If you’re facing tight deadlines, cost overruns, or inconsistent quality from traditional construction, modular construction may be the solution you’ve been looking for. In this article, we’ll dive into the key benefits of modular construction—from time savings to budget predictability—and explore how it can help you address common challenges.
What Is Modular Construction and How Does It Work?
Modular construction represents a contemporary building approach where the structural components are prefabricated in a factory setting, off-site, and subsequently assembled at the construction site. This methodology contrasts with traditional construction, which involves constructing everything from scratch at the site itself.
The key idea here is Geschwindigkeit Und Effizienz. By assembling large portions of the building in a controlled factory setting, much of the work happens away from the site. This reduces delays caused by weather, labor shortages, and other unpredictable factors common in traditional construction.
How Modular Construction Works:
- Design: It all starts with planning. Just like traditional construction, architects and engineers create designs. However, these designs are tailored to fit modular construction, which means they can be easily broken into parts that can be prefabricated.
- Herstellung: The sections, or modules, of the building are fabricated in a factory using the same materials as conventional constructions, but in a controlled setting, thereby guaranteeing enhanced precision and minimizing defects.
- Transportation and Assembly: Once the modules are completed, they are then transported to the designated construction site. On-site, these modules are lifted into place using cranes and connected to form the complete structure.
- Finishing Touches: After the modules have been positioned, the final stages resemble those of traditional construction methods. This includes interior finishing, plumbing, and electrical work, all of which can be done quickly and efficiently.
Why Should You Consider Modular Construction?
When it comes to construction, we all know the challenges: delays, cost overruns, Und quality control issues. These issues can result in delays, budget overruns, and dissatisfaction from clients or tenants. If you are a developer, contractor, or project manager, you are likely well-acquainted with these challenges.
So, why should you even consider modular construction? The simple answer is that it solves many of these common problems. Here’s how:
1. Faster Completion Times
Modular construction reduces the time needed to finish a project. By building modules off-site in a controlled factory environment, the construction process happens parallel to site preparation. This means less waiting around, and your building can be ready weeks or even months sooner than with traditional methods.
2. Better Cost Control
Modular construction can help you stick to your budget. With more predictable timelines, you avoid the costs associated with delays. Plus, factory-based building reduces waste and the need for expensive rework, helping you save money on materials and labor.
3. Consistent Quality
In a factory, everything is built to precise standards. This minimizes errors, guaranteeing greater consistency and a lower incidence of defects compared to traditional construction methods. It also eliminates delays due to bad weather or workforce shortages.
Growing Demand and Relevance in Today’s Market
The demand for modular construction is growing, and the reasons are clear. As projects get bigger, budgets get tighter, and timelines get shorter, developers are looking for ways to meet these pressures. Modular construction is not just a trend—it’s a response to the growing need for faster, cheaper, Und higher-quality buildings. Whether you are working on residential, commercial, or industrial projects, modular construction can offer the solutions you seek.
As the market evolves, more businesses and government projects are turning to modular solutions to stay competitive and meet the demand for efficient, sustainable construction.
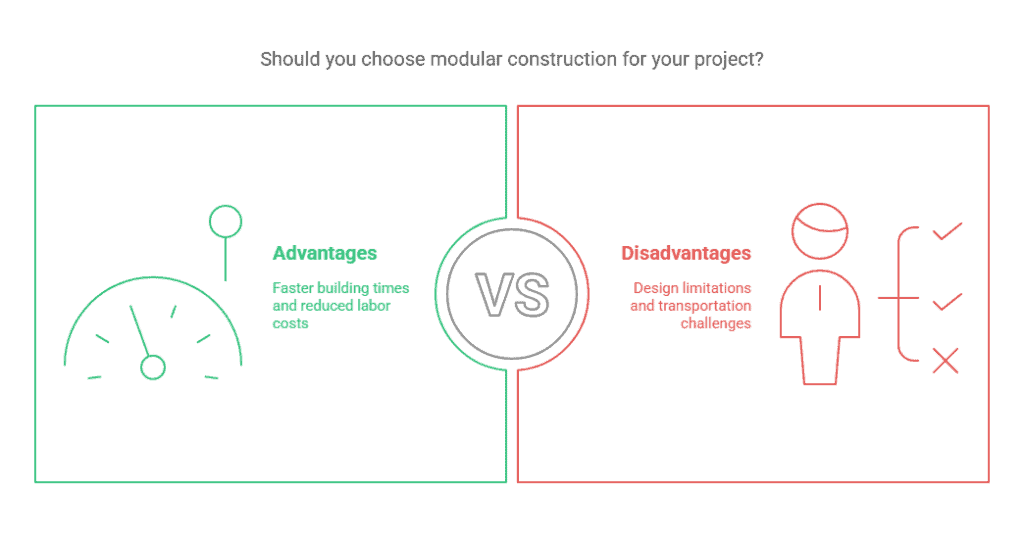
What are modular construction’s advantages and disadvantages?
