Tight deadlines. Unreliable labor. Too many moving parts on-site.
If you’ve faced any of this, modular construction might not just be an option—it might be the smarter path forward. But is it the right fit for your project?
In this guide, we break down what modular really looks like in practice—how it works, when it works best, and what to know before you commit. Straight answers, based on real experience—not marketing fluff.
Qué esperar en este blog:
What Exactly Is Modular Construction Technology?
Modular construction is a building method where structures are built off-site in sections—called modules—and then transported to the final location for assembly. These modules are made in a factory setting, often with better control over quality, materials, and timelines.
For construction professionals like you, this means less on-site work, fewer delays, and more predictable results. Unlike traditional construction, where everything happens at the job site, modular shifts a big part of the process into a controlled environment.
At the core of modular construction is precision and repeatability. Each module is designed to fit perfectly with others, like a puzzle. And because of this, the planning and engineering stages are critical.
Steel structures play a major role here. Why? Because steel offers strength, stability, and flexibility—three things modular buildings rely on. It’s also easier to pre-engineer steel frames, which shortens design cycles and speeds up production.
If you’re used to conventional building methods, modular might seem like a big shift. But in reality, it’s just a smarter, more streamlined way to get buildings up and running faster—with less risk along the way.
Why Are Developers and Contractors Turning to Modular?
Over the past few years, modular construction has shifted from niche to mainstream. Developers, contractors, and project owners are now looking beyond traditional methods—and for good reason.
Rising labor costs, tighter timelines, and increasing demand for precision have pushed the industry to rethink how buildings are delivered. Modular offers a way to meet these pressures without sacrificing quality.
Here’s what’s driving the shift:
- Faster project delivery
