The global B2B supply chain is under more pressure than ever. Events like pandemics, wars, and extreme weather have revealed how fragile traditional manufacturing systems can be.
You might be wondering — is there a smarter, more flexible way to build and deliver products? Companies like yours are facing rising costs, unpredictable demand, and ongoing delivery delays. It’s clear: the standard way of doing things no longer works.
In this article, we introduce modular manufacturing—a modern approach reshaping global industry. You’ll discover what it is, how it compares to traditional methods, and how it can improve your supply chain. From benefits to challenges, this guide will help you decide if modular manufacturing is right for your business.
What is Modular Manufacturing?
Modular manufacturing is a production strategy that breaks down complex products into smaller, standardized modules. These modules are designed to be produced independently and then assembled together, creating a complete system. This approach is fundamentally different from traditional integrated or linear manufacturing, where the product is built as a whole from start to finish in sequence.
The core idea behind modular manufacturing lies in standardization and parallel production. Each module follows a predefined set of design rules and interface standards, which means different teams, or even different factories, can work on various modules at the same time. By doing so, companies can significantly reduce production time, mitigate supply chain risks, and simplify product upgrades or customization.
Think of modular manufacturing as assembling a puzzle, where each piece is crafted separately but designed to fit perfectly within the big picture. For B2B industries, especially those dealing with complex or high-value products, this concept is revolutionizing how production and logistics are managed.
You’ll commonly find modular manufacturing in:
- Automotive industry (e.g., engine modules, dashboard systems)
- Consumer electronics (e.g., smartphones with replaceable units)
- Industrial equipment (e.g., conveyor systems and modular machining cells)
Understanding how modular manufacturing works is key to recognizing its value. It provides not only efficiency, but also more flexibility in meeting changing customer needs and scaling product variations. At SteelPRO Peb, we are passionate about applying this approach to create optimized, cost-effective, and customizable industrial steel solutions for clients worldwide.
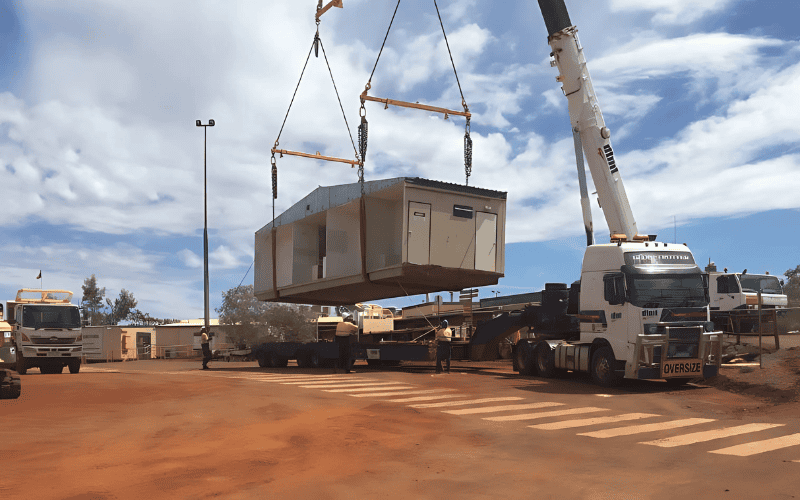
Modular Manufacturing Process
The modular manufacturing process involves creating standardized modules in a controlled environment, which are then assembled on-site or integrated into final products. This approach enhances efficiency, reduces costs, and improves flexibility. Key steps include:
- Design and Standardization: Standardized modules are designed for easy integration and consistent quality across products or projects. Flexible configurations are created while maintaining interoperability and scalability.
- Pre-fabrication: Modules are pre-fabricated in a factory setting using automated processes and skilled labor. Components like walls, engines, or circuit boards are built to precise standards, ensuring better control over production quality.
- Conjunto de componentes: Pre-fabricated modules are assembled into larger subassemblies or final products. The standardized nature of the modules simplifies final assembly, reducing errors.
- Control de calidad: Modules undergo strict quality checks for structural integrity, functionality, and performance, ensuring consistent and reliable results due to the controlled environment.
