Advantages of Steel Buildings
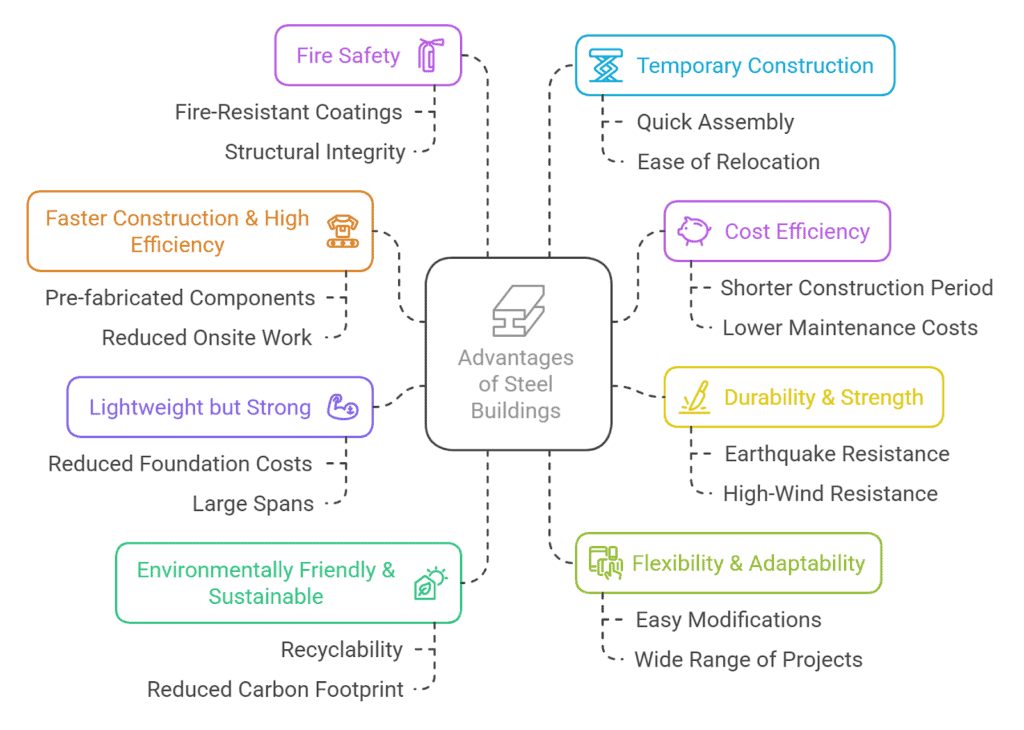
1. Faster Construction & High Efficiency
Steel buildings are known for their quick construction times. Pre-fabricated components are manufactured in factories, reducing onsite work. This streamlines the building process and cuts labor requirements. Compared to concrete structures, steel buildings can save 30-50% of construction time. For large projects, like warehouses, this could mean completing work months earlier.
2. Cost Efficiency
Steel’s initial material cost is higher than concrete or wood. However, the shorter construction period saves labor and project overhead costs. Overall, steel buildings reduce total costs by 15-20%. Maintenance is also cheaper, as steel resists corrosion and extreme weather, saving 10-20% in annual upkeep expenses.
3. Durability & Strength
Steel structures perform well in extreme conditions. They are highly earthquake-resistant due to steel’s flexibility and strength. In high-wind areas, steel’s resistance is 30-40% better than traditional materials. Properly treated, steel can last decades, even in harsh environments.
4. Lightweight but Strong
Steel structures weigh 30-50% less than concrete ones. This reduces foundation costs and structural loads. Steel also supports large spans, making it ideal for wide spaces like stadiums or factories. It can handle spans exceeding 30 meters without needing internal support.
5. Environmentally Friendly & Sustainable
Steel is 100% recyclable. Old steel can be reused without losing strength, reducing construction waste. Globally, the recycling rate for steel is 70-90%. Steel buildings also leave a smaller carbon footprint, cutting lifecycle emissions by 30-40%.
6. Flexibility & Adaptability
Steel structures are easy to modify or expand. Adding floors or altering layouts is simpler and cheaper than with concrete. Steel suits a wide range of projects, from industrial plants to skyscrapers.