Modules are built off-site while site work happens in parallel. That can cut your timeline by 30–50%. - More control, less risk
Factory production means fewer surprises on-site. Weather delays? Labor shortages? Far less of an issue. - Cost predictability
Clearer pricing from the start, less material waste, and fewer change orders. - Better quality assurance
Repeated processes in a controlled environment lead to consistent results—and fewer reworks. - Increased flexibility in design
Modular doesn’t mean boring. With steel framing, you can still achieve open spans, modern layouts, and custom finishes.
In short, modular isn’t just a cost-saving method—it’s a risk management strategy. If you’re working in a market where speed and certainty matter, it might be time to take a closer look.
How Does the Modular Construction Process Work?
Think of modular construction as a parallel workflow. While your site is being prepared, your building is already being built—somewhere else. That’s the core advantage: speed without compromise.
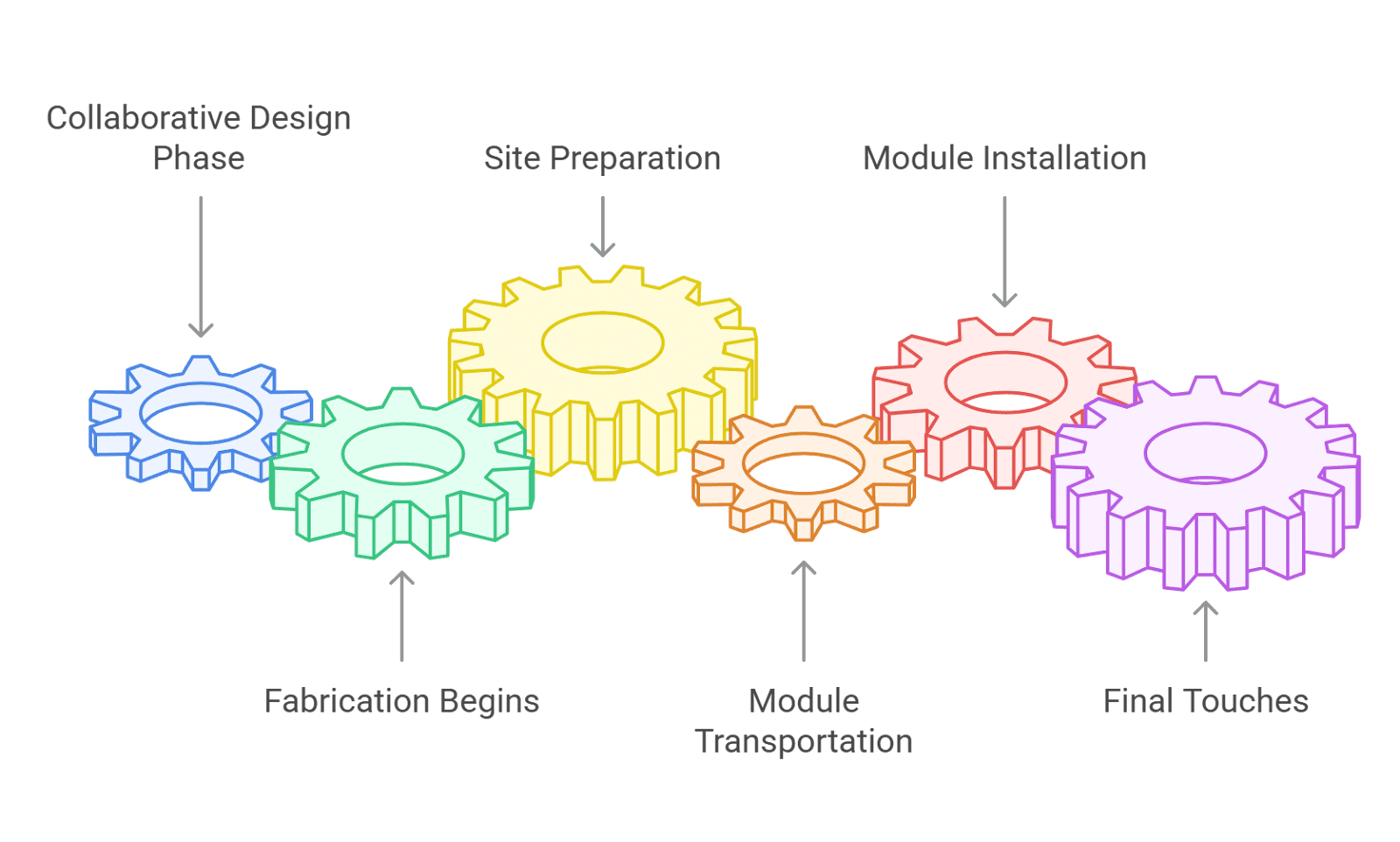
The process usually starts with a collaborative design phase. Here, we work closely with your team to finalize the layout, structural needs, and finishing specs. Unlike traditional projects where decisions get pushed to later stages, modular requires clarity up front—but that pays off later in speed and accuracy.
Once design is locked, fabrication begins in a controlled factory setting. Each module is built according to engineered drawings, using steel structures that ensure precision and strength. Quality checks are embedded at every step, from welding to finishing.
Meanwhile, on your site, foundations are prepared in parallel. No waiting. When the modules are ready, they’re transported to the site and installed using cranes—often in just a few days. Connections are sealed, utilities are linked, and final touches are completed on-site.
Throughout this process, SteelPRO PEB serves as your engineering and production partner. We don’t just deliver modules—we deliver predictable results. You’ll always know what’s happening, when, and why.
By the time your competitors are still pouring concrete, you could be handing over keys.
What Are the Practical Benefits for Project Owners and Contractors?
