.
- Expansion Space: If you anticipate growing hay production in the future, plan for additional storage capacity. Choose a design that allows for easy expansion, ensuring you can accommodate future needs without a complete rebuild.
- Flexibility: A flexible design can adapt to changing storage requirements. Consider buildings that allow for modifications in size or layout to accommodate varying storage needs over time.
Conclusion
Choosing the right hay storage building is essential to maintaining hay quality and ensuring the long-term sustainability of your farm. By thoroughly contemplating factors including size, location, materials, and climate, you can arrive at an informed decision that best aligns with your requirements.
At SteelPRO PEB, we offer a range of steel structures and custom building solutions designed to meet the specific requirements of hay storage. Whether prioritizing durability, cost-effectiveness, or adaptability, we will assist you in finding the ideal solution for your farm. Reach out to us today to discuss your requirements and embark on your hay storage endeavor.
FAQ
1. What are the factors that affect the quality of hay?
The quality of hay is primarily influenced by the type of grass, harvest time, weather conditions during harvesting, moisture content, and the storage conditions. Drying the hay properly, avoiding exposure to rain, and maintaining a dry, well-ventilated storage space are key to preserving its quality.
2. What are the conditions for hay storage?
Hay ought to be stored in a dry, well-ventilated setting to avert moisture accumulation, mold proliferation, and spontaneous ignition. The storage area should be elevated to avoid water exposure and should provide enough space for proper airflow to keep the hay dry and in good condition.
3. How many years can you store hay?
Hay can be stored for up to one year if properly handled. However, the quality of hay diminishes over time, so it’s best to use hay within a year of harvesting. The storage environment plays a pivotal role in extending its usability.
4. What is a place for storing hay high up?
A high place for storing hay is typically a loft or upper storage area in a barn or shed. These elevated spaces help prevent moisture from accumulating and offer better ventilation. It is crucial to guarantee that the area is readily accessible for loading and unloading operations.