7. Fire Safety
Modern steel buildings use fire-resistant coatings to protect against high temperatures. With these measures, steel can maintain structural integrity for 2-3 hours during a fire.
8. Temporary Construction
Steel is also preferred in temporary construction projects, such as military installations, where quick assembly and disassembly are required. These projects benefit from steel’s lightweight nature, fast assembly, and ease of relocation.
Related Reading:
How Long Do Temporary Buildings Last?
Disadvantages of Steel Buildings
1. Higher Initial Cost & Restricted Availability
Steel is more expensive upfront compared to concrete or wood. This can make it less appealing for smaller projects or when budgets are tight. In some countries, steel may not be readily available and can be particularly expensive, which may further discourage its use in certain regions.
2. Fire Vulnerability & Spread
Steel loses strength at high temperatures. While fireproof coatings mitigate this risk, they increase costs. Without these coatings, steel structures are more vulnerable to prolonged fires. Steel is also an excellent conductor of heat, meaning that fire in one part of the building can spread more easily to other sections. This can lead to greater fire damage. Additional insulation and fireproofing measures are necessary to mitigate this issue.
3. Heat Conductivity
Steel conducts heat more than other materials, which can cause temperature swings inside the building. Proper insulation is necessary, but this adds to the cost.
4. Buckling Risk
Steel structures are prone to buckling, especially under compressive loads. Steel columns, due to their slender profile, are particularly vulnerable to buckling, requiring additional reinforcement to prevent failure.
5. Corrosion & Maintenance
Steel is susceptible to corrosion if exposed to air and moisture. Regular maintenance, such as painting, is required to protect steel structures from degradation. If not properly maintained, steel can lose up to 1-1.5 mm of thickness each year, which can eventually lead to failure under load. Some weather-resistant steels can help mitigate this issue, but maintenance costs are still a concern.
Steel Buildings vs. Other Types of Construction
1. Construction Speed and Timeline
- Steel: Fastest construction time. Prefabricated components save 30%-50% of time, typically completed in 6 months.
- Concrete: Longer due to curing time; can take 12 months or more for large projects.
- Wood: Faster than concrete but less efficient for large spans; timeline may approach steel for complex projects.
- Brick: Longest timeline, usually 6 months to 1 year for low-rise buildings.
2. Building Costs
- Steel: Higher upfront cost but 15%-20% savings long-term due to faster construction and lower maintenance.
- Concrete: Lower initial cost but longer construction and higher maintenance, especially for high-rise buildings.
- Wood: Low initial cost but higher long-term maintenance, especially in damp or seismic regions.
- Brick: Low initial cost but slow construction and high labor costs for large projects.
3. Load-Bearing Capacity and Span
- Steel: Superior for large spans, can support over 30m. Ideal for sports arenas, factories, and large spaces.
- Concrete: Good for compression but spans typically limited to 20-25m; requires more support for large buildings.
- Wood: Limited to small spans (5-10m), suitable for low-rise residential.
- Brick: Limited to small spans (4-6m), unsuitable for large or high-rise buildings.
4. Seismic and Safety Performance
- Steel: Excellent seismic performance and wind resistance.
- Concrete: Strong but lacks flexibility, poor seismic performance in active zones.
- Wood: Decent seismic performance for low-rise, poor for tall buildings. Poor wind resistance.
- Brick: Poor seismic performance; generally unsuitable for seismic regions.
5. Durability and Maintenance
- Steel: High durability (50-100 years) with low maintenance (mainly rust/corrosion prevention).
- Concrete: Durable (50-70 years) but requires crack repairs and waterproofing.
- Wood: Shorter lifespan (30-50 years), vulnerable to pests and moisture, requiring frequent maintenance.
- Brick: Durable (50-100 years), low maintenance, but susceptible to water damage and aging.
6. Environmental Impact and Sustainability
- Steel: 100% recyclable, sustainable with high recycling rates. Production is energy-intensive but mitigated by recycling.
- Concrete: High energy consumption and carbon emissions, but design optimizations can reduce waste.
- Wood: Renewable, and environmentally friendly, but harvesting and transportation can have environmental impacts.
- Brick: High energy use and carbon emissions during production; non-recyclable.