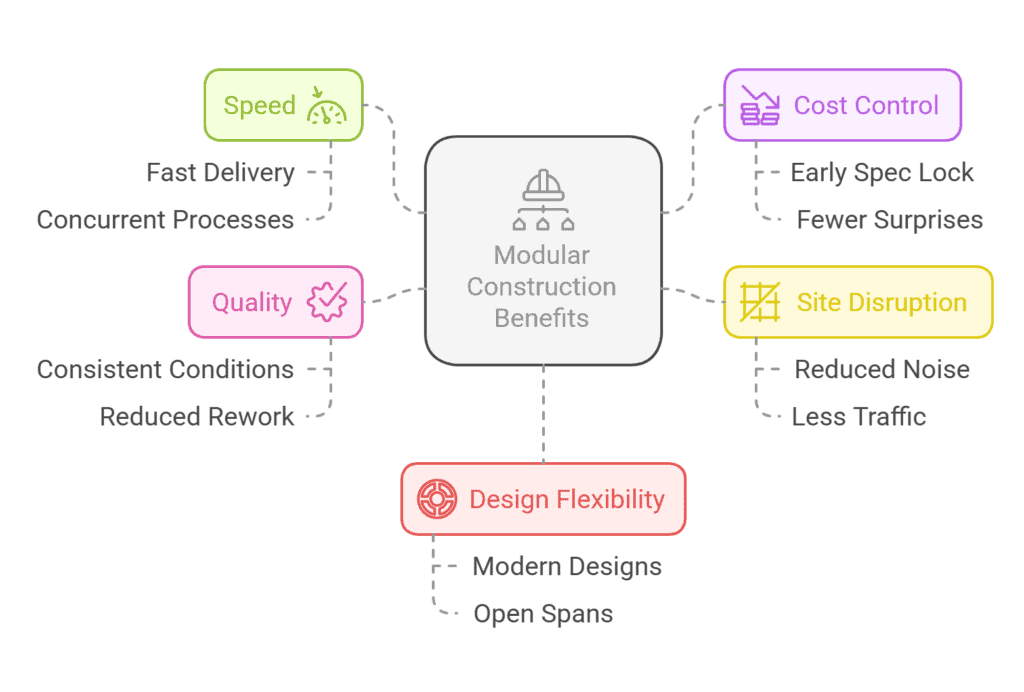
Speed That Matches the Market
If you’re working against tight deadlines—whether to meet a lease agreement, investor demand, or operational target—modular gives you a real edge. Because fabrication happens off-site while groundwork moves forward on-site, delivery can be up to 50% faster than conventional methods.
Clarity and Cost Control from Day One
You know how often budgets spiral when site conditions change or materials run late. With modular, you lock in your specs early, and most of the work happens in a factory with known inputs. That means fewer surprises, tighter cost control, and more predictable scheduling.
Reduced Site Disruption
Construction sites can be noisy, dirty, and disruptive—especially in urban or active-use environments. Since modular reduces on-site activity, you cut down on noise, traffic, and safety concerns. It’s a cleaner, quieter way to build.
Higher Consistency, Lower Rework
In traditional builds, quality depends heavily on day-to-day site labor and weather. Modular buildings are fabricated under consistent conditions, with repetitive processes and built-in QC. That reduces rework and defects—and increases handover confidence.
Design Freedom with Structural Discipline
Worried that modular means “boxy”? Think again. With steel frames, you’re not locked into cookie-cutter layouts. You can integrate modern designs, open spans, and premium finishes—without sacrificing the efficiency modular offers.
Is Modular Construction Always the Right Fit?
Modular construction offers a lot—but it’s not the answer to every project.
In reality, it’s not about whether modular works. It’s about where it works best. The method itself is highly efficient, but like any building approach, it needs the right conditions to deliver full value.
Modular performs best when a project has clear planning parameters. If your timeline is tight, your design is relatively fixed, and site access is predictable, modular can dramatically reduce complexity and delivery time. It’s also ideal when repeatable layouts are involved—like classrooms, dormitories, or office units.
On the other hand, if your project is still in flux—designs changing frequently, approvals pending, or scope unclear—modular might not give you the flexibility you need. Likewise, sites with extreme logistical constraints or highly customized one-off structures may be better served by traditional builds or hybrid models.
The key is to align your project’s needs with the method’s strengths. That’s where experience matters. At SteelPRO PEB, we help clients assess feasibility early—before any design dollars are committed. If it’s a good fit, we’ll show you the roadmap. If it’s not, we’ll tell you that too.
How a Modular Steel Building Comes Together—A Real Project Example
Here’s a real-world example from one of our clients in Southeast Asia.
They needed a 1,000 m² administrative building adjacent to their logistics hub—with a six-month operational deadline. Traditional construction in their region would have taken nearly double the time. They chose modular steel construction to meet both speed and cost targets.
From our side in China, we handled the full design, steel structure fabrication, and module production. Each module was engineered with precise dimensions, pre-installed with electrical routing and mechanical allowances, then packed for sea shipment. Modules were either loaded into standard containers or flat racks, depending on size and transport route.
While production was underway, the client prepared their site locally and arranged their own installation crew. We provided full technical documentation—including lifting points, installation sequencing, utility interface maps, and joint connection drawings—to support on-site assembly.
Delivery took approximately four weeks by sea. Once the shipment arrived, the local team completed installation in just over two weeks, with remote coordination support from our engineering team when needed.
