Los edificios agrícolas son un pilar importante de la producción agraria. Proporcionan cobijo al ganado, los cultivos y los equipos. Sin embargo, estas estructuras de acero se desgastan gradualmente debido al viento, el sol, la lluvia e incluso las colisiones con las actividades de los animales. Si se descuida el mantenimiento, los pequeños problemas pueden convertirse en elevadas facturas de reparación e incluso poner en peligro la seguridad del personal y los bienes.
Afortunadamente, mediante un mantenimiento regular y unas reparaciones a tiempo, podemos prolongar eficazmente la vida útil de los edificios de la granja y garantizar una producción agrícola segura y eficiente. Este artículo le proporcionará consejos prácticos detallados para el mantenimiento y la reparación de edificios agrícolas, para que sus edificios agrícolas sean siempre fiables y nuevos.
Tareas rutinarias de mantenimiento: Cuatro pasos clave para prolongar la vida útil de los edificios agrícolas
Para mantener los edificios de su granja en plena forma, el mantenimiento rutinario es fundamental. He aquí algunas tareas sencillas pero esenciales que pueden ayudarle a identificar y abordar los problemas a tiempo, evitando que los pequeños problemas se conviertan en grandes quebraderos de cabeza.
Inspección y limpieza
Las inspecciones periódicas son el primer paso en el mantenimiento. Hay que comprobar cuidadosamente el tejado, las paredes y las puertas y ventanas para detectar cualquier signo de daño o holgura. Por ejemplo, ¿hay grietas u óxido en los paneles del tejado? ¿Hay abolladuras o corrosión en las paredes? ¿Se abren y cierran bien las puertas y ventanas? Si no se atienden, estos pequeños problemas pueden provocar daños estructurales más graves.
Además, es imprescindible limpiar el tejado y los canalones. Las hojas, ramas y otros residuos pueden obstruir el sistema de drenaje, haciendo que el agua se acumule y provocando posibles fugas o corrosión. Una limpieza regular garantiza un drenaje adecuado y evita problemas innecesarios.
Prevenir la oxidación
Para las estructuras de acero, el óxido es un enemigo común. Inspeccione regularmente la superficie del acero, especialmente en las juntas y zonas soldadas, para detectar cualquier signo de óxido. Si encuentra óxido, elimínelo rápidamente con papel de lija o un cepillo de alambre, y aplique una nueva capa de pintura resistente al óxido. Esto no sólo prolonga la vida útil del edificio, sino que también mantiene su aspecto impecable.
Al mismo tiempo, es crucial garantizar una buena ventilación en el interior del edificio. La acumulación de humedad puede acelerar la oxidación, así que compruebe que los sistemas de ventilación funcionan correctamente. Si es necesario, considere la posibilidad de instalar equipos de ventilación adicionales.
Puertas, ventanas y sistemas de ventilación
Las puertas y ventanas son componentes vitales de los edificios agrícolas, pero también pueden convertirse en fuentes de corrientes de aire o fugas. Inspeccione periódicamente las juntas de puertas y ventanas, y sustitúyalas si es necesario. Si observa alabeos o dificultades para cerrar, es posible que haya que ajustar o sustituir las bisagras.
Los sistemas de ventilación también requieren un mantenimiento regular. El polvo, las telarañas y otros residuos pueden obstruir las rejillas de ventilación y dificultar el flujo de aire. Limpie con regularidad los equipos de ventilación para garantizar su funcionamiento eficaz. Esto no sólo mejora la calidad del aire interior, sino que también evita la acumulación de humedad.
Comprobaciones de integridad estructural
Por último, no olvide inspeccionar la estructura general del edificio. ¿Están sueltos o corroídos los pernos, las juntas soldadas y otros conectores? ¿Hay hundimientos o grietas en los cimientos? Si no se resuelven, estos problemas pueden provocar deformaciones estructurales o incluso el derrumbe. Compruebe y apriete periódicamente los conectores sueltos, y repare los problemas de los cimientos para garantizar que el edificio siga siendo estructuralmente sólido.
