Thinking about prefabricated buildings for your next project in South Africa? You’re probably wondering whether it’s really more cost-effective than traditional methods. From construction expenses to long-term maintenance, the answer depends on several key factors.
In this guide, we break it down for you. We’ll compare prefab and traditional construction costs, explore the major cost drivers specific to South Africa, and show how regional differences affect your budget. Real-life case studies will give you a closer look at how companies saved time and money with SteelPRO Peb solutions.
By the end, you’ll know exactly how to plan smarter and spend better with prefab construction.
Comparative Cost Analysis: Prefab vs Traditional Construction
When evaluating building solutions in South Africa, cost remains one of the most decisive factors for property developers, businesses, and government projects. This section focuses on comparing the financial aspects of prefabricated buildings versus traditional construction, not just on initial investment but over the total lifecycle of the building.
Lower Initial Costs Per Square Meter
One of the most immediate advantages of prefabricated buildings is their lower upfront cost. On average, prefab structures cost significantly less per square meter compared to conventional masonry or concrete structures. This cost-efficiency is largely due to mass production, better material utilization, and streamlined labor needs within controlled factory environments. For cost-sensitive industries such as mining, education, and small business, this means more building for less budget.
Reduced Total Cost of Ownership
Beyond initial investment, prefabricated buildings offer a lower Total Cost of Ownership (TCO). Maintenance costs tend to be lower due to modern materials that resist corrosion, mold, and weather damage. Additionally, prefab buildings are inherently more energy efficient because of tighter quality control in insulation and sealing during factory assembly. The long-term savings on repair and utility expenses contribute significantly to lowering the TCO.
Faster Return on Investment
Time is money, especially in sectors like retail, healthcare, and logistics. The shorter construction timeframe of prefabricated buildings allows assets to become operational weeks or even months earlier than traditional builds. That earlier start means quicker revenue generation or earlier access to facilities, making prefab a valuable option for investors looking for faster turnaround and ROI.
Better Budget Clarity and Cost Control
Unlike traditional construction, which often faces cost overruns due to weather, labor shortages, or unexpected site conditions, prefab projects benefit from greater predictability. Because much of the building process takes place offsite with standardized components and fixed timelines, customers can plan their budgets with greater accuracy. This transparency makes prefabricated construction particularly appealing to clients with tight financial margins or large-scale rollouts.
In summary, the financial advantages of prefabricated buildings go well beyond the initial savings. They offer a compelling cost-performance solution through lower lifecycle expenses, shorter construction timelines, and dependable budgeting.
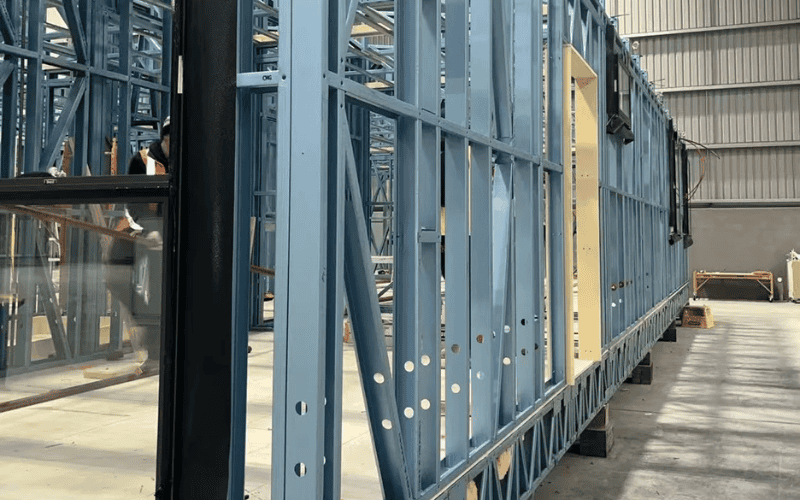
Key Cost Drivers of Prefabricated Buildings in South Africa
When considering a prefabricated building project in South Africa, understanding the key cost drivers can help you make better planning and procurement decisions. Let’s walk through the main factors that significantly affect the total investment.