- Transport and Delivery: After assembly, completed modules are transported to the final site or customer location. In industries like construction, pre-fabricated modules are quickly assembled on-site, shortening project timelines.
- Final Integration and Customization: Modules are integrated into larger systems at the final site, with customization based on client needs. In construction, modules are placed together to form buildings; in automotive, modules are installed into vehicles.
- Ongoing Maintenance and Upgrades: Modular manufacturing allows easy maintenance and upgrades since individual modules can be replaced or updated without affecting the entire system, particularly beneficial in industries like medical devices or electronics.
This process offers improved efficiency, cost savings, scalability, and faster time-to-market, making it ideal for industries such as construction, automotive, electronics, medical devices, and aerospace.
Current Challenges in B2B Supply Chains
B2B supply chains have faced increasing pressures in recent years due to global trade complexity and unexpected disruptions, exposing vulnerabilities in traditional manufacturing and logistics systems.
Global Supply Chain Disruptions: Events like COVID-19, geopolitical tensions, and extreme weather have caused delays and production halts, impacting businesses worldwide.
Demand Unpredictability: Market volatility, shifting customer expectations, and rapid technological changes make it challenging for businesses to align production with demand, leading to excess inventory or stockouts.
Rising Costs: The surge in raw material (e.g., steel, aluminum) and logistics costs (fuel, freight) pressures margins, with smaller businesses particularly vulnerable due to limited bargaining power.
As companies seek greater resilience, new models like modular manufacturing are gaining traction to create more efficient supply chains.
What are the benefits of modular manufacturing?
Modular manufacturing isn’t just a trend—it’s transforming the way B2B supply chains function across industries. By allowing manufacturers to break down products into standardized, interchangeable modules, companies can unlock significant operational advantages.
Let’s look at how modular manufacturing improves efficiency across core supply chain dimensions:
1. Enhanced Product Flexibility to Meet Market Demands
In traditional manufacturing, responding to new customer needs or market changes often means a complete redesign. Modular approaches change that dynamic. When product components are modularized, it becomes much easier to swap or upgrade parts without overhauling the entire product. For B2B buyers, this means suppliers can quickly customize solutions without long lead times.
2. Reduced R&D and Production Costs
Modular systems allow companies to reuse tested components across different products. This minimizes time spent on design and development while also reducing error risks during production. With economies of scale on commonly used modules, businesses can lower their cost per unit and improve overall product profitability.
3. Accelerated Production Timelines through Parallel Manufacturing
By separating a product into independent modules, manufacturers enable different teams or facilities to produce parts simultaneously. Unlike linear production, parallel workflows drastically reduce time-to-market—an advantage in fast-moving B2B environments where being first can mean winning the deal.
4. Better Collaboration Through Standardization
Modular manufacturing encourages the development of unified internal standards. This facilitates smoother collaboration between departments, making project handovers simpler and reducing inefficiencies. Externally, it also simplifies downstream integration with supply chain partners, such as assemblers or service providers.
5. Support for Distributed Manufacturing Models
Geopolitical instability, natural disasters, and logistical bottlenecks can disrupt centralized production. Modular manufacturing enables distributed production, where modules can be built in different locations and assembled closer to end markets. This lowers transportation risks and ensures business continuity even under unpredictable conditions.
Companies like SteelPRO Peb are leveraging this modular advantage to deliver high-quality, customizable steel structure solutions to international clients. With scalable modular systems and global delivery capabilities, we’re minimizing complexity and maximizing responsiveness for our partners worldwide.