Was everything plug-and-play? Not entirely—but the structure went up smoothly, and more importantly, without surprises. That’s what happens when modular design, factory control, and proper coordination come together.
With the right planning and a reliable partner, modular isn’t just faster—it’s smarter.
What Should You Consider Before Moving Forward?
If you’re seriously thinking about modular construction, you’re already ahead of the curve. But before jumping in, it’s worth pausing to make sure the approach truly aligns with your project’s needs—and your team’s capabilities.
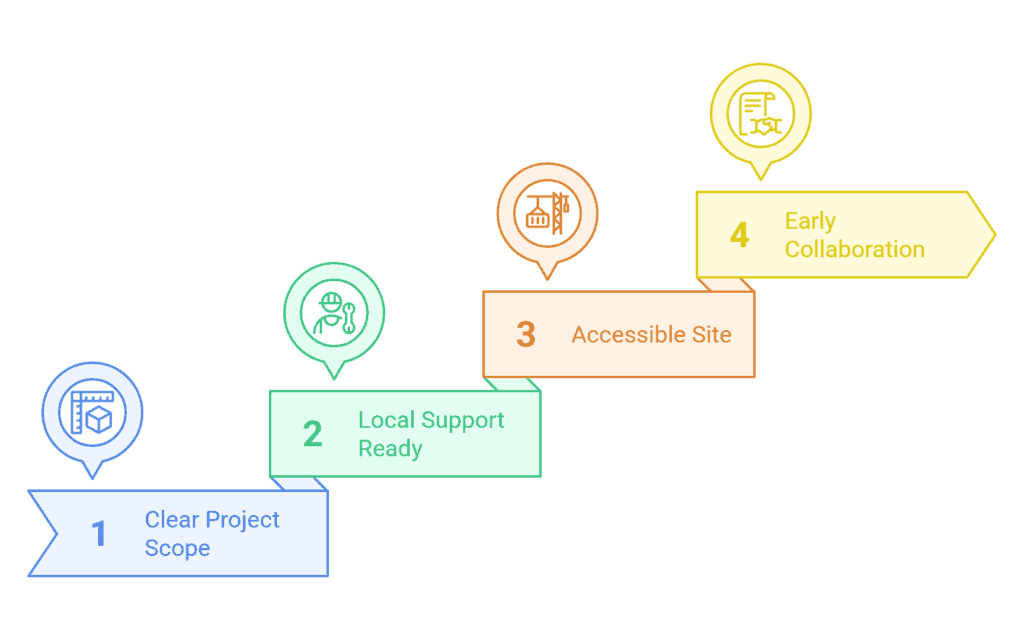
Is your project scope clear enough?
Modular thrives on early clarity. If your design is still changing every week, or your approvals are months away, the benefits of factory production may be harder to realize. A fixed layout and locked-in specs help unlock modular’s true speed advantage.
Do you have local installation support ready?
Since we deliver pre-fabricated modules, on-site assembly is handled by your local contractors. That part of the process needs planning: lifting equipment, interface coordination, and experienced crews. We’ll provide technical drawings and remote support—and when needed, we can also dispatch a qualified engineer to your site to assist with supervision and coordination during installation. But someone on your end needs to make it happen.
Is your site accessible for modular delivery?
Modules are large, often loaded in flat racks or high-cube containers. Your site must be able to receive and handle them—crane access, staging space, and road conditions all matter more than in conventional builds.
Are you ready for a different kind of collaboration?
Modular is fast—but it asks for more input up front. You’ll need to make key decisions earlier than you might be used to. That means involving your design team, contractors, and procurement partners sooner rather than later.
None of these are blockers. But understanding them early is the difference between a smooth modular build—and a frustrating one.
And if you’re not sure about any of the above, that’s okay. It’s what we’re here for.
Ready to See If Modular Is Right for Your Project?
Hablemos.
Whether you’re planning your first modular build or looking to optimize a current one, the earlier we connect, the more value we can add. Share your basic project details—we’ll assess feasibility, flag risks, and show you what’s possible.
No guesswork. No pressure. Just straight answers from engineers who’ve done it before.
Send us your project brief and get a free preliminary assessment—typically within 24 hours.
→ Start the conversation today.