Siguiendo estas tareas rutinarias de mantenimiento, puede prolongar considerablemente la vida útil de sus edificios agrícolas y mantenerlos en condiciones óptimas.
Mantenimiento estacional: Cuide los edificios de su granja como "el cuidado estacional de la piel".
Los edificios con estructura de acero son como la "piel" de una granja, y requieren cuidados específicos en las distintas estaciones. Siga esta guía estacional para que el edificio no tenga miedo a los retos climáticos durante todo el año.
🌱 Primavera: Despierta el "periodo dorado de reparación" de los edificios
Revisión estructural: Tras el deshielo, limpie la humedad residual del tejado y el suelo para evitar que la acumulación de agua dañe los materiales de construcción.
Primeros auxilios en sistemas de drenaje: Retira el codo de la tubería de desagüe y utiliza una pistola de agua a alta presión para purgar el sedimento (¿obstrucción persistente? Vierte media taza de vinagre blanco y déjalo reposar durante 10 minutos antes de enjuagar).
Actualización de óxido: ¿Se ha desprendido el revestimiento? Vuelva a aplicar pintura antioxidante y dé prioridad a la reparación de la zona húmeda orientada al norte.
❗ Acciones clave
- "3 comprobaciones y 1 desatasco": comprobar las juntas del tejado, comprobar las grietas de los cimientos, comprobar el óxido de los pernos; desatascar la zanja de drenaje.
☀️ Verano: Protección solar y prevención contra insectos
Mantenimiento del revestimiento de protección solar: Toque la superficie del techo con el dorso de la mano. Si está caliente (>50℃), significa que el revestimiento reflectante ha fallado. Vuelva a pulverizar pintura de protección solar blanca mate (la reflectividad aumenta en 30%, la temperatura se reduce en 5-8℃).
Línea de prevención de plagas: Espolvoree polvo de bórax (seguro para los animales domésticos) en los bordes de las fundas de alambre y algodón aislante, o cuelgue bolas de algodón con aceite de menta.
🔍 Amenazas ocultas
- Comprueba si la rejilla de ventilación está dañada (¡los ratones pueden entrar por un hueco de 1 cm!), y sustitúyela por una rejilla de acero inoxidable.
🍂 Otoño: Prepárate para la "última ventana" de viento y lluvia
Defensa del drenaje: Instale un filtro de nailon encima del canalón e inspecciónelo una vez a la semana.
Refuerzo estructural: Comprueba si hay daños causados por tormentas o fuertes vientos en verano, y repáralos a tiempo para evitar que se amplíen.
Sellado de puertas y ventanas: Utilice una cámara termográfica para detectar puntos de fuga de aire en puertas y ventanas (las zonas de color azul púrpura son fugas de aire a baja temperatura), y sustituya las tiras de sellado engrosadas.
📆 Recordatorio de cuenta atrás
- La inspección del tejado y el aislamiento de las tuberías deben realizarse 30 días antes de la primera helada.
❄️ Invierno: Una "guía de supervivencia" bajo la presión del hielo y la nieve
Reducción de la carga del tejado: Cuando la acumulación de nieve supere los 15 cm, utiliza un rascador de tejado de mango largo para limpiarla por secciones desde los aleros hacia arriba para evitar dañar el revestimiento.
Anticongelante para tuberías: Enrolle el cable calefactor eléctrico alrededor de las tuberías de agua expuestas y retírelo tras la descongelación.
⚠️ Plan de emergencia
- ¿Tormenta de nieve repentina? Utiliza postes telescópicos para apoyar las vigas de carga del tejado (apoya a intervalos de 2 metros para evitar sobrecargas locales).
- ¿Falla la calefacción? Cuelgue mantas aislantes de emergencia en el granero.