Lectura relacionada: Beneficios de la construcción modular
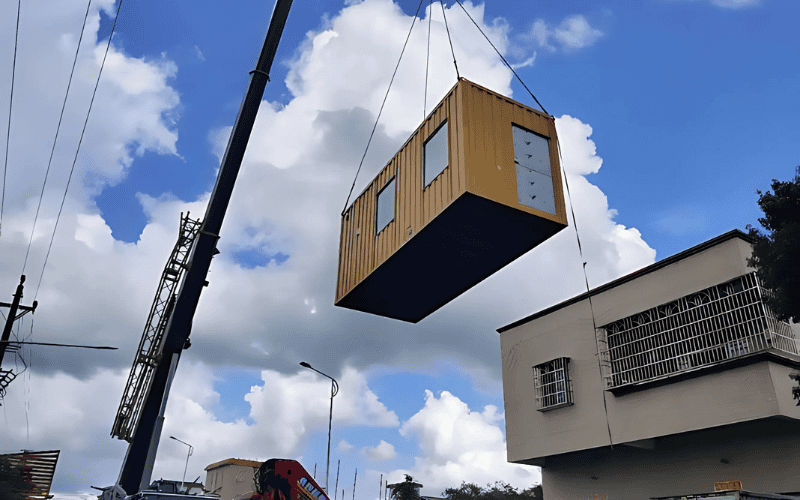
Challenges to Consider When Implementing Modular Manufacturing
While modular manufacturing offers agility and efficiency, its adoption comes with several challenges. Understanding these potential roadblocks is essential for successful implementation.
High Upfront Design Investment
Creating standardized, interoperable modules requires significant engineering and system-level thinking. The initial phase of developing modular products often demands more time and resources compared to traditional manufacturing, as companies must redesign product lines and restructure workflows to accommodate modularity.
Supply Chain Ecosystem Pressures
Modular manufacturing requires tight integration across the supply chain. Each module must be compatible with others, demanding closer collaboration with both upstream suppliers and downstream partners. Without consistent standards and shared protocols, modules can become bottlenecks rather than accelerate production.
Internal Cultural and Procedural Shifts
Adopting modular manufacturing requires cultural and procedural transformations within the company. Transitioning from traditional methods to modular approaches demands change management at all levels, including employee training and greater cross-functional collaboration. Resistance to change can slow progress if internal teams are unprepared for the shift in mindset.
Ultimately, moving to modular manufacturing involves more than process redesigns—it requires strategic foresight, effective stakeholder coordination, and a company-wide commitment to innovation. While the rewards are significant, businesses must be aware of the challenges and plan accordingly.
Which industry is modular manufacturing suitable for?
Application of Modular Manufacturing in the Construction Industry
Modular manufacturing is widely used in the construction industry, including residential, commercial buildings, education and medical facilities.
- Residential construction is a core application of modular manufacturing. By prefabricating modules such as walls, roofs and floors in factories and transporting them to the site for assembly, developers can quickly build affordable housing, apartments and single-family homes.
- In commercial construction, modular design is used in office buildings, hotels and shopping malls. On-site construction is simple and efficient, and buildings can be completed quickly to meet the needs of rapidly growing commercial projects.
- Educational facilities such as schools and university dormitories are also built modularly, especially for projects that require rapid expansion or temporary construction. Modular design enables schools to quickly build classrooms, laboratories and dormitories to solve the problem of limited educational resources.
- In the medical field, modular manufacturing helps to quickly build hospitals and clinics, especially in areas with limited medical resources. Hospitals can flexibly expand departments and wards as needed.
In addition, modular construction is also used in public facilities such as community centers, libraries, police stations and fire stations to ensure fast delivery and efficient construction.
Modular Manufacturing Applications in Other Industries
En el automotive industry, modular design breaks vehicles into standardized modules (e.g., chassis, body, engine) that can be produced in parallel, reducing assembly time and improving efficiency.
En electronics manufacturing, modular design allows products like smartphones and home appliances to quickly adapt to market demand. Standardizing components such as displays, processors, and cameras enables personalized options while simplifying production and reducing costs.
El medical device industry uses modular design in products like CT scanners and X-ray machines. Standardizing modules (e.g., electrical systems, displays, sensors) shortens production cycles, improves quality control, and simplifies maintenance and upgrades.
En el aerospace industry, modular design is applied to aircraft and satellite manufacturing, where components like fuselages, wings, and engines are pre-produced and assembled on-site. This speeds up production, reduces costs, and enhances flexibility, making repairs easier.
Modular manufacturing isn’t just a new technique—it’s a smarter way to build resilient, flexible supply chains.
At SteelPRO Peb, we’re ready to help you turn these ideas into results. If you’re looking to simplify operations, improve delivery times, and reduce costs, contact us. Let’s build something stronger, together.