Vorteile | Nachteile |
Schnellere Konstruktion | Transport and Logistics Costs |
Kostengünstig | Designbeschränkungen |
Quality and Consistency | Site Constraints |
Nachhaltigkeit | Perception and Market Acceptance |
Flexibilität und Anpassung | High Upfront Planning Requirements |
Improved Safety | Local Code and Permit Challenges |
Less Site Disruption | Limited Modifications On-Site |
Scalability and Repeatability | Supply Chain Dependency |
Easier Quality Control Documentation |
Weiterführende Literatur: Vor- und Nachteile von Fertighäusern
How Much Time Can Modular Construction Save?
Modular construction can reduce your project time by 30% to 50%, which means you could save weeks or even months compared to traditional methods. For larger projects, this time-saving becomes a huge advantage.
Traditional Construction vs. Modular Construction
Traditional construction usually follows a sequential process—foundation first, then the building, followed by finishing. This can lead to delays caused by weather or other unexpected issues. With modularer Aufbau, modules are built off-site while site work is happening at the same time. This parallel approach significantly shortens the overall timeline.
Impact on ROI and Leasing/Sale Timelines
Faster completion means your building is ready for leasing or sale sooner, which directly impacts ROI. Early occupancy generates rental income or sales revenue faster, and it also reduces financing costs. In competitive markets, this gives you a big edge.
What About Cost – Is Modular Construction Truly More Affordable?
When considering cost, modular construction frequently proves to be more economical in the long run. Here’s how it achieves this:
Initial Cost vs. Long-Term Savings
Während die Anschaffungskosten of modular construction can be similar to traditional building, the langfristige Einsparungen are significant. By building modules off-site, you reduce on-site labor costs, waste, and rework. Since a significant portion of the work is carried out in a controlled factory setting, the chances of errors and delays are greatly reduced. Consequently, this leads to savings on materials, labor, and the need for costly corrections later in the project.
Budget Predictability and Fewer Change Orders
One of the key financial advantages of modular construction is budget predictability. Since much of the work is pre-planned and executed in the factory, unexpected costs are far less common. There’s also less need for change orders, which can balloon costs and delay projects in traditional construction.
Is Modular Construction Better Than Traditional Methods?
Yes, modular construction can deliver superior quality compared to traditional building methods. Here’s why:
Factory-Controlled Environment = Precision and Consistency
In a factory setting, everything is built in a controlled environment. This means higher precision Und consistent results. The controlled conditions help eliminate variables like weather or site challenges that can affect quality in traditional construction.
QA/QC Measures During Off-Site Manufacturing
Quality assurance (QA) and quality control (QC) play pivotal roles in modular construction. Factory production follows strict standards, with regular inspections throughout the process. This ensures that each module meets the necessary specifications before it is shipped from the factory.
Reduced Human Error and Weather-Related Defects
Human errors and weather delays are major contributors to defects in traditional construction. By building modules off-site, in a controlled environment, errors are minimized Und weather-related issues like rain or extreme heat no longer impact the construction process. This results in a higher-quality finish.
Weiterführende Literatur: Traditionelle oder modulare Konstruktion
Will It Work for My Type of Project?
Modular construction is incredibly versatile, and can work for a wide range of projects. Here’s how it might fit your needs:
Types of Projects Where Modular Construction Thrives
Modular construction is ideal for projects that need to be built quickly and efficiently, including:
- Apartments and Residential Buildings
- Hotels and Lodging
- Offices and Commercial Spaces
- Schools and Educational Facilities
These types of projects benefit from modular construction because they often need to meet tight deadlines and cost constraints. Modular allows you to deliver high-quality buildings quickly while maintaining budget control.
Structural Flexibility: Low-Rise, Mid-Rise, Stackable Designs
Modular buildings aren’t limited to single-story designs. They can be adapted for:
- Low-rise (single-story)
- Mid-rise (multiple stories)
- Stackable designs (multiple modules stacked to create taller structures)
This flexibility allows modular construction to be used in various building types, from simple single-story offices to multi-story apartment complexes or hotels.