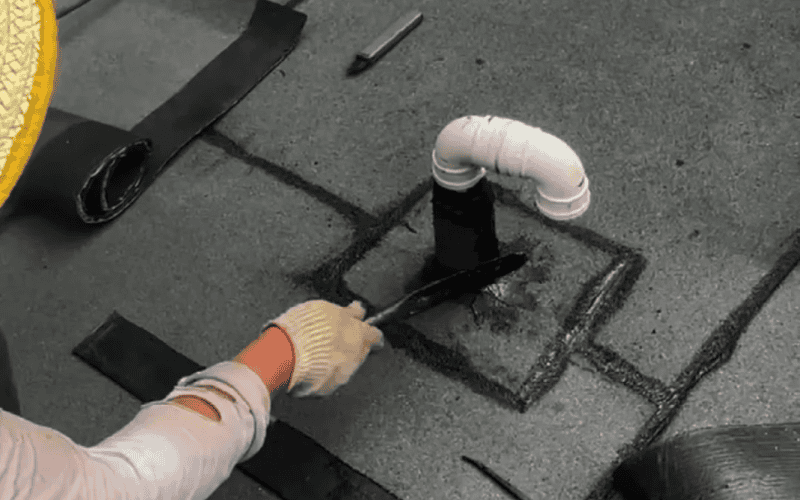
Problemas comunes de mantenimiento de edificios agrícolas y soluciones
① Corrosión y óxido
Causas: ambiente húmedo, volatilización de excrementos animales/fertilizantes, retención a largo plazo del agua de lluvia.
Lugares de alta incidencia: juntas del tejado, esquinas de las paredes y puntos de contacto con el suelo, debajo de los canalones, paredes de las zonas de almacenamiento de piensos.
Cómo determinarlo:
- Aparecen manchas de óxido de color marrón rojizo o ampollas del revestimiento en la superficie (rásquelo ligeramente con las uñas, si se desprende y deja al descubierto el metal, se está deteriorando).
- Polvo blanco cerca de la conexión metálica (signo de corrosión electrolítica).
Solución:
- Óxido leve: Lijar hasta dejar el metal desnudo con papel de lija → Aplicar imprimación epoxi rica en zinc → Cubrir con capa de acabado del mismo color que el edificio.
- Óxido severo: Corta la chapa de acero oxidada (mantén una zona intacta de 5 cm a su alrededor) → Suelda una nueva chapa de acero (se recomienda chapa galvanizada plata mate) → Tratamiento general de prevención del óxido.
📌 Consejos: Ponga una cinta roja de advertencia después de la reparación para recordarle que debe comprobar de nuevo después de 3 meses.
② Deformación estructural
Causas: fuerte presión del viento/nieve, colisión mecánica, la oxidación local debilita la capacidad de carga.
Lugares de alta incidencia: vigas del techo, encima de los marcos de las puertas, columnas de soporte de las paredes laterales.
Cómo determinarlo:
- Utiliza una regla para presionar contra las vigas y los pilares. Si la separación supera los 3 mm, significa que se está doblando.
- El interruptor del marco de la puerta está atascado o aparece una inclinación en forma de diamante (la diferencia de longitud diagonal es superior a 2 cm).
Solución:
- Deformación menor: instalar ángulo de acero de refuerzo en forma de L y fijarlo con pernos de expansión.
- Deformación grave: empújela lentamente a la posición original con un gato hidráulico → suelde la varilla de soporte horizontal.
⚠️ Nota: En caso de deformación grave, solicite a profesionales que realicen una evaluación estructural y una reparación. Mida la recuperación de la deformación cada día en las 48 horas siguientes a la corrección.
③ Conectores sueltos
Causas: Las vibraciones a largo plazo, la diferencia de temperatura provocan dilataciones y contracciones térmicas del metal, y un apriete insuficiente durante la instalación.
Lugares de alta incidencia: nodos de pernos de cerchas de tejado, conexiones de paneles de pared y columnas, pernos de anclaje.
Cómo juzgar:
- Utiliza un rotulador para trazar una línea recta entre la cabeza del tornillo y la tuerca. Al cabo de 1 mes, la posición de la línea está desalineada, lo que significa que está flojo.