1. Material Costs and Local Sourcing
The price of core construction materials, such as steel and insulation panels, heavily impacts the cost of prefab buildings. South Africa’s dependence on global steel prices means fluctuations in international markets can directly raise or lower project budgets. However, sourcing materials locally can help optimize spending, shorten lead times, and reduce import duties. Proximity to reliable suppliers of high-quality insulation panels, cladding, and frame elements often translates into better project cost control.
2. Logistik und Transport
Prefab units are manufactured off-site and then assembled on the actual site. For clients in remote regions, transport becomes a major cost component. Long distances, poor road conditions, and the need for special handling or oversized load escorts can all raise freight charges significantly. Therefore, working with suppliers like SteelPRO Peb who offer optimized shipping routes and onsite delivery planning can make a real financial difference.
3. Standardization vs. Customization
One of the biggest advantages of prefabricated construction is the use of standardized modules, which helps save on labor and equipment costs. Repetitive manufacturing of components ensures efficiency and price stability. However, if a building requires substantial customization in terms of dimensions, finishes, or integrated systems, the unit cost will rise. When project design stays closer to standard templates, budgets remain more predictable.
4. Site Preparation and Supporting Infrastructure
Often overlooked, foundation work and site preparation can quietly absorb a large portion of the budget. Uneven terrain might require grading, drainage planning, or even retaining walls. In addition, utility connections for electricity, plumbing, and internet are essential, and their availability—or lack thereof—will influence cost levels. In some rural settings, off-grid solutions even need to be factored into early-stage cost planning.
BRIEFLY: Each of these components—material pricing, logistics, building design, and site conditions—has the power to affect your final cost per square meter. At SteelPRO Peb, we help clients analyze cost drivers from day one, so they can make informed decisions, especially when working within fixed budgets or timelines.
Regional Considerations Influencing Costs in South Africa
When planning a prefabricated building project in South Africa, regional differences can dramatically affect your overall costs. Understanding the local environment—both economically and administratively—is essential, especially if you are new to the South African market.
Let’s start with construction hotspots. Gauteng, Western Cape, and KwaZulu-Natal are among the country’s most active regions for commercial and residential development. But each has its own pricing profile:
- Gauteng: As the economic hub, land prices and labor costs are notably high, particularly in Johannesburg and Pretoria. However, project infrastructure is generally well-developed, which can help reduce delays.
- Western Cape: Known for its stable governance and efficient municipal processes, Western Cape offers a reliable permitting process. Yet, land prices around Cape Town are also among the highest in the country.
- KwaZulu-Natal: Relative to the other two provinces, land costs can be more affordable, especially outside of Durban. However, labor costs vary widely, and infrastructure outside urban centers may pose logistical challenges.
Now, zooming in on red tape: provincial laws and municipal approval timelines matter more than many first-timers expect. In some provinces, bureaucratic delays or complex regulations can add weeks—sometimes months—to your timeline, which in turn drives up costs through extended equipment rental, labor hours, and finance charges.
Another overlooked variable is infrastructure readiness. Areas with poor power grids, limited road access, or inadequate water supply require additional investment in temporary facilities or off-grid solutions. This not only impacts cost, but often affects scheduling and the ability to meet deadlines.
That’s why at SteelPRO Peb, we assist our international clients with regional planning and site selection. Our in-country experts help you weigh all location-based factors so you aren’t blindsided by unexpected regional differences. Choosing the right region aligned with your priorities—whether it’s lower costs, faster approvals, or better access to infrastructure—can make a substantial impact on your investment’s success.
Case Studies: Cost-Efficient Prefab Projects in South Africa
To truly understand the cost advantages of prefabricated buildings in South Africa, it helps to look at real-world applications. At SteelPRO Peb, we have completed several projects that clearly demonstrate how modular construction can reduce expenses and shorten timelines without compromising quality.