Customization and Scalability Options
While modular buildings are often associated with standard designs, they can be individuell to fit specific needs. Whether you need specialized layouts, room configurations, or specific materials, modular construction can adapt to your vision.
Zusätzlich, scalability is a major advantage. If you need to expand the building in the future, you can easily add more modules to the existing structure without major disruptions or delays.
In short, modular construction is highly flexible and adaptable, making it a viable option for a wide range of project types. Whether you need a small office or a multi-story residential complex, it can meet your requirements.

What Are the Modular Construction Environmental and Compliance Advantages?
Modular construction offers key environmental and compliance benefits:
- Weniger Abfall: Materials are cut precisely in the factory, minimizing excess waste compared to traditional construction.
- Fewer Deliveries: Fewer trips to the site reduce transportation emissions and fuel use.
- Less On-Site Disturbance: Off-site construction results in less noise, dust, and disruption to the surrounding area, particularly in urban or environmentally sensitive locations.
- Green Building: Modular construction is inherently more environmentally sustainable. The factory-controlled environment facilitates efficient use of materials, energy conservation, and makes it easier to meet LEED or other green building standards.
- Codes and Standards: Modular construction adheres to the same building codes and fire safety standards as traditional construction. The controlled factory environment facilitates superior quality control and consistent adherence to safety and regulatory standards.
Who’s already doing it—and succeeding?
Modular construction isn’t just a concept—it’s being applied around the world to solve real-world challenges in a wide range of industries. Here are some of our standout projects:
1. Copper Processing Plant, Kazakhstan
Located in a region known for extreme cold and strong winds, the project required a structure that could handle seismic risk and heavy snow loads.
A modular steel system designed for wind and earthquake resistance was selected to reduce onsite labor and minimize weather delays. The result: precise installation, safer operations, and a consistent schedule.
2. Thermal Power Plant, Philippines
Humidity and high temperatures made boiler frame stability a primary concern. Modular construction provided a practical solution: high-strength, pre-treated steel modules were fabricated off-site, reducing exposure to moisture during construction.
This approach significantly reduced construction time and provided a structure that would maintain high performance over the long term in harsh climate conditions.
3. Zhengding E-commerce Industrial Base, China
Speed was everything. The project required fast delivery, efficient space utilization, and compliance with seismic codes.
The team used a modular portal frame system to optimize layout, reduce on-site time and ensure long-term durability. The project was completed ahead of schedule, featuring improved space utilization and reduced risk.
Want to know more about our successful projects? Click here to check it out!
Is Modular Construction Right for You?
So, is modular construction the right fit for your project? Here’s how to decide:
1. Is Your Project Time-Sensitive?
Modular construction speeds up the process by allowing site work and module fabrication to happen simultaneously. If meeting tight deadlines is important, modular construction can help you deliver faster, making your project ready for use earlier.
2. Do You Need Cost Control?
Modular construction offers budget predictability. With fewer delays, reduced labor, and minimized material waste, it keeps your project within budget and lowers the risk of cost overruns.
3. Are You Looking for Quality and Consistency?
Modular construction, which is carried out in a controlled factory environment, guarantees consistent quality and minimizes defects when compared to traditional methods, where site conditions can introduce variability.
4. Is Sustainability Important for Your Project?
Modular construction reduces material waste, transportation emissions, and makes it easier to achieve green building standards wie LEED certification, supporting sustainability goals.
5. Do You Have a Custom or Complex Design?
Modular construction offers sufficient flexibility to accommodate large-span designs, multi-story buildings, or unique structures. Additionally, it facilitates future expansion if required.
6. Does Your Project Have Strict Regulatory Requirements?
Modules are constructed to adhere to the same building codes and safety standards as traditional buildings, guaranteeing compliance and reliable safety from inception.
If your project needs Geschwindigkeit, cost control, Qualität, Und Nachhaltigkeit, modular construction could be the perfect choice. It is ideal for a diverse range of developments, encompassing commercial spaces and residential builds alike.
Unlock the Potential of Modular Construction for Your Next
Bei SteelPRO PEB sind wir spezialisiert auf modular solutions that provide unmatched flexibility, strength, and efficiency. If you are ready to enhance your project and optimize your construction process, please reach out to us today. Let us show you how our modular solutions can save you time, money, and hassle—while delivering the results you expect.