- Al golpear el punto de soldadura, el sonido es sordo (sólido) frente a hueco (desoldadura).
Solución:
- Pernos flojos: apriételos uno a uno en orden diagonal (para evitar una fuerza desigual), y ajuste la llave dinamométrica a 120N-m (consulte las especificaciones de los pernos).
- Agrietamiento del punto de soldadura: sustituya el conector o vuelva a soldar (esmerile la grieta → repare la soldadura con varilla de soldadura E71T-1 → aplique pintura ignífuga).
🔧 Consejos: Aplique lubricante antioxidante regularmente para prolongar la vida útil del conector.
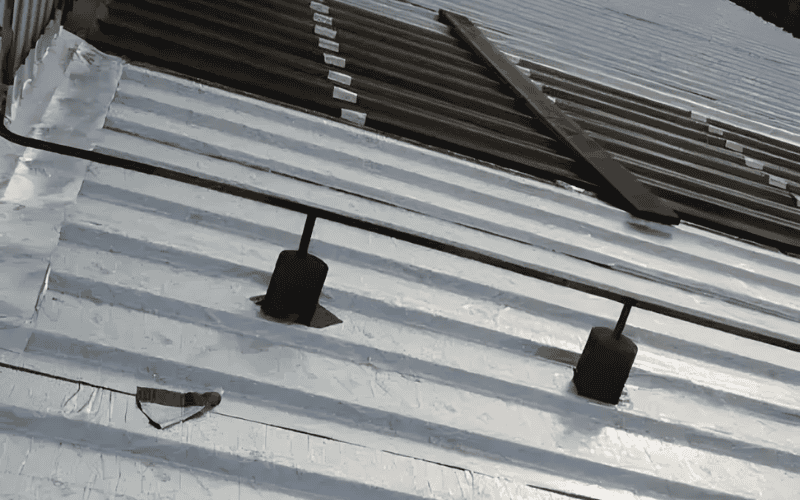
④ Problemas en tejados y desagües
Causas: Obstrucción por hojas caídas, envejecimiento del sellador, desplazamiento de los paneles del tejado debido a la dilatación y contracción térmicas.
Lugares de alta incidencia: esquinas de zanjas de drenaje, bordes de claraboyas y juntas de cumbreras.
Cómo juzgar:
- Hay charcos en el tejado después de llover (diámetro > 10 cm durante 1 hora).
- Manchas de agua o moho en las paredes interiores (especialmente en la unión del techo con la pared).
Solución:
- Obstrucción del desagüe: Utilice una pistola de agua a alta presión (con una boquilla en forma de abanico de 30°) para purgar en sentido inverso desde la salida.
- Fugas en la junta: Elimine el sellante antiguo (ablandado con un cuchillo multiusos + pistola de aire caliente) → Rellene con cola de poliuretano resistente a la intemperie (negra) → Raspe para formar una capa impermeable en forma de arco.
- Perforación del panel del techo: Corta un tablero de parche (del mismo material) que sea 10 cm más grande que el agujero → Pega con pegamento estructural → Refuerza con remaches de borde.
🌧️Test método: Después de la reparación, utilice una tubería de agua para simular la lluvia durante 10 minutos y observe la fuga.
⑤ Asentamiento o grietas en los cimientos.
Causa: Cambios en el contenido de humedad del suelo, rodadura de maquinaria pesada, drenaje deficiente y erosión de los cimientos.
Lugares de alta incidencia: cuatro esquinas del edificio, bajo el marco de la puerta, cerca de la salida del tubo de desagüe.
Cómo determinarlo:
- Utilice un nivel láser para detectar la inclinación del suelo (>2°, preste atención).
- La anchura de la grieta supera los 5 mm o se expande de forma escalonada.
Solución:
- Grietas poco profundas: inyectar material de rejuntado de resina epoxi (transparente) → cubrir la superficie con revestimiento impermeable a base de cemento.