One standout project is a modular classroom initiative completed for a primary school in Cape Town. The client required a fast-track solution due to a rising number of students and limited existing space. By applying our modular construction techniques, we were able to reduce the construction time by 60% compared to conventional methods. Even more significantly, total project costs were reduced by approximately 30%. The savings came from streamlined site work, factory-controlled production, and quicker deployment — minimizing labor and material inefficiencies.
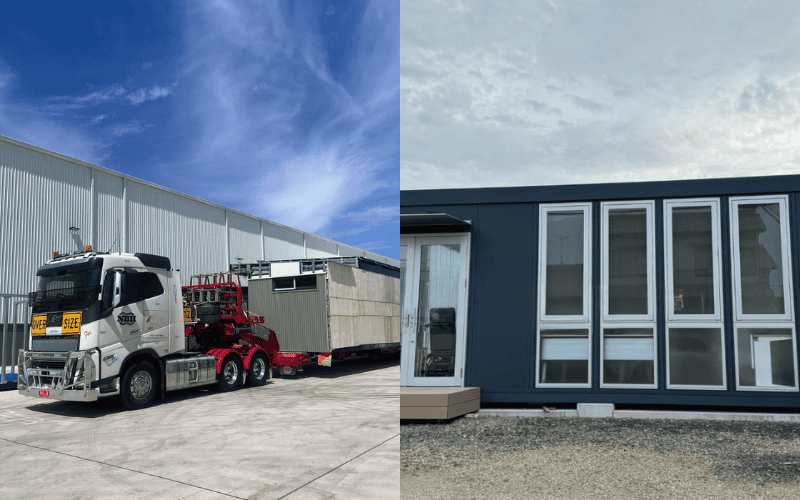
Another compelling example is a commercial park project in Johannesburg. The client prioritized speed to market and budget control. We utilized a repeating modular design that allowed for components to be manufactured and reused efficiently. This modular repetition saved considerable construction time and trimmed the overall budget substantially. The client was able to start operations weeks earlier than originally planned, unlocking revenue streams sooner than expected.
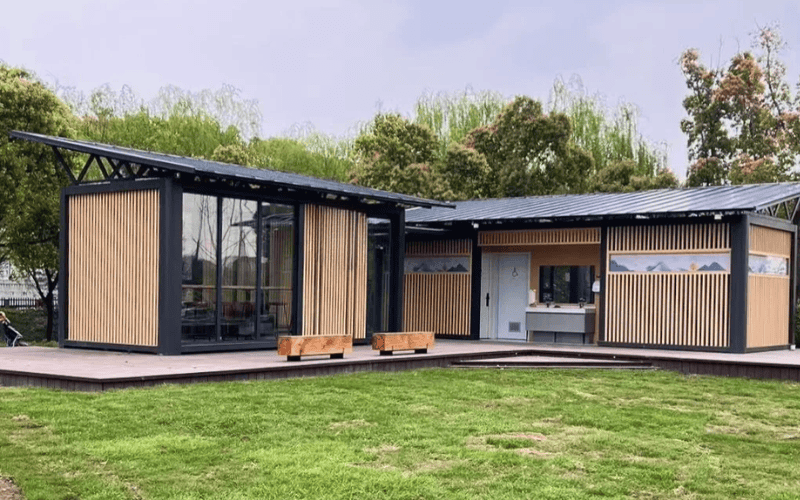
Across our projects, clients often emphasize the improved transparency and communication that modular construction enables. With clear production schedules, predictable pricing, and minimal on-site disruption, the experience is a marked improvement over traditional building processes. As one project manager put it, “Working with SteelPRO Peb was not just about saving money — it was about gaining clarity and confidence throughout the build.”
These case studies show that prefab construction is not only a cost-efficient choice but also a strategic decision that delivers operational and quality benefits. Whether for schools, commercial buildings, or temporary facilities, modular solutions continue to prove their value in the South African market.
At SteelPRO Peb, we’re more than just a prefab supplier — we’re your cost-efficiency partner in South Africa.
Whether you’re planning a school, a factory, or a commercial space, we help you control costs, speed up delivery, and reduce risks.
Reach out today to find out how we can support your next project.