- Asentamiento grave: refuerce los cimientos o utilice un gato para ajustar el nivel del edificio.
📐 Herramienta de supervisión: parche blanco indicador de grietas (cambia de color cuando está agrietado, compruébelo una vez al mes).
Estrategias de mantenimiento preventivo de edificios agrícolas
El mantenimiento preventivo puede ayudar a prolongar la vida útil de los edificios agrícolas y reducir los costes de reparación. He aquí algunas estrategias clave:
Calendario de inspecciones periódicas: Realice una inspección exhaustiva cada trimestre, centrándose en áreas clave como tejados, paredes y sistemas de desagüe para asegurarse de que los posibles problemas se descubren a tiempo.
Utilizar revestimientos protectores: Aplique regularmente revestimientos antioxidantes e impermeables de alta calidad para proteger las estructuras de acero de la humedad, los rayos UV y los productos químicos.
Instalar sistemas de protección: Asegúrese de que los sistemas de drenaje no estén obstruidos e instale revestimientos antioxidantes y medidas de impermeabilización para evitar la acumulación de humedad y daños estructurales.
Registrar la información de mantenimiento: Después de cada mantenimiento, registre la información detallada, incluido el contenido de la inspección, los problemas y las soluciones para su seguimiento y referencia futura.
Cuándo llamar a un profesional: No dude en estas 4 situaciones.
- Daños estructurales graves:
- Techo hundido más de 5 cm, puertas/ventanas atascadas debido a la deformación del marco, columnas de soporte inclinadas >10 grados. Colapso inminente. Aísle la zona con cinta roja de precaución y ponte en contacto con un ingeniero estructural con fotos.
- Sustitución o soldadura de acero a gran escala:
- Daños por óxido >20 pies cuadrados (2㎡) o soldaduras en vigas/paredes de carga.
- Fallo de cimentación:
- Grietas >0,4 pulgadas (1 cm) de ancho, patrones escalonados o inclinación visible del suelo.
- Reparaciones complejas de electricidad o fontanería:
- Fallos en el cableado con riesgo de incendio, corrosión de las tuberías de gas, rotura de tuberías congeladas.
🔧 Bricolaje frente a profesional: Conoce los límites
Edición | DIY-Friendly | Llame inmediatamente a un profesional |
Óxido | Manchas aisladas (< tamaño de hoja A4) | Herrumbre generalizada o daños en los soportes de carga |
Drenajes obstruidos | Eliminar los residuos de los canalones | Tuberías subterráneas rotas que necesitan excavación |
Pernos sueltos | Apriete los tornillos (par de apriete ≤37 lb-ft/50N-m). | Pernos de anclaje rotos o soldaduras agrietadas |
"Protección de por vida" para su explotación: SteelPRO PEB facilita el mantenimiento
Mientras te dedicas en cuerpo y alma a edificios agrícolasSteelPRO PEB está dispuesto a ser su respaldo más fiable. Nuestra gama completa de edificios agrícolas de la estructura de acero no sólo se construye con artesanía excelente, pero también promete:
✅ 50 años de garantía estructural: la resistencia del acero y la tecnología de soldadura están certificadas internacionalmente, sin miedo a los desafíos climáticos extremos.
✅ 25 años de garantía de recubrimiento - utilizando la tecnología antioxidante de grado militar, la personalización de la tarjeta de color, de larga duración como nuevo.
✅ Asistencia de mantenimiento de por vida: lista de comprobación de inspección anual gratuita, línea directa de mantenimiento 24/7, tutorial de mantenimiento exclusivo.
¿Por qué elegirnos?
- Testigo de datos: 90% de los clientes tienen cero gastos importantes de mantenimiento en 10 años.
- Servicio personalizado: desde el tamaño y el color hasta el diseño de ventilación a prueba de insectos, para satisfacer sus necesidades personalizadas.
- Compromiso de protección medioambiental: Todo el acero es reciclable 100%, y el revestimiento cumple las normas de protección medioambiental REACH de la UE.